Elastomer O-Rings are ubiquitous sealing components that have become indispensable in various industries due to their simplicity, reliability, and versatility. These circular elastomeric seals are designed to prevent the passage of liquids or gases between two or more surfaces. In this article, we will delve deep into the applications of Elastomer O-Rings, exploring their composition, properties, and use across diverse sectors.
What Are Elastomer O-Rings?
Elastomer O-Rings are mechanical gaskets in the shape of a loop with a round cross-section, typically made from elastomeric materials such as rubber, silicone, or other polymers. These seals fit into grooves or between two surfaces, compressing to create a tight seal.
Common Elastomer Materials
- Nitrile (NBR): Known for excellent resistance to oils and fuels.
- Silicone (VMQ): Exceptional for high-temperature applications and flexibility.
- Fluoroelastomers (FKM/Viton): Ideal for chemical resistance and high-performance sealing.
- Ethylene Propylene Diene Monomer (EPDM): Outstanding for weather and water resistance.
- Polyurethane (PU): Renowned for abrasion resistance and durability.
Applications of Elastomer O-Rings
Elastomer O-Rings are used in countless applications, spanning industries like automotive, aerospace, medical devices, food processing, and more. Below, we explore their specific uses in detail.
1. Automotive Industry
O-Rings are vital in automotive systems, ensuring fluid integrity and performance. Their uses include:
- Engine Seals: Prevent oil leaks in engines, ensuring lubrication and performance.
- Fuel Systems: Maintain pressure in fuel injectors and fuel pumps.
- Air Conditioning Systems: Ensure proper sealing in refrigerant systems, preventing leaks and maintaining efficiency.
- Brake Systems: Seal hydraulic fluids in braking systems, ensuring safety and reliability.
2. Aerospace and Defense
In aerospace, where reliability is paramount, O-Rings play a critical role:
- Fuel and Hydraulic Systems: Withstand extreme temperatures and pressures, ensuring the integrity of systems.
- Cabin Pressurization: Seal air systems to maintain cabin pressure at high altitudes.
- Space Exploration: Used in spacecraft to handle extreme vacuum and temperature conditions.
3. Industrial Applications
Industries depend on O-Rings for maintaining machinery and equipment efficiency:
- Hydraulic and Pneumatic Systems: Provide tight seals in pumps, cylinders, and valves.
- Rotary Equipment: Seal shafts and bearings in motors and compressors.
- General Maintenance: Prevent leakage and contamination in pipes and industrial systems.
4. Medical Devices
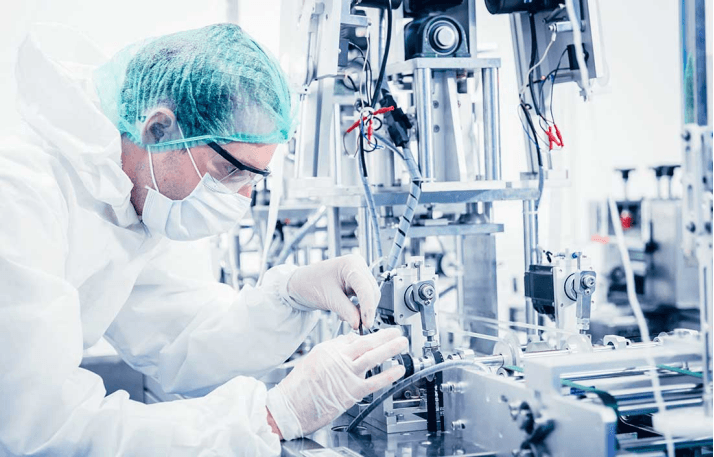
Elastomer O-Rings are used in medical devices where sterilization and biocompatibility are essential:
- Syringes and Pumps: Ensure precision in drug delivery systems.
- Diagnostic Equipment: Maintain airtight seals in imaging and laboratory devices.
- Prosthetics: Provide durable and flexible sealing components.
5. Food and Beverage Industry
In this sector, O-Rings must meet strict hygiene standards:
- Processing Equipment: Used in mixers, blenders, and separators to prevent contamination.
- Packaging Machines: Ensure seals in vacuum packaging and liquid filling.
- Pipelines: Maintain fluid integrity in food-grade systems.
6. Oil and Gas Sector
In challenging environments, O-Rings withstand harsh chemicals and extreme conditions:
- Drilling Operations: Seal wellheads and downhole equipment.
- Refineries: Maintain seal integrity in high-temperature and corrosive environments.
- Pipelines: Prevent leaks in high-pressure systems.
7. Electronics and Semiconductors
O-Rings are vital in sensitive and precise environments:
- Vacuum Chambers: Seal systems to maintain low-pressure environments for semiconductor manufacturing.
- Electronic Enclosures: Protect delicate electronics from dust and moisture.
8. Renewable Energy
Elastomer O-Rings are crucial in emerging renewable energy technologies:
- Wind Turbines: Seal hydraulic systems and gearboxes.
- Solar Panels: Prevent moisture ingress in photovoltaic systems.
- Hydroelectric Systems: Provide sealing in turbines and water channels.
Why Are Elastomer O-Rings Widely Used?
The versatility of elastomer O-Rings comes from their unique combination of properties:
- Versatility: Suitable for sealing a wide range of fluids and gases.
- Cost-Effectiveness: Economical to produce and replace.
- Ease of Use: Simple to install and maintain.
- Adaptability: Available in various sizes, materials, and durometers to suit diverse applications.
- Durability: Withstand extreme temperatures, pressures, and chemical exposures.
Factors to Consider When Choosing Elastomer O-Rings
Choosing the right O-Ring involves evaluating several factors:
- Material Compatibility: Ensure the elastomer is resistant to the media it will contact.
- Temperature Range: Select materials that can withstand the operating temperatures.
- Pressure Ratings: Consider the pressure the O-Ring will encounter.
- Dynamic vs. Static Seals: Use different designs for moving and stationary applications.
- Regulatory Compliance: Ensure adherence to industry standards, especially in medical or food applications.
Future of Elastomer O-Rings
As industries evolve, so do the demands on elastomer O-Rings. Innovations focus on:
- Improved Materials: Developing elastomers with enhanced properties for extreme conditions.
- Eco-Friendly Solutions: Creating recyclable and biodegradable options.
- Custom Designs: Tailoring O-Rings to specific applications using advanced manufacturing techniques like 3D printing.
Conclusion
Elastomer O-Rings are an essential component in modern technology, offering reliable sealing solutions across various industries. From automotive engines to medical devices and renewable energy systems, their applications are vast and varied. By understanding their properties and selecting the right material and design, industries can ensure optimal performance and longevity in their systems. Whether in harsh environments or precise medical devices, elastomer O-Rings continue to play a critical role in maintaining efficiency and reliability.