Ceramic Sputtering Targets
What Are Ceramic Sputtering Targets?
Ceramic sputtering targets are solid-state compounds, typically non-metallic, used in physical vapor deposition (PVD) and magnetron sputtering systems to deposit thin films on various substrates. Unlike metal targets, ceramic targets consist of complex compounds such as oxides, nitrides, carbides, sulfides, and selenides. They offer excellent control over film characteristics like transparency, conductivity, hardness, and thermal stability.
These targets are essential for manufacturing semiconductors, optical devices, coatings for aerospace components, and more. Their chemical complexity allows for a vast range of film properties that cannot be achieved with simple metallic targets alone.
Explore Our Ceramic Sputtering Target Selection
Ceramic Sputtering Targets (Planar Type)
Common Types of Ceramic Sputtering Targets and Their Key Properties
At Thin-Film Materials (TFM), we supply a comprehensive line of ceramic targets in various chemistries and compositions. Our common categories include:
1. Oxide Targets
Examples:
- Al₂O₃ (Aluminum Oxide)
- SiO₂ (Silicon Dioxide)
- Nb₂O₅ (Niobium Oxide)
- TiO₂ (Titanium Dioxide)
- ITO (Indium Tin Oxide)
- AZO (Aluminum-doped Zinc Oxide)
- YSZ (Yttria-stabilized Zirconia)
- IGZO (Indium Gallium Zinc Oxide)
Features: High dielectric constant, excellent optical clarity, stable at high temperatures
2. Nitride Targets
Examples: TiN, ZrN, TaN, NbN, VN
Features: High hardness, wear resistance, good conductivity, golden appearance
3. Carbide Targets
Examples: TiC, ZrC, TaC, NbC, Mo₂C, VC, HfC
Features: Extreme hardness, high thermal stability, ideal for hard coatings
4. Sulfide Targets
Examples: WS₂, MoS₂
Features: Excellent lubricity, used in dry film lubricants and advanced transistors
5. Selenide & Telluride Targets
Examples: MoSe₂, NbSe₂, TaSe₂, MoTe₂, NbTe₂, TaTe₂
Features: Semiconductor properties, used in photovoltaic and optoelectronic applications
6. Fluoride & Silicide Targets
Examples: HfF₄, TiF₃, TiSi₂, TaSi₂, NbSi₂
Features: Optical coatings, barrier layers in microelectronics
7. Boride Targets
Examples: TiB₂, TaB₂, NbB₂
Features: High temperature stability, wear resistance, corrosion resistance
Each material is available in standard and custom sizes and purities (up to 99.999%), with bonding and backing plate services offered.
Applications of Ceramic Sputtering Targets
Ceramic targets serve a wide array of high-tech and industrial applications, including:
Semiconductor & Microelectronics: Dielectrics, insulators, diffusion barriers
Solar Energy: Thin film solar cells (e.g., CIGS, CdTe, TCO layers)
Optical Coatings: Anti-reflection, IR filters, high-reflectivity mirrors
Display Technology: TFTs, OLEDs, and touchscreens
Decorative Coatings: Watches, automotive trim, sanitary hardware
Aerospace & Defense: Thermal barriers, wear-resistant coatings
R&D Laboratories: Custom materials for experimental deposition
Ceramic Sputtering Targets Customization & Bonding
Need a custom composition, shape, or purity level? TFM specializes in producing tailor-made ceramic sputtering targets to meet your exact specifications. Whether you’re working on experimental deposition, prototyping a new device, or scaling up for production, we offer:
Custom shapes (disc, rectangular, step, rotatable)
Custom chemical compositions
Bonding and backing plate options
Small-batch R&D support
Our engineers collaborate closely with your team to ensure precise tolerances and meet unique requirements. We provide round targets (1″ to 14″ diameter) and rectangular targets, with customizable sizes upon request. All targets can be bonded with copper backing plates using indium or elastomer to enhance durability.
For custom orders or more information, contact us at sales@thinfilmmaterials.com or call (786) 825-8645.
Ready to Source Your Ceramic Sputtering Targets?
Contact us at sales@thinfilmmaterials.com or Request a Quote to get started. We’re here to support your thin film deposition needs with materials you can trust—every time.
Understanding Ceramic Sputtering Targets: A Comprehensive Overview
With innovations continuously driving the need for more efficient and reliable coating techniques, ceramic sputtering targets have emerged as a significant material choice. Their unique properties—such as high thermal stability, excellent chemical resistance, and desirable electrical characteristics—make them indispensable in creating thin films with precise control over thickness, composition, and structure. In the following sections, we will address frequently asked questions and key topics that potential users, researchers, and industry professionals often search for online.
Table of Contents
Chapter 1
What Are Ceramic Sputtering Targets?
Ceramic Sputtering Targets are engineered ceramic materials specifically designed for use in sputtering deposition processes. Sputtering is a method where energetic particles, typically ions, bombard a target material causing atoms or molecules to be ejected and subsequently deposited onto a substrate. In the context of ceramic sputtering targets, these materials often comprise oxides, nitrides, carbides, or other ceramic compounds that have been processed to achieve high density and uniformity.
The primary attributes that define these targets include their purity, homogeneity, and stability under plasma conditions. Due to their ceramic nature, these targets offer excellent resistance to thermal shock and chemical degradation. They can be tailored to exhibit properties such as high dielectric strength, low thermal conductivity, and robust mechanical integrity—qualities that are critical in various applications from semiconductor manufacturing to optical coatings.
Moreover, ceramic sputtering targets are available in different forms and sizes to suit specific sputtering systems and deposition requirements. They can be manufactured using advanced powder metallurgy techniques, including high-temperature sintering and hot isostatic pressing, ensuring that the target material exhibits a fine-grained microstructure and minimal porosity. This high degree of densification is essential to maintain consistent sputtering yields and to avoid particulate contamination during the deposition process.
Chapter 2
How Are Ceramic Sputtering Targets Manufactured?
The production of ceramic sputtering targets is a highly controlled process involving several sophisticated techniques aimed at achieving optimal density and purity. The manufacturing process typically starts with high-purity ceramic powders, which are mixed with binders and other additives to achieve a homogeneous mixture. This mixture is then compacted into the desired shape through processes such as isostatic pressing or uniaxial pressing.
Following compaction, the green body (the pressed compact) is subjected to a sintering process. Sintering involves heating the material to a temperature below its melting point to facilitate atomic diffusion and bonding between particles. In many cases, pressure-assisted sintering techniques, like hot pressing or hot isostatic pressing, are used to achieve higher densification and reduce the presence of residual porosity. The goal is to produce a target that has a uniform microstructure and is free from cracks or defects that could compromise its performance during sputtering.
Quality control is critical at every stage of production. Advanced characterization techniques, such as scanning electron microscopy (SEM), X-ray diffraction (XRD), and density measurements, are employed to ensure that the ceramic sputtering targets meet stringent specifications. These techniques verify not only the purity and phase composition of the ceramic but also its grain size distribution and overall homogeneity.
Additionally, the final targets are often subjected to post-sintering treatments, including grinding and polishing, to achieve the precise dimensions and surface finish required for efficient sputtering. The combination of precise manufacturing techniques and rigorous quality control helps ensure that ceramic sputtering targets deliver consistent performance and reliability in demanding industrial applications.
Chapter 3
What Materials Are Used in Ceramic Sputtering Targets?
Ceramic sputtering targets are composed of a variety of ceramic compounds, each chosen for its unique properties and suitability for specific applications. Some of the most commonly used materials include:
- Metal Oxides: Materials such as indium tin oxide (ITO), zinc oxide (ZnO), and titanium dioxide (TiO₂) are widely used in optoelectronic applications due to their transparency and electrical conductivity. ITO, in particular, is popular in the display and photovoltaic industries.
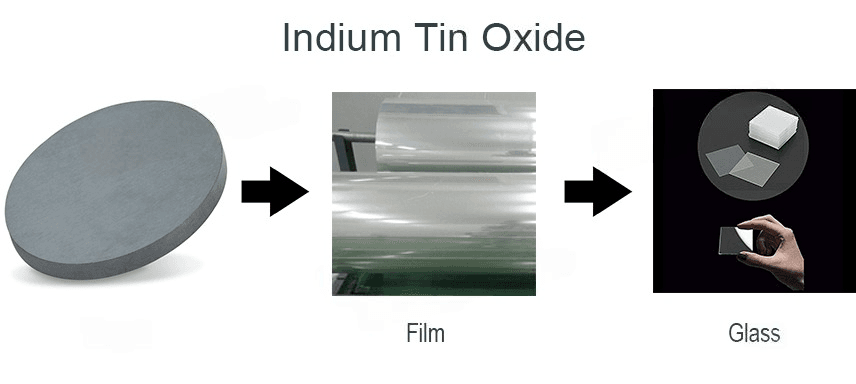
- Nitrides: Silicon nitride (Si₃N₄)and aluminum nitride (AlN) are employed in high-temperature and high-power electronic applications because of their excellent thermal conductivity and electrical insulation properties.
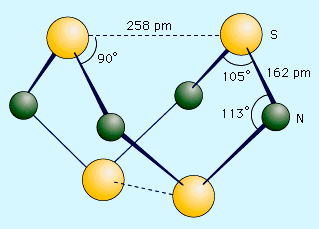
- Carbides: Titanium carbide (TiC) and silicon carbide (SiC) are known for their hardness and chemical stability, making them ideal for applications requiring wear resistance and thermal stability.
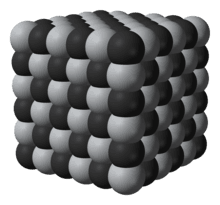
- Mixed Ceramic Compounds: In some cases, ceramic sputtering targets are engineered by combining different ceramic materials to tailor their properties. This can include blending oxides with nitrides or carbides to achieve a balance of conductivity, transparency, and mechanical strength.
The choice of material is dictated by the requirements of the deposition process and the final application of the thin film. For instance, in the semiconductor industry, the purity and stoichiometry of the ceramic target are critical, whereas in decorative coatings, the optical properties might be of greater importance. Advances in material science have enabled the development of composite and doped ceramic targets that offer enhanced performance characteristics, such as improved sputtering rates and better adhesion properties.
Chapter 4
What Are the Key Advantages of Ceramic Sputtering Targets?
Ceramic sputtering targets offer several advantages over their metallic counterparts and other deposition materials. Their inherent properties translate into performance benefits that are highly valued in various industrial and research applications:
- Thermal Stability: One of the most significant advantages of ceramic materials is their ability to withstand high temperatures. This property ensures that ceramic sputtering targets can operate efficiently even under the high-energy conditions of sputtering processes without degrading.
- Chemical Inertness: Ceramics are resistant to chemical reactions, which minimizes the risk of contamination during deposition. This quality is particularly important in semiconductor manufacturing, where purity is paramount.
- Electrical Properties: Many ceramic materials can be engineered to exhibit specific electrical characteristics, such as high dielectric strength or controlled conductivity. This is beneficial for applications requiring precise electronic properties in the thin films.
- Wear Resistance: Ceramic targets are less prone to erosion compared to metallic targets. Their hardness and low sputtering yield contribute to a longer operational lifetime and more consistent film deposition.
- Environmental Stability: Ceramics are resistant to corrosion and oxidation, which is advantageous in harsh environments or in processes that involve reactive gases.
- Customizability: The ability to tailor ceramic compositions through doping or by creating composite materials allows for the optimization of target properties for specific applications.
These advantages make ceramic sputtering targets highly desirable for producing high-quality, uniform thin films that meet the rigorous demands of modern technological applications. Whether in the production of advanced electronic devices, energy-efficient coatings, or optical components, the benefits of ceramic targets contribute significantly to improved performance and reliability.
Chapter 5
How Do Ceramic Sputtering Targets Compare to Metal Sputtering Targets?
A common question among industry professionals is how ceramic sputtering targets differ from metal sputtering targets. Both types of targets are used in sputtering deposition, but they offer distinct advantages and are chosen based on the application requirements.
- Material Properties: Metal targets are generally prized for their high electrical conductivity and ease of sputtering, making them suitable for applications where metallic films are desired. In contrast, ceramic targets often provide better thermal stability, chemical resistance, and tailored electrical properties, which are essential for semiconductor and optical applications.
- Sputtering Efficiency: Metal targets usually have higher sputtering yields due to their lower binding energies, which can lead to faster deposition rates. However, ceramic targets, with their denser structure, can offer more uniform deposition with less particulate generation, which is crucial for applications requiring high film quality.
- Film Characteristics: The films produced from metal targets are typically metallic in nature, which may require additional processing to achieve the desired electrical or optical properties. Ceramic targets, on the other hand, allow for the direct deposition of dielectric, semiconducting, or insulating films, reducing the need for post-deposition modifications.
- Operational Lifespan: Ceramic targets often exhibit longer lifespans under high-energy plasma conditions, thanks to their superior hardness and resistance to erosion. This makes them more cost-effective in long-term, high-volume production environments.
- Cost Considerations: While ceramic sputtering targets might be more expensive to produce due to their complex manufacturing processes and high material purity requirements, their extended service life and performance benefits can justify the initial investment.
Ultimately, the choice between ceramic and metal sputtering targets depends on the specific requirements of the deposition process and the intended application of the thin film. For industries that demand precision, durability, and high performance—such as semiconductor manufacturing, advanced optics, and renewable energy—ceramic targets offer a compelling advantage.
Chapter 6
What Are the Common Applications of Ceramic Sputtering Targets?
Ceramic sputtering targets are integral to a wide array of applications across diverse industries. Their versatility and superior properties have enabled breakthroughs in several high-tech fields:
- Semiconductor Manufacturing: In the semiconductor industry, ceramic sputtering targets are used to deposit dielectric films, barrier layers, and insulating coatings on silicon wafers. Materials like silicon nitride (Si₃N₄) and titanium dioxide (TiO₂) are common in these processes, contributing to the performance and reliability of microelectronic devices.
- Display Technology:
Transparent conductive oxides, such as indium tin oxide (ITO), are deposited from ceramic targets to produce films for flat-panel displays, touch screens, and photovoltaic cells. These films combine high electrical conductivity with optical transparency, critical for modern display technology.
- Optics and Photonics: Ceramic sputtering targets are employed in the fabrication of anti-reflective coatings, optical filters, and laser components. The ability to deposit thin films with controlled refractive indices and high durability is essential for the performance of optical devices.
- Energy Applications: In the renewable energy sector, ceramic sputtering targets are used to create thin-film coatings for solar cells. Oxide and nitride films can improve the efficiency and longevity of photovoltaic devices by enhancing light absorption and reducing reflective losses.
- Protective Coatings: Beyond electronic and optical applications, ceramic sputtering targets are also used for depositing hard, wear-resistant coatings on industrial components. These coatings improve the durability and performance of tools, cutting instruments, and other mechanical parts exposed to harsh operating conditions.
The diversity of applications is a testament to the flexibility and robustness of ceramic sputtering targets. By selecting the appropriate ceramic composition and optimizing the sputtering parameters, manufacturers can achieve highly specific film characteristics tailored to meet the demands of cutting-edge technologies.
Chapter 7
What Are the Quality Control Measures in Ceramic Sputtering Target Production?
Given the critical role that ceramic sputtering targets play in high-tech applications, ensuring their quality is paramount. Manufacturers implement rigorous quality control protocols throughout the production process to guarantee that each target meets strict industry standards. Key quality control measures include:
- Material Purity Verification: The production process begins with high-purity powders. Analytical techniques such as inductively coupled plasma (ICP)
spectroscopy are used to verify the elemental composition and detect any impurities that could affect performance.
- Microstructural Analysis: Techniques like scanning electron microscopy (SEM)
and X-ray diffraction (XRD) are employed to analyze the microstructure and phase composition of the sintered ceramic. This ensures that the grain size distribution is uniform and that the target is free from undesired phases or defects.
- Density and Porosity Testing: Achieving high density is essential for sputtering targets. Manufacturers use methods such as Archimedes’ principle and helium pycnometry to measure the density and porosity of the targets, ensuring they meet the required specifications.
- Dimensional Accuracy and Surface Quality: Post-sintering processes such as grinding and polishing are followed by precise dimensional inspections to confirm that the targets conform to the required size and surface finish. Any deviation can lead to uneven sputtering and poor film quality.
- Performance Testing: Finally, the targets are subjected to actual sputtering tests under controlled conditions. This practical evaluation confirms that the target will perform reliably in industrial sputtering systems, delivering the desired deposition rate and film uniformity.
These quality control measures are vital to maintaining the high standards demanded by industries such as semiconductor manufacturing and advanced optics. By adhering to stringent testing protocols, manufacturers ensure that each ceramic sputtering target contributes to the overall performance and reliability of the thin-film deposition process.
Chapter 8
What Are the Challenges and Limitations of Ceramic Sputtering Targets?
Despite their many advantages, ceramic sputtering targets also present certain challenges and limitations that must be addressed during both production and application:
- Manufacturing Complexity: The production of high-quality ceramic sputtering targets involves complex sintering and densification processes. Achieving a defect-free microstructure requires precise control over temperature, pressure, and material composition. Any deviations in these parameters can result in targets with inconsistent performance.
- Cost Considerations: Due to the sophisticated manufacturing processes and high-purity materials required, ceramic sputtering targets tend to be more expensive than their metal counterparts. For some applications, the higher initial cost can be a barrier, despite the long-term benefits of improved durability and performance.
- Sputtering Efficiency: While ceramics offer excellent film quality, their sputtering yields are generally lower than those of metals. This means that the deposition rates can be slower, which may impact production efficiency in high-volume manufacturing settings.
- Material-Specific Limitations: The performance of a ceramic sputtering target is highly dependent on its composition. Some ceramic materials might be more susceptible to cracking or delamination under prolonged high-power sputtering conditions. Moreover, variations in target composition can lead to differences in film properties, requiring careful optimization for each application.
- Integration with Existing Systems: Not all sputtering systems are optimized for ceramic targets. Adapting existing equipment or developing new configurations to accommodate the specific requirements of ceramic materials can involve additional investment and technical challenges.
Despite these challenges, ongoing research and development in materials science and process engineering continue to address these limitations. Manufacturers are constantly improving the production techniques, optimizing the target compositions, and developing innovative solutions to enhance sputtering efficiency and reduce production costs.
Chapter 9
Where to Buy Ceramic Sputtering Targets and What Are the Pricing Considerations?
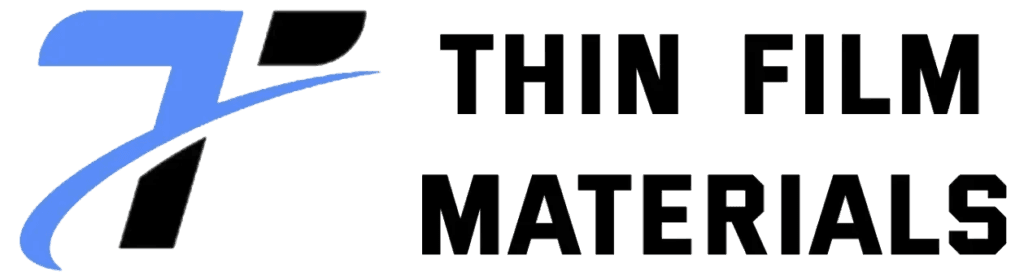
For companies and research institutions looking to invest in high-quality ceramic sputtering targets, selecting a trusted supplier is essential. The market is specialized, with several manufacturers offering tailored solutions for semiconductor, optics, and renewable energy applications.
Supplier Selection: Choosing the right supplier requires careful evaluation of product quality, manufacturing consistency, and the ability to offer customized solutions. TFM is a leading provider in this field, known for its precision-engineered ceramic sputtering targets that meet the highest industry standards.
Pricing Considerations: The cost of ceramic sputtering targets depends on factors such as material composition, size, and order volume. Compared to metal targets, ceramic options often involve more complex production processes, contributing to a higher price point. However, TFM’s advanced manufacturing techniques ensure extended target lifespan and superior film quality, delivering long-term value for customers.
Customization and Technical Support: TFM offers a wide range of standard and customized sputtering targets to meet specific deposition needs. Additionally, its team of experts provides technical support and consultation services to help optimize sputtering performance and maximize efficiency.
Global Availability: With a strong global presence, TFM ensures competitive pricing and reliable international shipping, catering to clients worldwide. Industry exhibitions and trade shows also serve as excellent platforms for learning about the latest advancements in sputtering technology and connecting with leading suppliers like TFM.
By partnering with TFM, customers can secure high-performance ceramic sputtering targets that align with both their technical requirements and budget constraints.
Chapter 10
Future Trends in Ceramic Sputtering Target Technology
The field of ceramic sputtering targets is continually evolving, driven by the increasing demand for advanced thin-film deposition technologies and the rapid pace of innovation in materials science. Several future trends are emerging that promise to shape the next generation of sputtering targets:
- Advanced Composite Materials: Researchers are exploring novel composite ceramic materials that combine the best properties of different ceramics. By doping or blending ceramics with metals or other compounds, it is possible to enhance sputtering yields, improve film uniformity, and further extend target lifespans.
- Nanostructured Targets: Innovations in nanotechnology are paving the way for the development of nanostructured ceramic targets. These targets could offer superior control over grain size and surface morphology, leading to ultra-smooth films with enhanced electrical and optical properties.
- Energy Efficiency Improvements: As industries strive to reduce energy consumption and production costs, advancements in sputtering system design and target manufacturing processes are expected. More energy-efficient sputtering targets that require lower power inputs without compromising performance will be in high demand.
- Sustainability and Environmental Considerations: With an increasing focus on sustainability, manufacturers are exploring eco-friendly production techniques and materials. Efforts to reduce waste, lower emissions during target production, and utilize recycled materials are gaining momentum in the industry.
- Integration with Emerging Technologies: The growth of emerging fields such as flexible electronics, wearable devices, and advanced photonics is driving demand for new sputtering target formulations. Ceramic targets specifically engineered for these applications could open new avenues for innovation, offering the precise material properties required for next-generation devices.
- Digitalization and Process Automation: Advanced monitoring techniques, real-time quality control systems, and process automation are set to further refine the production of ceramic sputtering targets. These developments will not only enhance product quality but also reduce manufacturing variability and improve overall efficiency.
As research continues and technological barriers are overcome, the ceramic sputtering target industry is poised to deliver even more robust, efficient, and versatile materials for a wide range of applications.
Chapter 11
Frequently Asked Questions
1. What are the advantages of ceramic sputtering targets over metal targets?
Ceramic sputtering targets often provide superior resistance to oxidation, higher hardness, and better stability in high-temperature environments compared to metal targets.
2. What is the typical purity of ceramic sputtering targets?
Ceramic sputtering targets are available in various purities, typically ranging from 99% to 99.999% (5N), depending on the application and deposition quality requirements.
3. What factors affect the lifespan of a ceramic sputtering target?
Lifespan depends on factors such as target material composition, power settings, deposition rate, sputtering pressure, and uniformity of plasma distribution.
4. How do you prevent cracking in ceramic sputtering targets?
To prevent cracking, manufacturers use high-density processing techniques and uniform bonding methods. Additionally, controlled heating and cooling cycles during sputtering help reduce thermal stress.
5. Can ceramic sputtering targets be repaired or recycled?
Yes, some ceramic targets can be reprocessed or reformed into new targets. Recycling depends on the composition and the level of contamination during use.
6. What are the common bonding methods used for ceramic sputtering targets?
Ceramic targets are often bonded using elastomeric bonding, indium bonding, or silver bonding to improve thermal conductivity and reduce mechanical stress.
7. Are ceramic sputtering targets brittle?
Yes, due to their ceramic nature, these targets are more brittle than metal targets, making proper handling and mounting essential to prevent damage.
8. What are the main differences between oxide and nitride ceramic sputtering targets?
Oxide ceramic targets are commonly used for transparent conductive coatings, while nitride ceramics provide excellent hardness, wear resistance, and chemical stability for applications like hard coatings and semiconductors.
9. How do impurities in ceramic sputtering targets affect thin film quality?
Impurities can cause defects, alter electrical or optical properties, and introduce unwanted contamination into the deposited film, making high-purity targets essential for precise applications.
10. What are some key applications of ceramic sputtering targets in optoelectronics?
Ceramic targets such as ITO (Indium Tin Oxide) and ZnO (Zinc Oxide) are widely used for transparent conductive films in LCDs, OLEDs, and touchscreens.
11. What deposition techniques are compatible with ceramic sputtering targets?
Ceramic sputtering targets are mainly used in physical vapor deposition (PVD) techniques such as magnetron sputtering and RF sputtering.
12. What are the thermal expansion characteristics of ceramic sputtering targets?
Ceramic materials typically have lower thermal expansion coefficients than metals, reducing stress-related issues in high-temperature applications. However, some ceramics may require special bonding techniques to accommodate thermal expansion mismatches.
Chapter 12
Conclusion
Ceramic sputtering targets play a crucial role in high-performance thin film manufacturing, finding widespread applications in semiconductors, display technology, optical coatings, and renewable energy. With their exceptional high-temperature resistance, chemical stability, and precision manufacturing, ceramic targets have become indispensable materials across various critical industries.
As materials science and manufacturing technologies continue to advance, the performance and applications of ceramic sputtering targets are also expanding. High-purity, high-density, and finely structured ceramic targets have become key factors in enhancing thin film quality and deposition efficiency, providing reliable support for precision manufacturing. At the same time, the industry’s demand for higher-performance materials is driving the development of new ceramic targets, laying the foundation for future technological innovations.
Whether in semiconductor device fabrication, optical coatings, or emerging energy technologies, ceramic sputtering targets play a vital role in improving thin film performance and optimizing process stability. As market demand grows and technological breakthroughs continue, ceramic targets are poised to unlock even greater potential in advanced applications.