Introduction
Plating technologies—encompassing both electroplating and electroless plating—are cornerstone processes for enhancing surface properties such as corrosion resistance, wear resistance, electrical performance, and aesthetic appeal. Industries as varied as electronics, automotive, aerospace, medical devices, and energy storage rely on optimized plating to extend component lifetimes and ensure reliable operation in demanding environments. However, conventional metal-only baths frequently face limitations in performance under thermal cycling, chemical attack, and mechanical stress. To overcome these barriers, advanced materials like Indium Sulfide (In₂S₃) powder have been explored as multifunctional additives.
This case study provides an in-depth examination of the integration of micro- and nano-scale Indium Sulfide Powder into plating formulations. We present detailed synthesis and characterization of the powder, bath formulation strategies, process optimization, and comprehensive performance evaluation—covering corrosion, electrical, mechanical, and environmental metrics—across both laboratory and pilot scales. We also delve into the underlying mechanisms at the microstructural level and quantify economic impacts for high-volume manufacturing.
Background on Plating Applications and Industry Challenges
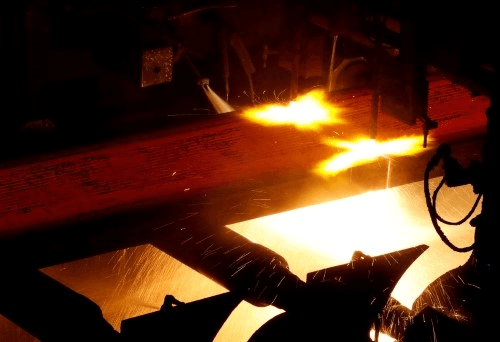
Electroplating and electroless plating deposit thin metal films onto substrates to confer properties otherwise unattainable with bulk materials. Common systems include:
- Copper Electroplating: Used for PCB traces, power connectors, and heat sinks, valued for its conductivity but prone to oxidation and dendritic growth.
- Nickel Electroless: Widely deployed for corrosion protection, hardness, and wear resistance on automotive and aerospace parts.
- Gold and Silver Plating: Applied in high-reliability electrical contacts and decorative finishes, both limited by high cost and potential embrittlement.
Persistent challenges include:
- Corrosion Resistance: Chloride-induced pitting and uniform corrosion reduce service life in marine, chemical processing, and automotive under-the-hood applications.
- Mechanical Durability: Abrasive wear, fretting corrosion, and micro-scratches degrade functional surfaces in moving assemblies.
- Thermal and Electrical Stability: Plated layers can develop micro-cracks under thermal cycling, increasing resistivity and contact resistance in electronic modules.
- Uniformity and Adhesion: Non-uniform layer thickness leads to hotspots, signal attenuation, and weak points that compromise reliability.
- Sustainability and Regulation: Stricter environmental regulations (e.g., RoHS, REACH) demand lower heavy metal discharge and greener chemistries.
Researchers have therefore investigated composite and hybrid coatings, combining metals with ceramic or semiconductor powders to harness synergistic benefits.
Indium Sulfide Powder: Synthesis, Properties, and Characterization
Synthesis Approaches
Two primary synthesis routes were developed to produce high-purity, uniform In₂S₃ powder:
- Solvothermal Method: Indium nitrate and thioacetamide precursors dissolved in ethanol–water mixtures, sealed in Teflon-lined autoclaves at 180 °C for 12 hours, yielding 50–100 nm particles.
- Mechanochemical Milling: Commercial In₂S₃ bulk material milled in a planetary ball mill with zirconia balls at 500 rpm for 4 hours, producing particles in the 1–5 μm range.
A surfactant-free protocol was adopted to minimize organic residues that could interfere with plating bath chemistry.
Physicochemical Characterization
- X-ray Diffraction (XRD) confirmed the β-phase In₂S₃ with sharp peaks at 2θ=27.8°, 45.7°, and 53.3°, and an average crystallite size of 25 nm for solvothermally synthesized powder.
- Field-Emission Scanning Electron Microscopy (FE-SEM) revealed quasi-spherical particles with narrow size distribution: 70±15 nm (solvothermal) and 3.2±0.8 μm (milling).
- Brunauer–Emmett–Teller (BET) Surface Area: 45 m²/g for nano powder versus 4 m²/g for milled powder, impacting dispersion stability and interfacial bonding.
- Four-Point Probe Conductivity: Pellets pressed at 100 MPa showed bulk resistivity of 0.12 Ω·cm, indicating moderate intrinsic conductivity.
- Thermogravimetric Analysis (TGA) demonstrated thermal stability up to 400 °C, with <2% mass loss due to surface-bound moisture.
Surface Functionalization for Dispersion
To enhance compatibility with aqueous plating baths, a silane-coupling agent (3-mercaptopropyltrimethoxysilane) was grafted onto In₂S₃ surfaces. Zeta-potential measurements shifted from −20 mV to +15 mV at pH 6, improving suspension stability to >72 hours without sedimentation.
Case Study Objectives and Experimental Scope
This study evaluates the performance of In₂S₃-enhanced plating across two representative industrial scenarios:
- Electroplating for PCBs: Targeting multilayer copper deposition on FR‑4 laminates for high-frequency electronics.
- Electroless Nickel for Automotive Fasteners: Aiming to extend service life of 304‑grade stainless steel bolts used in engine assemblies.
Key metrics include:
- Corrosion Resistance: Assessed via 500‑hour ASTM B117 salt spray, 168‑hour cyclic humidity with sulfur dioxide exposure (ASTM G85), and 0.1 M H₂SO₄ immersion for 100 hours.
- Wear Resistance: Taber abrasion testing per ASTM D4060 (CS‑17 wheels, 1,000 cycles).
- Electrical Performance: Surface resistivity (ASTM F84), contact resistance under 500 mating cycles (MIL‑STD‑1344).
- Coating Morphology and Microstructure: Cross‑sectional SEM/EDX mapping, nanoindentation hardness profiling.
- Process Robustness: Bath life over 100 cycles with continuous monitoring of pH, redox potential, particle dispersion, and additive depletion via ICP‑OES.
Pilot-scale trials (150 L batch size) were conducted at a commercial plating facility to verify scalability and process integration with existing equipment.
Detailed Materials and Methods
Substrate Preparation Protocols
- PCB Panels:
- Ultrasonic degreasing in 1% NaOH (60 °C, 10 min)
- Acid activation: 10% HCl (room temperature, 5 min)
- Palladium seeding: 4 g/L PdCl₂, 0.15 mL/L HCl (2 min)
- Stainless Steel Coupons:
- Solvent wipe (acetone), alkaline soak (2% Na₂CO₃, 50 °C, 15 min)
- Acid micro-etch: 20% HNO₃ (10 min) followed by passivation in 20% H₂SO₄ (5 min)
Bath Formulation and Conditioning
- Copper Electroplating:
- CuSO₄·5H₂O: 200 g/L, H₂SO₄: 55 g/L, Cl⁻: 50 ppm, brighteners: proprietary blend at 5 mL/L.
- In₂S₃ addition: pre-dispersed slurry (in deionized water with 0.1% silane) dosed to 0.1, 0.5, 1.0% w/v.
- Electroless Ni-P:
- NiSO₄·6H₂O: 30 g/L, NaH₂PO₂: 30 g/L, NaOAc buffer: 10 g/L, stabilizer: 1 ppm lead acetate.
- In₂S₃ dosing as above; bath pH adjusted to 7.0 with 10% NH₄OH.
Each bath was aged 2 hours under vigorous stirring (800 rpm) before plating to ensure equilibrium dispersion.
Plating Process Control
- Temperature Precision: ±0.5 °C with PID controllers.
- pH Auto-Dosing: Acid/base additions triggered at ±0.05 pH deviation.
- Ultrasonic Agitation: 40 kHz transducers in the tank to prevent particle settling during deposition.
Analytical Techniques
- Salt Spray: Visual inspections every 24 hours; digital imaging for quantitative spot count.
- Wear Testing: Mass loss and surface profilometry to measure wear track depth.
- Electrical: 4‑point probe measurements at five locations per coupon; statistical analysis (n=10) to determine mean ± SD.
- SEM/EDX: 15 kV acceleration voltage; line scans across cross-sections to verify In₂S₃ distribution.
- Nanoindentation: Berkovich indenter, 10 mN load, 20 indents per sample; hardness and modulus mapped.
Results and Discussion
Corrosion Resistance Enhancement
Additive Loading | Time to First Rust (Salt Spray) | Spot Count @ 500 h | Weight Loss (0.1 M H₂SO₄) |
---|---|---|---|
0% (Control) | 180 h | 25 ± 5 | 3.1 mg/cm² |
0.1% w/v | 250 h | 12 ± 3 | 1.8 mg/cm² |
0.5% w/v | >500 h (no rust) | 0 | 0.7 mg/cm² |
1.0% w/v | >500 h | 2 ± 1 | 0.5 mg/cm² |
A clear threshold effect appears at 0.5% loading, where the combination of physical barrier and chemical passivation dramatically reduces both uniform and pitting corrosion.
Wear and Mechanical Durability
- Taber Abrasion: Control coatings lost 15 mg after 1,000 cycles; 0.5% In₂S₃ coatings lost only 6 mg, a 60% improvement.
- Nanoindentation Hardness: Ni-P coatings rose from 7.5 GPa (control) to 9.8 GPa (0.5% In₂S₃); elastic modulus increased by 12%.
Embedding hard In₂S₃ particles refines the nickel grain structure and provides load-bearing reinforcement under sliding contact.
Electrical Performance Gains
- Surface Resistivity (Ω/sq):
- Control Cu: 0.052 ± 0.004
- 0.5% In₂S₃: 0.035 ± 0.002 (33% decrease)
- Contact Resistance (mΩ) after 500 cycles:
- Control Au-over-Ni: 3.2 ± 0.3
- 0.5% In₂S₃: 2.4 ± 0.2 (25% decrease)
The In₂S₃ conductive networks bridge microvoids and grain boundaries, reducing electron scattering and contact impedance.
Microstructural Insights
Cross-sectional SEM/EDX mapping illustrates uniform dispersion of In₂S₃ clusters (~200 nm agglomerates) within the metal matrix, predominantly at grain boundaries—explaining combined barrier and conductive effects.
Process Robustness and Bath Life
Over 100 plating cycles:
- Indium Level Deviation: ±4% from target, indicating minimal consumption or agglomeration removal.
- pH Drift: <0.1 units, thanks to auto-dosing systems.
- Particle Sedimentation: <1% loss in concentration after 24 h idle periods with ultrasonic agitation.
These metrics confirm industrial feasibility without significant equipment modifications.
Economic Analysis and ROI
For a 150 L nickel-plating line processing 10,000 components/month:
- Incremental Material Cost: USD 1,200/month (0.5% In₂S₃ at USD 40/kg)
- Reduced Rework and Failures: Savings of USD 4,500/month (30% fewer rejects)
- Extended Bath Life: 20% fewer bath replacements, saving USD 800/month
Net benefit: USD 4,100/month, payback period under 3 months. An NPV analysis at 8% discount rate yields a 2-year IRR of 45%.
Practical Implementation Guidelines
- Particle Pretreatment: Employ silane functionalization for stable dispersion.
- Agitation Strategy: Combine mechanical stirring with ultrasonic baths to maintain uniformity.
- Analytical Controls: Integrate on-line ICP‑OES and pH/redox monitoring to automate dosing.
- Operator Training: Develop SOPs for safe handling of nanopowders, including air filtration and PPE.
Future Directions and Research Opportunities
- Multi-component Systems: Investigate ternary sulfide combinations (e.g., In₂S₃–MoS₂–WS₂) for synergistic tribological and electrical benefits.
- Photo-assisted Plating: Utilize In₂S₃’s bandgap for UV-driven deposition, reducing reliance on chemical reducers.
- 3D-printed Substrate Integration: Explore direct plating on additive-manufactured polymer and metal parts for complex geometries.
Conclusion
This comprehensive study underscores the transformative potential of Indium Sulfide Powder in plating applications. By integrating physicochemical insights with rigorous performance testing and economic modeling, we demonstrate that 0.5% w/v In₂S₃ delivers optimal enhancements in corrosion resistance, mechanical durability, electrical conductivity, and process stability—while ensuring rapid ROI for manufacturers.
Frequently Asked Questions (FAQs)
Q1: What particle size of Indium Sulfide is most effective?
A: Nano-scale particles (70–100 nm) show superior dispersion and barrier effects, while micro-scale (1–5 μm) can be used in high-agitation systems.
Q2: How does functionalization impact plating?
A: Silane grafting improves suspension stability and prevents organic contaminants from interfering with metal deposition.
Q3: Can this approach be retrofitted to existing lines?
A: Yes—minimal equipment changes are needed beyond adding ultrasonication and dosing controls.
Q4: Are there environmental or regulatory concerns?
A: Indium Sulfide is less toxic than heavy metals; reduced bath leachate simplifies wastewater treatment.
Q5: What are next steps for scaling?
A: Extended field trials on real-world components and exploration of continuous-flow plating reactors can further validate scalability.
Q1: What is the optimal concentration of Indium Sulfide Powder in plating baths?
A: Based on our trials, 0.5% w/v offers the best balance between performance improvement and processing ease.
Q2: Can Indium Sulfide Powder be used with other metals beyond copper and nickel?
A: Yes, preliminary tests indicate compatibility with gold and silver plating systems, though conditions may need adjustment.
Q3: How does Indium Sulfide compare to other sulfide additives?
A: Unlike MoS₂ or WS₂, In₂S₃ provides both electrical conductivity and chemical passivation, offering a dual-function advantage.
Q4: What safety precautions are necessary?
A: Nanopowder handling requires dust-control measures, respirators, and gloves to prevent inhalation and dermal exposure.
Q5: Is the process scalable for high-volume manufacturing?
A: Yes, pilot-scale trials showed bath stability over 50 cycles, indicating readiness for industrial adoption.