Furnaces & Parts
Applications
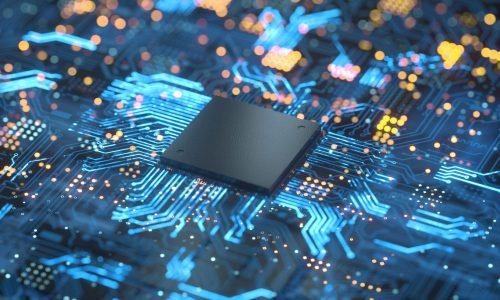
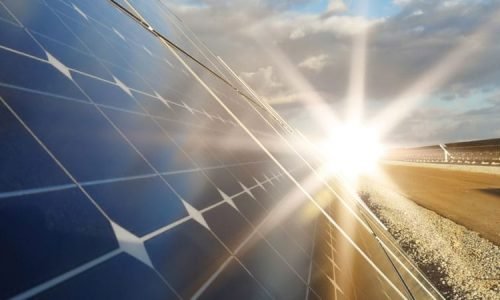
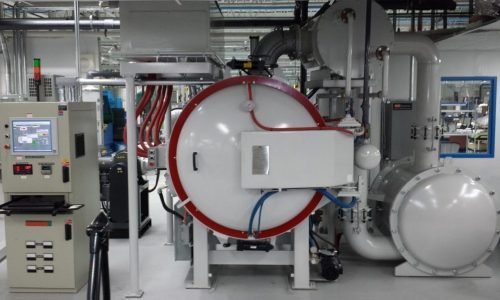
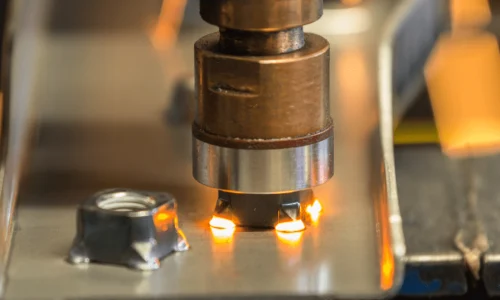
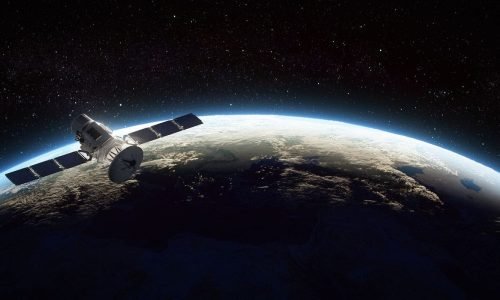
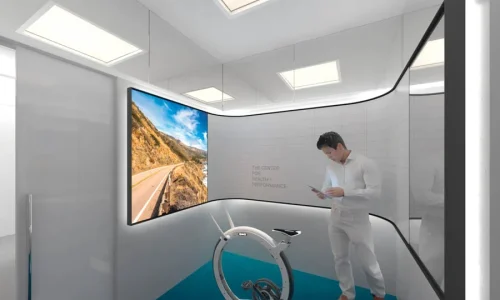
Vacuum furnace chambers have a wide range of applications across various industries:
Heat Treatment
- Annealing: Softening metals for improved machinability and to enhance mechanical and electrical properties
- Normalizing: Improving the mechanical properties of steel
- Hardening: Increasing the hardness of steel
- Tempering: Reducing the brittleness of hardened steel
- Carburizing: Increasing the carbon content of steel to improve wear resistance
- Nitriding: Improving the surface hardness of steel by introducing nitrogen
Sintering
- Ceramics: Reducing porosity and enhancing strength, transparency, thermal conductivity, or electrical conductivity
- Cermets: Joining ceramics and metals to create hard, wear-resistant materials
- Refractory metals: Producing high-melting-point metals like tungsten and molybdenum
- Cutting tools: Manufacturing cemented carbide cutting tools
Brazing
- Joining metal components using a filler material
- Producing vacuum switching chambers for the electrical industry
- Joining aluminum products like heat exchangers
Melting and Casting
- Glass: Melting raw materials to produce glass
- Non-ferrous metals: Melting metals like aluminum, copper, and precious metals
- Ferroalloys: Producing alloys containing iron
Pyrolysis
- Decomposing organic waste at high temperatures in the absence of oxygen
- Converting biomass into valuable products like charcoal and biofuels
Vacuum furnace chambers play a crucial role in many industries, enabling processes that are essential for the production of a wide range of materials and products while preventing oxidation and contamination
Our Factory
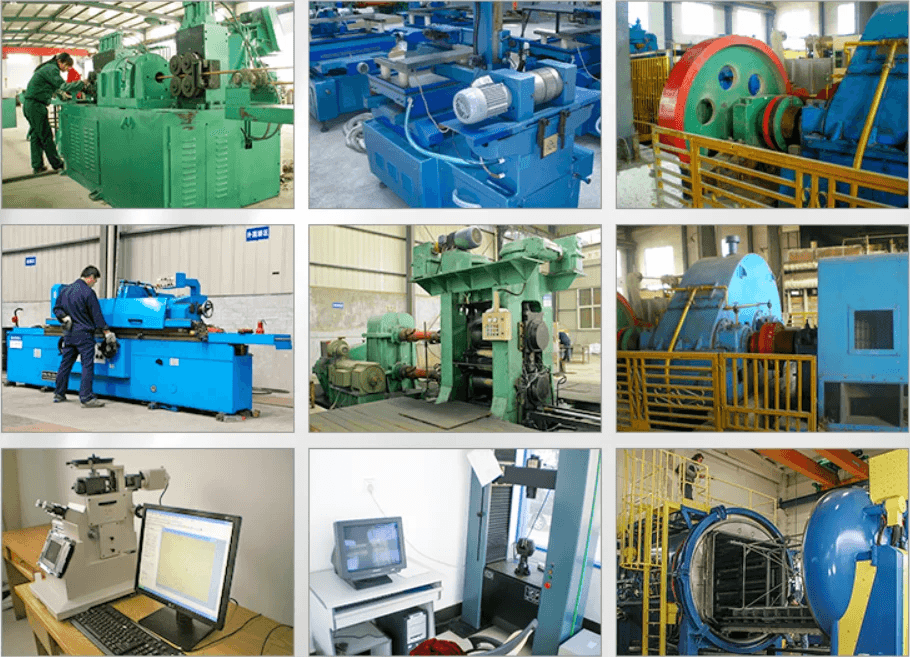
Cetificates
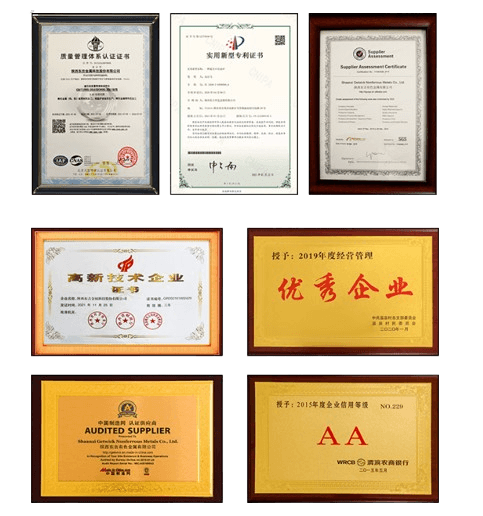
Furnaces & Parts: Advancing Industrial High-Temperature Processing
Industrial furnaces play a critical role in manufacturing, material processing, and metallurgy. They provide the controlled high-temperature environments necessary for processes such as heat treatment, sintering, brazing, and annealing. With evolving industrial demands, furnace design and technology have advanced significantly. This article examines specialized furnace components and parts—especially those related to vacuum furnace chambers using materials such as molybdenum and tungsten—while also addressing common questions about chamber furnaces, combustion chambers, and their maintenance and replacement.
Table of Contents
Chapter 1
1. An Overview of Furnace Technology
Furnaces come in a wide range of types and designs, each tailored to specific applications. Traditional combustion furnaces operate by burning fuel to generate heat, while more advanced models—such as vacuum furnaces—employ controlled environments that eliminate contaminants and oxidation during processing.
1.1 Traditional Furnaces vs. Vacuum Furnaces
- Traditional Combustion Furnaces:
These furnaces rely on combustion to generate heat and are common in applications where oxidation is not a critical concern. They have a combustion chamber, where fuel burns to create the necessary temperatures. Vacuum Furnaces:
In contrast, vacuum furnaces operate in a low-pressure environment. By removing oxygen and other gases, these furnaces prevent oxidation and contamination. They are ideal for treating metals and alloys that are sensitive to air exposure. Vacuum furnaces also offer improved temperature uniformity and precise control over the heating cycle, which is essential for high-performance materials.
Chapter 2
2. What Is a Chamber Furnace?
A chamber furnace is a type of furnace characterized by its enclosed interior space—referred to as the “chamber”—where the heating process occurs. This design isolates the material being processed from external atmospheric conditions. There are several benefits to this approach:
Controlled Atmosphere:
The chamber can be purged with inert gases or evacuated to a vacuum state, ensuring that the processed material does not oxidize or degrade.Uniform Heat Distribution:
The confined space allows for consistent temperature distribution, which is critical for achieving precise metallurgical properties.Energy Efficiency:
Insulated chambers reduce heat loss, making the process more energy efficient.
The term “chamber furnace” is sometimes used interchangeably with “vacuum furnace” when referring to furnaces that provide these controlled environments. However, while all vacuum furnaces are chamber furnaces, not every chamber furnace operates under a vacuum.
Chapter 3
3. Vacuum Furnace Chambers: Materials and Designs
Vacuum furnace chambers are often constructed using materials that can withstand extreme temperatures and harsh processing conditions. Among these materials, molybdenum and tungsten stand out due to their high melting points, strength, and resistance to thermal shock.
3.1 Vacyum (Vacuum) Furnace Chamber
Although “vacyum” may appear as a typographical variation, it is understood to refer to a vacuum furnace chamber. These chambers are engineered to operate under vacuum conditions, thereby reducing atmospheric contamination and oxidation during high-temperature processes. The vacuum environment within the chamber facilitates:
Precision Processing:
Temperature and atmosphere can be precisely controlled, which is essential for materials requiring specific metallurgical characteristics.
Enhanced Material Properties:
Products such as aerospace components, turbine blades, and high-performance alloys benefit from the oxidation-free environment, ensuring superior mechanical properties.
3.2 Molybdenum Vacuum Furnace Chamber
Molybdenum is an excellent material for vacuum furnace chambers due to its outstanding thermal conductivity, high melting point (approximately 2623 °C or 4753 °F), and mechanical strength. Molybdenum vacuum furnace chambers are particularly useful when processing components that require:
High-Temperature Stability:
They maintain structural integrity even at extremely high temperatures, reducing deformation and wear.Chemical Resistance:
Molybdenum’s resistance to chemical attack ensures that the furnace chamber does not contaminate the processed materials.
These attributes make molybdenum chambers ideal for advanced heat treatment processes in industries like aerospace, automotive, and energy.
3.3 Tungsten Vacuum Furnace Chamber
Tungsten, with an even higher melting point (around 3422 °C or 6192 °F), is another favored material for constructing vacuum furnace chambers. Tungsten vacuum furnace chambers offer:
Superior Thermal Resistance:
They can operate at temperatures where most other metals would melt or degrade.Enhanced Durability:
Tungsten is extremely hard and maintains its properties over prolonged high-temperature exposure, making it an excellent choice for long-life furnace components.Minimal Thermal Expansion:
Reduced expansion and contraction cycles contribute to longer service life and more consistent processing conditions.
These qualities ensure that tungsten vacuum furnace chambers are used in the most demanding industrial applications where consistent performance and longevity are paramount.
Chapter 4
4. Key Furnace Components and Parts
In addition to the primary furnace chamber, various components and accessories are crucial for the optimal operation of a furnace system. Below are some of the essential parts that play important roles in furnace assembly, performance, and maintenance.
4.1 Tungsten Bracket
Tungsten brackets are engineered to support heavy-duty components within the furnace assembly. Given tungsten’s high melting point and mechanical strength, these brackets ensure:
Structural Integrity:
They maintain secure positioning of internal components, even under extreme thermal stress.Stability and Safety:
Robust support structures are essential to prevent shifting or collapse during operation.
4.2 Tungsten Twisted Wire
Electrical Heating Elements:
Their high conductivity and strength make them ideal for wiring heating elements.Structural Reinforcement:
They can also be used in reinforcing other components within the furnace assembly.
4.3 W-Cu Alloy Part
The W-Cu (tungsten-copper) alloy combines the strength and high-temperature properties of tungsten with the excellent thermal and electrical conductivity of copper. W-Cu alloy parts are widely used in:
Thermal Management:
They help in dissipating heat quickly, which is vital for preventing overheating.High-Current Applications:
Their combined properties make them suitable for parts that require rapid and efficient heat transfer.
4.4 Tungsten Electrode
Tungsten electrodes are critical in various high-temperature applications, particularly in electric arc furnaces and welding processes. Their roles include:
Arc Generation:
Providing a stable and enduring arc for welding or melting operations.Consistency in Performance:
Tungsten’s ability to resist degradation under intense heat ensures consistent performance over extended periods.
4.5 Tungsten Fastener
Fasteners made from tungsten are designed to hold furnace components together securely under high thermal loads. Their benefits include:
High Strength:
They can endure the forces generated by thermal expansion and contraction.Long Service Life:
Due to tungsten’s resistance to heat-induced wear, these fasteners contribute to the overall longevity of the furnace system.
4.6 Molybdenum Fastener
Similar to tungsten fasteners, molybdenum fasteners offer durability in high-temperature environments. They are especially useful in parts of the furnace that experience frequent temperature fluctuations. The properties of molybdenum—such as good thermal conductivity and strength—make these fasteners ideal for critical load-bearing connections.
4.7 Tungsten Threaded Bar
Threaded bars made of tungsten are utilized for assembling and securing furnace components. Their fine threads and exceptional strength ensure that all parts remain tightly bound even under the duress of repeated heating and cooling cycles.
4.8 Molybdenum Rings
Molybdenum rings are often used as gaskets or sealing elements in furnace assemblies. They provide:
Effective Sealing:
Preventing gas leaks and ensuring the vacuum integrity of the furnace chamber.High Temperature Tolerance:
Their resilience under high thermal stress is essential for maintaining a controlled processing environment.
4.9 Tungsten Heater
Tungsten heaters are integral components in furnaces where rapid and precise heating is required. Their characteristics include:
Rapid Thermal Response:
Tungsten heaters quickly reach operating temperatures and provide even heat distribution.Extended Durability:
They can operate continuously for long periods without degradation, ensuring reliability and process consistency.
4.10 Furnace Accessories
A variety of furnace accessories enhance the performance and functionality of furnace systems. These include items such as:
Temperature Sensors:
For monitoring and regulating internal temperatures.Control Panels:
To allow operators to set and monitor process parameters.Insulation Materials:
Designed to reduce heat loss and improve energy efficiency.
4.11 Tungsten Hook
Tungsten hooks are used to suspend or support components within the furnace chamber during assembly or maintenance. Their strength and resistance to high temperatures make them ideal for handling heavy or delicate parts.
4.12 Tungsten Heater Accessories
These accessories complement tungsten heaters by providing components such as mounting brackets, connectors, and protective casings. They ensure that the heating elements are securely installed and maintained under optimal conditions.
Chapter 5
5. Economic Considerations: Cost to Replace a Furnace Combustion Chamber
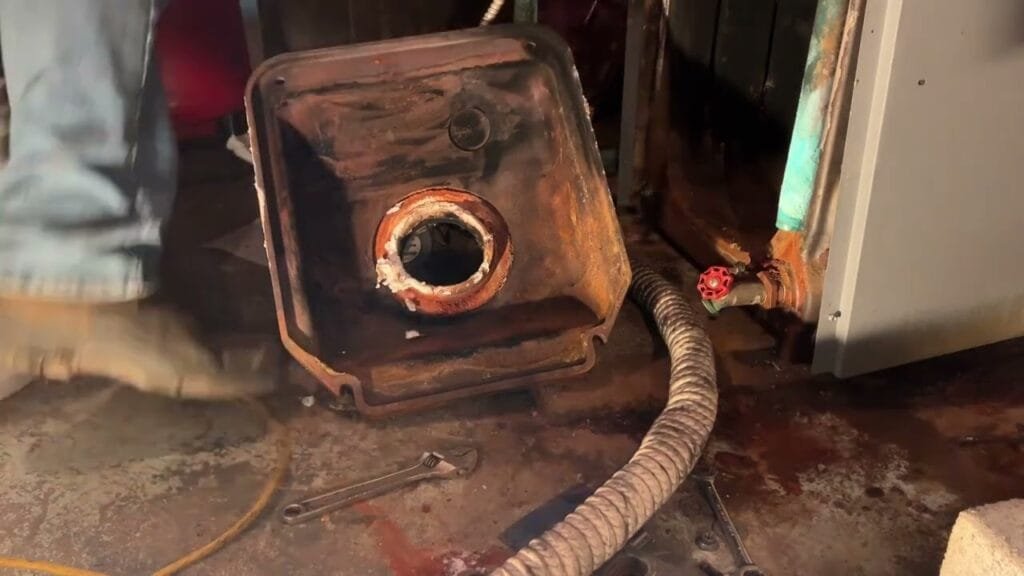
Replacing a furnace combustion chamber is a significant investment in industrial operations. The overall cost depends on several factors:
Material Costs:
The choice of materials—whether tungsten, molybdenum, or other high-performance alloys—directly impacts the price. Materials with higher melting points and better thermal properties tend to be more expensive.Size and Design:
Larger furnaces or custom-designed combustion chambers will incur higher replacement costs due to increased labor and material requirements.Labor and Installation:
Professional installation by qualified technicians is necessary to ensure safety and optimal furnace performance. Labor costs can vary widely depending on the region and the complexity of the installation.Downtime and Production Losses:
In some industrial settings, replacing a combustion chamber may require extended downtime. Companies must factor in the potential loss of productivity when planning a replacement.
While exact figures depend on the specific furnace and operating environment, typical replacement costs for industrial furnace combustion chambers can range from several thousand dollars to tens of thousands. Organizations often mitigate these expenses by investing in regular maintenance programs and predictive diagnostics to identify issues before they lead to complete failure.
Chapter 6
6. The Furnace Room: Nomenclature and Safety
Many facilities house their furnaces in dedicated spaces known as furnace rooms or boiler rooms. The terminology and configuration can vary based on the type of furnace and the specific industrial application.
Furnace Room:
This is typically the dedicated space where one or more furnaces operate. The room is designed with reinforced floors, proper ventilation, and safety features to manage the high temperatures and potential hazards.Boiler Room:
In some industrial contexts, especially in older facilities or combined systems, the furnace room may be referred to as the boiler room. Despite the name, a boiler room might house both combustion-based furnaces and boilers used for heating.
6.1 Safety Considerations
Ensuring safety in furnace rooms is paramount. Best practices include:
Proper Ventilation:
Adequate ventilation systems reduce the risk of gas buildup and ensure that combustion by-products are safely expelled.Regular Inspections:
Safety protocols require periodic inspections of both the furnace and its surrounding environment to detect potential issues early.Emergency Systems:
Fire suppression systems, emergency shutoff mechanisms, and clearly marked exit routes are essential for protecting personnel and equipment.
Chapter 7
7. Furnace vs. Combustion Chamber: Understanding the Differences
Despite their interconnected functions, a furnace and a combustion chamber are distinct components within a heating system.
7.1 Furnace
Definition and Function:
A furnace is the complete unit designed for heating materials. It includes the chamber where heating occurs, as well as all associated components like burners, insulation, heat exchangers, and control systems.Broader Scope:
The term “furnace” encompasses the entire assembly, including the mechanisms for fuel supply, ignition, temperature control, and safety systems.
7.2 Combustion Chamber
- Definition and Function:
The combustion chamber is a specific section within a furnace where the actual combustion of fuel takes place. It is designed to withstand high temperatures and direct flame exposure. - Key Differences:
While the furnace provides the overall environment and control, the combustion chamber is solely responsible for fuel combustion and the initial production of heat. In vacuum furnaces, the combustion chamber is often replaced by a controlled heating element or electric heater, as the primary goal is to maintain a clean, oxidation-free environment.
Chapter 8
8. When Should a Combustion Chamber Be Replaced?
Determining the right time to replace a combustion chamber is vital for both operational safety and economic efficiency. Replacement is generally considered when:
Visible Wear and Tear:
Cracking, corrosion, or significant material erosion can compromise the integrity of the combustion chamber, leading to decreased performance or hazardous conditions.Performance Decline:
A noticeable drop in efficiency, uneven heating, or increased fuel consumption may indicate that the combustion chamber is no longer functioning optimally.Scheduled Maintenance Intervals:
Many industrial operations follow a predetermined maintenance schedule that includes the replacement of key components, including the combustion chamber. This proactive approach minimizes the risk of unexpected failures.Technological Upgrades:
With ongoing advancements in furnace technology, older combustion chambers may be replaced as part of an upgrade program. Modern materials and designs offer improved energy efficiency, reduced emissions, and extended service life.
By monitoring operational parameters and adhering to maintenance protocols, companies can identify when a combustion chamber replacement is necessary, ultimately ensuring consistent furnace performance and safety.
Chapter 9
9. Old Furnace Transformation: Repair and Replacement
Many industrial facilities operate legacy furnace systems that may no longer meet modern efficiency and safety standards. Transforming an old furnace can involve repair, replacement, or a complete upgrade.
9.1 Repair vs. Replacement
Repair:
For furnaces with minor issues, targeted repairs—such as replacing worn fasteners, sealing rings, or heater accessories—can restore functionality without incurring the cost of a complete overhaul.Replacement:
When structural components, such as the combustion chamber or primary heating elements, exhibit extensive wear, replacement may be the more viable long-term solution. Modern furnace systems offer better performance, safety features, and energy efficiency.
9.2 Benefits of Modernization
Transforming an old furnace system can bring several advantages:
Enhanced Efficiency:
Modern furnaces, especially vacuum furnace systems with advanced materials like tungsten and molybdenum, provide more uniform heating and reduced energy consumption.Improved Safety:
Upgraded control systems, better insulation, and enhanced safety features reduce the risk of accidents and downtime.Extended Service Life:
Newer components are designed to handle the rigors of continuous industrial use, resulting in fewer breakdowns and lower maintenance costs over time.Regulatory Compliance:
Upgraded furnaces often meet or exceed current environmental and safety regulations, ensuring that facilities remain compliant with industry standards.
Chapter 10
10. Daily Maintenance: Best Practices for Furnace Longevity
Regular maintenance is the cornerstone of safe and efficient furnace operation. Daily checks and routine servicing can prevent unexpected failures and extend the lifespan of both the furnace and its components.
10.1 Routine Inspection Procedures
Visual Checks:
Inspect the furnace chamber, combustion area, and internal components for any signs of wear, discoloration, or damage.Sensor Calibration:
Regularly check and calibrate temperature sensors, pressure gauges, and control panels to ensure accurate readings.Cleaning:
Remove dust, soot, and any residue that may accumulate over time. A clean furnace operates more efficiently and reduces the risk of malfunction.
10.2 Scheduled Maintenance Tasks
Component Replacement:
Replace parts such as tungsten fasteners, molybdenum rings, and heater accessories as needed, following manufacturer recommendations.Insulation Checks:
Ensure that all insulation materials are intact and effective. Damaged insulation can lead to heat loss and increased energy consumption.System Calibration:
Perform routine calibration of the furnace’s control systems to maintain the desired operating parameters and prevent over-heating or under-heating.
10.3 Documentation and Record-Keeping
Maintaining detailed records of all maintenance activities, repairs, and inspections is crucial. This documentation helps identify recurring issues, schedule future maintenance, and provide valuable information for troubleshooting unexpected problems.
Chapter 11
11. Detailed Look at Specialized Furnace Components
Advanced furnace systems rely on a myriad of specialized parts to deliver precise and consistent performance. Below is a deeper dive into several components that are frequently referenced in high-performance furnace assemblies.
11.1 Tungsten-Based Components
Tungsten Bracket & Fasteners:
These components ensure that the furnace structure remains stable during operation. Due to tungsten’s high strength and thermal stability, these brackets and fasteners withstand extreme conditions without significant wear.Tungsten Twisted Wire & Threaded Bars:
Critical for electrical applications within the furnace, these elements are used to create efficient and durable electrical connections, ensuring rapid and even heating.Tungsten Heater & Heater Accessories:
In vacuum furnaces, tungsten heaters are used to generate the necessary heat while maintaining uniform temperature distribution. Accessories such as mounting brackets and connectors play a vital role in ensuring the heaters are securely positioned and function reliably under prolonged operation.Tungsten Hooks:
Serving as support or suspension devices, tungsten hooks help in the installation and maintenance of internal furnace components, ensuring that heavy or delicate parts remain secure during thermal cycling.
11.2 Molybdenum Components
Molybdenum Fastener & Rings:
These parts are chosen for their excellent resistance to high temperatures and corrosion. Molybdenum rings are often utilized in sealing applications to maintain the integrity of the vacuum within the furnace chamber, while fasteners keep all components securely in place.
11.3 W-Cu Alloy Parts
Application in Thermal Management:
W-Cu alloy parts are critical when rapid heat dissipation is necessary. Their hybrid properties—combining the durability of tungsten with the high conductivity of copper—make them indispensable in parts where precise thermal management is required.
11.4 Contact and Identification
In many industrial catalogs, part numbers and contact details such as “93012345678” may be provided to assist customers in identifying and ordering the right components. Such details ensure that buyers have direct access to suppliers for inquiries related to tungsten heater accessories, molybdenum fasteners, or any other specialized furnace parts.
Chapter 12
12. Integrating Advanced Furnace Components for Optimal Performance
Modern furnace systems are the result of decades of innovation in materials science and engineering. By integrating advanced components—such as tungsten and molybdenum-based parts—manufacturers can achieve:
Enhanced Reliability:
Each component is designed to perform optimally under extreme conditions, reducing the risk of unexpected breakdowns.Increased Efficiency:
High-quality materials and precise engineering lead to better thermal management, which translates into energy savings and more consistent processing outcomes.Extended Operational Life:
Using advanced alloys and engineered designs minimizes wear and tear, prolonging the service life of furnace components and reducing overall maintenance costs.
12.1 Synergy of Parts and Assembly
The synergy between different furnace components is critical. For example:
A Tungsten Vacuum Furnace Chamber benefits from the integration of tungsten heaters, brackets, and fasteners, ensuring that the entire system operates seamlessly at high temperatures.
Molybdenum Accessories such as fasteners and rings enhance the durability and stability of the chamber, particularly in applications where minor fluctuations in temperature could otherwise lead to material degradation.
Complementary Materials such as the W-Cu alloy parts improve heat distribution across the furnace, ensuring that no single component is subject to undue thermal stress.
The careful selection and integration of these components result in a furnace that not only meets but often exceeds modern industrial performance and safety standards.
Chapter 13
13. The Future of Furnace Technology
As industrial processes continue to evolve, so too does the technology behind furnace systems. Innovations in materials, such as advanced composites and refractory metals, are paving the way for furnaces that are more efficient, environmentally friendly, and capable of reaching even higher temperatures.
13.1 Sustainability and Energy Efficiency
The drive toward sustainable industrial practices has spurred the development of furnaces with reduced energy consumption and lower emissions. Vacuum furnaces, in particular, are a focus of research due to their ability to operate in controlled environments that minimize fuel waste and prevent the formation of pollutants.
13.2 Smart Maintenance and Diagnostics
Emerging trends in smart manufacturing are influencing furnace design. With the integration of IoT (Internet of Things) sensors and real-time diagnostic systems, operators can now monitor furnace performance continuously. This connectivity allows for predictive maintenance, where potential issues are flagged before they lead to critical failures, thereby minimizing downtime and extending the service life of furnace components.
13.3 Customization and Modularity
The future of furnace design also lies in modularity—allowing for custom configurations tailored to specific industrial needs. Whether it is a tungsten vacuum furnace chamber designed for ultra-high-temperature applications or a molybdenum chamber optimized for chemical stability, the ability to customize components will drive efficiency and performance improvements across a wide range of industries.
Chapter 14
14. Frequently Asked Questions
1. What is a furnace chamber?
A furnace chamber is the main heating area inside a furnace where materials are processed. In vacuum furnaces, the chamber is typically made of high-temperature-resistant materials such as molybdenum or tungsten to withstand extreme heat and vacuum conditions.
2. What is the difference between molybdenum and tungsten vacuum furnace chambers?
- Molybdenum (Mo) chamber: Suitable for 1300°C to 2000°C, commonly used for heat treatment, sintering, and metal melting.
- Tungsten (W) chamber: Can withstand temperatures above 2000°C, ideal for ultra-high-temperature applications, such as carbon material sintering or special alloy melting.
3. How much does it cost to replace a furnace combustion chamber?
The cost depends on the type, size, and material of the chamber. Typically:
- Industrial furnace combustion chamber replacement: $5,000–$50,000
- Residential furnace combustion chamber replacement: $500–$2,500
4. What is the room with the furnace called?
The room where a furnace is located is often called a boiler room or mechanical room in industrial and commercial settings. In homes, furnaces are commonly found in the basement, garage, or dedicated furnace room.
5. What is the difference between a furnace and a combustion chamber?
- Furnace: Refers to the entire heating system, including the combustion chamber, heat exchanger, and control system.
- Combustion chamber: The specific part of the furnace where fuel combustion occurs to generate heat.
6. When should a combustion chamber be replaced?
A combustion chamber should be replaced if it shows signs of:
- Metal corrosion or cracks (reducing efficiency)
- Incomplete combustion or excessive carbon buildup
- Decreased energy efficiency with increased heat loss
- Gas leaks or unusual odors, which may indicate a safety hazard
7. What is a tungsten electrode?
A tungsten electrode is a high-temperature, highly conductive material used in welding, vacuum furnace heating, and plasma discharge applications.
8. What is the difference between tungsten and molybdenum fasteners?
- Tungsten fasteners: Have a higher temperature resistance (above 2500°C) but are more brittle, making them suitable for extreme environments.
- Molybdenum fasteners: Can withstand up to 2000°C, offering better mechanical strength and flexibility, commonly used in high-temperature furnaces and electronics.
9. Why use a tungsten heater?
Tungsten heaters offer:
- Exceptional high-temperature resistance (up to 3000°C)
- Superior thermal conductivity
- Strong oxidation resistance in vacuum conditions
They are widely used in high-temperature sintering, semiconductor manufacturing, and aerospace materials processing.
10. Can an old furnace be upgraded?
Yes, an old furnace can be upgraded by:
- Replacing heating elements
- Upgrading the control system
- Installing a new combustion chamber
This can improve energy efficiency and extend the furnace’s lifespan.
11. How to maintain a furnace properly?
- Regularly inspect the combustion chamber and heating elements for damage
- Clean the furnace chamber to prevent carbon buildup and oxidation
- Check and tighten fasteners
- Ensure the vacuum system is properly sealed
12. What is tungsten-copper alloy (W-Cu)?
Tungsten-copper alloy combines tungsten’s high melting point with copper’s excellent thermal conductivity, making it ideal for high-temperature electrodes, heat sinks, and electronic packaging materials.
Chapter 15
15. Conclusion
The evolution of furnace technology—from traditional combustion systems to advanced vacuum furnaces—has been driven by the need for greater efficiency, safety, and precision in high-temperature processing. In this article, we have explored the critical elements of modern furnace systems:
Chamber Furnaces and Vacuum Furnaces:
Defined by their enclosed, controlled environments that prevent oxidation and ensure uniform heating.Material Innovations:
With materials such as tungsten and molybdenum providing unmatched thermal resistance and durability, modern vacuum furnace chambers can operate under the most extreme conditions.Key Components and Accessories:
From tungsten brackets and twisted wires to molybdenum rings and W-Cu alloy parts, every component plays a pivotal role in maintaining the integrity and performance of the furnace.Economic and Operational Considerations:
Understanding the cost of replacing combustion chambers, recognizing when to undertake repairs, and investing in modern furnace systems can yield significant long-term benefits for industrial operations.Maintenance and Upgrades:
Daily maintenance, scheduled inspections, and a proactive approach to repair and replacement ensure that furnace systems continue to operate at peak performance, thereby safeguarding both the equipment and the productivity of the facility.
As industries continue to push the boundaries of material science and engineering, the demand for high-performance furnaces will only grow. By embracing the latest technologies and maintaining a robust preventive maintenance program, companies can ensure that their furnace systems not only meet the current demands of production but are also poised to take advantage of future innovations.
Whether you are considering a transformation of an old furnace system, planning a comprehensive repair program, or evaluating the next generation of furnace accessories and parts, understanding the role of each component—from the tungsten heater accessories to the molybdenum fasteners—is essential for long-term success in high-temperature processing.
For further inquiries, product details, or technical support, companies often provide contact numbers such as “93012345678” to ensure that customers can get the specialized assistance they need for everything from furnace repair and replacement to daily maintenance best practices.
In summary, the integration of advanced materials and meticulous design in modern furnace systems ensures not only enhanced operational efficiency but also greater safety and reliability. By investing in quality furnace components and following rigorous maintenance protocols, industries can continue to innovate and achieve superior results in high-temperature processing.