Introduction
Crucible heaters are essential components in high-temperature material processing across a wide range of industries, including metallurgy, semiconductor fabrication, ceramics, glassmaking, and advanced research. Designed to uniformly heat crucibles containing various substances—metals, oxides, salts, or composites—these heaters provide precise thermal control critical for applications such as melting, evaporation, chemical vapor deposition (CVD), crystal growth, and thermal treatment processes.
This article provides a detailed overview of crucible heaters, their working principles, classifications, design considerations, and typical use cases. It also explores their role in thin film deposition systems, vacuum environments, and how they integrate into modern research and manufacturing setups.
1. What Is a Crucible Heater?
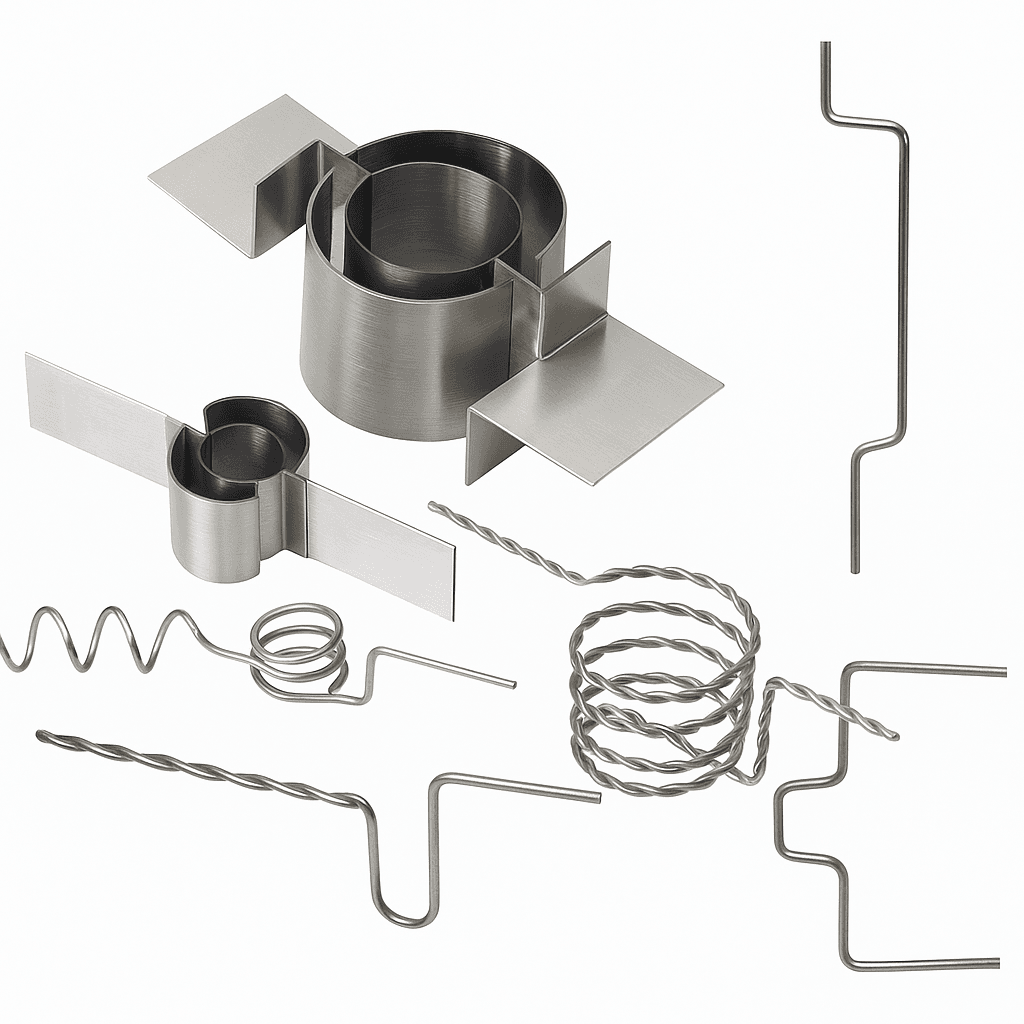
A crucible heater is a thermal system or device designed to apply heat to a crucible, which is a container that holds substances at high temperatures. Crucible heaters are optimized to deliver consistent and controllable thermal energy to ensure that the material inside the crucible reaches and maintains the desired temperature for melting, vaporization, or chemical transformation.
The materials used in crucible heaters are typically high-temperature metals or ceramics such as tungsten (W), molybdenum (Mo), tantalum (Ta), graphite, alumina (Al₂O₃), or silicon carbide (SiC). The heating element may surround the crucible or be embedded directly beneath or around it depending on the specific heating mechanism.
2. Key Functions and Advantages
Crucible heaters offer several distinct advantages:
Uniform Heating: Prevents hotspots, ensuring homogenous material processing.
High Temperature Capability: Can operate at 1000°C to 3000°C depending on material and design.
Controlled Atmosphere Compatibility: Supports operation in vacuum, inert gas, or reducing environments.
Customizable Design: Configurable to suit the size, material, and geometry of the crucible.
Precise Temperature Control: Integrates with thermocouples and PID controllers for accurate feedback.
These features make crucible heaters indispensable for processes such as crystal growth (e.g., Czochralski method), physical vapor deposition (PVD), sintering, and high-purity material preparation.
3. Classification of Crucible Heaters
Crucible heaters can be classified based on several criteria:
a) By Heating Method
Heating Method | Description |
---|---|
Resistive Heating | Uses electric current through resistive elements (e.g., tungsten coil, graphite tube). Common in vacuum and high-purity processes. |
Induction Heating | Uses electromagnetic fields to induce eddy currents in conductive crucibles. Rapid and clean heating. |
Radiant Heating | Infrared heaters or filaments radiate heat to the crucible. Suitable for uniform external heating. |
Gas Heating | Uses combustion of gases around the crucible (less common in modern cleanrooms). |
b) By Crucible Integration
Type | Description |
---|---|
Embedded Heater | Heating element integrated into the crucible walls (e.g., MoSi₂ elements in ceramics). |
Surround Heater | External heating coils or jackets surrounding the crucible. |
Base Heater | Heating element positioned below the crucible (hot plate or pedestal style). |
c) By Application Environment
- Vacuum Crucible Heater: Designed for high vacuum systems, such as PVD or thermal evaporation.
- Atmosphere-Controlled Heater: Used in argon, nitrogen, hydrogen, or reactive gases.
- Laboratory Bench-Top Heater: Compact models used in R&D or analytical labs.
4. Common Heating Element Materials
The choice of heating element depends on the required temperature, environment, and material compatibility:
Material | Max Temp (°C) | Atmosphere Compatibility |
---|---|---|
Tungsten (W) | ~3000 | Vacuum, inert gas |
Molybdenum (Mo) | ~2600 | Vacuum, inert gas |
Tantalum (Ta) | ~2400 | Reducing atmospheres |
Graphite | ~3000 | Vacuum, inert gas (oxidizes in air) |
Kanthal (FeCrAl) | ~1400 | Air, oxidizing environments |
SiC / MoSi₂ | ~1600–1800 | Air, inert, reducing |
5. Typical Crucible Heater Configurations
a) Cylindrical or Basket Type
Used for vertical evaporation or sublimation processes. The crucible sits in a basket-shaped resistive coil made of tungsten or molybdenum.
b) Box or Chamber Type
Flat or box heaters for large crucibles, commonly used in ceramic sintering or powder metallurgy.
c) Conical or Tapered Design
For directional crystal pulling or zone refining, ensuring localized heat focus.
d) Multi-Zone Heaters
Segmented into multiple heating zones with independent controls for gradient control or precision temperature profiling.
6. Applications of Crucible Heaters
6.1 Thin Film Deposition
Crucible heaters are crucial in thermal evaporation systems used for:
- Semiconductor thin films
- Optical coatings (e.g., Al, Au, Ag deposition)
- Organic electronics and OLEDs
6.2 Crystal Growth
Used in systems such as:
- Czochralski Method for silicon or sapphire
- Bridgman and Zone Melting techniques for compound semiconductors
6.3 Material Purification
Crucible heaters enable sublimation and distillation of high-purity materials such as:
- Rare earth oxides
- High-purity metals (e.g., Nb, Ta, Hf)
- Alloys for research
6.4 Ceramic and Glass Processing
High-temperature crucible furnaces for melting or annealing:
- Alumina, zirconia, borosilicate glasses
- Ceramic frits and glazing powders
6.5 Analytical and Research Labs
- Thermogravimetric analysis (TGA)
- Differential thermal analysis (DTA)
- Melting point studies and phase transition analysis
7. Design Considerations
When choosing or designing a crucible heater, the following factors are important:
a) Temperature Range and Uniformity
Ensure the heater meets the required peak temperature with ±1°C stability.
b) Atmosphere Compatibility
Heater and crucible material must match the process gas or vacuum level.
c) Thermal Efficiency
Use of radiation shields and insulation reduces heat loss and power consumption.
d) Material Compatibility
Avoid reactions between the heater, crucible, and material being processed (e.g., avoid graphite with oxidizing materials).
e) Size and Load Capacity
Heater size must support the crucible mass, material volume, and thermal expansion tolerance.
f) Control and Monitoring
- Integrated thermocouples (Type C, K, or B)
- PID or PLC control systems
- Safety features: over-temperature shutoff, current limiters
8. Integration With Vacuum Systems
Crucible heaters are often integrated into:
- Thermal Evaporation Systems
For metals like Al, Cr, Au, or Ti. - MBE (Molecular Beam Epitaxy)
Using crucibles and effusion cells for ultra-thin epitaxial layers. - High Vacuum or UHV Chambers
With shielding, feedthroughs, and load-lock compatibility.
9. Maintenance and Safety
a) Maintenance Tips
- Regular inspection of connections and thermal elements.
- Replace worn-out refractory insulation.
- Monitor resistance and insulation degradation over time.
b) Safety Guidelines
- Use proper grounding and insulation.
- Never expose graphite heaters to air at high temperatures.
- Avoid thermal shock to ceramic crucibles (preheat gradually).
10. Future Trends in Crucible Heating
- Additive Manufacturing: Precise melting of alloys and powders in metal 3D printing.
- Clean Energy: High-purity crystal growth for solar and battery industries.
- Miniaturization: Compact heaters for MEMS, microreactors, and lab-on-chip systems.
- AI Integration: Smart PID controllers and thermal profiling based on machine learning.
Conclusion
Crucible heaters are indispensable tools in high-temperature material science and industrial processing. Whether used in thermal evaporation, alloy melting, or crystal growth, they ensure consistent and controllable heating within a wide range of atmospheres and configurations. Understanding the principles behind their operation, as well as the materials and systems they support, is key for engineers, researchers, and manufacturers seeking reliable thermal solutions.
With advances in material engineering and control technologies, crucible heaters continue to evolve, supporting emerging sectors such as quantum materials, optoelectronics, and nanotechnology.
You May Also Want to Know
- What is the typical lifespan of a crucible heater?
It varies by material and usage but ranges from hundreds to thousands of hours under proper conditions. - Can crucible heaters be repaired or refurbished?
Yes, resistive elements and insulation can often be replaced or repaired. - What is the maximum size of a crucible heater?
Industrial models can heat crucibles several liters in volume; custom systems can go larger. - What power supply is needed for crucible heaters?
Typically ranges from 12V to 240V, with power ratings between 500W to 20kW depending on application. - Can I use a crucible heater in air?
Some can (e.g., SiC or Kanthal), but many (e.g., graphite, tungsten) must be used in vacuum or inert gas. - How do I measure temperature inside the crucible?
Thermocouples placed close to or embedded in the crucible wall are standard. - What is the most efficient crucible heater material?
Graphite offers excellent thermal conductivity but must be protected from oxidation. - Can I automate crucible heater temperature control?
Yes, using PID controllers or PLCs with thermocouple feedback. - Do crucible heaters come in modular designs?
Yes, many are modular for easy replacement, retrofitting, and scalability. - Are custom crucible heaters available?
Absolutely. Manufacturers offer custom sizes, shapes, and materials based on process needs.