Evaporation materials are an essential component in the world of modern manufacturing, particularly when it comes to creating thin films for advanced technology applications. The process of evaporation deposition, where materials are vaporized and then condensed onto substrates, forms the backbone of industries such as electronics, optics, and energy production. This article delves into the characteristics of evaporation materials, their selection criteria, key applications, and the intricate processes that make this technique an indispensable part of modern innovation.
1. Introduction: What Are Evaporation Materials?
At its core, evaporation materials are substances that, when subjected to heat, transition from a solid or liquid state into a gas. In the context of thin-film deposition, these materials are vaporized in a controlled environment, such as a vacuum chamber, and deposited onto a surface, forming a thin, solid layer. These films can serve numerous purposes, ranging from providing conductive paths to enhancing optical properties or even creating protective coatings for various components.
The evaporation process is a highly specialized technique used in industries where precise control of material properties is essential. The quality and thickness of the deposited film are determined by factors like the material’s vapor pressure, temperature, and the duration of the evaporation process.
Types of Evaporation Materials
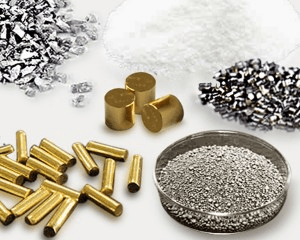
Evaporation materials vary significantly in terms of composition and the properties they offer. Broadly, these materials can be categorized into the following types:
- Metals: Known for their electrical conductivity and thermal properties, metals like gold, aluminum, silver, copper, and titanium are widely used in evaporation deposition processes. Each of these metals provides distinct benefits such as excellent adhesion or superior reflectivity, making them ideal for various applications in electronics, optics, and more.
- Semiconductors: Materials like silicon, gallium, and arsenide are used in the creation of thin films for semiconductors. These materials are critical in manufacturing transistors, diodes, and other electronic components where precise material control is vital.
- Oxides and Non-Metals: Some non-metallic materials like silicon dioxide (SiO₂), magnesium fluoride (MgF₂), and titanium dioxide (TiO₂) are often chosen for optical coatings due to their transparency and refractive properties.
- Alloys: When specific properties from a combination of metals are required, alloys are employed. For instance, chromium-aluminum alloys are used in applications where durability and resistance to oxidation are necessary.
2. The Science Behind Evaporation Deposition
How Does Evaporation Deposition Work?
Evaporation deposition is a fascinating process that involves several key stages. Here’s an in-depth look at how the process unfolds:
- Material Heating: The evaporation material is placed in a heating chamber where it is subjected to high temperatures. This is typically done inside a vacuum chamber to prevent unwanted chemical reactions with oxygen or other air components.
- Vaporization: Once the material reaches a sufficiently high temperature, it transitions from a solid or liquid state into a vapor. The energy supplied to the material overcomes the intermolecular forces holding its atoms or molecules in place, allowing them to enter the gas phase.
- Transport to the Substrate: The vaporized material then travels through the vacuum environment to a cooler substrate, where it will condense and form a thin film.
- Condensation and Film Formation: Upon reaching the cooler surface, the vaporized material condenses and forms a layer. This film can vary in thickness, depending on how long the material is allowed to evaporate and the conditions within the vacuum chamber.
Key Evaporation Techniques
Several methods of evaporation deposition are used depending on the material being processed and the desired outcome:
- Thermal Evaporation: In thermal evaporation, a resistive heating method is employed. The material is heated by passing an electric current through it, causing it to melt and vaporize. This technique is most suitable for materials with lower melting points.
- Electron Beam Evaporation: This technique uses a focused electron beam to heat the material. The electron beam provides highly concentrated heat, which allows for the evaporation of materials that have high melting points, such as tungsten or gold.
- Flash Evaporation: Flash evaporation is an accelerated method that rapidly heats the material to a temperature high enough for it to vaporize almost instantaneously. This is particularly useful for creating high-quality thin films quickly, such as those needed in the production of displays.
3. Factors That Determine the Choice of Evaporation Materials
Choosing the right material for evaporation deposition depends on several factors, including the required properties of the final film and the conditions under which the deposition will take place. Below are some of the most critical factors to consider when selecting evaporation materials:
3.1. Physical and Chemical Properties
- Melting Point: Evaporation materials must have a high enough melting point to withstand the heating process without decomposing or deteriorating. Materials with higher melting points like titanium and platinum are often chosen for high-temperature applications, whereas materials like aluminum or gold are more common for standard applications.
- Vapor Pressure: The vapor pressure of a material at a given temperature determines how easily it will vaporize. Materials with higher vapor pressures will evaporate more readily, which is essential for ensuring a consistent deposition rate during the process.
- Chemical Stability: The chemical reactivity of materials plays a key role in their selection. Materials like gold are chemically inert and resistant to oxidation, making them suitable for use in high-performance electronics or in environments where corrosion resistance is crucial.
- Adhesion and Film Quality: The ability of a material to adhere to the substrate is critical. Poor adhesion can result in weak or uneven films, which can compromise the performance of the final product. Materials like aluminum and copper provide strong adhesion to a wide variety of substrates, making them versatile choices for many applications.
3.2. Specific Applications
The intended application of the evaporation material significantly impacts the material selection process:
- Optical Coatings: For optical devices such as lenses, mirrors, and optical fibers, materials like magnesium fluoride (MgF₂) and titanium dioxide (TiO₂) are selected due to their optical properties, such as high transparency and specific refractive indices.
- Electronics and Semiconductor Devices: In semiconductor fabrication, materials like gold, copper, and silicon are chosen for their conductivity and ability to form high-quality thin films. These materials are used in the production of interconnects, transistors, and capacitors.
- Solar Energy: In the manufacture of thin-film solar cells, evaporation materials such as copper indium gallium selenide (CIGS) are used for their ability to convert sunlight into electrical energy efficiently.
- Magnetic Coatings: For hard drives and other data storage devices, magnetic materials like cobalt, nickel, and iron are used to create thin films that store data magnetically.
3.3. Economic Considerations
The cost of evaporation materials is another significant consideration. Metals like aluminum and copper are relatively inexpensive and widely available, making them ideal for mass-produced products. However, for specialized applications where material performance is critical, more expensive materials like gold or platinum might be required.
4. Diverse Applications of Evaporation Materials
Evaporation materials are used across a variety of industries and applications. Below are some of the most significant uses:
4.1. Semiconductor Manufacturing
Evaporation deposition is a cornerstone technique in semiconductor manufacturing, where thin layers of metal or other materials are deposited onto silicon wafers to create electrical components. These thin films are essential for the creation of ICs (integrated circuits), transistors, and other electronic components that power everything from smartphones to computers.
4.2. Optical Coatings
In the optical industry, evaporation materials are used to create thin films for optical coatings. These coatings can improve the performance of lenses, mirrors, and other optical components. Magnesium fluoride (MgF₂) and silicon dioxide (SiO₂) are frequently used to create anti-reflective coatings, which help reduce glare and increase light transmission in optical devices.
4.3. Renewable Energy and Solar Cells
The production of solar cells often involves the deposition of thin films of semiconductor materials using evaporation techniques. Materials like CIGS (copper indium gallium selenide) are deposited onto substrates to form efficient solar panels. These thin-film technologies are becoming increasingly popular for their ability to be produced at lower costs and with improved efficiency.
4.4. Data Storage Devices
Evaporation materials are also critical in the production of magnetic coatings used in hard drives and other data storage devices. The thin films deposited on these devices allow them to store data magnetically, playing a pivotal role in the functioning of digital storage technologies.
4.5. Aerospace and Defense
In aerospace and defense, evaporation materials are used to create coatings that protect sensitive equipment from extreme conditions. These materials are chosen for their ability to withstand high temperatures, resist corrosion, and maintain structural integrity under stress.
5. Conclusion
Evaporation materials are essential to a wide range of industries, from electronics to renewable energy and aerospace. The process of evaporation deposition allows for the precise creation of thin films that are used to manufacture critical components in modern technology. By understanding the properties of different materials and selecting the right ones for specific applications, manufacturers can ensure that their products meet the highest standards of performance and reliability. As the demand for advanced technology continues to grow, the role of evaporation materials will only become more crucial in shaping the future of manufacturing and innovation.