Tantalum Tube
Tantalum Tube, Tantalum Pipe
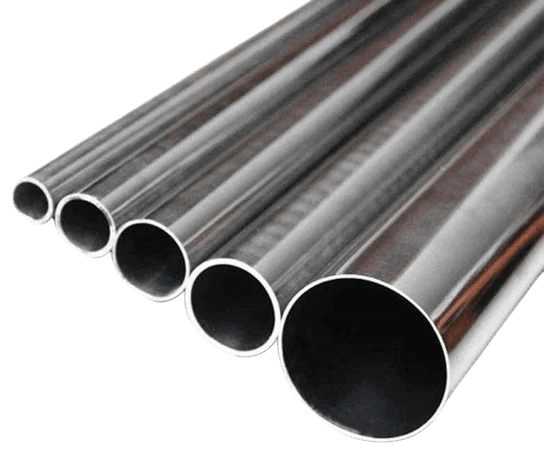
Material: Tantalum / Tantalum Alloy
Grade: R05200, R05400, R05252(Ta-2.5W), R05255(Ta-10W)
Purity: 99.9%, 99.95%, 99.99%
Standard: ASTM B521-98
Standard Sizes: OD1~150mm, Wall Thick 0.2~5.0mm, Length 10~6,000mm
Other: Material, Size, and Surface Can be Customized
Applications: Reaction Vessel Production, Heat Exchange Pipe, Condensers, Bayonet Heaters, Helical Coils, Thermocouples, Protective Tubes, etc.
Tantalum Capillary
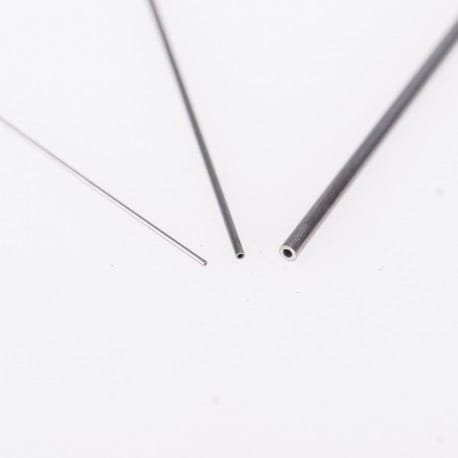
Material: Tantalum / Tantalum Alloy
Grade: R05200, R05400, R05252(Ta-2.5W), R05255(Ta-10W)
Purity: 99.9%, 99.95%, 99.99%
Standard: ASTM B521-98
Standard Sizes: OD0.3~35.0mm, Wall Thick 0.08~1.00mm, Length Tailored
Tolerances: OD +/-0.003mm, Wall Thick +/-0.005mm, Length +/-0.05mm
Other: Material, Size, and Surface Can be Customized
Applications: Platinum Substitute, Filament Lead Tube of the Cathode Insulator in X-Ray Tube, Liquid Tantalum Electrolytic Capacitors
Tantalum Tubing Size Ranges
Outer Diameter | 0.30~150.00mm |
Wall Thickness | 0.08~5.00mm |
Length | <6000mm, Tailored Lengths |
Material | R05200, R05400, R05252, R05255, R05240 |
Standatd | ASTM B521 |
Purity | 99.95% or 99.99%, or Customized |
Tantalum Tubing Price Referrences
- OD8.7mm*ID8.34mm*W.T.0.18mm*100mm US$356.00
Tantalum Tube, Ta 99.9% Min., Length Can be Tailored
- OD1.05mm*ID0.65mm*W.T.0.2mm*500mm US$865.00
Tantalum Capillary, Ta 99.9% Min., Length Can be Tailored
- OD0.31mm*ID0.19mm*W.T.0.06mm*300mm US$802.00
Tantalum Capillary, Ta 99.9% Min., Length Can be Tailored
*Price for reference only. Bulk orders are with factory-direct prices.
Description
Tantalum Tube or Tantalum Pipe is a type of tube made from the rare and highly dense metal tantalum (CAS# 7440-25-7). It is known for its excellent corrosion resistance and good thermal conductivity, making it suitable for various applications, such as heat exchangers, condensers, shell and tube heaters, and high-temperature furnace parts, as well as military satellites, cutting-edge medical technologies, semiconductor and electronics, defense, furnace parts, chemical processing equipment, and medical applications.
Tantalum finds versatile applications in fabricating both welded and seamless tubes/pipes. Producing seamless tantalum tubes/pipes involves techniques such as extrusion, tube reduction, or deep drawing using sheet metal. In contrast, welded tantalum tubes/pipes are manufactured by forming a strip, shaping it into a tube, and welding the joint using gas tungsten arc welding. These seamless or welded tubes cater to a broad spectrum of industrial uses.
There are two types of tubes for Tantalum tubes: seamless tubes and welded tubes. The welded tube is recommended for a thin-wall thickness tube, while for a thicker-wall thickness tube, a seamless tube is recommended. For even smaller-sized tubes, Tantalum Capillary is your choice. The outer surface of the Tantalum Tube is polished, with roughness below 3.2um. The inner surface is up to customers’ unique needs.
Common Specifications
- ASTM B521 R05200 » Electron Beam Melted (unalloyed)
- ASTM B521 R05400 » Powder Metallurgy Grade (unalloyed)
- ASTM B521 R05252 » Tantalum 2.5% Tungsten Alloy
- ASTM B521 R02555 » Tantalum 10% Tungsten Alloy
- ASTM B521 R05240 » Tantalum 40% Niobium Alloy
Available Materials
- Tantalum
- Tantalum 2.5% Tungsten
- Tantalum 7.5% Tungsten
- Tantalum 10% Tungsten
- Furnace Grade Tantalum
- Tantalum 40% Niobium
Grade | Tensile Strength | Yield Strength | Elongation in 1″ / 2″ Gage Length |
---|---|---|---|
bpsi / MPa, ≥ | psi / MPa, ≥ | %, ≥ | |
R05200 | 30000 (207) | 20000 (138) | 25 |
R05400 | 30000 (207) | 20000 (138) | 25 |
R05252 | 40000 (276) | 28000 (193) | 20 |
R05255 | 70000 (481) | 60000 (414) | 15 |
R05240 | 40000 (276) | 28000 (193) | 20 |
Applications
Tantalum Tubes, renowned for their exceptional corrosion resistance and thermal stability, find extensive applications across various industries. Some notable uses include:
- 1. Chemical Industry: Tantalum tubes are widely employed in the chemical sector, particularly for handling corrosive acids and reactive chemicals due to their resistance to corrosion.
- 2. Electronics and Semiconductors: Tantalum Tubes play a vital role in the electronics industry, where their high melting point and conductivity make them suitable for manufacturing capacitors and other electronic components.
- 3. Aerospace and Defense: Tantalum Tubes contribute to aerospace applications, including the production of components for satellites and other space exploration equipment, owing to their durability and resistance to extreme conditions.
- 4. Medical Devices: Tantalum Tubes are utilized in medical applications, such as the manufacture of implants and medical devices, benefiting from their biocompatibility and resistance to bodily fluids.
- 5. Energy Industry: In the energy sector, Tantalum Tubes are employed in various capacities, from handling corrosive materials in chemical processes to contributing to the development of high-temperature and corrosion-resistant components.
- 6. Nuclear Applications: Tantalum's ability to withstand harsh environments makes it valuable in nuclear applications, where it can be used in the construction of reactor components.
- 7. Heat Exchangers: Tantalum Tubes are suitable for use in heat exchangers due to their resistance to corrosion and their ability to withstand high temperatures.
- 8. Research and Development: Tantalum Tubes are crucial in laboratory settings and research environments where resistance to corrosion and high temperatures is essential.
In summary, Tantalum Tubes are a critical material in various industries. Their unique properties make them indispensable for applications demanding durability, corrosion resistance, and high performance in challenging environments.
Packaging
Our Tantalum Tube are clearly tagged and labeled externally to ensure efficient identification and quality control. Great care is taken to avoid any damage which might be caused during storage or transportation.
The Ultimate Guide to Tantalum Tubes: Properties, Applications, and Market Insights
Tantalum tubes are premium components used in a wide range of high-performance applications, thanks to their exceptional corrosion resistance, high melting point, and superior stability. These tubes play a critical role in industries such as chemical processing, aerospace, medical devices, and electronics—where materials must perform reliably under extreme conditions. In this ultimate guide, we explore every aspect of tantalum tubes: their unique properties, manufacturing techniques, various applications, and market insights. Additionally, we answer 12 of the most frequently asked questions (FAQs) to ensure you have all the information needed for informed decision-making.
Table of Contents
Chapter 1
1. Introduction
In today’s advanced industrial environment, materials that can endure extreme conditions are in high demand. Tantalum—a rare, corrosion-resistant metal—has emerged as one of the most critical materials in modern engineering. Tantalum tubes, specifically, offer a combination of properties that make them ideal for use in hostile environments. Their ability to withstand harsh chemicals, high temperatures, and mechanical stress makes them invaluable for sectors ranging from chemical processing and aerospace to medical devices and electronics.
Whether you are evaluating Tantalum Tube Prices or searching for a reputable Tantalum Tube Supplier or Manufacturer, understanding the material’s properties, processing techniques, and market trends is essential. This guide provides an in-depth look at tantalum tubes, covering the science behind the material, the detailed manufacturing processes, various applications, and market dynamics. In addition, we address 12 popular FAQs that potential buyers and engineers frequently ask.
Chapter 2
2. What Is a Tantalum Tube?
A tantalum tube is a hollow cylindrical component fabricated from high-purity tantalum or tantalum-based alloys. Known for its outstanding corrosion resistance, high melting point, and excellent mechanical strength, tantalum is a material that consistently performs in the harshest of environments.
Structure and Design
Tantalum tubes are engineered with precise inner and outer diameters and wall thicknesses. The design specifications vary depending on the application. For instance, in chemical processing, a tube might require a very thin wall to maximize heat transfer, whereas in aerospace applications, a thicker wall might be needed for mechanical strength. The ability to produce Custom Tantalum Tubes to meet specific dimensional requirements is one of the significant advantages of using tantalum in high-tech applications.
Material Characteristics
The exceptional properties of tantalum are the main reasons for its extensive use. With a melting point of approximately 3017°C, tantalum remains stable under extremely high temperatures. Its nearly inert nature in corrosive environments makes it ideal for applications where other metals might degrade. Moreover, tantalum is biocompatible, which means it can be safely used in medical devices and implants.
Why Choose Tantalum Tubes?
Corrosion Resistance: Tantalum is highly resistant to acids and other corrosive substances.
Thermal Stability: With a very high melting point, tantalum tubes can operate reliably in high-temperature applications.
Mechanical Strength: The metal’s density and strength ensure that tantalum tubes can withstand mechanical stresses.
Biocompatibility: Tantalum is non-toxic and well-tolerated by the human body, making it suitable for medical applications.
Overall, tantalum tubes are a premium choice when long-term performance and reliability in extreme conditions are required.
Chapter 3
3. Key Properties of Tantalum Tubes
Understanding the inherent properties of tantalum is crucial to appreciating its value in various applications. Below are the key properties that define tantalum tubes:
Exceptional Corrosion Resistance
Tantalum is one of the most corrosion-resistant metals known. It is immune to attack by most acids, including hydrochloric, sulfuric, and nitric acids. This chemical inertness is vital for applications in chemical processing plants, where equipment is continuously exposed to aggressive substances.
High Melting Point and Thermal Stability
With a melting point of around 3017°C, tantalum exhibits excellent thermal stability. This high-temperature resistance makes it ideal for use in applications such as high-temperature furnaces, heat exchangers, and aerospace components that require materials to perform under intense thermal stress.
Superior Mechanical Strength and Ductility
Tantalum’s high density contributes to its exceptional mechanical strength. Despite being very strong, tantalum is also ductile, allowing it to be formed into tubes with precise dimensions. This combination of strength and formability is critical for creating components that can maintain their integrity under mechanical and thermal loads.
Biocompatibility
Tantalum is renowned for its biocompatibility. It does not react adversely with bodily fluids, making it a preferred material for medical devices and implants. Its use in surgical instruments and prosthetic devices has been well-documented, highlighting its safety and long-term stability within the human body.
Electrical and Thermal Conductivity
In addition to its strength and corrosion resistance, tantalum provides excellent electrical and thermal conductivity. This makes tantalum tubes valuable in electronic applications, where precise thermal management and efficient electrical performance are required.
Dimensional Stability and Customization
Modern manufacturing processes allow for the production of tantalum tubes with very tight tolerances. This precision ensures that tantalum tubes meet exact Tantalum Tube Specifications. Many suppliers offer customization options, providing Custom Tantalum Tube solutions tailored to specific requirements.
These properties make tantalum tubes an attractive option for high-tech and industrial applications where performance under extreme conditions is essential.
Chapter 4
4. Manufacturing and Processing
Producing high-quality tantalum tubes involves advanced manufacturing techniques that ensure both the purity of the material and the precision of the final product. Let’s explore the key stages of manufacturing and processing tantalum tubes.
Powder Metallurgy and Sintering
Powder metallurgy is the most common method used to manufacture tantalum tubes. The process typically involves the following steps:
Powder Preparation: High-purity tantalum powder is prepared, often with a binder to aid in compaction.
Pressing: The tantalum powder is pressed into a preform or billet. The pressing process determines the initial shape and density of the material.
Sintering: The pressed billet is heated in a controlled atmosphere to a temperature below its melting point. Sintering causes the powder particles to bond together, resulting in a dense and homogeneous material. This step is critical to achieving the mechanical properties and dimensional accuracy required for high-performance applications.
Extrusion and Drawing
After sintering, the billet undergoes extrusion to form the initial tube shape. Extrusion involves forcing the material through a die to produce a cylindrical shape. Once extruded, the tube is drawn to reduce its diameter and refine the wall thickness. Drawing is essential for improving surface finish and ensuring the tube meets stringent Tantalum Tube Specifications.
Chemical Vapor Deposition (CVD)
For applications requiring ultra-high purity and superior surface quality, Chemical Vapor Deposition (CVD) is sometimes employed. In the CVD process, tantalum is deposited onto a pre-formed tube from a gaseous precursor. This technique results in a uniform coating and can help eliminate impurities that may be present after traditional processing methods. CVD is especially useful for manufacturing High Temperature Tantalum Tubes for critical applications.
Post-Processing and Finishing
Following the primary forming processes, tantalum tubes often undergo additional post-processing steps such as machining, polishing, and coating. These steps are crucial to achieve the desired surface finish and dimensional accuracy. Polishing enhances the aesthetic quality and improves the performance in applications where surface smoothness is critical. Coating may further enhance the corrosion resistance or tailor the tube’s surface properties for specific uses.
Quality Control
Every stage of manufacturing is monitored by rigorous quality control processes. Advanced measurement techniques ensure that the final product meets all required tolerances and performance standards. Quality control is critical in maintaining consistent Tantalum Tube Performance, especially in high-reliability applications.
The combination of these advanced processing methods results in tantalum tubes that offer exceptional durability, precision, and performance in extreme environments.
Chapter 5
5. Applications of Tantalum Tubes
Tantalum tubes are used across a variety of industries thanks to their unique combination of properties. Below are some of the primary applications:
Chemical Processing
One of the most common applications of tantalum tubes is in the chemical processing industry. Tantalum’s remarkable corrosion resistance makes it ideal for constructing reactors, heat exchangers, and piping systems that handle aggressive chemicals. In these environments, the longevity and reliability of tantalum tubes significantly reduce maintenance costs and downtime.
Aerospace and Defense
In the aerospace and defense sectors, materials must perform reliably under extreme conditions. Tantalum tubes are used in high-temperature engine components, missile parts, and protective shielding. Their ability to maintain integrity at elevated temperatures and resist corrosive environments is critical for safety and performance in these high-stakes applications.
Medical Devices and Implants
Tantalum’s biocompatibility is a key factor that drives its use in the medical industry. Tantalum tubes are used in surgical instruments, implants, and prosthetic devices. Their non-toxic nature and long-term stability in bodily fluids make them ideal for applications where patient safety is paramount.
Electronics and Semiconductor Manufacturing
Tantalum plays a crucial role in the electronics industry due to its excellent electrical conductivity and thermal stability. Tantalum tubes are used in the production of high-performance capacitors and vacuum tubes. They are also essential components in semiconductor manufacturing processes where precise temperature control is required.
Industrial Furnaces and Heat Exchangers
In heavy industrial applications, tantalum tubes serve as key components in high-temperature furnaces and heat exchangers. Their ability to withstand extreme thermal cycles without degrading ensures that industrial processes remain efficient and reliable over long periods.
Specialized Research and High-Purity Applications
In research laboratories and high-tech manufacturing facilities, tantalum tubes are used in applications that require ultra-high purity and precise performance characteristics. Whether used in vacuum systems or as part of critical measurement instruments, the properties of tantalum ensure that these tubes deliver consistent results.
Other Niche Applications
Beyond these primary industries, tantalum tubes are also used in:
Catalytic Processing Equipment: Due to their inert nature, they are used in reactors that require minimal chemical interaction.
Marine and Offshore Applications: Their corrosion resistance is beneficial in harsh saltwater environments.
High-Temperature Sensors and Instrumentation: In applications requiring accurate temperature measurements under extreme conditions, tantalum tubes provide reliable performance.
Each application leverages tantalum’s inherent strengths, making these tubes indispensable in environments where performance, reliability, and longevity are non-negotiable.
Chapter 6
6. Market Insights: Price, Suppliers, and Manufacturers – TFM Perspective
Tantalum Tube Price and Market Trends
At TFM, we understand that the Tantalum Tube Price is influenced by several key factors, including raw material availability, production complexity, and market demand. Tantalum is a rare metal with limited supply, and its extraction and processing are both labor-intensive and technologically demanding. These challenges naturally result in a higher price point compared to more common metals. Despite these factors, market trends indicate a rising demand for tantalum tubes, particularly driven by sectors such as chemical processing, aerospace, and medical applications. As industries continuously push performance limits, buyers increasingly request detailed Tantalum Tube Quotes—and TFM is proud to provide competitive pricing while maintaining uncompromising quality.
TFM: Leading Tantalum Tube Manufacturer and Supplier
TFM has established itself as a leading Tantalum Tube Manufacturer and Tantalum Tube Supplier in the industry. When selecting TFM as your supplier, you benefit from several critical factors:
Production Capacity: TFM boasts robust production capabilities to meet both small-scale projects and mass production demands, ensuring that volume requirements are consistently fulfilled.
Quality Certifications: TFM adheres to strict international quality standards, including ISO certifications, guaranteeing that every product meets the highest levels of reliability and performance.
Customization Options: TFM offers extensive Custom Tantalum Tube solutions, allowing you to tailor dimensions, wall thickness, and finishes to perfectly match your specific requirements.
Technical Support and After-Sales Service: Our comprehensive support and after-sales service ensure that any technical challenges are quickly addressed, providing long-term satisfaction and reliable performance.
Transparent Pricing: TFM is committed to clear and competitive pricing. We provide detailed Tantalum Tube Quotes that help build trust and enable informed purchasing decisions.
Global Supply Chain and Availability
The tantalum market is highly specialized, and TFM is strategically positioned within a global supply chain known for advanced metal processing capabilities. Due to tantalum’s rarity, the supply chain is more concentrated than that of common metals. TFM emphasizes transparency, rigorous quality control, and timely delivery. This ensures that every tantalum tube meets the strict specifications and performance standards required by our customers, regardless of global supply fluctuations.
Competitive Advantages of Choosing TFM
Partnering with TFM offers significant benefits that set us apart from other suppliers:
Competitive Pricing Models: TFM’s competitive pricing ensures you receive the best value for your investment while maintaining exceptional quality.
Extensive Technical Support: With expert technical guidance and extensive customization options, TFM ensures your application requirements are fully met.
Consistent Quality and On-Time Delivery: Our robust quality control processes and reliable delivery schedules guarantee that your production processes remain uninterrupted.
Comprehensive Documentation and After-Sales Support: TFM provides detailed product documentation and outstanding post-sales support to help you integrate tantalum tubes seamlessly into your operations.
These market insights, centered on TFM, enable buyers to navigate the complex global supply chain confidently and secure high-quality tantalum tubes that fulfill both performance and budgetary requirements.
Chapter 7
7. Tantalum Tube Specifications and Customization
Standard Specifications
Tantalum tubes are manufactured to meet strict dimensional and performance standards. Key specifications typically include:
Inner Diameter and Outer Diameter: Available in a range of sizes to accommodate different applications.
Wall Thickness: Critical for ensuring mechanical strength and durability; wall thicknesses can be optimized based on the operational environment.
Length: Standard lengths are offered, but many suppliers provide the option for custom lengths to suit unique project needs.
Surface Finish: Depending on the application, tantalum tubes may be polished, brushed, or coated to enhance their performance and appearance.
These specifications ensure that tantalum tubes can be integrated into complex systems with minimal modification. For industries where precision is essential, suppliers provide detailed Tantalum Tube Specifications to guarantee compatibility and performance.
Custom Tantalum Tube Solutions
Many applications require tailored solutions that go beyond standard specifications. Customization options may include:
Tailored Dimensions: Adjusting the inner diameter, outer diameter, wall thickness, and length to meet specific design requirements.
Special Finishes and Coatings: Enhancing surface properties for improved corrosion resistance or to meet aesthetic preferences.
Material Composition: Selecting between high-purity tantalum or tantalum alloys based on the desired balance of strength, ductility, and corrosion resistance.
Packaging and Delivery Options: Custom packaging can be arranged to protect the product during transportation and storage.
By offering Custom Tantalum Tube options, manufacturers can cater to a wide range of industries and applications, ensuring that each tube is perfectly suited to its intended use.
Quality Assurance
Quality assurance is a critical component of the manufacturing process. Every batch of tantalum tubes undergoes rigorous testing for dimensional accuracy, mechanical strength, and corrosion resistance. Detailed inspection protocols ensure that every tube meets the strict standards demanded by high-performance applications. Comprehensive documentation provided by suppliers gives buyers confidence that the product will perform reliably in the field.
Chapter 8
8. Tantalum Tube Comparison and Performance
When selecting a material for high-temperature and corrosive environments, it’s important to compare tantalum tubes with alternatives such as titanium or molybdenum tubes. Here, we explore how tantalum stands out:
Tantalum vs. Titanium Tubes
Corrosion Resistance: Tantalum is generally more resistant to corrosive chemicals than titanium, particularly in environments with highly aggressive acids.
Thermal Stability: With a melting point around 3017°C, tantalum can operate at higher temperatures compared to titanium, making it a better option for extreme heat applications.
Mechanical Strength: Tantalum offers excellent strength and ductility, which is essential for maintaining structural integrity under mechanical stress.
Cost Considerations: Tantalum is rarer and more expensive than titanium; however, its superior properties often justify the higher cost in critical applications.
Application Suitability: For applications in chemical processing and medical devices, tantalum’s biocompatibility and inertness give it an edge over titanium.
Tantalum vs. Molybdenum Tubes
Chemical Inertness: Tantalum exhibits superior corrosion resistance compared to molybdenum, making it more suitable for aggressive chemical environments.
Temperature Performance: Both metals have high melting points, but tantalum’s thermal stability is generally more favorable in ultra-high temperature applications.
Mechanical Properties: While both metals are strong, tantalum’s excellent ductility enables more precise fabrication of tubes with tight tolerances.
Cost and Availability: Molybdenum is typically less expensive than tantalum, so the choice may depend on budget constraints and performance needs.
Performance in Extreme Conditions
High Temperature Tantalum Tubes are designed to operate reliably in environments with extreme heat and corrosive substances. Their ability to withstand temperatures approaching 3000°C and their resistance to chemical attack ensure that they maintain performance and structural integrity over time. These characteristics make tantalum tubes an excellent choice for demanding applications in aerospace, industrial furnaces, and chemical reactors.
Processing Advantages
The advanced manufacturing processes used for tantalum tubes—such as powder metallurgy, extrusion, and chemical vapor deposition—ensure that the tubes meet exact Tantalum Tube Specifications. These methods yield products with uniform microstructures, high density, and exceptional durability. Consistent quality control during production translates into superior Tantalum Tube Performance in the field.
Chapter 9
9. Frequently Asked Questions (FAQs) About Tantalum Tubes
Below are 12 popular FAQs that address the most common questions about tantalum tubes:
1. What is a tantalum tube?
A tantalum tube is a hollow cylindrical component made from high-purity tantalum or tantalum alloys. Its unique properties, including exceptional corrosion resistance and high thermal stability, make it ideal for a variety of industrial applications.
2. What are the primary applications of tantalum tubes?
Tantalum tubes are extensively used in chemical processing, high-temperature furnaces, aerospace components, medical devices, and electronic systems. Their resilience against corrosive chemicals and extreme heat makes them indispensable in these fields.
3. Why is tantalum used in chemical processing?
Due to its nearly complete resistance to most acids, tantalum is the preferred material for equipment in chemical processing plants. Tantalum tubes are used in reactors, heat exchangers, and piping systems where aggressive chemicals are present.
4. How does tantalum compare to titanium in terms of corrosion resistance?
Tantalum is generally more corrosion-resistant than titanium, especially in environments containing highly aggressive acids. This superior resistance makes tantalum tubes the top choice for applications requiring maximum chemical stability.
5. What are the typical specifications for tantalum tubes?
Tantalum tubes are available in various inner and outer diameters, wall thicknesses, and lengths. Standard sizes exist, but many suppliers also offer Custom Tantalum Tube solutions to meet specific application needs and stringent tolerance requirements.
6. How are tantalum tubes manufactured?
Tantalum tubes are primarily produced through powder metallurgy, where tantalum powder is pressed and sintered into a billet, which is then extruded and drawn into tube form. Advanced techniques like chemical vapor deposition (CVD) may also be used to achieve high purity and precise dimensions.
7. Can tantalum tubes be customized?
Yes, many manufacturers offer customization options that allow customers to specify dimensions, wall thickness, surface finishes, and material grades to meet their specific requirements.
8. How does the price of tantalum tubes compare to other metals?
The Tantalum Tube Price is generally higher than that of more common metals due to tantalum’s rarity and the complex manufacturing processes involved. Buyers typically request detailed Tantalum Tube Quotes to compare prices across suppliers.
9. Where can I purchase high-quality tantalum tubes?
High-quality tantalum tubes are available from reputable Tantalum Tube Suppliers and Tantalum Tube Manufacturers who provide transparent pricing, detailed documentation, and strong quality assurance processes.
10. How do tantalum tubes perform in high-temperature environments?
Thanks to their high melting point and excellent thermal stability, High Temperature Tantalum Tubes maintain their structural integrity and performance even under extreme heat, making them ideal for use in industrial furnaces and aerospace applications.
11. What industries most commonly use tantalum tubes?
Industries such as chemical processing, aerospace, defense, medical, and electronics are the primary users of tantalum tubes. Their exceptional properties make them critical for applications where reliability and performance are crucial.
12. What maintenance is required for tantalum tubes?
Tantalum tubes generally require minimal maintenance due to their inherent corrosion resistance. Regular inspections and gentle cleaning with non-abrasive solutions are usually sufficient to keep them in optimal condition.
Chapter 10
10. Conclusion
Tantalum tubes are an essential material solution for applications demanding high corrosion resistance, exceptional thermal stability, and robust mechanical strength. From chemical processing and aerospace to medical devices and electronics, the unique properties of tantalum make it a critical choice for industries that operate under extreme conditions.
Understanding the technical aspects of tantalum—its properties, manufacturing techniques, and customization options—is crucial for making informed decisions. Whether you are comparing Tantalum Tube Prices, searching for a reliable Tantalum Tube Supplier or Manufacturer, or exploring Custom Tantalum Tube options to meet precise application requirements, this guide provides the comprehensive information you need.
Market trends indicate that despite its higher cost, the demand for tantalum tubes is increasing due to their superior performance in hostile environments. Reputable suppliers ensure competitive pricing through transparent Tantalum Tube Quotes and offer extensive technical support and after-sales service. Their commitment to quality and customization means that tantalum tubes will continue to be a cornerstone of high-performance engineering.
The detailed manufacturing processes—from powder metallurgy and sintering to extrusion and CVD—ensure that every tantalum tube meets stringent Tantalum Tube Specifications. With rigorous quality control, these tubes deliver consistent Tantalum Tube Performance over extended periods, even under extreme conditions.
In comparing tantalum tubes with alternative materials like titanium or molybdenum, tantalum stands out for its unmatched chemical stability and thermal performance, despite a higher price point. For critical applications where failure is not an option, investing in high-quality tantalum tubes is essential.
This article has also answered 12 of the most frequently asked questions regarding tantalum tubes, offering clear insights into their properties, applications, and maintenance practices. Whether you are a design engineer looking to integrate these components into your systems, a procurement specialist evaluating supplier options, or a market analyst monitoring industry trends, the information provided here will help you navigate the tantalum tube market confidently.
As technological advancements drive industries to operate under more extreme conditions, the demand for robust, reliable materials like tantalum continues to grow. Tantalum tubes offer the durability and performance necessary for the most challenging environments, ensuring long-term efficiency and safety in your applications.
Invest in quality, choose reliable suppliers, and leverage the advantages of tantalum tubes to stay ahead in your industry. With comprehensive technical support, competitive pricing, and unmatched performance, tantalum tubes are a wise investment for any application that demands excellence.