Metal Powder
Understanding Metal Powders: Products, Processes, and Applications
Metal powders are finely divided metals that serve as the foundation for a host of advanced manufacturing techniques. Their unique properties make them indispensable in industries ranging from aerospace to automotive, electronics, and even additive manufacturing. This article explores what metal powders are, how they are produced and processed, their myriad applications, and the important safety concerns they pose. We also address specific questions such as: “What is iron metal powder used for?”, “What is metal powder used for?”, “Is metal powder hazardous?”, “What is the powder that burns through metal?”, “Can thermite destroy steel?”, and “What metal powders are explosive?”
Table of Contents
Chapter 1
What Are Metal Powders?
Metal powders are materials made up of microscopic particles of metals. They can be produced from almost any metal, including iron, aluminum, copper, nickel, titanium, and even precious metals. The particle sizes can vary from a few micrometers to hundreds of micrometers, depending on the application. The properties of metal powders—such as particle size distribution, morphology, purity, and surface area—can be carefully controlled during production to meet specific industry needs.
Production Methods
The most common methods to produce metal powders include:
- Atomization: A molten metal stream is broken up into droplets that rapidly solidify into powder particles. Gas atomization and water atomization are common variants.
- Mechanical Milling: This method involves grinding or milling a solid metal into fine particles using high-energy ball mills or other milling equipment.
- Chemical Reduction: Metal oxides or salts are reduced chemically to form pure metal powders. This method is often used for producing extremely fine and pure powders.
- Electrolysis: Metal powders can also be produced by electrolytic deposition where metals are precipitated from a solution onto a substrate and then collected in powder form.
The choice of production method is influenced by the intended application, the desired purity, and the cost-effectiveness of the process.
Chapter 2
Metal Powder Products and the Global Market
Overview of Metal Powder Products
Metal powders find applications in numerous fields. Some of the most widely recognized products include:
- Powder Metallurgy Components: Used to manufacture gears, bearings, filters, and many other parts that require precise mechanical properties.
- Metal Coatings: Metal powders are used in thermal spray coatings to provide wear resistance, corrosion protection, and aesthetic finishes on various substrates.
- Additive Manufacturing: Also known as 3D printing, where metal powders are selectively fused using lasers or electron beams to build parts layer by layer.
- Catalysts: Certain metal powders serve as catalysts in chemical reactions, especially in automotive catalytic converters.
- Energy Storage: Metal powders are finding roles in the emerging energy storage sector, including battery technologies and fuel cells.
Leading Suppliers and the U.S. Market
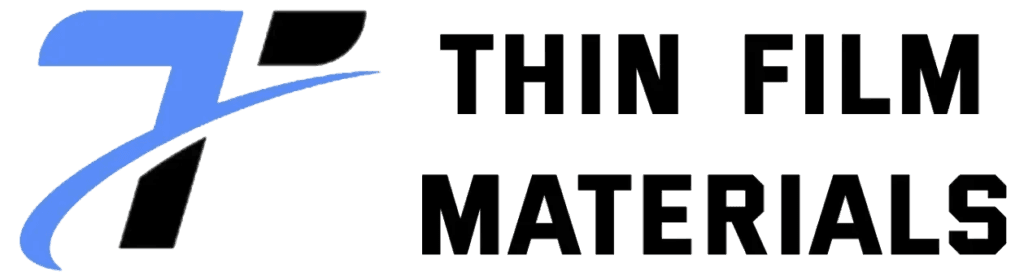
The United States is home to numerous companies specializing in metal powders, with TFM being a key supplier of high-quality metal powder products. As a trusted name in the industry, TFM provides a diverse range of metal powders for various applications, serving both domestic and international markets. Our company is committed to upholding rigorous quality standards and utilizing advanced production techniques to support innovation in aerospace, automotive, medical, and other critical industries.
Metal Powders USA
At TFM, we prioritize research and development to enhance metal powder properties and optimize processing techniques. With a strong focus on quality control, we ensure that our metal powders meet the highest industry standards, making them ideal for demanding applications. Our close collaboration with customers enables us to drive innovation, improve product performance, and explore new application possibilities, reinforcing our position as a leader in the metal powder industry.
Chapter 3
Processing Techniques: Pressing, Sintering, and Coating
The transformation of raw metal powders into functional parts involves several key processing techniques. These processes enable the creation of components with specific mechanical properties and intricate shapes that would be difficult or impossible to achieve with traditional manufacturing methods.
Metal Powder Pressing
Pressing is one of the initial steps in powder metallurgy. In this process, metal powders are loaded into a die and subjected to high pressure to form a compacted “green” part. There are two main types of pressing:
- Cold Pressing: Carried out at room temperature, cold pressing is used to form simple shapes and is often followed by sintering.
- Hot Pressing: This method combines pressure and elevated temperatures to achieve higher density and improved mechanical properties in the final product.
The pressing process is critical because it affects the uniformity and density of the powder compact, which in turn influences the final properties of the component.
Metal Powder Sintering
Sintering is a heat treatment process used to bond the pressed metal particles together. During sintering, the green compact is heated to a temperature below its melting point, causing the particles to bond through diffusion mechanisms. Sintering enhances the mechanical properties of the material, such as strength and durability, by:
- Reducing porosity.
- Increasing particle cohesion.
- Enhancing the overall structural integrity of the part.
Modern sintering techniques also include microwave sintering and spark plasma sintering, which allow for more controlled and energy-efficient processing.
Metal Powder Coating
Metal powder coating is a process in which fine metal powders are applied to a substrate to provide a protective or decorative finish. This technique is widely used in industries where corrosion resistance and surface durability are essential. The powder is typically applied electrostatically and then cured under heat, resulting in a uniform and hard coating that adheres strongly to the underlying material.
Coating applications range from automotive body panels to household appliances, and they offer a more environmentally friendly alternative to traditional liquid coatings.
Chapter 4
Applications of Metal Powders
The transformation of raw metal powders into functional parts involves several key processing techniques. These processes enable the creation of components with specific mechanical properties and intricate shapes that would be difficult or impossible to achieve with traditional manufacturing methods.
What Is Metal Powder Used For?
Metal powders serve as the raw material for several advanced manufacturing processes, including:
- Powder Metallurgy: Used to create high-performance parts in automotive, aerospace, and industrial machinery.
- Additive Manufacturing: In 3D printing, metal powders are selectively fused to build components with complex geometries.
- Thermal Spray Coatings: Metal powders provide protective layers against wear, corrosion, and high temperatures.
- Chemical Catalysts: Certain metal powders accelerate chemical reactions in catalytic converters and industrial chemical processes.
- Energy Devices: They are used in battery electrodes, fuel cells, and other components critical to energy storage and conversion technologies.
What Is Iron Metal Powder Used For?
Iron metal powder, one of the most common types, is primarily used in:
- Powder Metallurgy: It is the primary feedstock for producing automotive components such as gears, camshafts, and engine parts. Iron powder’s ability to be sintered into high-density parts makes it ideal for these applications.
- Magnetic Materials: Iron powder is used in the production of soft magnetic composites for use in electrical motors, transformers, and inductors.
- Additive Manufacturing: With its excellent magnetic and mechanical properties, iron powder is increasingly used in 3D printing for both industrial prototypes and end-use parts.
- Blast Furnaces: Iron powder also plays a role in recycling and remelting processes in steel production, ensuring that the final product has uniform composition and properties.
The controlled particle size and purity of iron powder are critical in ensuring that the final components possess the desired strength, wear resistance, and magnetic properties.
Chapter 5
Safety Considerations and Hazardous Properties
While metal powders open up innovative manufacturing possibilities, they also pose significant safety challenges. Handling these fine powders requires strict adherence to safety protocols to prevent accidents and ensure worker health.
Is Metal Powder Hazardous?
Yes, metal powders can be hazardous under certain conditions. Their small particle size and large surface area make them particularly reactive. Key safety concerns include:
- Dust Explosions: When dispersed in the air at the right concentration, many metal powders can form explosive mixtures. Fine metal dusts such as aluminum, titanium, or magnesium are especially susceptible to ignition.
- Inhalation Risks: Breathing in fine metal particles can cause respiratory issues and long-term health effects, making proper ventilation and protective equipment essential.
- Fire Risks: Certain metal powders, when exposed to air or ignition sources, can combust spontaneously or accelerate fires. This reactivity necessitates careful storage and handling procedures.
Safety protocols in facilities that process metal powders typically include dust collection systems, inert gas environments, explosion-proof equipment, and comprehensive employee training on proper handling and emergency response procedures.
Reactive Metal Powders and Their Unique Hazards
Some metal powders are designed to react vigorously under controlled conditions. For instance, in pyrotechnics and welding, metal powders are intentionally used for their reactive properties. Their highly exothermic reactions can be harnessed for cutting or welding metal parts, but they must be handled with extreme care to prevent accidental ignition.
Chapter 6
The Chemistry Behind Reactive Powders: Thermite and Beyond
One of the most intriguing aspects of metal powders is their role in exothermic reactions. These reactions not only serve industrial purposes but also raise questions about the reactivity of certain powders.
What Is the Powder That Burns Through Metal?
The phrase “the powder that burns through metal” often brings to mind thermite, a pyrotechnic composition widely known for its intense exothermic reaction. Thermite is composed of a metal powder (usually aluminum) and a metal oxide (typically iron oxide). When ignited, the aluminum powder reduces the iron oxide to molten iron, releasing enormous amounts of heat in the process. This reaction can generate temperatures exceeding 2500°C (4500°F), which is sufficient to melt or cut through metal.
Can Thermite Destroy Steel?
Thermite reactions have been used for welding, metal cutting, and even in military applications to disable armored vehicles. In controlled conditions, thermite can indeed destroy or cut through steel. The intense heat produced by the reaction is capable of melting steel, making thermite a powerful tool for:
- Welding Railroad Tracks: Thermite welding is a well-established technique for joining steel rails.
- Metal Demolition: In certain scenarios, the thermite reaction can be employed to cut or weaken steel structures.
- Military Applications: Thermite has been used in incendiary devices and munitions designed to disable armored vehicles by melting or burning through critical components.
It is important to note that while thermite can destroy steel, the reaction must be carefully managed due to its extreme temperature and rapid energy release.
What Metal Powders Are Explosive?
Several metal powders are known for their explosive properties when dispersed in air. Key examples include:
- Aluminum Powder: Due to its high reactivity and the large amount of energy it releases when oxidized, aluminum powder is a common ingredient in explosives and pyrotechnic formulations.
: Similar to aluminum, titanium powder can be highly reactive, particularly in fine particulate form, and is sometimes used in specialized energetic formulations.
- Magnesium Powder: Magnesium is another metal that, when finely divided, can react explosively in air. It is often used in fireworks and other pyrotechnic devices.
- Zinc and Iron Powders: While not as reactive as aluminum or magnesium, under certain conditions even these powders can become hazardous if dispersed in a combustible atmosphere.
The potential for an explosive reaction is not inherent in the powders themselves but is greatly increased when they are in the right (or rather, the wrong) concentration, combined with oxygen and exposed to an ignition source.
Chapter 7
Advanced Applications and Future Trends
Metal powders continue to be at the forefront of innovation in various high-tech industries. Recent advancements in additive manufacturing, nanotechnology, and high-performance materials are expanding the role of metal powders beyond traditional uses.
Additive Manufacturing and 3D Printing
The rise of additive manufacturing has created a surge in demand for high-quality metal powders. In laser sintering and electron beam melting processes, metal powders are used to produce parts with complex geometries that cannot be easily machined using traditional methods. The ability to precisely control particle size and distribution has made metal powders integral to producing lightweight, high-strength components for aerospace, automotive, and biomedical applications.
Nanostructured Metal Powders
Research into nanostructured metal powders is opening new possibilities in catalysis, energy storage, and electronics. Nanometal powders, with their extraordinarily high surface area, offer enhanced reactivity and unique physical properties. These powders are finding applications in:
- Catalysis: Improving the efficiency of chemical reactions in industrial processes.
- Energy Storage: Enhancing the performance of batteries and fuel cells.
- Electronics: Enabling the development of miniature and highly efficient electronic components.
Sustainable Manufacturing
Environmental concerns and the need for energy-efficient production methods are driving the development of greener processes in powder metallurgy. Advances in powder recycling, energy-efficient sintering methods, and the use of inert atmospheres are making metal powder production more sustainable. This focus on sustainability is expected to boost innovation and lead to new applications in industries that are actively seeking to reduce their environmental footprint.
The Role of Metal Powder Companies and Suppliers
The future of metal powders is closely tied to the innovation and quality control provided by leading suppliers and companies. In the USA and around the world, metal powder companies are investing in state-of-the-art production facilities and research laboratories to refine the characteristics of their powders. The continuous development of new alloys and composites is enabling manufacturers to meet increasingly demanding specifications in areas such as aerospace, defense, and medical technology.
Chapter 8
Summary of Key Points
To summarize, metal powders represent a fascinating and versatile group of materials with a broad range of applications:
- Production and Properties: Metal powders are produced through various methods such as atomization, mechanical milling, chemical reduction, and electrolysis. Their properties—particle size, shape, and purity—can be tailored for specific applications.
- Industrial Applications: They are used in powder metallurgy, additive manufacturing, thermal spray coatings, chemical catalysis, and energy devices. Iron metal powder, for instance, is crucial in producing automotive components and magnetic materials.
- Processing Techniques: Key processes such as pressing, sintering, and coating transform raw metal powders into finished products. Each process is essential in achieving the desired density, strength, and surface finish.
- Safety Considerations: Metal powders can be hazardous due to their potential for dust explosions, respiratory issues, and reactive behavior when exposed to ignition sources. Rigorous safety protocols are essential for handling and processing these materials.
- Reactive Powders: Thermite—composed of aluminum powder and iron oxide—is a well-known example of a reactive mixture that can generate extreme temperatures and even cut through steel. Similarly, certain metal powders (e.g., aluminum, titanium, magnesium) are known to be explosive under the right conditions.
- Emerging Trends: Advances in additive manufacturing, nanotechnology, and sustainable production methods are driving innovation in the metal powder industry. Companies are continually developing new alloys and processes to meet the growing demands of modern manufacturing.
Chapter 9
Frequently Asked Questions
1. What is metal powder?
Metal powder consists of fine metallic particles produced through physical or chemical processes. It is commonly used in powder metallurgy, additive manufacturing (3D printing), coatings, and other industrial applications.
2. What are the main applications of metal powder?
Metal powders are widely used in industries such as automotive (for brake pads and engine components), aerospace, electronics, batteries, capacitors, magnetic materials, and tooling.
3. Is powder metallurgy a complex process?
Powder metallurgy requires skilled personnel, precise mold design, and high-quality presses. The process involves compacting metal powder into a desired shape and then sintering it at high temperatures to bond the particles together, resulting in strong and durable components.
4. Can powder metallurgy be used for both low and high-volume production?
Yes, powder metallurgy is suitable for both low and high-volume manufacturing. Production volumes vary depending on the company, with some manufacturers producing between 2,500 and 500,000 parts annually.
5. How strong are powder metallurgy parts?
In many cases, powder metallurgy parts have comparable strength to forged parts. However, factors like application environment, lifespan, and further processing must be considered when selecting the right material and technique.
6. What are the advantages of powder metallurgy?
Powder metallurgy offers several benefits, including cost-effective production, the ability to create complex shapes, tight and uniform tolerances, excellent surface finishes, lower material waste, energy-efficient processes, and the ability to work with unique materials.
7. Is metal powder hazardous?
Yes, handling metal powders can be dangerous due to their flammability, explosion risk, and potential health concerns from inhalation or skin contact. Safety precautions, including proper handling and equipment maintenance, are essential.
8. What are the main methods for producing metal powder?
Common methods include electrolysis, chemical reduction, and atomization. Atomization is the preferred method for producing spherical metal powders used in additive manufacturing (3D printing).
9. Can powder metallurgy parts be machined?
Yes, powder metallurgy parts can undergo secondary machining processes such as drilling, grinding, and turning. It is recommended to discuss machining needs with suppliers to choose the most suitable material and process.
10. How precise are powder metallurgy parts?
Powder metallurgy is known for its ability to maintain tight tolerances. Typically, pressed and sintered parts achieve tolerances of ±0.004 inches (0.1 mm) in the pressing direction and ±0.2% in the mold direction.
11. What metals can be used in powder metallurgy?
Almost any metal that can be melted can be processed into powder, including iron, copper, steel alloys, brass, bronze, aluminum, tin, lead, zinc, cadmium, tungsten, titanium, and rhenium.
12. How much does powder metallurgy tooling cost?
The cost of tooling for powder metallurgy varies depending on part complexity. Simple mold designs may cost a few thousand dollars, while complex large-scale parts may require tooling investments of up to $30,000.
Chapter 10
Conclusion
Metal powders are at the heart of many modern manufacturing technologies. Their unique properties, versatility, and the ability to be processed into high-performance components make them indispensable in a wide range of industries. From the production of everyday automotive parts to the development of cutting-edge aerospace components and energy solutions, metal powders are fueling innovation and efficiency.
The industry continues to evolve rapidly, with leading companies in the USA and worldwide spearheading research and development. Their focus on quality control, sustainable practices, and process innovation ensures that metal powders will remain a key material in industrial and technological advancements for years to come.
Whether you are interested in powder metallurgy, thermal spraying, or the dramatic reactions seen in thermite applications, understanding metal powders is essential. This article has provided a detailed look at how metal powders are produced, processed, and applied, as well as the safety challenges and future trends that define this dynamic field.
As manufacturing technology continues to advance, metal powders will likely play an even greater role in creating components that are stronger, lighter, and more durable. With the constant drive for improved efficiency and performance, the innovations in metal powder processing and application are set to open up new possibilities in design, engineering, and industrial production.