Boat Sources
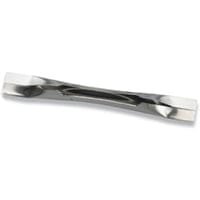
Canoe Boat Sources
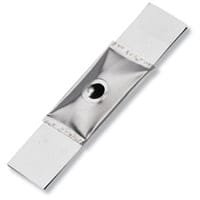
Covered Boat Sources
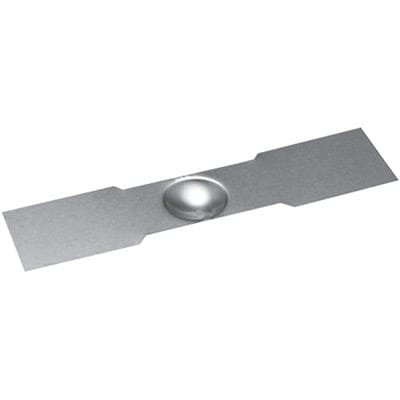
Dimple Boat Sources
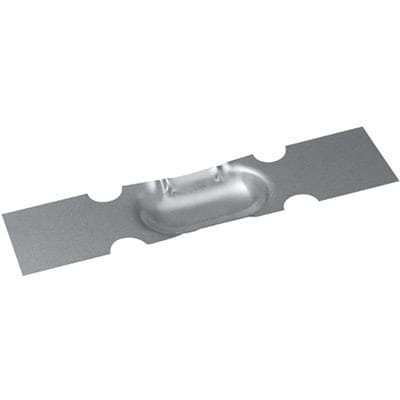
Notched Boat Sources
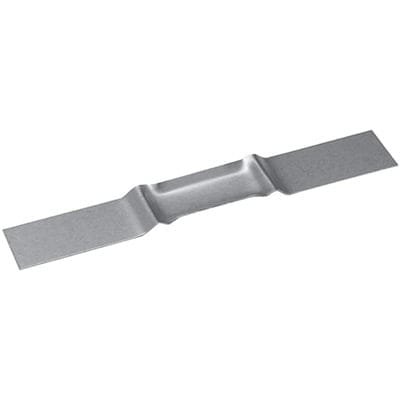
Flat Boat Sources
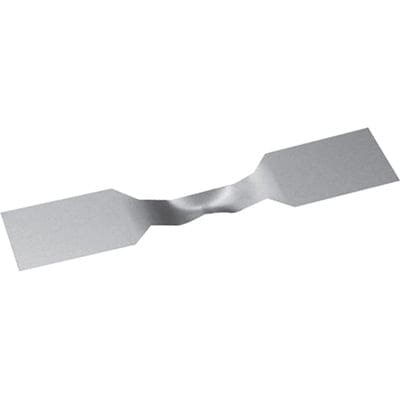
Pan Trough Boat Sources
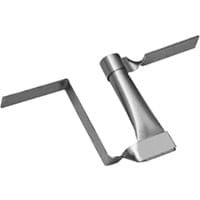
Boat Sources - Closed End Tube Heaters
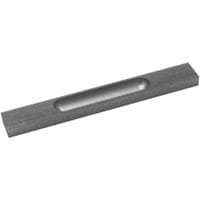
Boat Sources - Slab Heaters
The Comprehensive Guide to Boat Sources in Thermal Evaporation Processes
This comprehensive guide explores the pivotal role of boat sources in thermal evaporation processes, which are integral to thin film deposition across high-tech industries such as semiconductors, optics, and solar energy. Boat sources—fabricated from refractory metals like tungsten, tantalum, and molybdenum, often enhanced with alumina coatings—serve as the heating elements that vaporize materials under high-vacuum conditions. The article examines the working principles of these sources, highlights key selection criteria including material compatibility, operating temperature, and power supply matching, and discusses various configurations such as standard, custom, folded, and covered boats. Additionally, the guide addresses common challenges like thermal shock, material migration, and contamination, and provides maintenance and troubleshooting best practices to extend the operational lifespan of the sources. With detailed insights into applications, advantages, and future trends, this resource serves as an essential reference for optimizing deposition processes and achieving high-quality, uniform thin films.
Table of Contents
Chapter 1
Introduction
In the field of thin film deposition, thermal evaporation is one of the most commonly used physical vapor deposition (PVD) techniques. At the heart of many of these systems are specialized components known as evaporation boat sources. These boat sources—also referred to as thermal evaporation boats, vacuum evaporation boats, or simply boat sources—are designed to hold and heat evaporant materials so that they vaporize and deposit uniformly onto a substrate. The right boat source is crucial for producing high-quality, uniform thin films that are essential for applications in semiconductors, optical coatings, solar cells, and various high-tech industries.
This comprehensive guide will explore what boat sources are, how they work, and why they are indispensable for thermal evaporation processes. We will cover topics from materials selection and design considerations to performance parameters and troubleshooting common issues. Throughout this guide, we incorporate key search terms—such as “thermal evaporation boats,” “tungsten evaporation boat,” “tantalum evaporation boat,” “molybdenum evaporation boat,” “alumina coated evaporation boat,” “resistive evaporation source,” “vacuum evaporation boat,” “thin film deposition boat,” “boat source selection,” “high temperature evaporation boat,” and “custom evaporation boat”—as well as answers to frequently asked questions to help you understand the subject matter in depth.
Chapter 2
What Are Boat Sources?
Definition and Function
An evaporation boat source is a boat-shaped container that holds the source material (evaporant) used in a thermal evaporation process. The boat is typically made from refractory metals such as tungsten, tantalum, or molybdenum—materials that can withstand extreme temperatures without melting or degrading. In many cases, the boat may be alumina coated to prevent wetting or unwanted chemical reactions between the boat material and the evaporant. During operation, the boat source is heated—usually by resistive heating (making it a resistive evaporation source) or electron-beam heating—to temperatures high enough to cause the material to evaporate. Under high-vacuum conditions, the evaporated atoms travel to a cooler substrate where they condense, forming a thin film.
Boat sources are essential components in vacuum deposition systems. Their design and material properties allow for:
High temperature operation
Efficient and uniform evaporation of material
Compatibility with a wide range of evaporants
Precise control over deposition rates and film thickness
Keywords Overview
In the world of thermal evaporation, certain key terms are frequently searched:
Evaporation boat sources
Thermal evaporation boats
Tungsten evaporation boat
Tantalum evaporation boat
Molybdenum evaporation boat
Alumina coated evaporation boat
Resistive evaporation source
Vacuum evaporation boat
Thin film deposition boat
Boat source selection
High temperature evaporation boat
Custom evaporation boat
These keywords represent the core attributes and materials used in designing evaporation boats and guide researchers and engineers in selecting the appropriate source for their specific deposition process.
Chapter 3
How Do Boat Sources Work?
The Basic Principle
Boat sources function based on a simple yet effective physical process. When an electric current is passed through the boat (which acts as a resistive heating element), it heats up to a predetermined temperature. This heat is then transferred to the evaporant material placed in the boat. As the temperature rises, the vapor pressure of the material increases until it reaches a point where the material begins to evaporate. The vapor then travels through the vacuum chamber and condenses on the cooler substrate, forming a thin, uniform film.
This process is highly dependent on several factors:
Temperature: Sufficient heating must be provided to achieve the required vaporization of the material.
Vacuum Conditions: High vacuum minimizes collisions with background gases, ensuring that evaporated atoms travel in a straight line to the substrate.
Power Supply Parameters: The voltage and current supplied to the boat source must be matched to the source’s requirements. For example, tungsten boats typically operate at around 1800°C, tantalum boats around 1600°C, and molybdenum boats around 1400°C.
Resistive Versus Electron-Beam Heating
Resistive Versus Electron-Beam Heating
Sintering is a heat treatment process used to bond the pressed metal particles together. During sintering, the green compact is heated to a temperature below its melting point, causing the particles to bond through diffusion mechanisms. Sintering enhances the mechanical properties of the material, such as strength and durability, by:
- Reducing porosity.
- Increasing particle cohesion.
- Enhancing the overall structural integrity of the part.
Modern sintering techniques also include microwave sintering and spark plasma sintering, which allow for more controlled and energy-efficient processing.
FAQ: How Do Thermal Evaporation Sources Work?
The answer is that thermal evaporation sources heat an evaporant material by passing an electrical current through a resistive element. This heating raises the temperature of the evaporant until it vaporizes. The vapor then travels through a vacuum chamber and condenses onto a substrate to form a thin film. This process relies on precise control of temperature, power, and vacuum conditions to ensure uniform film deposition.
Chapter 4
Materials Used in Boat Sources
Refractory Metals: Tungsten, Tantalum, and Molybdenum
Boat sources are typically constructed from refractory metals due to their ability to withstand extreme temperatures and harsh conditions. The most common materials include:
Tungsten: Known for its extremely high melting point (3422°C) and excellent thermal conductivity, tungsten is the most popular choice for high-temperature evaporation processes. Tungsten evaporation boats are widely used when very high operating temperatures are required.
Tantalum: With a melting point around 3017°C, tantalum offers high resistance to corrosion and chemical reactivity. Tantalum evaporation boats are particularly useful for materials that might react with tungsten.
Molybdenum: Molybdenum has a melting point of 2623°C and is valued for its stability and lower operating temperatures (typically around 1400°C). Molybdenum evaporation boats are preferred when processing materials that require a slightly lower temperature range.
Alumina Coated Boats
For reactive or corrosive materials, an alumina coated evaporation boat is often used. The alumina coating (Al₂O₃) prevents the evaporant from wetting the metal surface, which reduces unwanted chemical reactions and prolongs the life of the boat. This is especially beneficial when evaporating materials like gold, aluminum, or other materials that might otherwise degrade the boat.
FAQ: What Materials Are Commonly Used to Fabricate Evaporation Boats?
The answer is that evaporation boats are typically made from refractory metals such as tungsten, tantalum, and molybdenum. Often, these boats are coated with materials like alumina to improve chemical resistance and prevent wetting by the evaporant.
Chapter 5
Types of Boat Sources and Their Configurations
Boat sources come in various designs and configurations, each tailored to specific process requirements and materials. Some common types include:
Standard Boat Sources
These are the most common type of evaporation boats. They are designed to provide a large surface area for the evaporant and are available in standard sizes and shapes. Standard boats are used in a wide range of applications where uniform thin film deposition is needed.
Custom and Folded Boats
For specialized applications or space-constrained systems, custom evaporation boats and folded boats are available. These designs can be tailored to specific dimensions or deposition requirements, offering flexibility for unique processing needs.
Covered Boat Sources
Covered boats, sometimes referred to as “covered evaporation boats,” provide additional control over the deposition process by limiting the direct exposure of the evaporant to the environment. This can be important for preventing contamination and achieving highly uniform coatings.
Dimple and Notched Boats
Some boat sources feature dimpled or notched designs. These features help to concentrate the heat in the center of the boat, ensuring more uniform melting of the material. Notched boats can also help control the flow of the evaporant, reducing migration to undesired areas.
FAQ: What Are the Advantages of Using Boat Sources in Evaporation Processes?
Boat sources offer controlled deposition of materials, high-temperature capability, and uniform thin film formation. Their design enables precise control over film thickness and minimizes contamination. Additionally, the variety of available configurations—including standard, folded, and alumina coated boats—ensures that there is a solution tailored to almost every evaporation requirement.
Chapter 6
Key Factors in Boat Source Selection
Choosing the right boat source is critical to achieving optimal performance in thermal evaporation. Here are several key factors that must be considered:
1. Evaporant Material Compatibility
The first consideration is the material you wish to evaporate. The boat’s material must be compatible with the evaporant to avoid unwanted reactions. For instance, if the evaporant is highly reactive, an alumina coated boat may be necessary to prevent alloying or corrosion.
2. Operating Temperature
Different materials require different operating temperatures to evaporate efficiently.
Tungsten boats are generally used for processes needing temperatures around 1800°C.
Tantalum boats often operate near 1600°C.
Molybdenum boats are typically used for temperatures around 1400°C.
It is essential to match the source’s operating temperature with the requirements of the evaporant.
3. Power Supply Parameters
Boat sources must be paired with a power supply that meets the voltage and current requirements needed to reach the desired temperature. A mismatch here could lead to inefficient evaporation or premature failure of the boat.
4. Capacity and Geometry
The geometry of the boat affects the evaporation rate and uniformity of the thin film. Boats with larger surface areas can hold more evaporant, which is useful for thicker films, while boats with a dimpled or notched design may provide more controlled evaporation for smaller quantities.
5. Process Requirements
Consider the specific requirements of your deposition process, such as the direction of evaporation (upward, downward, or lateral), the required film thickness, and the uniformity of deposition across the substrate.
6. Customization Needs
For specialized applications, custom evaporation boats may be necessary. These boats can be designed with specific dimensions, coatings, or configurations to meet unique process requirements.
FAQ: How Do I Choose the Right Evaporation Boat for My Process?
The answer involves evaluating the evaporant material’s properties, operating temperature, available power supply, boat geometry, and overall process requirements. Matching these factors ensures that the boat source will perform reliably and produce high-quality thin films.
Chapter 7
Applications of Boat Sources
Boat sources are integral components in many industrial and research applications. Some key areas include:
Semiconductor Manufacturing
In the semiconductor industry, boat sources are used to deposit metal contacts, interconnects, and other thin films required for integrated circuits. The precise control afforded by these sources is essential for creating the fine structures needed in microelectronics.
Optical Coatings
Optical coatings—used to enhance the transmission, reflection, or absorption properties of lenses and mirrors—are often produced using evaporation techniques. Boat sources allow for the deposition of highly uniform, pure films critical for high-performance optical components.
Solar Cells and Photovoltaics
For various electronic devices—from displays to sensors—precise thin films are necessary. Boat sources help deposit materials such as metals, oxides, and semiconductors onto substrates with high uniformity, ensuring optimal electronic performance.
Materials Research
In research laboratories, boat sources are used in physical vapor deposition (PVD) experiments. They allow researchers to deposit thin films for the study of material properties, the development of novel coatings, and the exploration of nanotechnology.
FAQ: What Applications Are Thermal Evaporation Sources Used For?
Thermal evaporation sources are used in optical coatings, semiconductor manufacturing, solar cell production, and various electronics and materials research applications. Their versatility and precision make them ideal for depositing uniform, high-purity thin films across a wide range of industries.
Chapter 8
Advantages and Challenges of Boat Sources
Advantages
Boat sources offer several benefits that have made them a popular choice for thermal evaporation processes:
Versatility: They can accommodate a wide range of evaporant materials and are available in various shapes, sizes, and configurations.
High Purity Films: By using high-quality source materials and controlled deposition parameters, boat sources can produce films with minimal impurities.
Precise Control: They allow for accurate control of film thickness and deposition rates, which is essential for applications where even minor variations can affect device performance.
Cost-Effective: Compared to some alternative deposition methods, thermal evaporation using boat sources is relatively simple and economical.
Customization: Many suppliers offer custom evaporation boats tailored to specific process needs.
Challenges
Despite their many advantages, boat sources also present some challenges:
Material Compatibility: Not all materials are compatible with every boat type. Reactive or corrosive evaporants may require coated or specially designed boats.
Thermal Shock: Rapid heating or cooling can cause boat cracking or degradation. It is essential to ramp temperatures gradually.
Power Matching: Ensuring that the boat’s voltage and current requirements match the available power supply is critical. A mismatch can lead to suboptimal performance.
Uniformity: Achieving uniform deposition over large substrates can be challenging due to geometric factors and shadowing effects.
Limited Reusability: While many boats can be reused if maintained properly, prolonged use—especially with corrosive materials—can necessitate frequent replacement.
FAQ: What Are the Advantages of Using Thermal Evaporation Sources?
the answer is that they offer high deposition rates, excellent directionality, and uniform thin film formation. They are relatively simple and cost-effective compared to more complex methods, making them widely applicable in various industries.
Chapter 9
Technical Considerations and Optimization
Matching Power Supply and Boat Source
A critical factor in the successful operation of evaporation boat sources is matching the power supply to the boat’s specifications. The voltage and current ratings of the source must align with what the power supply can deliver to achieve the required operating temperature. For instance, tungsten boats may require higher current and voltage to reach 1800°C compared to tantalum or molybdenum boats.
Temperature Control and Monitoring
Precise temperature control is vital for uniform evaporation. Process engineers often use power requirement tables and temperature monitoring tools to ensure that the boat source reaches and maintains the desired temperature throughout the deposition process. Consistent temperatures help ensure that the evaporant vaporizes uniformly and that the resulting film has consistent thickness and properties.
Process Geometry and Film Uniformity
The design of the boat source—including its shape, size, and whether it is coated (e.g., with alumina)—affects how evenly the evaporant is distributed. For applications requiring very thin films or precise deposition patterns, choosing the right boat source geometry is essential. Engineers may opt for dimpled or notched boat sources to focus the heat and control material migration.
Preventing Thermal Shock
Thermal shock can lead to cracks or premature failure of the boat. To mitigate this risk, the heating process must be gradual. Many evaporation systems are designed to ramp up and down slowly, allowing the boat material to expand and contract uniformly without stress.
FAQ: What Are the Main Types of Thermal Evaporation Sources?
the response is that there are resistive evaporation sources (which include boat sources, filaments, and baskets), electron-beam evaporation sources, and flash evaporation sources. Each type uses a different heating mechanism to vaporize the source material, and boat sources remain one of the most popular due to their simplicity and versatility.
Chapter 10
Technical Considerations and Optimization
Matching Power Supply and Boat Source
A critical factor in the successful operation of evaporation boat sources is matching the power supply to the boat’s specifications. The voltage and current ratings of the source must align with what the power supply can deliver to achieve the required operating temperature. For instance, tungsten boats may require higher current and voltage to reach 1800°C compared to tantalum or molybdenum boats.
Temperature Control and Monitoring
Precise temperature control is vital for uniform evaporation. Process engineers often use power requirement tables and temperature monitoring tools to ensure that the boat source reaches and maintains the desired temperature throughout the deposition process. Consistent temperatures help ensure that the evaporant vaporizes uniformly and that the resulting film has consistent thickness and properties.
Process Geometry and Film Uniformity
The design of the boat source—including its shape, size, and whether it is coated (e.g., with alumina)—affects how evenly the evaporant is distributed. For applications requiring very thin films or precise deposition patterns, choosing the right boat source geometry is essential. Engineers may opt for dimpled or notched boat sources to focus the heat and control material migration.
Preventing Thermal Shock
Thermal shock can lead to cracks or premature failure of the boat. To mitigate this risk, the heating process must be gradual. Many evaporation systems are designed to ramp up and down slowly, allowing the boat material to expand and contract uniformly without stress.
FAQ: What Are the Main Types of Thermal Evaporation Sources?
the response is that there are resistive evaporation sources (which include boat sources, filaments, and baskets), electron-beam evaporation sources, and flash evaporation sources. Each type uses a different heating mechanism to vaporize the source material, and boat sources remain one of the most popular due to their simplicity and versatility.
Chapter 11
Customization and Special Configurations
Custom Evaporation Boats
For specialized applications, standard boat sources may not meet all process requirements. Custom evaporation boats can be fabricated to precise dimensions and with specific coatings to match unique deposition conditions. For example, a customer might require a custom boat with a particular trough depth or a unique alumina coating thickness to optimize performance with a reactive evaporant.
Folded Boats and Covered Boats
Folded boat designs and covered boats provide additional benefits in certain applications. Folded boats can be used in systems with limited space, while covered boats help reduce unwanted deposition on chamber components by confining the evaporant to a designated area. These configurations help improve film uniformity and reduce contamination.
FAQ: Can Evaporation Boats Be Reused?
The answer is yes—evaporation boats can be reused if they remain in good condition, are free from cracks, and have been properly cleaned. However, the reusability depends on factors such as the corrosiveness of the evaporant, the heating cycles, and maintenance practices. Boats that show significant wear or damage should be replaced to maintain process quality.
Chapter 12
Maintenance, Troubleshooting, and Lifespan
Routine Inspection and Cleaning
Regular maintenance of evaporation boat sources is essential to ensure long-term performance. After each deposition cycle, it is critical to inspect the boat for any signs of degradation, such as cracks, warping, or coating buildup. Cleaning the boat helps remove any residual evaporant, which might affect future depositions.
Troubleshooting Common Issues
Some common issues with boat sources include:
Cracking or Fracturing: Often due to thermal shock. This can be mitigated by controlled heating and cooling cycles.
Contamination: If the boat is not cleaned properly, residual materials can contaminate subsequent films.
Non-Uniform Deposition: Variations in boat geometry or improper alignment with the substrate can lead to uneven film thickness.
Corrosion and Alloying: For reactive materials, using an uncoated boat may result in alloying between the boat and the evaporant. In such cases, an alumina coated evaporation boat is recommended.
FAQ: What Is the Typical Lifespan of an Evaporation Boat?
The lifespan varies based on the boat material, operating conditions, and maintenance practices. Boats made of refractory metals such as tungsten, tantalum, and molybdenum are generally more durable. With proper handling, cleaning, and controlled thermal cycling, evaporation boats can be used for many deposition cycles; however, signs of wear such as cracking or excessive material buildup indicate it is time for a replacement.
Chapter 13
Applications Across Industries
Semiconductor and Microelectronics
In semiconductor manufacturing, the deposition of metal layers, dielectric films, and other materials requires the precise control offered by boat sources. These processes demand high purity and uniformity to ensure the performance and reliability of integrated circuits. The ability to control film thickness down to the nanometer scale is crucial for modern microelectronics.
Optical Coatings
Optical coatings are critical in devices such as lenses, mirrors, and displays. Evaporation boat sources allow for the deposition of highly uniform thin films that can enhance or modify the optical properties of a substrate. For instance, anti-reflective coatings and high-reflectivity mirrors are often produced using thermal evaporation processes that rely on the precise operation of boat sources.
Solar Cell Production
The renewable energy industry, particularly solar cell manufacturing, also benefits from evaporation boat sources. Thin film deposition is used to apply semiconductor layers on substrates, and the uniformity and purity of these films directly impact the efficiency of solar cells. Boat sources made of tungsten, tantalum, or molybdenum are chosen based on the specific materials being deposited and the required operating temperatures.
Materials Research and Nanotechnology
Research laboratories frequently use evaporation sources to deposit thin films for experimental studies. In materials science and nanotechnology, the ability to create high-quality, controlled thin films is essential for the development of new materials and coatings. Boat sources provide researchers with the versatility to experiment with a wide range of materials under different conditions.
FAQ: What Applications Are Thermal Evaporation Sources Used For?
Thermal evaporation sources are employed in the production of optical coatings, semiconductor devices, solar cells, and various electronic components. They are also critical in research settings where the deposition of high-purity thin films is necessary for the study of material properties.
Chapter 14
Conclusion
Boat sources are a vital element in the thermal evaporation process, enabling the precise deposition of high-quality thin films across a variety of industries. Whether it’s a tungsten evaporation boat, tantalum evaporation boat, or molybdenum evaporation boat, these components are engineered to withstand extreme temperatures, ensure uniform material deposition, and deliver excellent performance in vacuum conditions.
Key factors in selecting the right boat source include compatibility with the evaporant material, operating temperature, power supply matching, and the specific process geometry required for the desired film properties. With options ranging from standard boat sources to specialized alumina coated evaporation boats and custom configurations, users have a broad array of tools at their disposal to optimize thin film deposition.
Through careful maintenance, proper process control, and regular troubleshooting, evaporation boat sources can provide consistent and reliable performance, ensuring that deposition processes meet the stringent requirements of modern manufacturing and research. As technological advancements continue to drive innovation in materials science and thin film deposition, the role of boat sources will only grow more critical.
This guide has incorporated key search terms and answered frequently asked questions to help you navigate the complexities of boat sources. From understanding how they work to selecting the right material and configuration for your needs, this comprehensive resource serves as an essential reference for anyone involved in thermal evaporation processes.
Whether you are working in semiconductor manufacturing, optical coatings, solar cell production, or materials research, choosing the right evaporation boat can significantly impact the efficiency, quality, and reliability of your deposition process. With ongoing innovations in material coatings and automation, the future of boat sources in thermal evaporation looks promising—enabling improved performance and expanding the capabilities of thin film deposition technologies.
By staying informed about the latest developments and best practices in evaporation source selection and maintenance, engineers and researchers can continue to push the boundaries of what is possible in thin film deposition, driving progress in high-tech industries around the world.