The Ultimate Guide to Tungsten Tubes: Properties, Processing, Applications, and FAQs
Tungsten tubes are among the most critical components in high‐temperature industrial applications. Thanks to tungsten’s exceptional heat resistance, high melting point, and remarkable durability, these tubes are widely used in sectors ranging from aerospace and defense to electronics and metalworking. In this comprehensive guide, we cover everything you need to know about tungsten tubes—from their properties and manufacturing process to their diverse applications and market insights. We’ll also answer 12 of the most frequently asked questions about tungsten tubes, making this guide a one-stop resource for engineers, buyers, and industry professionals.
Table of Contents
Chapter 1
Introduction
In industries that demand performance under extreme conditions, tungsten tubes have established themselves as essential components. With a melting point exceeding 3400°C and excellent thermal and mechanical properties, tungsten is used to fabricate tubes that can withstand high temperatures and severe wear. Whether you are looking for a Custom Tungsten Tube solution or comparing different Tungsten Tube Prices from various suppliers, understanding the nuances of tungsten tube technology is crucial.
This guide will provide an in-depth exploration of tungsten tubes, starting with a basic definition and moving into technical details on properties, processing, and applications. Additionally, we’ll address common queries about tungsten tube performance, heat resistance, and processing methods to help you make informed purchasing and design decisions.
Chapter 2
What Is a Tungsten Tube?
A tungsten tube is a hollow, cylindrical structure fabricated from tungsten or tungsten-based alloys. Tungsten is one of the most robust metals available, offering unmatched resistance to heat and wear. These tubes are designed to provide structural integrity and stability under conditions that would cause many other materials to fail.
Due to its high melting point, tungsten is often the material of choice in applications that involve extreme temperatures. Tungsten tubes are used in industries such as aerospace, defense, and metallurgy, where they serve critical roles in components like high-temperature furnace liners, heating elements, and vacuum tubes. Their cylindrical design, characterized by specific inner and outer diameters and precise wall thickness, allows them to be integrated seamlessly into various industrial systems.
Chapter 3
Key Properties of Tungsten Tubes
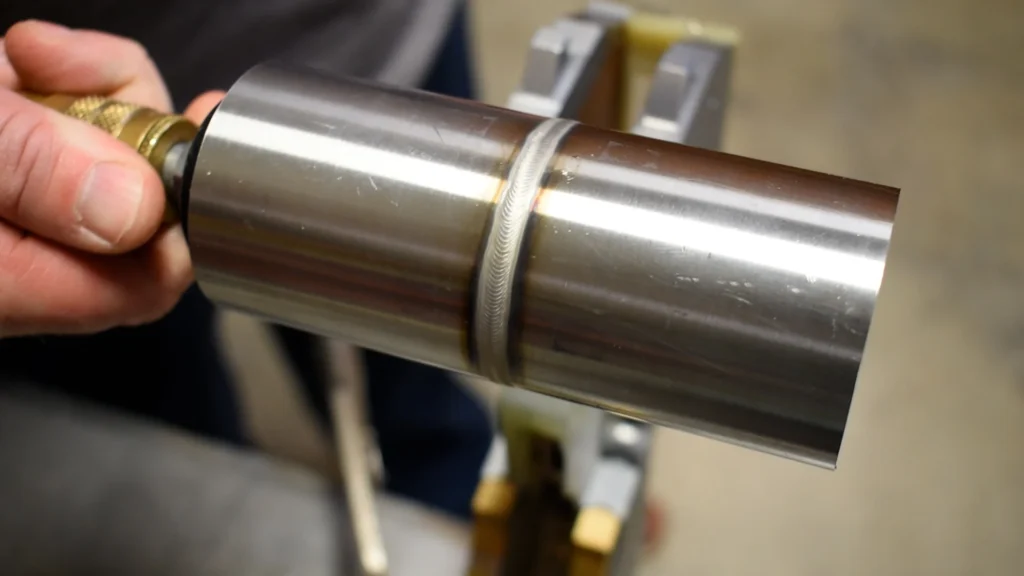
Tungsten tubes stand out for a variety of physical and chemical properties that make them ideal for challenging applications. Here are the key properties:
Shape | Tube |
Item No. | PM74-T |
Purity | W≥99.95% |
Density | 18.3g/cc to 19.2g/cc |
Process | Sintered or machined from rod |
Size | 20-640mm OD x 50-1000mm length |
Fine tubes | 3.0-20mm diameter x 50-300mm length |
Surface | Grinding, Finish turning |
Exceptional Heat Resistance and High Melting Point
High Temperature Tungsten Tube: Tungsten has the highest melting point among all metals (over 3400°C), making it indispensable for high-temperature applications.
Heat Resistance: The inherent heat resistance of tungsten ensures that tubes maintain structural integrity and performance even under prolonged exposure to extreme temperatures.
Superior Mechanical Strength and Durability
Tungsten is known for its high density and strength, ensuring that tungsten tubes can endure significant mechanical stress and harsh operational environments.
These properties contribute to the excellent Tungsten Tube Performance in industrial settings where reliability is paramount.
Chemical Stability and Corrosion Resistance
Tungsten is chemically inert at room temperature and resists attack from most acids and bases, ensuring longevity even when exposed to aggressive environments.
Dimensional Precision and Customization
Modern manufacturing processes enable the production of tungsten tubes with very tight tolerances and consistent quality, fulfilling Tungsten Tube Specifications demanded by various industries.
Many manufacturers offer Custom Tungsten Tube options to meet unique project requirements.
Chapter 4
Manufacturing and Processing of Tungsten Tubes
Powder Metallurgy and Sintering
Tungsten tubes are primarily produced using powder metallurgy. This process involves mixing tungsten powder with a binder material, followed by pressing and sintering at high temperatures to create a solid, homogenous structure. Sintering not only consolidates the material but also enhances its mechanical properties, making it ideal for high-temperature applications.
Extrusion and Drawing
Once sintered, the tungsten billet is extruded and drawn into tube form. The extrusion process shapes the tube, while drawing is used to reduce the diameter and improve the surface finish. This two-step process ensures that the final product meets precise Tungsten Tube Specifications.
Chemical Vapor Deposition (CVD)
For applications requiring ultra-high purity and performance, chemical vapor deposition is sometimes employed. CVD involves the deposition of tungsten onto a substrate from a vapor phase, forming a tube with exceptional uniformity and minimal impurities.
Post-Processing and Quality Control
After the tubes are formed, additional processes such as machining, polishing, and coating may be used to achieve the desired surface finish and dimensional accuracy. Quality control measures are critical in this stage to ensure that each tube meets the industry’s strict performance and safety standards.
These processing methods directly influence the Tungsten Tube Processing and ultimately determine the overall Tungsten Tube Performance and durability in operational settings.
Chapter 5
Applications of Tungsten Tubes
Tungsten tubes are deployed in a variety of high-tech and industrial applications. Their unique properties make them suitable for environments where other materials would fail. Below are some of the primary applications:
High-Temperature Furnaces and Heating Elements
Due to their excellent Tungsten Tube Heat Resistance, tungsten tubes are commonly used as liners in high-temperature furnaces. They provide a protective barrier that can withstand extreme thermal cycling without degrading.
Aerospace and Defense
In aerospace and defense, tungsten tubes are used in applications where materials are subjected to severe heat and mechanical stresses. They are found in components like missile nozzles, rocket engine parts, and other high-performance systems. Their high density also makes them ideal for balancing applications in aircraft and other vehicles.
Electronics and Vacuum Tubes
Tungsten’s superior electrical conductivity and thermal stability make it an excellent material for electronic components. Tungsten tubes are used in vacuum tubes and electron microscopes, where precise thermal and electrical characteristics are critical.
Metalworking and Cutting Tools
Tungsten carbide, a compound derived from tungsten, is widely used in the manufacture of cutting tools and abrasives. Although tungsten tubes are distinct from tungsten carbide products, the underlying properties that make tungsten desirable—such as hardness and wear resistance—are similarly valuable in cutting tool applications.
Industrial Reactors and Chemical Processing
In chemical processing plants, tungsten tubes can serve as critical components in reactors that operate under extreme conditions. Their ability to resist corrosion and high temperatures ensures that they can safely contain reactive chemicals and serve in catalytic processes.
Medical Equipment
Some advanced medical devices use tungsten tubes for applications that require precise temperature control and durability. Their reliability under extreme conditions makes them suitable for specialized diagnostic equipment.
Each application leverages the unique characteristics of tungsten, ensuring that systems remain efficient and safe even under the most challenging conditions. As industries continue to push the limits of technology, the demand for high-performance materials like tungsten tubes is expected to grow.
Chapter 6
Tungsten Tube Specifications and Customization
Dimensional and Tolerance Specifications
Tungsten tubes are available in a wide range of dimensions, including various inner diameters, outer diameters, and wall thicknesses. Manufacturers adhere to strict tolerance levels to ensure that the tubes can be seamlessly integrated into complex assemblies.
Standard Specifications: Many suppliers provide tungsten tubes in standard sizes, which are suitable for general industrial applications.
Custom Tungsten Tube Solutions: For specialized applications, many manufacturers offer customization options. Buyers can specify unique dimensions, lengths, and surface finishes tailored to their specific requirements.
Material Composition and Grades
Tungsten tubes are manufactured from high-purity tungsten or tungsten alloys. The choice of material grade depends on the intended application and operating conditions. High-purity tungsten tubes are ideal for applications requiring maximum heat resistance, while tungsten alloys may offer additional benefits such as improved machinability or enhanced mechanical properties.
Surface Finishing and Coatings
To further enhance performance, tungsten tubes can undergo various surface finishing processes. These processes may include:
Polishing: To achieve a smooth, reflective surface that minimizes friction and enhances heat dissipation.
Coatings: In some cases, tungsten tubes are coated to improve corrosion resistance or to tailor surface properties for specific applications.
By focusing on detailed Tungsten Tube Specifications, manufacturers ensure that each product meets stringent quality standards and delivers consistent performance.
Chapter 7
Market Insights: Price, Suppliers, and Manufacturers
Tungsten Tube Price and Market Trends
The price of tungsten tubes is shaped by various factors, including raw material availability, production techniques, and industry demand. As tungsten is widely used in high-temperature applications, its cost is typically higher than other metals. At TFM, we provide competitive Tungsten Tube Prices and detailed Tungsten Tube Quotes to help customers make well-informed purchasing decisions.
TFM: A Trusted Manufacturer and Supplier
TFM is a leading Tungsten Tube Manufacturer and Tungsten Tube Supplier, offering high-quality tungsten tubes tailored to diverse industry needs. Our products meet stringent quality standards, and we provide both standard and custom solutions to match specific application requirements. With a strong focus on quality assurance and customer satisfaction, TFM stands out as a reliable choice in the global tungsten market.
Global Supply and Availability
The tungsten supply chain is highly specialized, requiring precision manufacturing and stringent quality control. TFM ensures transparent pricing and rigorous quality checks, guaranteeing that our tungsten tubes deliver optimal performance and safety in critical applications.
Why Choose TFM?
Partnering with TFM provides distinct advantages, including:
Competitive Tungsten Tube Pricing and Quotes
Extensive Customization and Technical Support
Reliable Quality Control and On-Time Delivery
Comprehensive Product Documentation and After-Sales Service
With TFM, customers gain access to superior tungsten tube solutions designed to excel in demanding environments.
Chapter 8
Frequently Asked Questions (FAQs) About Tungsten Tubes
What is a tungsten tube?
A tungsten tube is a hollow cylindrical component made from pure tungsten or tungsten alloys. It is designed to withstand extremely high temperatures and harsh environments, making it ideal for applications in furnaces, aerospace, and electronic devices.
What are the main applications of tungsten tubes?
Tungsten tubes are used in high-temperature furnaces, vacuum tubes, heating elements, and components in aerospace and defense systems. They are also used in metalworking and industrial reactors where durability and heat resistance are critical.
What are the key properties of tungsten tubes?
Tungsten tubes exhibit exceptional heat resistance, a high melting point (over 3400°C), high density, and excellent wear resistance. These properties contribute to their superior performance in demanding industrial applications.
How are tungsten tubes manufactured?
Tungsten tubes are primarily manufactured through powder metallurgy. The process includes mixing tungsten powder with binders, pressing, sintering at high temperatures, and subsequent extrusion or drawing to form tubes with precise dimensions.
What is the typical price range for tungsten tubes?
The price of tungsten tubes depends on their dimensions, purity, and production volume. Buyers often look for Tungsten Tube Price comparisons and Tungsten Tube Quote details from various suppliers to ensure competitive pricing.
Where can I purchase tungsten tubes?
Tungsten tubes are available from TFM, Tungsten Tube Manufacturers, and industrial material distributors. It is advisable to choose suppliers with robust quality control and reliable delivery records.
What dimensions and tolerances are common for tungsten tubes?
Tungsten tubes are available in a variety of inner and outer diameters, wall thicknesses, and lengths. Standard specifications are available, but many manufacturers also offer Custom Tungsten Tube solutions to meet specific requirements with tight tolerances.
How does a tungsten tube compare with alternative materials?
Compared to molybdenum or ceramic tubes, tungsten tubes offer a higher melting point, greater density, and superior mechanical strength. However, they may come at a higher cost. Buyers often perform a Tungsten Tube Comparison to decide which material best suits their needs.
Can tungsten tubes be welded or machined?
Yes, tungsten tubes can be machined and, in some cases, welded using techniques such as tungsten inert gas (TIG) welding. However, due to tungsten’s high hardness, specialized tools and expertise are required for processing.
What industries most commonly use tungsten tubes?
Industries including aerospace, defense, electronics, metallurgy, and high-temperature processing rely on tungsten tubes. Their unique properties make them indispensable for applications where extreme performance and reliability are required.
What is the heat resistance and durability of tungsten tubes?
Tungsten tubes excel in environments with extreme heat. Their ability to maintain structural integrity at temperatures above 3400°C makes them one of the most durable materials available for high-temperature applications.
How should tungsten tubes be maintained and cleaned?
- Maintenance of tungsten tubes typically involves gentle cleaning with non-abrasive solutions to prevent surface scratches. Regular inspections for signs of wear or damage are recommended to ensure long-term performance and safety.
Chapter 9
Conclusion
Tungsten tubes are indispensable components in many industrial and high-temperature applications due to their exceptional properties. With a high melting point, excellent heat resistance, and superior mechanical strength, these tubes serve critical roles in sectors such as aerospace, defense, electronics, and metalworking. Understanding the manufacturing process—from powder metallurgy and sintering to extrusion and post-processing—sheds light on the technical prowess required to produce high-quality tungsten tubes.
When evaluating tungsten tubes, buyers should consider detailed specifications, including dimensions and tolerances, as well as custom options provided by leading manufacturers. With competitive Tungsten Tube Price information and reliable suppliers available, sourcing the right tungsten tube becomes a straightforward process. Moreover, comparing tungsten tubes against alternative materials such as molybdenum or ceramics allows industry professionals to select the best material based on performance, cost, and operational requirements.
This article has also addressed the 12 most frequently asked questions regarding tungsten tubes, offering clear insights into their properties, applications, and maintenance practices. Whether you are an engineer designing high-temperature systems, a procurement specialist sourcing materials, or an industry professional seeking technical guidance, understanding tungsten tubes and their market dynamics is critical.
In summary, tungsten tubes provide unparalleled performance in extreme environments, making them an essential material for modern industry. With ongoing advancements in manufacturing techniques and customization options, the future of tungsten tube applications is bright. For those seeking reliable, high-performance solutions, the choice is clear: invest in tungsten tubes to ensure durability, efficiency, and long-term performance in your most demanding applications.
By integrating the trending keywords and addressing frequently asked questions, this guide serves as a comprehensive resource for anyone interested in learning about tungsten tubes—from Tungsten Tube Price and Tungsten Tube Manufacturer details to Tungsten Tube Applications and technical specifications. As industries continue to push the boundaries of technology, tungsten tubes will remain at the forefront of high-temperature, high-performance material solutions.