Alloy Evaporation Material
Alloy Evaporation Materials (Pieces, Pellets & Powder)
TFM provides high-purity alloy evaporation materials in a variety of shapes and sizes to seamlessly integrate with coils, boats, crucibles, or hearth liners. Known for exceptional performance, TFM has earned a strong reputation as a trusted supplier of metal powders.
The most popular forms of evaporation materials include pellets, powders, granules, tablets, rods, plates, and rings. We ensure a wide range of materials, including metal pieces, pellets, and powders, are readily available in stock, allowing us to process your orders quickly and efficiently.
Below is a comprehensive list of our Alloy Evaporation Materials. Click on the product name for detailed information or use the “Inquiry” button to access competitive pricing and premium quality.
Alloy Evaporation Materials List
Custom Solutions and Additional Products
If your R&D or production requirements call for specialized materials not listed, feel free to contact us at sales@thinfilmmaterials.com or by phone at (786) 825-8645.
Additionally, TFM supplies a range of evaporation sources such as crucibles, boats, and thermal filaments. For more information, click here.
Comprehensive Insights into Alloy Evaporation Materials: Techniques, Applications, and Future Trends
Alloy evaporation materials have become an integral part of modern thin-film deposition techniques, impacting industries ranging from electronics and optics to energy and microfabrication. These materials, which are combinations of two or more metals (and sometimes non-metals), are vaporized under high-vacuum conditions and subsequently condensed onto various substrates to form thin films with unique properties. The ability to tailor the composition of these alloys enables researchers and engineers to optimize electrical, optical, and mechanical properties for a wide range of applications.
Table of Contents
Chapter 1
What Are Alloy Evaporation Materials?
Alloy evaporation materials are specially formulated mixtures of two or more elements designed to be vaporized and deposited as thin films under controlled conditions. Unlike pure metals, these alloys are engineered to combine the favorable properties of their constituent elements. For example, an alloy might be designed to improve conductivity while simultaneously enhancing resistance to oxidation or wear.
The process begins with the selection of a specific alloy composition based on desired film characteristics. Parameters such as melting point, vapor pressure, and chemical reactivity are crucial in determining which alloys are suitable for evaporation. Once chosen, the alloy is placed in a high-vacuum chamber where it is heated until it reaches a vapor state. The vapor then condenses onto a substrate, forming a uniform thin film. This film inherits many of the engineered properties of the original alloy, making it ideal for applications in electronics, optics, and even energy storage devices.
Historically, alloy evaporation materials have been used in a variety of applications—from semiconductor device fabrication to the production of optical coatings. The technique has evolved over time with the advent of advanced deposition methods, ensuring high purity and precision in the film’s thickness and composition. Today, research is pushing the boundaries further by exploring novel alloy combinations and innovative deposition techniques to meet the increasingly demanding requirements of modern technology.
Understanding alloy evaporation materials requires a firm grasp of both the physical vapor deposition (PVD) process and the role of material science in tailoring the properties of thin films. This combination of advanced processing and meticulous alloy design underpins the modern applications and potential future advancements in this field.
Chapter 2
How Does the Alloy Evaporation Process Work?
The alloy evaporation process is a form of physical vapor deposition (PVD) that involves converting a solid alloy into vapor and then condensing it onto a target substrate. This process is performed in a high-vacuum environment to minimize contamination and ensure the formation of a pure, uniform film. The essential steps of the process include evaporation, vapor transport, and condensation.
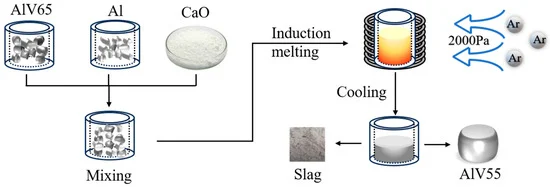
How Does the Alloy Evaporation Process Work?
The process begins with the alloy material being placed in a crucible or on a target holder within a vacuum chamber. Under vacuum conditions, the alloy is heated using either resistive heating, electron-beam heating, or laser-based methods until it reaches its evaporation point. At this stage, the material transitions from a solid or liquid phase into a vapor phase. The rate of evaporation is critically dependent on the alloy’s vapor pressure, which is determined by the properties of its constituent elements.
Transport of Vapor
Once the material has been vaporized, the individual atoms or clusters of atoms travel through the vacuum chamber. In a high-vacuum environment, the mean free path of these atoms is long, meaning they travel in relatively straight-line trajectories toward the substrate. This ballistic transport is essential for achieving a uniform deposition, as it minimizes collisions and scattering that could otherwise affect the film’s uniformity and composition.
Condensation and Film Formation
When the vapor reaches the cooler substrate, it condenses and forms a thin film. The quality of the resulting film is influenced by various factors such as the substrate’s temperature, the rate of deposition, and the inherent properties of the alloy. Uniform condensation is vital for producing films with consistent electrical and optical properties. Advanced techniques such as substrate rotation and controlled heating are often used to further enhance film uniformity.
Process Control and Optimization
Precise control over the evaporation rate and the deposition environment is critical. Modern deposition systems are equipped with real-time monitoring tools that allow for adjustments in temperature, pressure, and deposition rate. These parameters must be optimized to match the unique properties of the alloy being evaporated. As research in this field advances, techniques such as pulsed evaporation and multi-source co-evaporation are emerging, allowing for even more complex film architectures and improved film quality.
In summary, the alloy evaporation process is a sophisticated technique that transforms a bulk alloy into a finely tuned thin film through a series of controlled physical transitions. This process not only underscores the interplay between material science and advanced engineering but also highlights the critical role of precise control in achieving high-performance thin films.
Chapter 3
Key Techniques in Alloy Evaporation: E-beam and Thermal Evaporation
Two of the most commonly employed techniques for alloy evaporation are electron-beam (E-beam) evaporation and thermal evaporation. Each method has its distinct advantages and challenges, making them suitable for different types of alloys and applications.
Electron-Beam (E-beam) Evaporation
In E-beam evaporation, a high-energy electron beam is directed at the alloy target. The energy from the beam rapidly heats the target material, causing it to evaporate. One of the major advantages of this method is its ability to achieve very high evaporation temperatures, which is essential for materials with high melting points. E-beam evaporation also provides excellent control over the deposition rate, allowing for precise adjustments in film thickness and composition.
However, E-beam evaporation comes with challenges. The high-energy electrons can lead to localized overheating and potential damage to sensitive components in the deposition system. Additionally, the equipment required for E-beam evaporation tends to be more complex and expensive compared to other methods.
Thermal Evaporation
Thermal evaporation, on the other hand, involves resistive heating of the alloy. The material is heated in a controlled manner until it evaporates. This method is simpler in terms of equipment and is generally more cost-effective. Thermal evaporation is widely used for materials that have moderate evaporation temperatures and where ultra-high purity is not the primary concern.
Despite its simplicity, thermal evaporation has its limitations. The process can be less precise in controlling the evaporation rate, and the uniformity of the deposited film may suffer when compared to E-beam techniques. However, for many applications, especially where cost is a significant factor, thermal evaporation remains a popular choice.
Combining Techniques and Innovations
In recent years, hybrid approaches have been developed that combine the benefits of both E-beam and thermal evaporation. These advanced systems allow for better control over the deposition environment and can be tailored to deposit multi-component alloys with enhanced properties. Research is ongoing to further refine these techniques, with innovations focusing on improving deposition rates, reducing energy consumption, and achieving greater film uniformity.
The choice between E-beam and thermal evaporation ultimately depends on the specific requirements of the application, such as the alloy’s physical properties, desired film quality, and budget constraints. By understanding the strengths and limitations of each technique, researchers and engineers can select the optimal method to achieve the best performance in their thin-film applications.
Chapter 4
Advantages of Alloy Evaporation Over Other Deposition Methods
Alloy evaporation presents several advantages compared to alternative deposition methods like sputtering or chemical vapor deposition (CVD). Its unique characteristics make it particularly attractive for applications where film purity, uniformity, and precise control over composition are essential.
High Purity and Composition Control
One of the primary benefits of alloy evaporation is the high purity of the resulting films. Because the process takes place in a high-vacuum environment, the risk of contamination from ambient gases or particulates is significantly reduced. This is especially important in applications such as semiconductor fabrication, where even minor impurities can have a dramatic impact on device performance. Additionally, the ability to control the deposition rate precisely means that the composition of the film can be finely tuned to meet specific requirements.
Superior Film Uniformity
The ballistic transport of vapor atoms in a high-vacuum setting results in films with excellent uniformity. This is particularly advantageous when depositing films on substrates with complex geometries or when consistent film thickness is critical for optical and electrical performance. Uniform films ensure that devices operate reliably and that any variations in properties are minimized.
Versatility and Adaptability
Alloy evaporation is a highly versatile process. It can be used to deposit a wide range of materials, including metals, alloys, and even some dielectric materials. This adaptability makes it suitable for a broad spectrum of applications—from decorative coatings and protective layers to high-performance electronic and optical devices. Moreover, the process parameters can be adjusted to accommodate new and emerging materials, allowing for continuous innovation in material science.
Cost-Effectiveness in Specific Applications
While the initial investment in high-vacuum equipment may be significant, the operational costs of alloy evaporation are often lower than those of some alternative deposition techniques. For instance, processes like CVD require complex chemical precursors and extensive post-deposition processing, which can drive up both cost and production time. In contrast, alloy evaporation systems, once set up, can provide consistent performance with relatively simple maintenance routines.
Energy Efficiency and Scalability
Recent advances in deposition technology have also improved the energy efficiency of the alloy evaporation process. Innovations in heating methods and chamber design have reduced energy consumption while maintaining high deposition rates. This makes the process more environmentally friendly and economically viable for large-scale industrial applications.
In summary, the advantages of alloy evaporation—ranging from high purity and uniformity to adaptability and cost-effectiveness—make it a preferred method in many high-tech manufacturing processes. Its ability to deliver tailored thin films with controlled properties is a major reason why the method continues to be refined and widely adopted in various technological fields.
Chapter 5
Applications of Alloy Evaporation Materials in Industry
The practical applications of alloy evaporation materials span a wide array of industries, demonstrating the versatility and importance of this deposition method. The ability to create thin, uniform, and highly tailored films is key to the performance and longevity of many modern devices.
Microelectronics and Semiconductor Devices
In the microelectronics industry, the deposition of thin metallic films is crucial for fabricating integrated circuits and semiconductor devices. Alloy evaporation provides the high-purity, uniform films required for the intricate features of modern microchips. These films are often used for interconnects, contacts, and barrier layers that protect against diffusion and corrosion. The precise control offered by evaporation techniques is vital for ensuring the performance and reliability of semiconductor devices in applications ranging from consumer electronics to advanced computing systems.
Optical Coatings and Displays
Alloy evaporation is also extensively used in the production of optical coatings. Thin films deposited by this method can enhance reflectivity, reduce glare, or serve as anti-reflective layers on lenses and screens. Transparent conducting oxides like ITO, deposited through controlled alloy evaporation, are essential components in flat-panel displays, touchscreens, and solar cells. These films not only provide excellent optical clarity but also contribute to the electrical performance of the devices.
Aerospace and Automotive Industries
The aerospace and automotive sectors benefit from the use of alloy evaporation materials in various high-performance components. For example, protective coatings deposited via evaporation methods can significantly improve the wear resistance and corrosion protection of engine parts and structural components. The high-temperature stability of certain refractory alloys makes them particularly suitable for these demanding environments, ensuring long-term reliability and performance under extreme conditions.
Biomedical and Sensors
In the biomedical field, thin films created through alloy evaporation are used to fabricate sensors, implantable devices, and diagnostic tools. The biocompatibility and controlled properties of these films are essential for applications such as medical imaging and drug delivery systems. Additionally, the ability to deposit layers with specific electrical and optical characteristics allows for the creation of advanced biosensors capable of detecting minute changes in biological systems.
All these applications illustrate not only the technical versatility of alloy evaporation but also its critical role in advancing technology across multiple domains. As industries continue to demand higher performance and miniaturization, the importance of high-quality thin films produced by alloy evaporation is expected to grow further.
Chapter 6
Advantages of Alloy Evaporation Over Other Deposition Methods
Alloy evaporation presents several advantages compared to alternative deposition methods like sputtering or chemical vapor deposition (CVD). Its unique characteristics make it particularly attractive for applications where film purity, uniformity, and precise control over composition are essential.
High Purity and Composition Control
One of the primary benefits of alloy evaporation is the high purity of the resulting films. Because the process takes place in a high-vacuum environment, the risk of contamination from ambient gases or particulates is significantly reduced. This is especially important in applications such as semiconductor fabrication, where even minor impurities can have a dramatic impact on device performance. Additionally, the ability to control the deposition rate precisely means that the composition of the film can be finely tuned to meet specific requirements.
Superior Film Uniformity
The ballistic transport of vapor atoms in a high-vacuum setting results in films with excellent uniformity. This is particularly advantageous when depositing films on substrates with complex geometries or when consistent film thickness is critical for optical and electrical performance. Uniform films ensure that devices operate reliably and that any variations in properties are minimized.
Versatility and Adaptability
Alloy evaporation is a highly versatile process. It can be used to deposit a wide range of materials, including metals, alloys, and even some dielectric materials. This adaptability makes it suitable for a broad spectrum of applications—from decorative coatings and protective layers to high-performance electronic and optical devices. Moreover, the process parameters can be adjusted to accommodate new and emerging materials, allowing for continuous innovation in material science.
Cost-Effectiveness in Specific Applications
While the initial investment in high-vacuum equipment may be significant, the operational costs of alloy evaporation are often lower than those of some alternative deposition techniques. For instance, processes like CVD require complex chemical precursors and extensive post-deposition processing, which can drive up both cost and production time. In contrast, alloy evaporation systems, once set up, can provide consistent performance with relatively simple maintenance routines.
Energy Efficiency and Scalability
Recent advances in deposition technology have also improved the energy efficiency of the alloy evaporation process. Innovations in heating methods and chamber design have reduced energy consumption while maintaining high deposition rates. This makes the process more environmentally friendly and economically viable for large-scale industrial applications.
In summary, the advantages of alloy evaporation—ranging from high purity and uniformity to adaptability and cost-effectiveness—make it a preferred method in many high-tech manufacturing processes. Its ability to deliver tailored thin films with controlled properties is a major reason why the method continues to be refined and widely adopted in various technological fields.
Chapter 7
Common Materials Used in Alloy Evaporation
The choice of materials for alloy evaporation is vast and depends heavily on the intended application of the thin film. Researchers and industry professionals continually explore new alloy combinations to achieve desired properties such as high conductivity, improved corrosion resistance, or enhanced optical clarity.
Common Materials Used in Alloy Evaporation
Many commonly evaporated alloys are based on metals like aluminum, copper, titanium, and chromium. For example, aluminum alloys are widely used due to their lightweight nature and good conductivity, making them ideal for electronic applications. Titanium alloys, known for their strength and resistance to corrosion, are used in applications ranging from aerospace components to biomedical devices.
Copper-based alloys are popular in applications where high electrical and thermal conductivity is essential. In contrast, chromium alloys are often employed for their hardness and wear resistance. By combining these metals in various proportions, it is possible to create films that exhibit a unique blend of properties tailored for specific industrial needs.
Transparent Conducting Oxides (TCOs)
Another important class of materials in alloy evaporation is transparent conducting oxides. Indium tin oxide (ITO) is a prime example, commonly used in the production of flat-panel displays, solar cells, and touchscreens. The deposition of ITO films via alloy evaporation allows for precise control over the film’s transparency and conductivity, which is critical for optoelectronic applications.
Refractory and High-Temperature Alloys
For applications that require high thermal stability, such as components in aerospace or high-power electronics, refractory alloys are often the material of choice. These alloys typically consist of elements with very high melting points and are engineered to maintain their properties even under extreme conditions. The evaporation of such alloys requires specialized techniques, often involving electron-beam evaporation to achieve the necessary temperatures.
Novel and Composite Alloys
In addition to traditional metals and oxides, researchers are investigating novel composite alloys that combine metals with non-metallic elements to achieve multifunctional properties. These composite materials can offer advantages such as improved adhesion, enhanced mechanical strength, and unique optical characteristics. As the field evolves, the development of these advanced materials continues to push the boundaries of what is achievable with thin-film deposition.
The diversity in material selection not only highlights the versatility of alloy evaporation but also underscores the importance of material science in developing solutions for next-generation applications. As new alloy systems are discovered and existing ones optimized, the scope of alloy evaporation is expected to expand even further, offering innovative solutions for a broad range of technological challenges.
Chapter 8
Applications of Alloy Evaporation Materials in Industry
The practical applications of alloy evaporation materials span a wide array of industries, demonstrating the versatility and importance of this deposition method. The ability to create thin, uniform, and highly tailored films is key to the performance and longevity of many modern devices.
The practical applications of alloy evaporation materials span a wide array of industries, demonstrating the versatility and importance of this deposition method. The ability to create thin, uniform, and highly tailored films is key to the performance and longevity of many modern devices.
Microelectronics and Semiconductor Devices
In the microelectronics industry, the deposition of thin metallic films is crucial for fabricating integrated circuits and semiconductor devices. Alloy evaporation provides the high-purity, uniform films required for the intricate features of modern microchips. These films are often used for interconnects, contacts, and barrier layers that protect against diffusion and corrosion. The precise control offered by evaporation techniques is vital for ensuring the performance and reliability of semiconductor devices in applications ranging from consumer electronics to advanced computing systems.
Optical Coatings and Displays
Alloy evaporation is also extensively used in the production of optical coatings. Thin films deposited by this method can enhance reflectivity, reduce glare, or serve as anti-reflective layers on lenses and screens. Transparent conducting oxides like ITO, deposited through controlled alloy evaporation, are essential components in flat-panel displays, touchscreens, and solar cells. These films not only provide excellent optical clarity but also contribute to the electrical performance of the devices.
Energy and Solar Cells
In the renewable energy sector, alloy evaporation techniques are employed in the fabrication of photovoltaic cells. High-quality, uniform thin films are critical for the efficient conversion of light into electricity. By tailoring the composition and thickness of the evaporated films, manufacturers can optimize the performance of solar cells, enhancing both efficiency and durability.
Aerospace and Automotive Industries
The aerospace and automotive sectors benefit from the use of alloy evaporation materials in various high-performance components. For example, protective coatings deposited via evaporation methods can significantly improve the wear resistance and corrosion protection of engine parts and structural components. The high-temperature stability of certain refractory alloys makes them particularly suitable for these demanding environments, ensuring long-term reliability and performance under extreme conditions.
Biomedical and Sensors
In the biomedical field, thin films created through alloy evaporation are used to fabricate sensors, implantable devices, and diagnostic tools. The biocompatibility and controlled properties of these films are essential for applications such as medical imaging and drug delivery systems. Additionally, the ability to deposit layers with specific electrical and optical characteristics allows for the creation of advanced biosensors capable of detecting minute changes in biological systems.
All these applications illustrate not only the technical versatility of alloy evaporation but also its critical role in advancing technology across multiple domains. As industries continue to demand higher performance and miniaturization, the importance of high-quality thin films produced by alloy evaporation is expected to grow further.
Chapter 9
Challenges and Limitations of Alloy Evaporation
Despite its many advantages, alloy evaporation faces several challenges that researchers and engineers must overcome to further optimize the process and expand its applications.
Process Complexity and Equipment Costc
One of the primary challenges of alloy evaporation is the complexity of the deposition process itself. Maintaining a high-vacuum environment, precise temperature control, and uniform deposition over large areas requires sophisticated equipment. The initial cost of setting up such systems can be significant, and the ongoing maintenance demands specialized expertise. This high barrier to entry can limit the adoption of the technology, especially in smaller-scale operations or research laboratories with budget constraints.
Material-Specific Challenges
Each alloy behaves differently under evaporation conditions, and factors such as melting point, vapor pressure, and reactivity must be carefully balanced. Some alloys may form undesirable compounds during evaporation, or their components may evaporate at different rates, leading to compositional inconsistencies in the deposited film. Overcoming these material-specific challenges requires detailed knowledge of the alloy’s behavior and often involves extensive trial and error to optimize the process parameters.
Film Uniformity and Thickness Control
Achieving uniform film thickness across a substrate is critical for many applications but can be challenging when dealing with complex geometries or large-area substrates. Variations in substrate temperature, distance from the evaporation source, and deposition angle can all contribute to non-uniform films. Advanced techniques, such as substrate rotation and the use of collimators, are often necessary to mitigate these issues, yet they add another layer of complexity to the deposition process.
Scalability and Reproducibility
While alloy evaporation is highly effective for laboratory-scale experiments and prototype development, scaling the process up for industrial production poses its own set of challenges. Reproducibility is essential for commercial applications, and slight variations in process conditions can result in significant differences in film properties. Developing robust, scalable processes that maintain consistency across large production runs is an ongoing area of research.
Environmental and Safety Considerations
The high-vacuum and high-temperature conditions required for alloy evaporation can present environmental and safety challenges. Energy consumption, the handling of high-power equipment, and the management of hazardous materials all need to be addressed through careful process design and safety protocols. As industry standards become increasingly strict regarding environmental impact and worker safety, the development of greener and safer deposition methods is a key focus.
Addressing these challenges is essential for the continued advancement and broader adoption of alloy evaporation technologies. Ongoing research is focused on refining process parameters, developing new equipment designs, and exploring alternative materials that can help overcome these limitations while maintaining or enhancing film quality.
Chapter 10
Recent Innovations in Alloy Evaporation Technologies
The field of alloy evaporation is not static; it is constantly evolving as new research and technological advances pave the way for improved processes and novel applications. Several recent innovations have significantly enhanced the capabilities of alloy evaporation, making it more efficient, versatile, and adaptable to emerging technological demands.
Advanced Deposition Techniques
Recent developments in deposition techniques include the integration of real-time monitoring and feedback systems. These systems use sensors to continuously track parameters such as deposition rate, chamber pressure, and substrate temperature. This data is used to adjust process parameters on the fly, ensuring optimal film quality and consistency. Innovations such as pulsed evaporation—where the vapor flux is modulated in short bursts—have also shown promise in reducing thermal stress on both the target material and the substrate, thereby enhancing film uniformity.
Multi-Source and Co-Evaporation Systems
To overcome issues related to compositional control, new multi-source evaporation systems have been developed. These systems allow for the simultaneous evaporation of multiple materials from separate sources, enabling the creation of complex alloy films with finely tuned compositions. Co-evaporation techniques are particularly valuable when producing composite films that require a precise balance between different elements. This approach has opened up possibilities in creating multifunctional coatings with properties that cannot be achieved through single-source evaporation alone.
Nanostructured and Graded Films
Another innovative area is the development of nanostructured and compositionally graded films. By controlling the evaporation rate and the arrangement of material sources, researchers can create films with nanoscale features or a gradual change in composition across the thickness of the film. These structures have significant implications for optical and electronic applications, as they can lead to improved performance characteristics such as enhanced conductivity, superior light absorption, or increased catalytic activity.
Automation and Process Integration
Automation in alloy evaporation has also seen considerable progress. Modern deposition systems are increasingly integrated with software that automates many aspects of the process, from substrate handling to process optimization. This not only improves reproducibility and scalability but also reduces the likelihood of human error during deposition. Furthermore, the integration of alloy evaporation systems with other manufacturing processes—such as lithography and etching—facilitates the production of complex multilayer structures in a streamlined, cost-effective manner.
Sustainable and Energy-Efficient Processes
With growing emphasis on sustainability, researchers are also exploring ways to reduce the energy consumption and environmental impact of the alloy evaporation process. Advances in power management, the use of more efficient heating sources, and improved chamber designs that minimize energy loss are helping to make alloy evaporation more environmentally friendly. These innovations are critical for industries seeking to meet stricter environmental regulations while maintaining high production standards.
The recent innovations in alloy evaporation technologies not only address some of the long-standing challenges in the field but also open up new avenues for research and application. As these technologies mature, they are expected to significantly enhance the performance and reliability of thin-film deposition processes, thereby supporting the development of next-generation electronic, optical, and energy devices.
Chapter 11
Future Trends and Opportunities in Alloy Evaporation
Looking forward, the field of alloy evaporation materials is poised for significant growth, driven by continuous technological advancements and evolving market demands. Several key trends and opportunities are emerging that will likely shape the future landscape of this technology.
Integration with Nanotechnology
One of the most exciting future directions is the integration of alloy evaporation techniques with nanotechnology. As devices become smaller and more complex, the ability to deposit ultra-thin, highly uniform films at the nanoscale becomes increasingly important. Future research is expected to focus on refining evaporation processes to achieve even better control over film thickness and composition at the nanometer level. This integration could lead to breakthroughs in semiconductor devices, sensors, and other applications where precision at the nanoscale is paramount.
Development of Smart and Adaptive Materials
The next frontier in alloy evaporation is the development of smart and adaptive materials. These are materials whose properties can change in response to external stimuli such as temperature, light, or electrical fields. By using alloy evaporation to create films with graded or tunable compositions, researchers hope to develop surfaces and coatings that can adapt to their environment. Such materials have potential applications in areas ranging from self-healing coatings to adaptive optics and responsive sensors.
Enhanced Process Automation and Artificial Intelligence
As automation technologies and artificial intelligence (AI) become more sophisticated, their integration with alloy evaporation systems will likely lead to significant improvements in process efficiency and product quality. AI-driven process control systems can analyze real-time data and optimize deposition parameters, ensuring consistent film quality even in large-scale manufacturing. This trend toward greater automation not only promises higher throughput but also reduces the operational complexity and potential for human error.
Focus on Sustainability and Energy Efficiency
Sustainability is becoming a central focus in many industrial processes, and alloy evaporation is no exception. Future research will likely concentrate on developing energy-efficient deposition systems and greener processes. Innovations such as alternative heating methods, improved vacuum technologies, and better material recycling strategies are expected to reduce the environmental footprint of alloy evaporation while maintaining or enhancing performance.
Broadening Industrial Applications
The continuous improvement in alloy evaporation technologies is expected to open up new markets and applications. As the demand for high-performance thin films grows in sectors like renewable energy, aerospace, and biomedical devices, the versatility and precision of alloy evaporation will be increasingly valued. In particular, the ability to produce multilayered, multifunctional films can lead to the development of devices that are more efficient, durable, and capable of meeting the rigorous demands of modern technology.
Collaborative Research and Global Innovation
The future of alloy evaporation materials will also be driven by collaborative research efforts across academia, industry, and government institutions. International collaborations and research consortia are expected to accelerate the pace of innovation, leading to breakthroughs that can be rapidly translated into commercial applications. These collaborations will be vital in addressing the technical challenges of alloy evaporation and in exploring new materials and process innovations that can drive the next wave of technological advancement.
In summary, the future of alloy evaporation materials is bright, with numerous opportunities for innovation and application growth. As technology continues to evolve, the ability to deposit tailored, high-quality films will remain critical to the advancement of many modern industries. By staying at the forefront of process improvements, material science breakthroughs, and integration with emerging technologies, the field of alloy evaporation is set to play a pivotal role in shaping the future of thin-film technology.
Chapter 12
Frequently Asked Questions
1. How should I store lithium evaporation pieces?
To prevent oxidation, lithium evaporation pieces should be stored in oil or an argon inert atmosphere. After use, any remaining pieces should be repackaged in oil, sealed tightly, and kept in a cool, dry place.
2. How do I clean oil-covered evaporation pieces?
Evaporation materials that react with air or moisture are often stored in low-viscosity mineral oil. Before use, this oil must be thoroughly removed using appropriate solvents to avoid contamination in the vacuum system and during thin-film deposition processes.
3. What is the recommended method for thermally evaporating silicon dioxide?
It’s advisable to heat the substrate to 350°C before thermally evaporating silicon dioxide. A deposition rate of approximately 2 angstroms per second can be achieved at an evaporation temperature around 1,200°C. Maintaining an oxygen partial pressure of 1-2 x 10⁻⁴ Torr is recommended to produce smooth, amorphous films. Replace the material when it becomes dark or black.
4. How can I effectively evaporate aluminum?
Aluminum can be evaporated using either electron-beam (e-beam) or thermal evaporation techniques. In thermal evaporation, a thin-width, thick-gauge, high-current tungsten boat (e.g., EVS20A015W) can be used. This setup allows deposition rates exceeding 30 angstroms per second and film thicknesses over 3,000 angstroms per run. Typically, such boats can be used for multiple runs (approximately four) with two ¼” x ¼” pellets per run. It’s crucial not to disturb the boat when venting the chamber for reloading, as the boat becomes brittle after initial use.
5. What type of crucible should I use for thermally evaporating nickel/iron (81/19 wt%) alloys?
Nickel/iron alloys can be evaporated from an aluminum oxide crucible. However, due to differences in thermal expansion coefficients between the alloy and the crucible, the crucible may only last for one run. Additionally, the material tends to settle at the bottom, requiring higher temperatures to achieve evaporation, which may lead to contamination from the crucible and heater materials.
6. Why does a tungsten boat break during the thermal evaporation of nickel/iron (81/19 wt%) alloys?
Both nickel and iron can react with refractory metals when in liquid form, making it challenging to evaporate them from a tungsten boat. As the boat heats and the alloy melts, it can alloy with the tungsten, causing the boat to become brittle and crack, often within a single run.
7. What type of crucible liner should I use for e-beam evaporating tungsten?
For e-beam evaporation of tungsten, using a Fabmate crucible liner is recommended. Alternatively, tungsten can be evaporated directly from the copper hearth of the e-gun. Some users prefer pre-machined slugs that fit directly into the hearth pocket, offering ease of use and excellent packing density.
8. How do I evaporate cobalt?
Cobalt can be evaporated using thermal or e-beam evaporation, with e-beam being the preferred method. Cobalt tends to alloy with refractory metals; attempting thermal evaporation from a tungsten boat often results in the boat becoming brittle and cracking due to alloy formation during heating.
9. How can I evaporate a niobium-tantalum alloy using e-beam evaporation?
Evaporating niobium-tantalum alloys via e-beam evaporation can be challenging. Using a graphite crucible and applying 1kW power may not yield evaporation, as the heat can dissipate within the melt pool. It’s essential to consider proper cooling and maintaining low pressure to achieve successful evaporation.
10. Which crucible materials are suitable for evaporating metals like aluminum, silver, gold, and copper?
For metals such as aluminum, silver, gold, and copper, ceramic or quartz crucibles are commonly used to prevent contamination and ensure high-purity deposition. Graphite crucibles can also be suitable due to their high thermal conductivity, provided the evaporation temperatures are controlled to avoid adverse reactions.
11. Can liquid metal alloys like indium-gallium (InGa) evaporate at room temperature under high vacuum conditions?
Liquid metal alloys such as InGa, which are liquid at room temperature and atmospheric pressure, may evaporate under high vacuum conditions (e.g., 10⁻⁷ Torr). It’s crucial to assess the enthalpy of vaporization for the specific alloy to determine the evaporation rate and potential for contaminating vacuum systems.
12. Are there systems capable of co-deposition using dual e-beam sources or a combination of e-beam and thermal sources?
Yes, co-deposition systems utilizing dual e-beam sources or a combination of e-beam and thermal sources exist. These systems allow for precise control over the composition of thin-film alloys, enabling the deposition of materials with tailored properties.
Chapter 13
Conclusion: The Impact of Alloy Evaporation Materials on Modern Technology
Alloy evaporation materials play a pivotal role in modern thin-film deposition, providing high-purity, uniform coatings essential for advanced applications across microelectronics, optics, energy, and aerospace. Their ability to precisely control film composition and thickness enables the fabrication of high-performance devices, although challenges such as process complexity and equipment cost still need to be managed.
Looking ahead, innovations in nanotechnology, real-time monitoring, and AI-driven process control are set to drive significant advancements in alloy evaporation. With an increasing focus on sustainability and scalable manufacturing, ongoing collaborative research is expected to overcome current limitations, ensuring that alloy evaporation remains a key technology in shaping the future of high-performance thin-film applications.