Indium powder is a unique, rare, and versatile material that has drawn attention across various industries, from electronics to solar energy. With its distinctive properties and wide-ranging applications, indium powder has become a subject of interest for researchers and engineers alike. This article offers an in-depth look at the world of indium powder—its properties, production methods, applications, environmental considerations, and future prospects.
Introduction
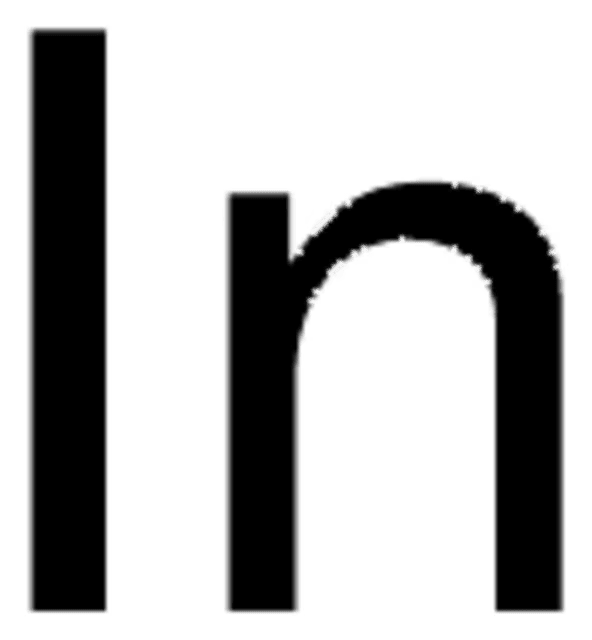
Indium is a post-transition metal that was discovered in the 1860s. It is a relatively soft, malleable metal with a bright, silvery appearance. In its powdered form, indium exhibits properties that make it highly desirable for modern technological applications. Unlike many other metals, indium possesses a combination of low melting point, ductility, and high thermal and electrical conductivity[1], which are essential attributes in high-tech manufacturing. The conversion of indium into a powder enhances its utility in processes like thin-film deposition[2], solder production, and as a catalyst in chemical reactions. Due to these factors, industries ranging from electronics to renewable energy have found innovative ways to incorporate indium powder into their processes. This article provides an exhaustive discussion of indium powder, delving into its history, characteristics, and significant roles in contemporary technology.
Historical Background and Discovery
Indium was first identified in 1863 by Ferdinand Reich and Theodor Richter during their spectroscopic analysis of zinc ores. The element was named for its indigo blue spectral line, a characteristic that set it apart from other metals at the time. Initially, indium was considered a curiosity of nature, largely due to its rarity and limited applications. However, as industries advanced and the need for specialized materials increased, the unique properties of indium became increasingly valued.
The early years of indium research were marked by experiments to understand its physical and chemical behavior. Over time, researchers realized that indium could be made even more useful when converted into various forms, including powders and thin films. Today, the powdered form of indium is a critical material in many high-tech applications, underpinning innovations in electronics and energy production.
Physical and Chemical Properties
Property | Value |
---|---|
Vapor Pressure | <0.01 mmHg (25 °C) |
Quality Level | 100 |
Assay | 99.99% trace metals basis |
Form | Powder |
Resistivity | 8.37 μΩ-cm |
Melting Point | 156.6 °C (lit.) |
Density | 7.3 g/mL at 25 °C (lit.) |
SMILES String | [In] |
InChI | 1S/In |
InChI Key | APFVFJFRJDLVQX-UHFFFAOYSA-N |
Indium powder is characterized by several key physical and chemical properties that set it apart from other powdered metals. Understanding these properties is essential for both its safe handling and effective utilization in industrial applications.
1. Particle Size and Surface Area
Indium powder can be produced with varying particle sizes, typically ranging from a few micrometers to sub-micrometer scales. The particle size influences many aspects of its performance, including reactivity, melting behavior, and ease of incorporation into composite materials. A smaller particle size usually means a higher surface area-to-volume ratio, which can enhance chemical reactivity—a desirable attribute in catalysis and certain electronic applications.
2. Melting Point and Thermal Properties
One of indium’s most notable characteristics is its low melting point of approximately 156.6 °C (313.9 °F). In its powdered form, this property allows for the production of low-melting point alloys and solders, which are crucial in electronics for attaching delicate components. Moreover, the excellent thermal conductivity of indium powder ensures efficient heat dissipation in high-performance electronic devices.
3. Electrical Conductivity
Indium is known for its high electrical conductivity, an essential feature for its role in electronic applications. When processed as a fine powder, indium can be used in conductive pastes and coatings, contributing to the production of reliable electrical contacts and circuits. This property is particularly valued in the manufacturing of touch screens and flat-panel displays.
4. Chemical Stability and Reactivity
Despite its high reactivity in powdered form (owing to increased surface area), indium is relatively resistant to oxidation. The formation of a thin, protective oxide layer on its surface can inhibit further corrosion, a beneficial trait when used in environments where chemical stability is paramount. This duality of reactivity and stability enables controlled chemical reactions, making indium powder a useful catalyst in specific chemical processes.
5. Malleability and Ductility
When indium is converted into a powder, its inherent malleability and ductility remain advantageous. These physical properties allow the material to be easily mixed with binders or other metals to form alloys. In applications like flexible electronics, the ability of indium-containing materials to sustain deformation without cracking is critical.
Production of Indium Powder
The production of indium powder involves several steps, each designed to preserve the unique properties of the metal while ensuring high purity and optimal particle size distribution. Here’s a look at some of the common methods used in manufacturing indium powder.
1. Extraction from Ores
Indium is typically extracted as a byproduct of zinc ore processing. In these processes, zinc ores are subjected to various purification methods that isolate indium from other metals. The extracted indium is usually in a molten state, from which it can be further processed into powder.
2. Atomization Techniques
Atomization is one of the primary methods used to produce metal powders, including indium powder. In this process, molten indium is forced through a nozzle or atomizer, where it is rapidly cooled by a jet of inert gas or water. The rapid solidification results in fine, spherical particles with controlled size distributions. This technique is highly valued for its ability to produce powders with a uniform morphology and excellent flowability.
3. Mechanical Milling
Another method to produce indium powder is through mechanical milling, where larger pieces of indium are ground into fine particles. Although this method is simpler, it can sometimes result in a broader distribution of particle sizes and may introduce impurities from the milling media. Consequently, additional purification steps are often necessary.
4. Chemical Reduction Processes
Chemical methods involve the reduction of indium compounds to produce elemental indium powder. These processes typically employ reducing agents in controlled environments, ensuring that the final product is of high purity. Chemical reduction can be finely tuned to achieve specific particle sizes and surface characteristics, making it a preferred method for applications where purity is critical.
5. Post-Processing and Quality Control
After the primary production, indium powder undergoes rigorous quality control to ensure consistency in particle size, morphology, and purity. Techniques such as scanning electron microscopy (SEM) and X-ray diffraction (XRD) are commonly used to analyze the structure and composition of the powder. This quality control step is essential, especially for applications in the electronics and photovoltaic industries where even minor impurities can significantly affect performance.
Applications in Modern Technology
Indium powder’s unique properties have spurred its use in a variety of technological applications. Its role is particularly prominent in industries that demand materials with specific electrical, thermal, and chemical properties.
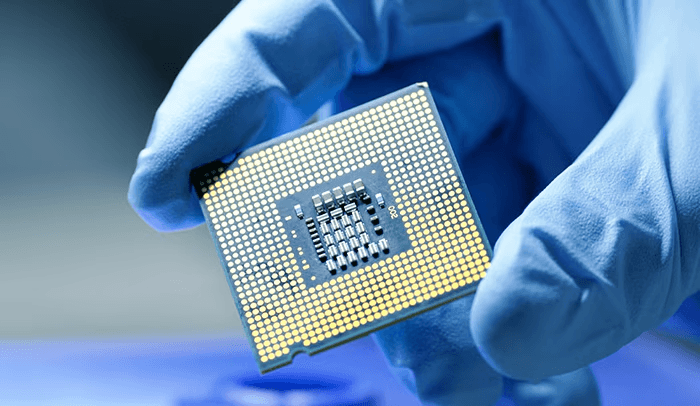
1. Electronics and Semiconductors
In the realm of electronics, indium powder is primarily used in the creation of conductive pastes and solders. Its low melting point allows for the production of low-temperature solders, which are crucial for assembling delicate semiconductor components without damaging them. Additionally, indium-based solders are renowned for their ability to form strong, reliable joints that maintain excellent electrical conductivity even under thermal stress.
Conductive Pastes
Indium powder is a key component in conductive pastes that are applied to circuits and electronic displays. These pastes facilitate efficient electrical connections while ensuring that heat is effectively dissipated, which is vital in high-performance electronic devices.
Transparent Conductive Films
Another significant application is in the manufacturing of transparent conductive films. Indium tin oxide (ITO), which incorporates indium, is widely used for producing touch screens, flat-panel displays, and solar cells. Although ITO is a compound rather than a pure indium powder, the production processes often start with high-purity indium powder that is later oxidized and mixed with tin oxide.
2. Photovoltaics and Renewable Energy
The renewable energy sector has embraced indium powder through its use in thin-film solar cells. Indium-based compounds are employed to enhance the efficiency of solar cells by acting as buffer layers or transparent electrodes. The superior conductivity and optical transparency of these compounds contribute to the overall performance of photovoltaic devices, making them a cornerstone in the advancement of solar energy technologies.
3. Soldering and Bonding Materials
Due to its low melting point and excellent bonding properties, indium powder is a preferred material in various soldering applications. It is used in the production of specialty solders that require high reliability, such as those found in aerospace, medical devices, and cryogenic equipment. The unique ability of indium-based solders to maintain mechanical integrity at extreme temperatures makes them indispensable in environments where conventional solders might fail.
4. Catalysis and Chemical Reactions
Indium powder also finds applications as a catalyst or catalyst support in several chemical reactions. Its high surface area and reactivity enable it to facilitate complex chemical transformations, particularly in organic synthesis. Research is ongoing to expand the use of indium-based catalysts in green chemistry applications, where efficiency and environmental considerations are of paramount importance.
5. Advanced Coatings and Composite Materials
In addition to its direct applications, indium powder is often incorporated into advanced coatings and composite materials. When mixed with polymers or other metals, indium can enhance the thermal, electrical, and mechanical properties of the final product. These composite materials are finding increasing use in industries such as automotive manufacturing, aerospace engineering, and consumer electronics.
Environmental and Safety Considerations
With any industrial material, understanding and mitigating environmental and safety risks is essential. Although indium is not considered highly toxic compared to some heavy metals, its powdered form can pose challenges if not handled properly.
1. Occupational Exposure
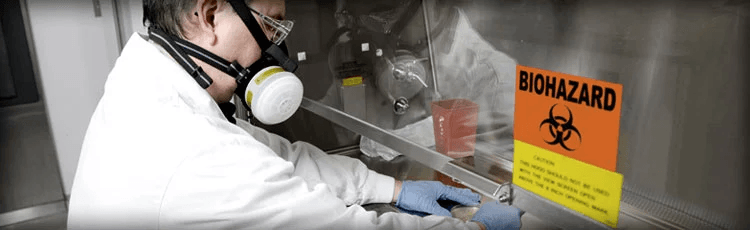
Workers involved in the production and handling of indium powder need to adhere to strict safety protocols. Inhalation of fine particles, for instance, can lead to respiratory issues. Therefore, proper personal protective equipment (PPE) such as respirators, gloves, and protective clothing is necessary. Facilities often employ advanced ventilation systems and dust collection methods to minimize exposure.
2. Environmental Impact
Indium is classified as a critical raw material, and its mining and extraction can have significant environmental implications. The recovery process from zinc ores involves several steps that may produce hazardous by-products. Recycling and responsible waste management are thus vital components of the indium supply chain. Research is underway to improve extraction and recycling techniques to reduce environmental footprints and enhance sustainability.
3. Regulatory Compliance
In regions where the production and use of indium powder are significant, regulatory frameworks are in place to ensure that environmental and worker safety standards are maintained. Compliance with international guidelines and local regulations is critical to preventing adverse health effects and minimizing environmental degradation.
Research and Future Prospects
The evolving landscape of technology continuously drives the demand for materials with specialized properties, and indium powder is no exception. Ongoing research seeks to harness its unique attributes in novel applications and enhance its production processes.
1. Nanotechnology
Advances in nanotechnology have opened new avenues for the application of indium powder. By engineering the particle size down to the nanoscale, scientists can tailor its optical, electrical, and catalytic properties with greater precision. Nano-indium powder is being investigated for use in next-generation semiconductor devices, sensors, and even in medical applications where biocompatibility and precision are critical.
2. Energy Storage and Conversion
Energy storage is another frontier where indium powder shows potential. Research is focused on incorporating indium into advanced battery technologies and fuel cells. Its ability to conduct heat and electricity efficiently makes it a promising candidate for enhancing the performance and longevity of energy storage devices.
3. Improving Soldering Technology
The electronics industry continually seeks materials that offer superior reliability and performance, particularly in miniaturized and high-density circuits. Indium-based solders are at the forefront of this effort. Future research aims to develop formulations that further reduce the melting temperature while maintaining excellent mechanical and electrical properties, paving the way for more efficient and robust electronic packaging solutions.
4. Sustainable Production and Recycling
Given the critical role of indium in many high-tech applications, sustainability remains a major research focus. Innovations in extraction, production, and recycling methods are being pursued to ensure a steady supply of high-purity indium powder while minimizing environmental impacts. Developing more efficient recycling processes not only conserves this scarce resource but also helps reduce the ecological footprint associated with its extraction and processing.
5. Collaborative Industry-Academia Efforts
The future of indium powder is being shaped by collaborative efforts between academia, research institutions, and industry players. Joint ventures and interdisciplinary research projects are accelerating the development of novel applications and improved production techniques. These collaborations are crucial for addressing the challenges associated with scaling up production, reducing costs, and meeting the increasing demand in electronics, renewable energy, and advanced materials.
Challenges and Considerations
Despite the promising outlook, several challenges must be addressed to fully harness the potential of indium powder. These challenges include:
1. Supply Chain and Resource Scarcity
Indium is relatively rare, and its supply is closely linked to zinc production. This dependency makes the supply chain vulnerable to fluctuations in zinc mining and processing activities. Efforts to improve recycling rates and develop alternative sources are essential to mitigating this risk.
2. Cost Implications
The cost of indium, particularly in its high-purity powder form, can be significant. For many industries, especially those operating on thin margins, the price of indium-based materials is a critical factor. Research into more cost-effective production and recycling methods could help reduce the overall expense and encourage broader adoption.
3. Technical and Processing Challenges
Producing indium powder with consistent quality requires advanced processing technologies and stringent quality control measures. Variations in particle size distribution or the presence of impurities can significantly affect performance in sensitive applications like semiconductors and solar cells. Continuous improvement in production technology and quality assurance protocols is necessary to meet the rigorous demands of modern industry.
4. Environmental Regulations
As global awareness of environmental issues grows, stricter regulations may impact the production and disposal of materials like indium powder. Companies will need to invest in sustainable practices and cleaner technologies to comply with evolving environmental standards while remaining competitive.
Conclusion
Indium powder stands as a testament to how even the most obscure elements can find critical applications in modern technology. From its discovery in the 19th century to its current role in cutting-edge industries such as electronics, photovoltaics, and advanced materials, indium powder has evolved into a material of significant scientific and industrial importance.
Its unique combination of low melting point, excellent conductivity, and chemical stability makes it indispensable in the production of specialized solders, conductive pastes, and transparent conductive films. These attributes, coupled with the versatility provided by modern production techniques such as atomization and chemical reduction, ensure that indium powder will continue to play a vital role in future technological advancements.
Moreover, the ongoing research in nanotechnology, energy storage, and sustainable production methods promises to unlock even more potential for this extraordinary material. The challenges related to supply chain security, cost, and environmental impact are being actively addressed by collaborative efforts across industries and research institutions, paving the way for innovations that could redefine the applications of indium powder.
As industries move toward more sustainable and efficient practices, the importance of critical raw materials like indium is set to increase. Advances in recycling technology, improved extraction methods, and enhanced processing techniques are essential to meet the growing demand while preserving environmental integrity.
In summary, the journey of indium powder—from its serendipitous discovery to its current status as a cornerstone material in high-tech applications—illustrates the remarkable interplay between scientific discovery and industrial innovation. Its future is intertwined with the development of next-generation technologies, and continued research and collaboration will undoubtedly further enhance its applications. As we look to the future, indium powder not only symbolizes the progress made in material science but also stands as a beacon for the potential of sustainable, innovative manufacturing in a rapidly changing world.
The evolution of indium powder also underscores the importance of investing in research and development. With every new application, from flexible electronics to renewable energy systems, the material’s role is redefined and expanded. The continuous quest to improve its production and integration into advanced materials highlights the dynamic nature of modern industrial chemistry and the broader fields of materials science and engineering.
In a world that increasingly relies on miniaturized, efficient, and sustainable technologies, indium powder is poised to remain at the forefront of innovation. Researchers are already exploring ways to harness its properties to create materials that can operate under extreme conditions, offer enhanced performance, and contribute to a more sustainable industrial ecosystem. Whether it is through novel catalyst designs or the development of next-generation electronic components, the journey of indium powder is far from over.
The interplay of economic, environmental, and technological factors makes the study of indium powder not just a niche academic pursuit but a critical component of future industrial strategies. As we navigate the complexities of resource management and technological advancement, materials like indium powder remind us that even rare elements can drive significant progress and innovation.
Ultimately, the future of indium powder will depend on our ability to integrate its unique properties into scalable, sustainable technologies. The continued collaboration between industry, academia, and regulatory bodies will be essential in ensuring that this valuable resource is used responsibly and efficiently. In doing so, we can unlock new possibilities in electronics, renewable energy, and beyond—ushering in an era where the seemingly modest indium powder plays a starring role in powering the technologies of tomorrow.
With the challenges ahead and the immense potential on the horizon, indium powder serves as an excellent example of how targeted research, innovative production methods, and thoughtful application can transform a rare element into a cornerstone of modern industry. Its story is one of discovery, adaptation, and continuous innovation—one that will likely inspire future breakthroughs in materials science and engineering.
In conclusion, indium powder is more than just a component in high-tech applications—it is a symbol of progress in material science. From its early days as a minor byproduct of zinc mining to its current status as a critical material in electronics, renewable energy, and advanced composites, indium powder has cemented its place in the modern industrial landscape. As research continues to reveal new ways to exploit its properties, the future looks bright for this fascinating material, promising further innovations and applications that may well redefine our technological capabilities in the decades to come.