Sputtering is a widely used thin film deposition process in various industries such as semiconductor manufacturing, optics, and materials science. It is used to deposit thin layers of material onto a substrate through a physical vapor deposition (PVD) process. Among the different sputtering techniques, DC sputtering, magnetron sputtering, and sputtering coating are commonly used methods. This article compares these sputtering techniques, outlining their principles, advantages, applications, and differences.
What is Sputtering?
Sputtering is a process in which atoms from a target material are ejected and deposited onto a substrate. This process occurs in a vacuum chamber where a gas (usually argon) is ionized and accelerated by applying a voltage between the target (cathode) and a substrate (anode). The accelerated ions bombard the target material, causing the ejection of atoms that then settle on the substrate. The three techniques discussed—DC sputtering, magnetron sputtering, and sputtering coating—each have unique features and applications.
DC Sputtering
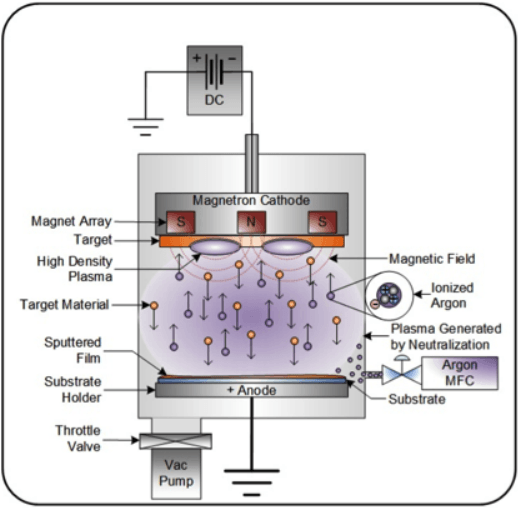
Principle of DC Sputtering
DC sputtering is one of the simplest forms of sputtering. It involves the application of direct current (DC) voltage to a target material, which is typically a metal or conductive material. The DC power causes ions from the plasma to bombard the target, causing the target atoms to be ejected and deposited onto the substrate.
Advantages of DC Sputtering
- Simplicity: DC sputtering is relatively easy to implement and control.
- Cost-Effective: It is a cost-efficient sputtering method, especially for small-scale applications.
- Ideal for Conductive Targets: DC sputtering works best with conductive materials as the target.
Limitations of DC Sputtering
- Limited to Conductive Targets: Non-conductive targets cannot be used effectively in DC sputtering because the process relies on the flow of electrons to maintain the discharge.
- Lower Deposition Rates: DC sputtering tends to have lower deposition rates compared to other methods like magnetron sputtering.
Applications of DC Sputtering
DC sputtering is commonly used for applications requiring the deposition of metallic films, such as in the production of semiconductor devices, solar cells, and coatings for optics.
Magnetron Sputtering
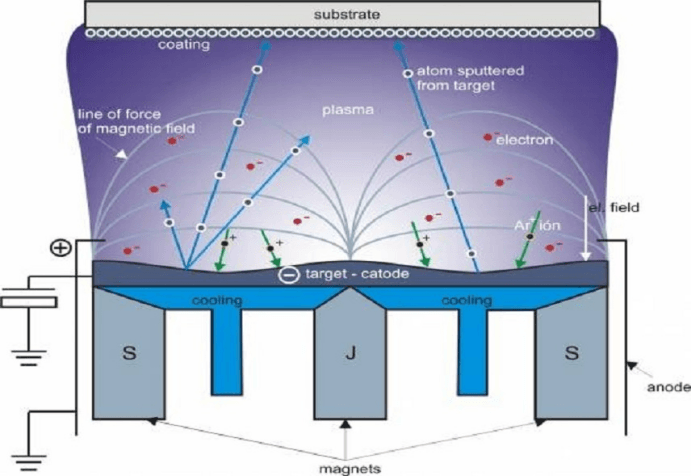
Principle of Magnetron Sputtering
Magnetron sputtering is an advanced version of DC sputtering that uses a magnetic field to enhance the sputtering process. A magnetron is a device that creates a magnetic field behind the target, which helps trap electrons near the target surface. This increases the density of the plasma and improves the sputtering efficiency, leading to higher deposition rates.
Advantages of Magnetron Sputtering
- Higher Deposition Rates: The use of magnets increases the efficiency of ionization, leading to faster sputtering and higher deposition rates.
- Versatility: Magnetron sputtering can be used with both conductive and non-conductive targets, unlike DC sputtering.
- Better Film Quality: The enhanced plasma density improves the uniformity and quality of the deposited films.
Limitations of Magnetron Sputtering
- Complexity: Magnetron sputtering is more complex to implement than DC sputtering, requiring additional equipment such as magnets and specialized power supplies.
- Cost: The initial setup cost of magnetron sputtering systems is generally higher.
Applications of Magnetron Sputtering
Magnetron sputtering is used extensively in industries requiring high-quality thin films, such as the semiconductor industry, solar cell manufacturing, optical coatings, and hard coatings for tools and components.
Sputtering Coating
Principle of Sputtering Coating
Sputtering coating refers to a broader range of sputtering processes used for coating materials. It includes both DC and magnetron sputtering techniques, as well as others, to apply thin coatings onto substrates. The process can involve different configurations, such as multi-target systems and varying power sources, to achieve specific coating requirements.
Advantages of Sputtering Coating
- Versatile Coatings: Sputtering coating allows for the deposition of various materials, including metals, alloys, ceramics, and composites, making it versatile for a wide range of applications.
- Uniform Coatings: The sputtering coating technique ensures uniform deposition of material, which is crucial for applications requiring consistent coatings.
- Fine Control: The process allows for precise control over the thickness and composition of the deposited coating.
Limitations of Sputtering Coating
- Equipment Cost: The cost of sputtering coating systems can be higher due to the complexity of the equipment and the need for precise control systems.
- Deposition Time: Depending on the material and thickness of the coating, sputtering can take a relatively long time compared to other coating methods.
Applications of Sputtering Coating
Sputtering coating is used in a wide range of industries, including aerospace, automotive, electronics, and energy, for applications such as protective coatings, decorative coatings, and functional films.
Comparison of DC Sputtering, Magnetron Sputtering, and Sputtering Coating
Key Differences
Feature | DC Sputtering | Magnetron Sputtering | Sputtering Coating |
---|---|---|---|
Voltage Type | Direct Current (DC) | Alternating Current (AC) | Both DC and AC |
Target Type | Conductive targets | Conductive and non-conductive targets | Conductive and non-conductive targets |
Deposition Rate | Lower | Higher | Varies (depends on the setup) |
Film Quality | Moderate | High | High |
Complexity | Simple | Moderate | Moderate to Complex |
Cost | Low | High | High |
Typical Applications | Metallic films, Semiconductors | Semiconductor coatings, Optical films, Hard coatings | Protective and decorative coatings, Functional films |
Conclusion
In summary, DC sputtering, magnetron sputtering, and sputtering coating each offer unique advantages and are suited for different applications. DC sputtering is simple and cost-effective for conductive targets, but its deposition rate is relatively low. Magnetron sputtering, with its higher deposition rates and better film quality, is ideal for a wide range of applications, including semiconductor manufacturing and optical coatings. Sputtering coating encompasses various sputtering methods to achieve precise, uniform coatings and is versatile for a wide range of materials. Understanding the differences between these sputtering techniques is crucial for selecting the most appropriate process for a given application.