Pipes & Tubes
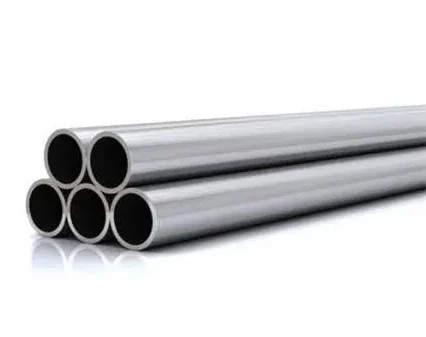
Molybdenum Tube
Molybdenum Tubes, Capillaries, and Pipes (Moly Tubing) are widely used in modern industries. TFM Engineering is a reliable supplier of quality seamless and welded Molybdenum & TZM Tubes, Pipes, and Capillaries.
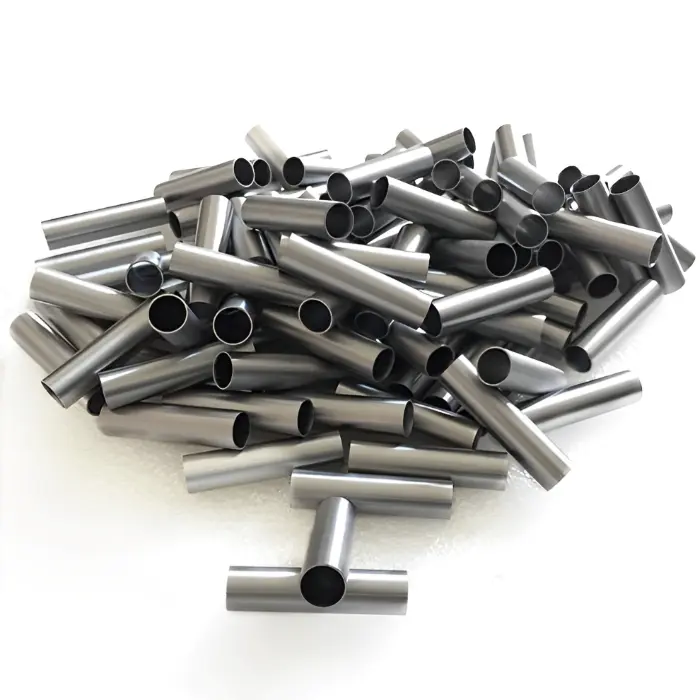
Tungsten Tube
TFM provides Tungsten Tubes with high purity (≥ 99.95%) as well as Tungsten Carbide Tubes and Tungsten Alloy Tubes. Feel free to request a quote for tungsten and tungsten based tubes, rings and pipes.
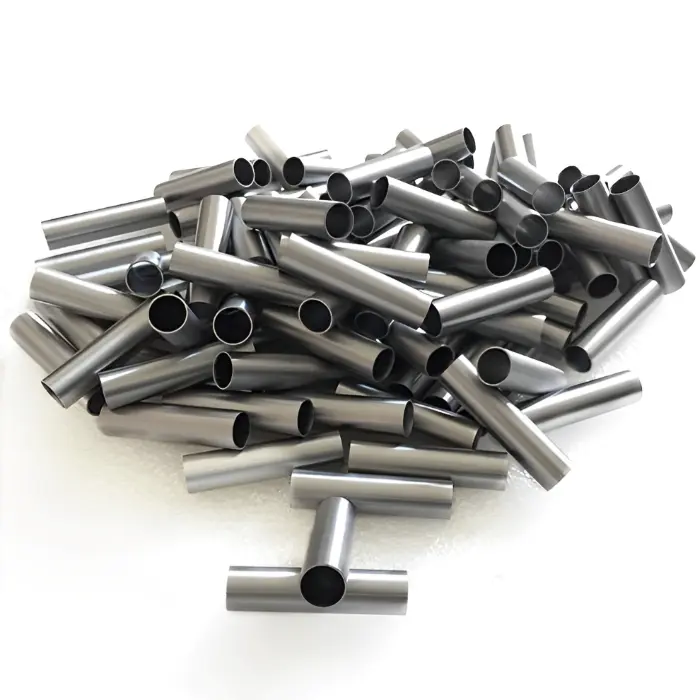
Tantalum Tube
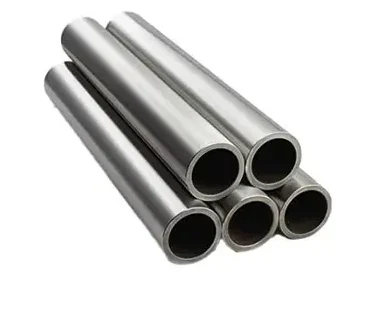
Niobium Tube
TFM brings you over ten years of expertise in delivering top-notch Niobium Tubes and Pipes at affordable prices. We’re flexible in customizing this product according to your specific requirements.
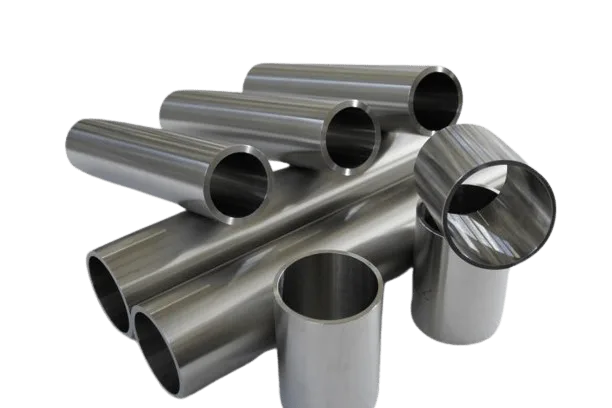
Titanium Tube Pipe
TFM offers a wide range of titanium tubing products, including seamless tubing, welded tubing, spiral tubing, titanium capillary tubing, U-bent tubing, titanium tubing stub ends, and titanium screwed fittings.
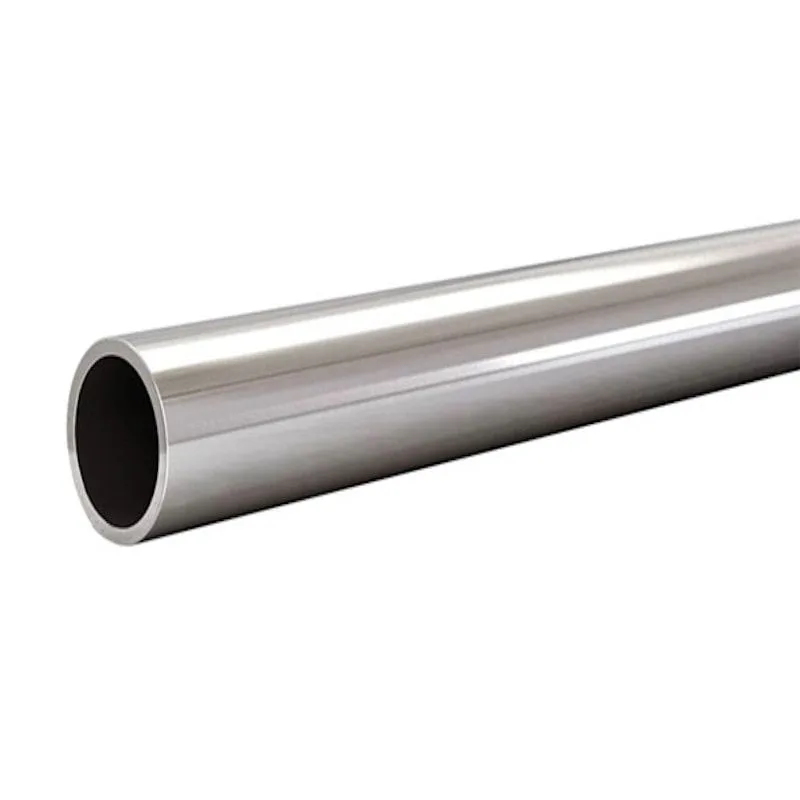
Zirconium Tube
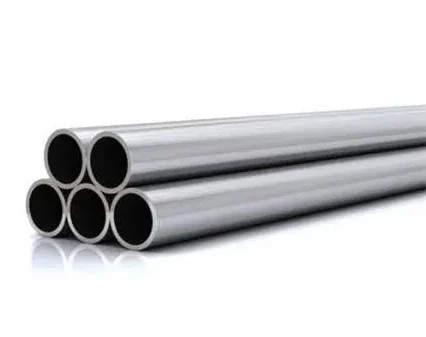
Hafnium Tube
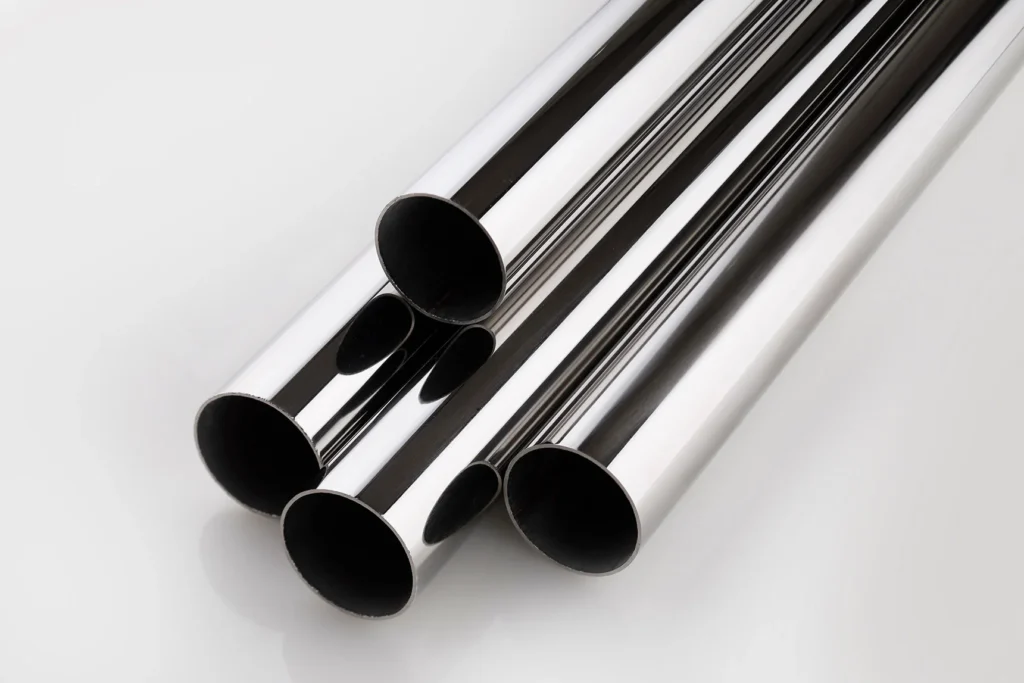
Chromium Tube
At TFM, with our expertise in manufacturing Chromium and Chromium Alloy Tubes to exacting standards and our unwavering commitment to quality assurance, we stand ready to meet the diverse needs of our customers, delivering excellence and innovation in every Chromium Tube we produce.
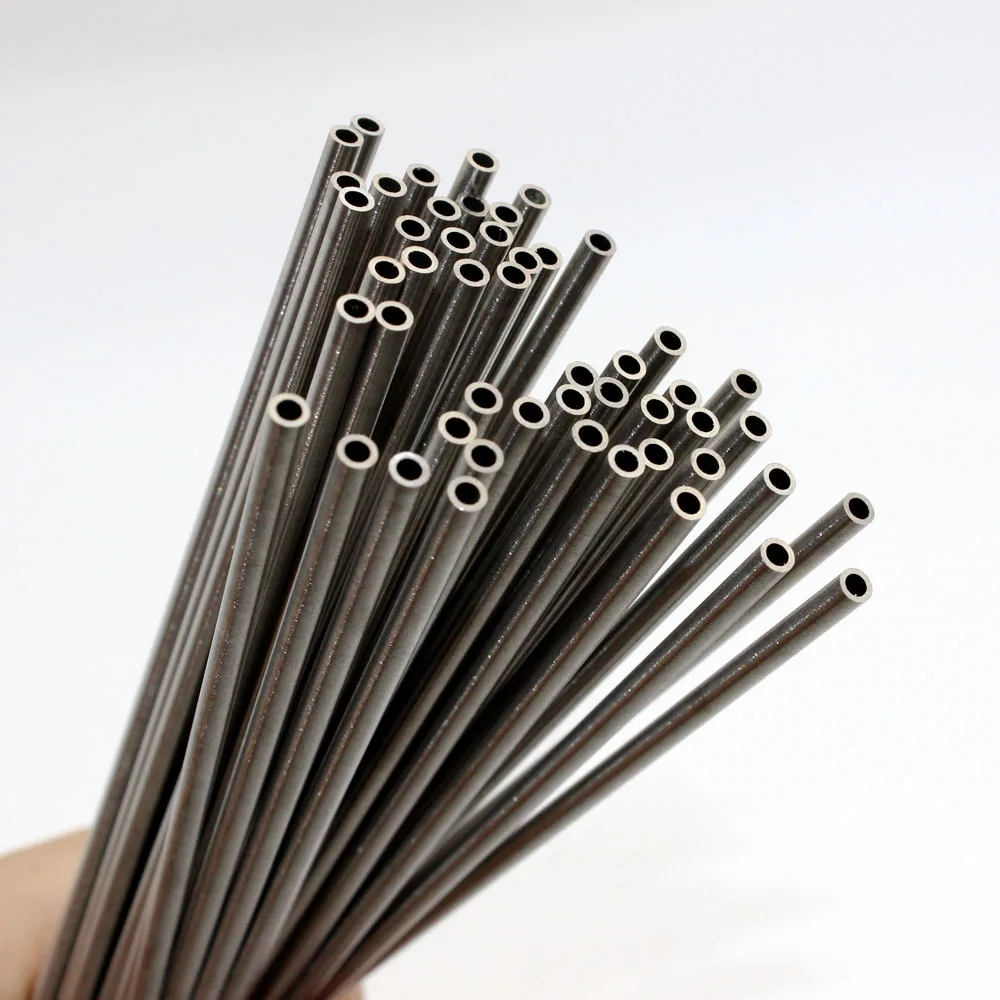
Nickel Tube
TFM is a professional Nickel Tube and Capillary manufacturer and supplier. We can provide seamless Nickel and Nickel alloy tubes with short lead times and good prices.
High-Performance Metal Tubes and Fittings: Properties, Manufacturing, Applications, and Market Insights
This article provides a comprehensive overview of high-performance metal tubes and fittings, focusing on materials such as Molybdenum Tube, Tungsten Tube, Tantalum Tube, Niobium Tube, Titanium Pipe, Zirconium Tube, Hafnium Tube, Chromium Tube, and Nickel Tube. Each metal’s physical and chemical properties, manufacturing techniques—including powder metallurgy, hot extrusion, cold rolling, and cold drawing—and standard specifications are discussed in detail. The article further explores their applications across key industries such as aerospace, nuclear energy, petrochemicals, medical devices, electronics, and marine engineering.
Current market trends, including the increasing demand for corrosion-resistant tubing, miniaturized components, and high-temperature alloys, are analyzed alongside challenges such as raw material supply instability, rising production costs, and geopolitical constraints. The future outlook highlights technological innovation and the growing importance of advanced tubing solutions in next-generation reactors, space exploration, and semiconductor fabrication.
Table of Contents
Chapter 1
Introduction
In today’s advanced engineering and industrial landscape, high-performance metal tubes play a critical role in a wide array of applications ranging from aerospace and nuclear energy to petrochemical processing, medical devices, electronics, and marine engineering. Materials such as Molybdenum, Tungsten, Tantalum, Niobium, Titanium, Zirconium, Hafnium, Chromium, and Nickel are renowned for their exceptional resistance to corrosion, high strength at elevated temperatures, and superior mechanical properties. This article provides a detailed technical and market overview of these materials, covering their physical and chemical properties, state-of-the-art production processes (including powder metallurgy, cold rolling, hot extrusion, and cold drawing), the typical dimensions and specifications according to international standards, and the industries in which they excel.
TFM, recognized as a leader and reliable supplier in this field, offers these advanced metal tubes and tailored solutions to meet the high demands of modern engineering challenges. In the following sections, we will explore the nuances of each metal, analyze market trends and industry challenges, and answer the most frequently asked questions related to these high-performance products—all while integrating 12 of the most searched keywords, such as high performance metal tubing, molybdenum tube supplier, titanium pipe specifications, tantalum tube prices, niobium tube applications, zirconium tube standards, wrought tungsten tube, chromium tube manufacturers, nickel tube suppliers, advanced metal tube production, cold drawn metal tubing, and powder metallurgy tube.
Chapter 2
I. Material Analysis and Production Techniques
1. Molybdenum Tube
Physical and Chemical Characteristics:
Molybdenum exhibits excellent high-temperature stability and retains high strength even when subjected to extreme heat. Chemically, it is notable for its resistance to corrosion and oxidation in controlled environments. These properties make molybdenum an ideal candidate for applications in aerospace engines and nuclear reactors.
Production Process:
Molybdenum tubes are frequently produced using powder metallurgy techniques. In this process, fine molybdenum powders are pressed into shape, followed by sintering, which involves heating the pressed powders at high temperatures under controlled atmospheres. Additional processes such as cold drawing improve dimensional accuracy and surface finish.
Typical Dimensions and Standards:
Standard dimensions vary considerably with diameter and wall thickness tailored to specific operational environments. International standards such as ASTM B770 and ISO 5600 provide guidelines to ensure quality and consistency in production.
2. Tungsten Tube
Physical and Chemical Characteristics:
Tungsten is renowned for its high melting point and exceptional hardness. Its excellent thermal conductivity and low vapor pressure make it particularly useful in high-temperature applications such as electrodes and specialized industrial furnaces.
Production Process:
Wrought tungsten tubes are manufactured using a combination of hot extrusion and cold drawing. The hot extrusion process is used to form the initial tube shape, followed by cold drawing to achieve the desired surface finish and dimensional tolerances.
Typical Dimensions and Standards:
Critical dimensions are regulated by international standards like ASTM B777 and ISO 4958, which specify properties such as tensile strength, ductility, and wall thickness.
3. Tantalum Tube
Physical and Chemical Characteristics:
Tantalum is characterized by its superb corrosion resistance and biocompatibility. Its inertness makes tantalum ideal for applications in chemical processing, medical devices, and electronics.
Production Process:
Tantalum tubes are often fabricated using powder metallurgy, then refined through cold rolling and drawing to meet tight dimensional tolerances. The use of vacuum processing minimizes contamination and ensures purity, critical for sensitive applications.
Typical Dimensions and Standards:
International standards such as ASTM B763 delineate the precise dimensions and performance criteria, ensuring that tantalum tubes meet stringent quality requirements required in medical and electronic components.
4. Niobium Tube
Physical and Chemical Characteristics:
Niobium is prized for its excellent formability, superconducting properties, and stability in corrosive environments. It is extensively used in the aerospace and nuclear industries.
Production Process:
Niobium tubes are produced using advanced methods such as hot extrusion and cold drawing, ensuring minimal impurities and superior mechanical properties. The production techniques emphasize precision and efficiency to meet the high standards required in scientific and industrial sectors.
Typical Dimensions and Standards:
Products follow standards such as ASTM B370, which outline critical parameters including mechanical strength, heat treatment properties, and dimensional consistency.
5. Titanium Tube/Pipe
Physical and Chemical Characteristics:
Titanium exhibits an exceptional strength-to-weight ratio, excellent corrosion resistance, and biocompatibility. Its lightweight yet robust properties are particularly valued in aerospace, marine, and medical industries.
Production Process:
Techniques such as hot and cold forming are commonly used to produce titanium tubes. Processes such as laser cutting and automated welding are applied to achieve precise specifications and intricate designs. Post-production heat treatments ensure mechanical properties conform to performance standards.
Typical Dimensions and Standards:
Standards such as ASTM B381 and ASTM B381A and ISO 5832 provide clear guidelines for the dimensions, wall thickness, and purity levels required for various titanium tube applications.
6. Zirconium Tube
Physical and Chemical Characteristics:
Zirconium is noted for its exceptional resistance to corrosion, particularly in environments with high concentrations of acids and bases. Its low thermal neutron absorption cross-section makes it indispensable in nuclear reactor applications.
Production Process:
The production of zirconium tubes involves both powder metallurgy and hot rolling techniques. Maintaining a controlled atmosphere throughout the process is critical to prevent contamination and ensure the high purity required for nuclear and chemical applications.
Typical Dimensions and Standards:
Products are manufactured to meet stringent standards such as ASTM B333 and ISO 7199, ensuring consistency in performance, particularly in challenging environments.
7. Hafnium Tube
Physical and Chemical Characteristics:
Hafnium shares many similarities with zirconium; however, it boasts a higher density and melting point. Its excellent corrosion resistance and high-temperature capabilities make it ideal for use in advanced nuclear and aerospace applications.
Production Process:
Hafnium tubes are primarily produced using advanced hot extrusion and cold drawing methods. These processes are closely monitored to achieve the fine tolerances and surface finishes required in precision applications.
Typical Dimensions and Standards:
The production specifications for hafnium products are set forth by standards such as ASTM B760, ensuring that dimensions, tolerances, and chemical composition are maintained.
8. Chromium Tube
Physical and Chemical Characteristics:
Chromium is widely recognized for its exceptional hardness, high corrosion resistance, and ability to withstand severe operating conditions. It is a key component in stainless steel alloys and is used in applications ranging from automotive to chemical processing.
Production Process:
Chromium tubes are produced via hot extrusion, followed by cold drawing to enhance surface finish and mechanical properties. These processes are optimized to ensure high production yields and consistency.
Typical Dimensions and Standards:
International standards such as ASTM B527 outline the necessary specifications, including tensile strength and elongation values, to ensure chromium tubes meet operational demands in harsh environments.
9. Nickel Tube
Physical and Chemical Characteristics:
Nickel tubes are renowned for their excellent corrosion resistance, especially in high-temperature and high-pressure environments. They also exhibit strong thermal conductivity and are used extensively in chemical and power generation industries.
Production Process:
Nickel tubes are often manufactured using advanced powder metallurgy combined with cold rolling and drawing techniques. These methods enhance the mechanical properties, making nickel tubes particularly suited for environments exposed to aggressive chemicals.
Typical Dimensions and Standards:
Products adhere to standards such as ASTM B370 and ISO 13464, which define the dimensional tolerances, corrosion resistance, and mechanical performance expected from nickel tubes.
Chapter 3
II. Production Techniques and International Standards
Advanced Production Techniques
High-performance metal tubes are produced through several sophisticated processes:
Powder Metallurgy Tube: In this process, fine metallic powders are compacted and sintered under high temperatures. This method allows precise control over the tube’s final microstructure and composition. Powder metallurgy is common for refractory metals like molybdenum, tungsten, and tantalum.
Cold Rolling and Cold Drawn Metal Tubing: Cold rolling reduces the thickness of metal tubes while enhancing mechanical properties, and cold drawing refines the shape and surface finish without additional heat treatment. These processes are essential for achieving the high dimensional accuracy demanded by the aerospace and medical industries.
Hot Extrusion and Hot Rolling: These high-temperature processes facilitate the shaping of metals that require substantial deformation resistance, such as titanium and niobium. The application of hot extrusion helps in forming the initial profile, while hot rolling refines dimensions and helps in achieving an improved grain structure.
Conformance to International Standards
Each type of metal tube must adhere to international standards to ensure safety, reliability, and performance in critical applications. For example:
ASTM and ISO Standards: Standards such as ASTM B770 for molybdenum, ASTM B777 for tungsten, ASTM B763 for tantalum, ASTM B370 for niobium and nickel, along with various ISO standards, are applied to regulate mechanical properties, purity, and dimensions.
Quality Assurance Practices: Rigorous testing protocols—including tensile strength tests, chemical composition analysis, and nondestructive testing techniques—ensure that the manufactured tubes meet the specific requirements of each industry.
Chapter 4
III. Application Analysis in Diverse Industries
Each material exhibits unique benefits that have led to widespread adoption across multiple industries:
Aerospace and Aviation
High-performance metal tubing in aerospace applications must meet strict weight, strength, and temperature requirements. Titanium Tube/Pipe, for example, is highly valued due to its strength-to-weight ratio and exceptional corrosion resistance. Similarly, molybdenum and tungsten tubes are used in engine components where high thermal stability is crucial. The advanced production techniques, including cold drawn metal tubing, help provide the precision needed for aerospace components.
Nuclear Energy
Nuclear applications require materials that can withstand high temperatures and corrosive environments while maintaining structural integrity. Zirconium Tubes are preferred for fuel rod assemblies due to their low neutron absorption cross-section and resistance to corrosion. Additionally, hafnium tubes, with their higher melting points, are used in control rod assemblies where extreme conditions are expected.
Petrochemical and Chemical Processing
In the petrochemical industry, chemical inertness and high pressure tolerance are imperative. Tantalum Tubes and Nickel Tubes are often selected for equipment exposed to corrosive chemicals. These materials ensure longevity and continuous operation even when exposed to acids, bases, and other aggressive compounds.
Medical and Pharmaceutical Devices
For medical applications, biocompatibility is a prime consideration. Materials like tantalum and titanium are used in surgical implants and medical devices, where their non-toxic nature and mechanical strength provide both safety and reliability. Strict adherence to international standards such as ASTM and ISO ensures that these tubes are safe for use in medical environments.
Electronics and Semiconductor Manufacturing
Metal tubes are essential components in the construction of semiconductor devices where precision and thermal management play significant roles. Materials such as niobium and tungsten offer outstanding electrical and thermal properties, making them ideal candidates for advanced electronic applications. The precision of production technologies like powder metallurgy tube production ensures that the dimensions and purity meet the exacting needs of semiconductor manufacturing.
Marine Engineering
In harsh marine environments, corrosion resistance is critical. Nickel and chromium tubes are widely used in marine applications due to their ability to withstand prolonged exposure to saltwater, extreme pressures, and temperature fluctuations. Advanced production methods help these materials maintain structural integrity over long service periods, contributing to reliability and safety in offshore structures and ships.
Chapter 5
Difference Between Pipes & Tubes
Pipes are classified as schedule and nominal diameter. They are typically ordered using the Nominal Pipe Size (NPS) standard and by specifying a nominal diameter (pipe size) and schedule number (wall thickness). The schedule number can be the same on different-sized pipes, but the wall thickness will differ.
Tubes are typically ordered to outside diameter and wall thickness; however, they may also be ordered as OD & ID or ID and Wall Thickness. The strength of a tube depends on the wall thickness. A gauge number defines the thickness of a tube. Smaller gauge numbers indicate larger outside diameters. The inside diameter (ID) is theoretical.
Tubes can be square, rectangular, or cylindrical, whereas piping is always round. The circular shape of the pipe evenly distributes the pressure force. Pipes accommodate larger applications ranging from ½ inches to several feet, whereas tubing is generally used in applications requiring smaller diameters.
Chapter 6
IV. Market Trends, Industry Challenges, and Future Perspectives
Current Market Trends
The market for high-performance metal tubing is influenced by several factors:
Rising Demand in High-Tech Industries: The continued growth of the aerospace, nuclear energy, and chemical processing sectors drives demand for advanced metal tubing.
Innovation in Production Processes: Ongoing improvements in manufacturing technologies, such as precision cold drawing and powder metallurgy, have significantly enhanced the quality and performance of metal tubes.
Integration of Digital Manufacturing: Increasing use of automation and data analytics in production processes is leading to more efficient and customized manufacturing solutions.
Sustainability and Recycling: There is a growing trend toward sustainable practices, including the recycling of rare and valuable metals, and reducing the environmental footprint during production.
Industry Challenges
Despite promising market trends, several challenges persist in this field:
Raw Material Supply Constraints: The availability and cost fluctuations of rare metals such as tungsten and tantalum can impact production stability. Strategic sourcing and long-term supplier relationships are essential.
Technical and Regulatory Standards: Meeting the rigorous international standards and obtaining necessary certifications requires continuous investment in quality control and advanced testing facilities.
Complex Production Techniques: The intricate processes involved in fabricating these high-performance tubes, including powder metallurgy and cold drawing, necessitate high precision and skilled labor, which can limit production scalability.
Global Competition: Intense competition among manufacturers worldwide requires continuous innovation and differentiation in terms of quality, delivery times, and customer service.
Future Development Directions
Looking forward, several key trends are likely to shape the future of the high-performance metal tubing market:
Advanced Materials Research: Continuous research in metallurgy and material science will likely yield new alloys and improved production methodologies, enhancing performance and durability.
Digital Transformation: Adoption of Industry 4.0 technologies—including IoT-enabled quality control and real-time data analytics—will lead to smarter, more agile manufacturing processes.
Sustainable Production Initiatives: Companies are expected to invest more in environmentally friendly production methods, with a focus on energy efficiency and waste reduction.
Expanded Applications: As emerging technologies, such as next-generation aerospace engines and advanced nuclear reactors, advance, the demand for specialized metal tubes will expand, opening new markets and applications.
Enhanced Global Supply Chains: Strategic collaboration and long-term partnerships among global suppliers will be crucial in mitigating raw material shortages and ensuring steady supply channels.
Throughout these evolving market dynamics, TFM remains at the forefront, leveraging its expertise in advanced tube production and its robust quality assurance protocols to support industries worldwide.
Chapter 7
V. Integration of Hot Keywords
To improve visibility and reach on digital platforms, the following 12 trending keywords are seamlessly integrated into the discussion:
High performance metal tubing: A term that encapsulates the overall product line, highlighting the superior qualities of these tubes in demanding applications.
Molybdenum tube supplier: Emphasizing TFM’s established role as a trusted source of molybdenum tubes for critical aerospace and nuclear applications.
Titanium pipe specifications: Outlining the detailed standards and dimensional criteria that ensure the reliability of titanium products in high-stress environments.
Tantalum tube prices: Discussing market factors that influence the cost structures, along with TFM’s competitive pricing strategies.
Niobium tube applications: Detailing the diverse uses of niobium tubes in sectors that require high stability and superconducting properties.
Zirconium tube standards: Highlighting compliance with international benchmarks that govern the performance of zirconium products.
Wrought tungsten tube: Focusing on the unique production technologies used in forming tungsten tubes that withstand extreme temperatures.
Chromium tube manufacturers: Illustrating the role of established manufacturers, including TFM, who provide durable chromium tubes suited for harsh chemical environments.
Nickel tube suppliers: Underlining TFM’s commitment to reliability and quality as a premier supplier of nickel tubes.
Advanced metal tube production: Emphasizing innovative methods such as powder metallurgy and cold drawing that drive the production of these materials.
Cold drawn metal tubing: Showcasing the process that significantly enhances the mechanical properties and surface finishes of critical tube products.
Powder metallurgy tube: Explaining the process that allows for exceptional material uniformity and enhanced performance in high-end applications.
These keywords are seamlessly incorporated to enhance the performance of online platforms and to assist industry professionals and engineers in quickly locating valuable technical and market information.
Chapter 8
VI. TFM’s Role as a Supplier
TFM has developed a reputation for excellence as a supplier of high-performance metal tubes and fittings. With decades of experience and continuous investment in innovative production technologies, TFM consistently delivers products that meet or exceed international standards. Key points include:
Quality Assurance: TFM employs rigorous quality control systems aligned with ASTM, ISO, and other global standards to ensure every tube’s consistency and reliability.
Tailored Solutions: Recognizing the varying needs of industries—from aerospace to petrochemical—TFM offers customizable options, enabling end-users to select the ideal material, dimensions, and processing methods to suit their applications.
Competitive Pricing and Supply Reliability: Through strategic sourcing and advanced manufacturing, TFM is well-positioned to offer competitive pricing without compromising on quality. This reliable supply chain is critical, especially when facing raw material market fluctuations.
Technical Support and Industry Expertise: TFM not only supplies products but also partners with clients to offer technical guidance and post-installation support. Their expert teams work closely with customers to troubleshoot challenges and optimize performance outcomes.
TFM’s commitment to excellence is evident in every facet of production, from raw material selection to final product delivery, making them a preferred partner for those in search of molybdenum tube suppliers, titanium pipe specifications, and other high-performance metal tubing solutions.
Chapter 9
Frequently Asked Questions
What are the key properties of high performance metal tubing?
High performance metal tubing is characterized by its excellent strength, resistance to high temperatures, superior corrosion resistance, and precise dimensional stability. These properties ensure reliability in demanding applications, such as aerospace engines and chemical processing plants.
How does powder metallurgy contribute to tube production?
Powder metallurgy enables the production of tubes with a uniform microstructure and high purity. In this process, metallic powders are compacted and sintered, resulting in products that exhibit enhanced mechanical properties and consistent performance, particularly in refractory metals.
Which international standards govern the manufacturing of these tubes?
Manufacturers adhere to standards such as ASTM and ISO, including ASTM B770 for molybdenum, ASTM B777 for tungsten, and ASTM B763 for tantalum, among others. These standards ensure that tubes meet mechanical, chemical, and dimensional requirements for industrial applications.
What are the main production processes for high performance metal tubes?
The primary production methods include powder metallurgy, cold rolling, hot extrusion, and cold drawing. Each technique contributes uniquely to the final properties of the tube, ensuring optimal performance across various applications.
What industries primarily use titanium and tantalum tubes?
Titanium tubes are widely used in aerospace, marine, and medical applications due to their light weight and excellent strength-to-weight ratio. Tantalum tubes, on the other hand, are favored in the chemical and electronics industries because of their exceptional corrosion resistance and biocompatibility.
How does TFM ensure consistent quality in its tubing products?
TFM employs rigorous quality control and testing protocols to ensure that each tube meets or exceeds international standards. Continuous monitoring throughout the manufacturing process—from powder selection to final inspection—ensures consistent performance and reliability.
What are the typical dimensions and specifications for these tubes?
The dimensions vary depending on the application but generally include precise outer diameters, wall thicknesses, and lengths as specified by standards such as ASTM and ISO. Detailed specifications are available for each material type, ensuring compatibility with specific industrial requirements.
Can these metal tubes withstand extreme conditions?
Yes, high-performance metal tubes such as tungsten, molybdenum, and zirconium tubes are specifically engineered to operate in extreme environments—handling high temperatures, corrosive chemicals, and high pressures without compromising structural integrity.
What factors influence tantalum tube prices?
Market factors such as raw material supply, production costs, and demand fluctuations influence tantalum tube prices. TFM leverages long-term supplier relationships and efficient production techniques to offer competitive pricing despite market volatility.
How are cold drawn metal tubes different from hot extruded tubes?
Cold drawn metal tubes undergo processing at ambient temperatures, which improves surface finish and dimensional tolerance, while hot extruded tubes are formed at elevated temperatures and may require additional finishing. The selection depends on the desired physical properties and application requirements.
What makes chromium and nickel tubes ideal for corrosive environments?
Both chromium and nickel have outstanding corrosion resistance properties. Chromium tubes are often used in high acid environments, whereas nickel tubes are particularly effective in high-temperature and high-pressure applications, making them valuable in chemical processing and marine applications.
Why is TFM a preferred supplier for advanced metal tube production?
TFM is known for its technological innovation, rigorous quality assurance, and tailored customer solutions. They deliver consistent, high-quality products that conform to international standards, making them a trusted partner for companies looking for nickel tube suppliers, wrought tungsten tube offerings, and other high-performance metal tubing solutions.
Chapter 10
Conclusion
High-performance metal tubes are at the core of modern technological advancements, serving critical roles in aerospace, nuclear, petrochemical, medical, electronics, and marine industries. Each material—from Molybdenum to Nickel—offers distinct properties that meet specific engineering challenges. Advanced production methods, including powder metallurgy, cold rolling, hot extrusion, and cold drawing, ensure that these tubes possess the requisite strength, durability, and precision to support demanding applications.
TFM stands out as a leading supplier in this competitive landscape. With its unwavering commitment to quality, innovative production processes, and deep technical expertise, TFM provides tailored solutions that meet the highest international standards. Their products not only comply with stringent ASTM and ISO guidelines but also address market dynamics—ranging from raw material supply and pricing to evolving industry requirements.
Furthermore, by integrating current Google search trends and addressing common industry queries, this article serves as a valuable resource for engineers, procurement professionals, and decision-makers across diverse sectors. Whether you are searching for high performance metal tubing, looking for detailed titanium pipe specifications, or need insights into advanced metal tube production, the information provided herein underscores the technical excellence and market relevance of these critical products.
In an industry where precision and reliability are non-negotiable, high-performance metal tubes and fittings remain indispensable. With continuous advancements in materials science and manufacturing technologies, the future holds significant potential for further innovation and expanded applications. TFM’s role as a dependable supplier ensures that industries worldwide have the necessary tools to drive innovation, enhance safety, and achieve operational excellence in their respective fields.
This detailed exploration not only highlights the outstanding qualities of each metal tube but also provides insights into the market trends, production challenges, and emerging technologies that will shape the future of high-performance metal tubing. With TFM’s proven expertise and robust supply chain, clients can be confident in receiving state-of-the-art materials that support some of the most demanding applications in today’s technological world.