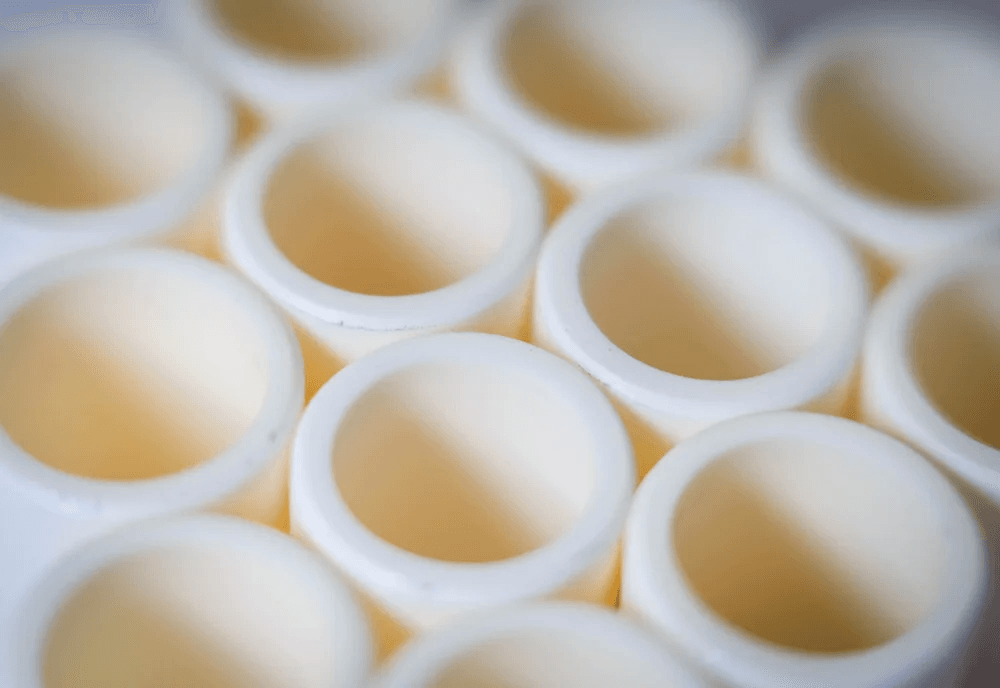
Ceramic materials, widely used in various industries due to their excellent thermal, electrical, and mechanical properties, are essential components in products like electronics, aerospace parts, medical devices, and engineering applications. One of the most critical material properties that determine a ceramic’s durability, wear resistance, and performance in real-world applications is its hardness.
Hardness is defined as the ability of a material to resist permanent deformation, indentation, or scratching. For ceramics, which are typically brittle, understanding their hardness is vital in determining how they will perform under stress or in environments prone to wear and tear. This article explores the different methods of testing the hardness of ceramic materials, the importance of hardness in ceramic applications, and the factors that influence their hardness.
Why Test the Hardness of Ceramic Materials?
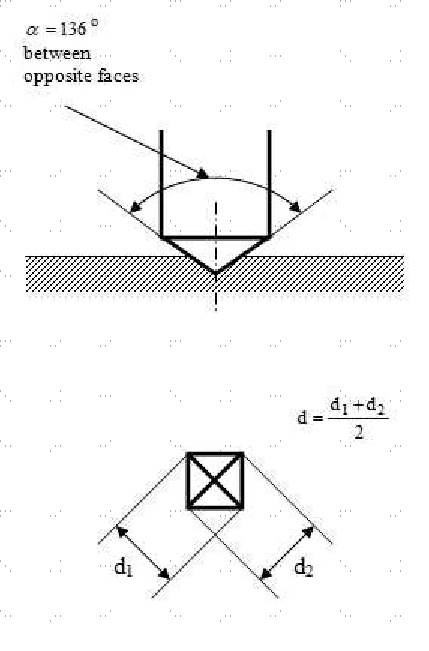
Before diving into testing techniques, it’s essential to understand why hardness testing is so crucial for ceramics. Ceramics, unlike metals, are brittle and prone to cracking or fracturing under stress. However, the hardness of ceramics plays a significant role in several areas:
- Wear Resistance: Harder ceramics resist abrasion and wear, making them ideal for components used in high-wear applications such as cutting tools, automotive parts, and industrial machinery.
- Strength Prediction: While hardness does not directly correlate with overall strength, harder ceramics tend to exhibit better resistance to fracture under loading conditions.
- Tool Selection and Manufacturing Process: The hardness of a ceramic material will influence the choice of cutting or machining tools during production. Harder materials may require specialized tools or techniques to work with.
- Product Performance and Durability: For products exposed to harsh conditions (e.g., high temperatures, wear, and corrosion), hardness can predict their lifespan and serviceability.
- Quality Control: Hardness testing helps ensure that ceramic products meet the necessary standards and specifications before they are used in applications.
Methods of Hardness Testing for Ceramics
Testing the hardness of ceramic materials can be more challenging compared to metals because of their brittle nature. Several techniques are employed, each suited to different types of ceramics and specific applications. The most commonly used hardness testing methods for ceramics include:
1. Vickers Hardness Test
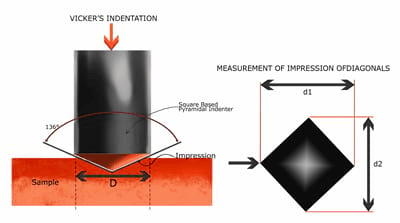
The Vickers hardness test is one of the most commonly used methods for testing the hardness of ceramic materials. It is a microhardness test that measures the resistance of a material to plastic deformation under a precisely applied load.
- Procedure: A diamond pyramid indenter with an apex angle of 136° is pressed into the material’s surface under a specific load, typically ranging from 1 to 100 kgf (kilogram-force). The size of the indentation left by the diamond indenter is then measured using a microscope. The Vickers hardness value (HV) is calculated by dividing the applied load by the surface area of the indentation.
- Advantages:
- Suitable for both small and large test specimens.
- Provides accurate and precise measurements.
- Works well for thin, hard, or brittle materials like ceramics.
- Limitations:
- The test can cause some cracking in brittle materials.
- The method requires a precise measurement of the indentation size, which can be time-consuming.
- Applications: The Vickers hardness test is widely used in research and quality control processes, especially for high-performance ceramics like alumina, zirconia, and silicon carbide.
2. Knoop Hardness Test
The Knoop hardness test is another microhardness test that is particularly effective for testing materials with very thin sections or coatings. It uses a diamond-shaped indenter, but the indentation formed is more elongated, allowing for easier measurement in small or fine samples.
- Procedure: A diamond indenter with an elongated rhombohedral shape is applied to the ceramic surface. The length of the indentation is measured under a microscope, and the hardness value is calculated based on the load applied and the size of the indentation.
- Advantages:
- Ideal for testing brittle or thin materials.
- Provides highly localized hardness measurements, making it suitable for thin films or small regions.
- Limitations:
- The test might not be suitable for thicker samples as the indenter may penetrate too deeply.
- Requires precision in measuring the indentation length.
- Applications: The Knoop hardness test is often used for ceramics in coatings or thin films, especially in microelectronics and aerospace.
3. Rockwell Hardness Test
The Rockwell hardness test is one of the most widely known and employed tests for hardness, but it is generally more suited for metals and is not as effective for ceramics. However, for certain ceramics that are less brittle, this test can be used.
- Procedure: The Rockwell test uses a diamond or carbide ball indenter, which is pressed into the ceramic surface under a specific load. After the test, the depth of penetration is measured, and a Rockwell hardness number (HR) is calculated.
- Advantages:
- Quick and simple to perform.
- Suitable for materials that do not fracture easily.
- Limitations:
- Not ideal for very brittle materials like many ceramics, as it can cause excessive cracking or fracturing.
- The results can be less accurate for materials with irregular surfaces or coatings.
- Applications: The Rockwell test is more commonly used in softer or tougher ceramics that can withstand the indenter without significant damage.
4. Mohs Hardness Test
The Mohs hardness test is a qualitative scale that ranks materials based on their ability to scratch other materials. While not as precise as other hardness tests, it provides a simple way to compare the relative hardness of ceramic materials.
- Procedure: A scratch is made on the ceramic material using a set of standard minerals with known hardness levels. The hardness is determined by which minerals the ceramic can scratch and which minerals scratch the ceramic.
- Advantages:
- Simple and low-cost method.
- Does not require specialized equipment.
- Limitations:
- Subjective results.
- Provides only a relative measure of hardness, not an exact numerical value.
- Applications: This method is often used in educational settings or in field tests where precise measurements are not required.
5. Indentation Fracture Toughness Test
For ceramics that are extremely brittle, the indentation fracture toughness method can be used. This method involves creating an indentation on the ceramic surface and measuring the crack propagation from the indentation. The degree of crack propagation provides insights into the material’s fracture toughness and, indirectly, its hardness.
- Procedure: A diamond indenter is applied under a controlled load, and the length of cracks propagating from the indentation is measured. From this data, the fracture toughness can be inferred.
- Advantages:
- Effective for brittle materials.
- Provides information on both hardness and fracture resistance.
- Limitations:
- The test can be time-consuming and requires precision in measuring crack lengths.
- Applications: This method is commonly used for testing very hard, brittle ceramics, such as those used in aerospace or cutting tools.
Factors Affecting the Hardness of Ceramic Materials
Several factors influence the hardness of ceramic materials, including:
- Composition: The chemical composition of a ceramic plays a significant role in its hardness. For example, ceramics like alumina (Al2O3) and silicon carbide (SiC) are known for their exceptional hardness, while others, like clay-based ceramics, are generally softer.
- Grain Size: Smaller grain sizes in ceramics usually lead to higher hardness values due to increased grain boundary resistance to deformation.
- Porosity: Ceramics with higher porosity tend to have lower hardness, as the pores provide areas of weakness that reduce the material’s overall resistance to indentation and wear.
- Processing Conditions: The sintering temperature and time, as well as any post-processing treatments like glazing or coating, can affect the final hardness of a ceramic. Proper control over these conditions is essential to optimize the hardness and durability of the material.
- Phase Composition: The crystalline structure of the ceramic influences its hardness. Some ceramics may contain more than one phase, with certain phases being much harder than others. For instance, zirconia-based ceramics are often modified with yttria to improve toughness and hardness.
- Temperature: The hardness of ceramic materials may decrease at elevated temperatures due to changes in the microstructure, including phase transformations or softening of certain phases.
Conclusion
Testing the hardness of ceramic materials is an essential step in evaluating their suitability for specific applications. Different hardness testing methods, such as the Vickers, Knoop, Rockwell, and Mohs tests, provide valuable insights into the material’s resistance to wear, indentation, and fracture. Each method has its advantages and limitations, so choosing the correct one is crucial based on the type of ceramic and the intended application. Understanding the factors that affect hardness, such as composition, grain size, and processing conditions, can help manufacturers optimize ceramics for high-performance uses in industries ranging from aerospace to medical devices. Ultimately, hardness testing is a vital tool for ensuring the quality and durability of ceramic products.