Valves & Pipe Fittings
Box sources are available in a variety of styles. These box sources reduce spitting as a result of heating some materials. Baffling in the sources eliminates line of sight between the bulk material and substrate.
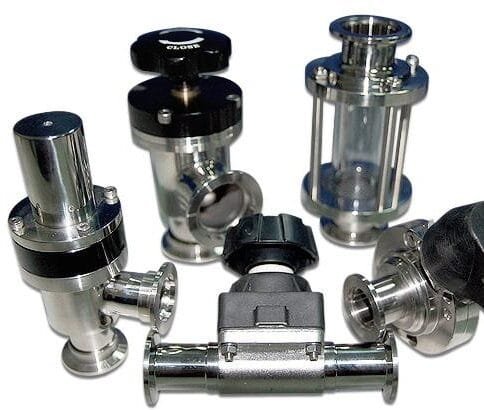
Vacuum Valves
We offer a wide range of valves, including ball, gate, butterfly, angle, and diaphragm valves, primarily designed for vacuum environments. Whether you require precise control, exceptional sealing, or durability under challenging conditions, our vacuum valves deliver unparalleled performance. Explore our selection and find the perfect fit for your specific requirements, supported by our commitment to quality and innovation.
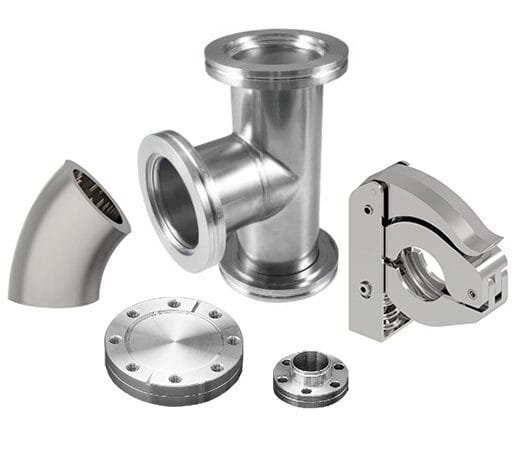
Vacuum Fittings
We provide a comprehensive selection of high-quality pipe fittings designed to meet the rigorous demands of various industries. Our range includes flanges, elbows, tees, reducers, couplings, and more, ensuring secure and efficient connections. Whether you need fittings for high-pressure applications, sanitary environments, or vacuum systems, our products deliver exceptional reliability and performance. Explore our offerings to find the perfect solutions for your piping needs.

Pipes & Tubes
Discover high-quality pipes and tubes designed for various industrial applications. Explore durable, corrosion-resistant options available in multiple materials and sizes to meet your specific needs.
A Comprehensive Guide to Vacuum Components: Valves, Fittings, and Pipes & Tubes
In today’s advanced industrial environments, maintaining precise control over vacuum systems is essential for applications ranging from semiconductor manufacturing to pharmaceutical processing. Whether you are developing a cutting-edge production line or optimizing an existing system, understanding the role of vacuum valves, vacuum fittings, and pipes & tubes is critical. In this comprehensive guide, we explore the technologies behind these components, their applications, key design considerations, and common troubleshooting practices.
Table of Contents
Chapter 1
1. Introduction to Vacuum Systems
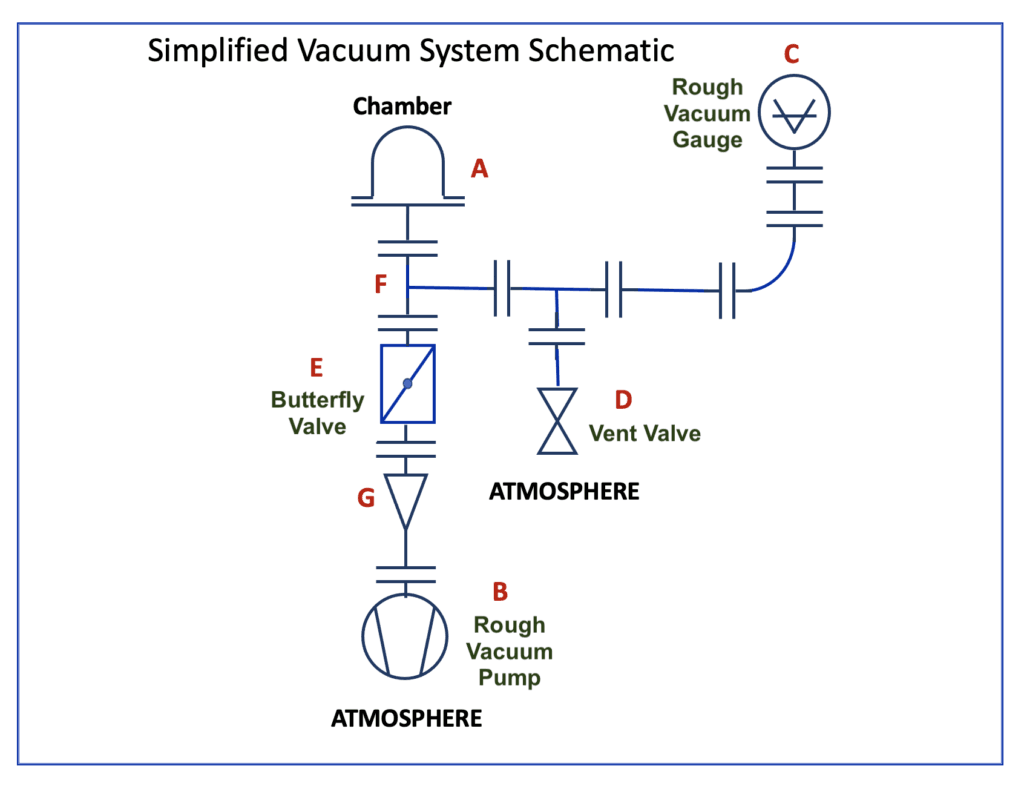
A vacuum system is a sophisticated network designed to remove air and other gases from a designated area, creating a controlled environment. This controlled vacuum environment is essential in numerous industries. Key applications include:
Semiconductor Manufacturing: Ensuring contamination-free environments for circuit fabrication.
Pharmaceutical Production: Maintaining sterile environments for drug production.
Food Processing: Providing controlled conditions to prevent spoilage and contamination.
Scientific Research: Creating conditions necessary for experiments in physics and chemistry.
Within these systems, the proper integration of valves, fittings, and tubes ensures efficient operation and safety. Each component plays a distinct role, from regulating gas flow to providing secure connections and transporting gases under controlled conditions.
Chapter 2
2. The Role and Function of Vacuum Valves
2.1 Overview
Vacuum valves are the heart of any vacuum system. Their primary function is to regulate the flow of gases and maintain the desired vacuum pressure. They control when and how much gas is introduced or evacuated from the system, making them essential for both starting and stopping processes.
2.2 Key Functions
Pressure Regulation: Vacuum valves adjust the vacuum level within the system, ensuring that processes run under the correct pressure conditions.
Flow Control: They precisely manage the flow of gases, preventing sudden pressure surges or drops.
Isolation: Valves allow sections of the vacuum system to be isolated for maintenance or process changes without compromising the entire system.
2.3 Design and Material Considerations
When selecting a vacuum valve, it’s important to consider:
Sealing Performance: High-quality valves provide superior sealing to prevent leaks. These often incorporate advanced materials such as high-grade stainless steel or specialized alloys.
Temperature Resistance: Vacuum valves are used in a variety of environments. In high-temperature settings, specialized designs ensure that the valve maintains performance without degradation of seals.
Precision Control: For industries requiring exact vacuum levels, precision-engineered valves offer fine control over gas flow. This is particularly important in processes where even minor fluctuations in pressure can affect outcomes.
2.4 Applications in Industry
Industries rely on vacuum valves for several reasons:
Semiconductor Fabrication: Precision control is paramount in chip production. Vacuum valves help maintain the contamination-free environment needed for high yields.
Pharmaceuticals: Valves ensure that vacuum systems used in drug manufacturing remain stable, preventing contamination and ensuring consistent product quality.
Research Laboratories: In experiments where pressure must be meticulously controlled, vacuum valves provide the necessary accuracy and reliability.
Chapter 3
3. Connecting the Dots: Vacuum Fittings
3.1 Understanding Vacuum Fittings
Vacuum fittings are the connecting components that join various parts of a vacuum system. They create the necessary links between vacuum valves, pipes, tubes, and other accessories. Without reliable fittings, even the best valves and tubes could fail to perform properly.
3.2 Key Features and Benefits
Material Compatibility: Fittings are typically made from corrosion-resistant materials like stainless steel or aluminum. This compatibility ensures that fittings do not react with the gases or chemicals present in the vacuum system.
Integrity and Sealing: Proper vacuum fittings are designed to maintain system integrity by preventing leaks. Their design ensures that connections remain secure under varying pressures and temperatures.
Ease of Assembly: Many modern vacuum fittings are designed for quick and secure assembly, which minimizes downtime during installation or maintenance.
3.3 Material Selection
The choice of material for vacuum fittings is crucial. Common materials include:
Stainless Steel: Known for its strength, durability, and resistance to corrosion. It is often the material of choice in high-vacuum applications.
Aluminum Alloys: Lighter than stainless steel, aluminum is suitable for applications where weight is a concern but still offers good resistance to corrosion.
Specialized Alloys: In certain high-demand applications, specialized alloys are used to provide enhanced durability, temperature resistance, or chemical compatibility.
3.4 Installation and Maintenance
For optimal performance, vacuum fittings require proper installation and regular maintenance:
Secure Connections: Ensure that fittings are properly tightened to avoid leaks. This is particularly important in high-vacuum environments where even small leaks can have significant impacts.
Regular Inspections: Routine checks can identify wear, corrosion, or damage early, preventing system failures.
Cleaning Procedures: Keeping fittings free of contaminants such as dust or chemical residues can prolong their service life and ensure continued system performance.
3.5 Industrial Applications
In many industrial settings, vacuum fittings are indispensable. For instance, in the semiconductor industry, even the smallest leak can lead to costly contamination issues. Similarly, in pharmaceutical production, maintaining a sterile environment is critical. High-quality vacuum fittings help ensure that these conditions are met consistently.
Chapter 4
4. The Critical Role of Pipes & Tubes in Vacuum Systems
4.1 Overview
Pipes & tubes are the channels that transport gases and maintain the vacuum environment. They connect various components of a vacuum system and ensure the efficient flow of gases. Their design and installation are key to maintaining system pressure and efficiency.
4.2 Design Considerations
When selecting pipes & tubes for a vacuum system, several factors must be taken into account:
Transmission Efficiency: Pipes & tubes are engineered to minimize pressure drop and ensure smooth transmission of gases. Their internal diameter, wall thickness, and material all contribute to their efficiency.
Connection Quality: The joints between pipes, valves, and fittings must be airtight. Special attention must be paid to how these components are connected, ensuring that the entire system remains leak-free.
System Layout: The physical layout of the pipes & tubes is crucial. Avoiding sharp bends, long runs, or sudden changes in direction can help maintain optimal gas flow and minimize losses.
Flexibility and Adaptability: Pipes & tubes can often be customized to meet specific requirements. Whether the application involves high vacuum levels or moderate conditions, there are designs available to suit a wide range of needs.
4.3 Material and Durability
The materials used in pipes & tubes affect both performance and durability:
Stainless Steel Tubing: Offers excellent durability, corrosion resistance, and is ideal for high-vacuum applications.
Aluminum Tubing: Lightweight and easier to install, aluminum is suitable for applications where weight is a factor but does not compromise on performance.
Special Coatings: In some cases, pipes & tubes are coated with materials that further enhance their resistance to corrosion, chemical attack, or high temperatures.
4.4 Installation Best Practices
Proper installation of pipes & tubes is crucial for maintaining system performance:
Avoiding Sharp Bends: Sharp bends can lead to increased resistance and pressure drops. Instead, use gentle curves or flexible tubing solutions.
Securing Connections: Ensure that all joints are properly sealed using appropriate fittings or welding techniques.
Minimizing Length: Where possible, design the system to keep tubing runs as short as possible, reducing the potential for pressure loss.
Maintenance Access: Design layouts that allow easy access for maintenance and inspection, helping to quickly address any issues that may arise.
4.5 Common Challenges and Solutions
Even well-designed systems can face challenges:
Pressure Loss: Over long distances or with poor connections, pressure drops can occur. Addressing these issues through proper design and regular maintenance can minimize their impact.
Leaks: Even minor leaks can lead to system inefficiencies. Routine leak detection and repair protocols are essential for long-term reliability.
Contamination: In certain environments, pipes & tubes can become contaminated with particulates or chemical residues. Implementing regular cleaning schedules helps prevent performance degradation.
Chapter 5
Frequently Asked Questions (FAQs) Addressed in Detail
Understanding the intricacies of vacuum systems involves answering common questions about each component. Below, we explore some FAQs in depth to provide clarity for system designers, engineers, and end-users alike.
What is the Difference Between a Vacuum Valve and Vacuum Fittings?
Vacuum Valves
Vacuum valves serve as the control points within a vacuum system. They regulate gas flow, maintain pressure balance, and isolate different sections of the system during maintenance or operational adjustments. Their precise mechanical design allows for rapid response times and fine-tuned control, essential in high-demand environments.
Vacuum Fittings
On the other hand, vacuum fittings are the connectors that integrate various components. They ensure that vacuum valves, pipes, and other accessories are securely joined, maintaining an airtight network. While valves actively control flow, fittings passively maintain system integrity by providing robust, leak-free connections.
How Do I Choose the Right Vacuum Valve?
Choosing the right vacuum valve involves several key considerations:
Pressure Range: Determine whether your application requires low, medium, or high vacuum conditions. The valve must operate effectively within this range.
Sealing Performance: Look for valves that provide excellent sealing capabilities to prevent leaks. Quality materials and precision machining are crucial.
Temperature Resistance: Ensure the valve is rated for the operating temperatures in your system. High-temperature environments may require specialized valve designs.
Compatibility: Confirm that the valve’s design and materials are compatible with other system components, such as fittings and tubes.
Precision Control: In applications requiring fine adjustments, select valves known for precision control, ensuring minimal fluctuations in gas flow.
What Role Do Pipes & Tubes Play in a Vacuum System?
Pipes & tubes are critical as they:
Transport Gases: They provide the channels through which gases flow, maintaining the overall vacuum environment.
Ensure Pressure Balance: Their design minimizes pressure drops, ensuring that the vacuum system operates efficiently.
Connect Components: They serve as the physical links between valves, fittings, and other system parts, ensuring a cohesive structure.
Adapt to Specific Needs: Customizable in length, diameter, and material, they can be tailored to meet specific operational requirements.
How Can I Ensure the Sealing Performance of My Vacuum System?
Ensuring robust sealing performance involves:
Using High-Quality Materials: Select components made from high-grade stainless steel or other corrosion-resistant materials.
Precision Manufacturing: Opt for components that have been manufactured with tight tolerances to guarantee a secure seal.
Regular Maintenance: Routine inspections and leak tests can identify and address issues before they become significant.
Proper Installation: Ensure that all fittings and joints are installed correctly, with adequate torque and alignment.
Which Materials Are Best for Vacuum Fittings?
Common materials include:
Stainless Steel: Preferred for its strength, durability, and resistance to corrosion.
Aluminum Alloys: Chosen for applications requiring a lighter weight solution without sacrificing performance.
Specialized Alloys: Used in environments with extreme temperatures or chemical exposures, these alloys provide enhanced durability and compatibility.
What Are the Best Practices for Maintaining a Vacuum System?
Maintenance is key to longevity and performance:
Regular Inspections: Check for leaks, wear, or corrosion at scheduled intervals.
Cleaning Protocols: Clean components such as pipes and fittings to remove dust, chemical residues, or other contaminants.
Component Replacement: Replace seals, gaskets, and other wear parts as recommended by manufacturers.
Documentation: Keep detailed records of maintenance activities to track component performance and anticipate future replacements.
What is the Working Principle of a Vacuum Valve?
The operating principle of a vacuum valve centers around its ability to control gas flow. The valve uses a mechanical mechanism—often a piston, ball, or diaphragm—to open or close a pathway for gases. This action modulates the vacuum level by either allowing air to be evacuated or isolating parts of the system. Precision-engineered components ensure that the valve can quickly and reliably adjust to the system’s requirements.
How Do I Detect Leaks in a Vacuum System?
Leak detection is critical in maintaining performance:
Gas Leak Detectors: These instruments can identify even minor leaks.
Pressure Monitoring: Sudden drops or fluctuations in system pressure may indicate a leak.
Visual Inspections: Regular checks of seals and joints can reveal physical signs of wear or damage.
Ultrasonic Detectors: These devices pick up the sound of escaping gas, providing an additional method for leak detection.
What Are the Key Considerations When Installing Pipes & Tubes?
Installation is as important as component quality:
Alignment and Routing: Ensure pipes are aligned correctly and avoid unnecessary bends that can cause pressure loss.
Secure Connections: Use appropriate fittings to create airtight seals at joints.
Length Optimization: Design the system to keep tubing runs as short as possible, reducing potential for pressure drop.
Accessibility: Plan the layout to allow for easy access during maintenance and inspections.
What Are Common Issues in Vacuum Systems?
Common issues include:
Sealing Failures: Resulting in gas leaks and pressure instability.
Component Wear: Over time, valves, fittings, and tubing can deteriorate due to continuous use, exposure to chemicals, or high temperatures.
Pressure Instability: Caused by fluctuations in flow or improper integration of components.
Contamination: Dust or chemical residues can compromise the vacuum environment, particularly in sensitive applications.
Can Vacuum Valves Be Used in High-Temperature Environments?
Yes, but with careful selection:
Specialized High-Temperature Models: Designed to operate under elevated temperatures without compromising seal integrity.
Material Considerations: Components must be made from materials that maintain performance at high temperatures.
Application Specifics: Ensure that both the valve and the surrounding system components are rated for the expected thermal load.
How Can the Lifespan of Vacuum Fittings Be Extended?
Extending the service life of vacuum fittings involves:
Preventive Maintenance: Regular cleaning and inspection can prevent premature wear.
Proper Handling: Ensure fittings are installed and used in accordance with manufacturer guidelines.
Environment Control: Minimizing exposure to corrosive substances or extreme conditions helps preserve the integrity of the fittings.
Timely Replacement: Replace components as soon as signs of wear or damage are detected to avoid system-wide issues.
Chapter 6
6. Integration of Vacuum Components in Industrial Applications
6.1 Creating a Cohesive Vacuum System

The effectiveness of a vacuum system hinges on the seamless integration of its components. Each element—whether a vacuum valve, fitting, or tube—must be carefully selected and installed to achieve optimal performance. Here are some key integration strategies:
System Design: Begin with a detailed design that outlines every component’s role. Use simulation tools to predict system behavior under various conditions.
Component Compatibility: Ensure that every component is compatible in terms of pressure ratings, material properties, and operating temperatures.
Modular Construction: Consider modular systems that allow for easy replacement or upgrading of individual parts without a complete system overhaul.
Redundancy and Safety: In critical applications, incorporate redundant components or safety valves that can take over in case of a failure.
6.2 Real-World Examples
Semiconductor Manufacturing:
In a semiconductor fabrication plant, even the tiniest leak can ruin an entire batch of chips. Vacuum valves and fittings with high sealing performance and precise control are used to maintain an ultra-clean, stable environment. Pipes & tubes designed for minimal pressure drop ensure that the vacuum remains constant throughout the system, protecting delicate processes.
Pharmaceutical Production:
Pharmaceutical production often requires sterile environments. Vacuum systems in these facilities use valves and fittings made from corrosion-resistant materials, ensuring that no contaminants enter the system. The ease of maintenance and robust design of pipes & tubes contributes to the overall reliability of the process, which is critical when dealing with sensitive drug formulations.
Scientific Research Laboratories:
Research laboratories often require customizable vacuum systems for experiments in physics, chemistry, and material science. The flexibility of pipes & tubes and the precision of vacuum valves allow scientists to create environments with highly specific pressure conditions. Modular fittings enable quick reconfiguration of the system to suit evolving experimental needs.
Chapter 7
7. Advanced Topics in Vacuum System Optimization
7.1 Innovations in Vacuum Valve Technology
Recent advancements in vacuum valve technology include:
Smart Valves: Integration of sensors and digital controls allows for real-time monitoring and automatic adjustments. These smart valves can optimize system performance and reduce downtime.
Improved Materials: Development of new alloys and composite materials has led to valves that offer higher temperature resistance and longer operational life.
Precision Engineering: Advances in manufacturing techniques have improved the tolerances and precision of valves, enabling finer control over gas flow and pressure regulation.
7.2 Enhancing Fitting Reliability
Efforts to improve the reliability of vacuum fittings include:
Enhanced Sealing Technologies: Innovations in gasket materials and sealing methods have resulted in fittings that maintain integrity even under extreme conditions.
Integrated Leak Detection: Some fittings now come with built-in leak detection features, allowing operators to quickly identify and address potential issues.
Standardization: Adoption of industry standards for vacuum fittings has improved interoperability between components from different manufacturers, simplifying system design and maintenance.
7.3 Optimizing Pipe & Tube Configurations
Optimizing the design of pipes & tubes is crucial for minimizing pressure drops and ensuring efficient gas transport:
Flow Dynamics Analysis: Advanced computational fluid dynamics (CFD) simulations help engineers design piping layouts that optimize flow and minimize turbulence.
Material Innovations: Research into new materials and coatings continues to improve the durability and performance of pipes & tubes, especially in corrosive or high-temperature environments.
Custom Solutions: Tailoring pipe diameters, wall thickness, and surface finishes to specific applications can result in significant performance improvements, particularly in systems requiring high precision.
Chapter 8
8. Maintenance, Troubleshooting, and Longevity
8.1 Establishing a Maintenance Protocol
A proactive maintenance program is essential for any vacuum system:
Scheduled Inspections: Establish a regular inspection schedule to identify potential issues with valves, fittings, and tubing before they escalate.
Leak Testing: Implement routine leak detection tests using gas leak detectors, ultrasonic sensors, or pressure monitoring systems.
Component Replacement: Keep spare parts on hand and replace seals, gaskets, and other wear items according to manufacturer recommendations.
Documentation: Maintain detailed logs of all maintenance activities, inspections, and component replacements. This documentation helps track system performance and predict future maintenance needs.
8.2 Troubleshooting Common Issues
Even the best systems can encounter problems. Here are some common issues and troubleshooting tips:
Pressure Instability:
Cause: Leaks, improper valve operation, or inefficient pipe design.
Solution: Perform leak detection tests, check valve functionality, and review the layout of the piping system for potential bottlenecks.Component Wear:
Cause: Prolonged use in harsh environments can lead to wear on seals and fittings.
Solution: Regular maintenance, timely replacement of worn components, and use of high-quality materials can mitigate wear-related issues.Temperature-Related Issues:
Cause: Components not rated for high temperatures may fail in elevated conditions.
Solution: Ensure that all valves and fittings are rated for the operating temperature. Consider upgrading to specialized high-temperature models if necessary.
8.3 Extending the Lifespan of Your Vacuum Components
Long-term reliability is achieved by:
Implementing Preventive Maintenance: Regular cleaning, inspection, and timely replacement of components prevent premature failure.
Optimizing System Design: A well-integrated system with minimal stress on individual components results in lower wear and longer service life.
Investing in Quality: Using high-quality vacuum valves, fittings, and pipes & tubes may have a higher upfront cost but pays dividends in reduced downtime and maintenance expenses over time.
Chapter 9
9. Environmental and Safety Considerations
9.1 Safety Standards in Vacuum Systems
Adherence to safety standards is non-negotiable in any industrial application:
Regulatory Compliance: Ensure that all components meet local and international safety standards. This includes certifications for pressure vessels, leak testing, and material safety.
Operator Training: Regular training for operators on proper handling, maintenance, and emergency procedures is essential to ensure safe operations.
System Monitoring: Install sensors and automated controls that monitor vacuum levels, temperature, and potential leakages. This real-time data helps in proactive safety management.
9.2 Environmental Impacts
Modern vacuum systems are designed with environmental sustainability in mind:
Energy Efficiency: Optimizing the flow dynamics and sealing performance of vacuum components reduces energy consumption. Smart valves and efficient pipe designs contribute to overall energy savings.
Reduced Emissions: In applications where vacuum systems interface with chemical processes, proper sealing and maintenance prevent the unintended release of hazardous gases.
Recyclable Materials: Many high-quality components are made from materials that can be recycled or reclaimed, reducing the environmental footprint of industrial operations.
Chapter 10
10. Future Trends in Vacuum Technology
10.1 The Rise of Automation and IoT
The integration of the Internet of Things (IoT) into vacuum systems is transforming the industry:
Smart Monitoring: Sensors embedded in valves, fittings, and pipes continuously monitor system performance and report data to centralized control systems.
Predictive Maintenance: Machine learning algorithms analyze performance data to predict when maintenance is required, reducing unexpected downtime.
Remote Control: Advanced systems allow operators to adjust vacuum parameters remotely, improving responsiveness and reducing the need for manual intervention.
10.2 Advances in Materials Science
Innovations in materials are driving improvements in vacuum components:
Nanomaterials: Research into nano-engineered surfaces could lead to even better sealing properties and reduced friction in valves.
Composite Materials: Combining the strengths of multiple materials, composite fittings and pipes offer improved durability, temperature resistance, and weight reduction.
Smart Coatings: Coatings that can respond to environmental changes may soon be used to enhance the performance and lifespan of vacuum components.
10.3 Integration with Digital Manufacturing
Digital manufacturing techniques, including 3D printing and computer-aided design (CAD), are streamlining the production of vacuum components:
Customization: Components can be tailored to precise specifications, ensuring optimal performance for unique applications.
Rapid Prototyping: Digital techniques enable faster development cycles, allowing companies to quickly iterate and improve designs.
Quality Control: Advanced monitoring during manufacturing helps ensure that every component meets strict quality standards.
Chapter 10
11. Case Studies and Real-World Implementations
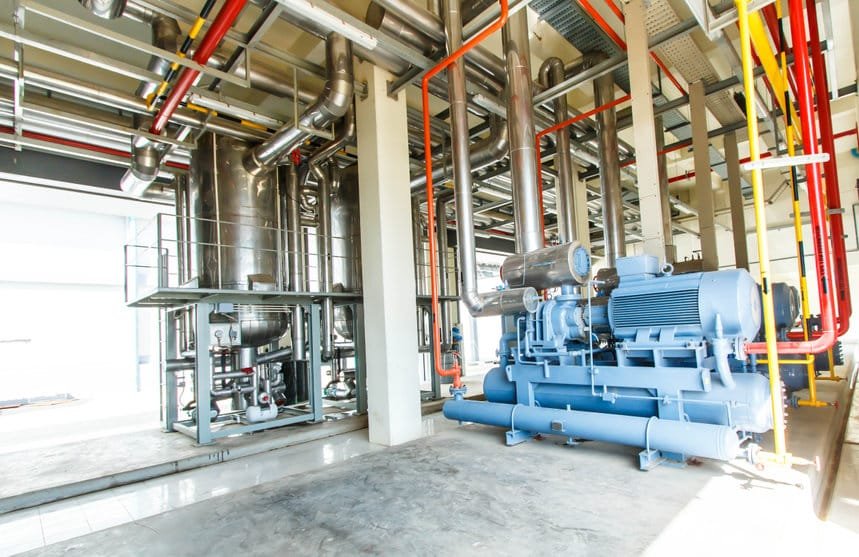
11.1 Case Study: Semiconductor Manufacturing
A leading semiconductor manufacturer recently overhauled its vacuum system to improve production yields. By integrating precision vacuum valves, high-integrity fittings, and optimized pipes & tubes, the company achieved:
Reduced Contamination: Enhanced sealing minimized the risk of particulate ingress.
Improved Pressure Stability: Optimized piping reduced pressure drops, ensuring consistent vacuum conditions.
Lower Maintenance Costs: A modular design allowed for quicker repairs and scheduled maintenance, resulting in fewer production stoppages.
11.2 Case Study: Pharmaceutical Production
In the pharmaceutical sector, a production facility upgraded its vacuum system to comply with stricter environmental and safety regulations. The key improvements included:
High-Temperature Valves: Specially designed valves that maintained performance during sterilization cycles.
Corrosion-Resistant Fittings: The use of stainless steel and specialized alloys in fittings prevented chemical degradation.
Efficient Gas Transport: Redesigned pipes & tubes improved flow efficiency, reducing energy consumption and ensuring a sterile environment throughout the process.
11.3 Lessons Learned
From these case studies, several lessons emerge:
Integration is Key: The performance of the overall system depends on the harmonious interaction between valves, fittings, and pipes.
Customization Matters: Tailoring component specifications to meet the unique demands of each application results in better performance and longer lifespans.
Proactive Maintenance: Regular inspections and preventive measures are essential to avoid downtime and costly repairs.
Chapter 10
12. Conclusion
The effective design and maintenance of vacuum systems hinge on a deep understanding of their critical components: vacuum valves, vacuum fittings, and pipes & tubes. Each component has its unique role—from regulating gas flow to ensuring airtight connections and efficient transport of gases. This comprehensive guide has explored the principles, materials, design considerations, and maintenance protocols that underpin the successful operation of vacuum systems in a variety of industrial applications.
By addressing common FAQs, discussing advanced technologies, and examining real-world case studies, this article provides a valuable resource for engineers, system designers, and industrial professionals. The integration of high-quality, precision-engineered vacuum components not only enhances operational performance but also contributes to safety, energy efficiency, and environmental sustainability.
For companies looking to optimize their vacuum systems, investing in the right combination of valves, fittings, and pipes & tubes is essential. The advancements in material science, automation, and digital manufacturing are paving the way for even more reliable and efficient vacuum systems in the future. As industries continue to evolve, staying informed about these developments will be key to maintaining competitive advantage and ensuring the highest levels of performance and safety.
Explore our range of products and solutions to discover how you can integrate advanced vacuum components into your systems. Whether you are upgrading an existing setup or building a new system from scratch, our expertise and quality products are designed to meet your stringent requirements and deliver superior results.