Introduction to Molybdenum Oxide Evaporation Materials
Molybdenum oxide (MoO₃) is a compound formed by the combination of molybdenum with oxygen, and it plays a crucial role in various industrial processes, particularly in thin film deposition. Thin film deposition involves the application of a layer of material onto a substrate in the form of a very thin layer, often just a few microns or nanometers thick. Molybdenum oxide is used as an evaporation material in this process due to its unique physical and chemical properties.
Evaporation materials like molybdenum oxide are essential in several industries, including electronics, optoelectronics, and solar technology. These materials are used to create thin films with specific properties that enhance the performance and functionality of electronic devices, sensors, coatings, and other products.
This article delves deep into the uses of molybdenum oxide as an evaporation material, its role in various industries, and the specific applications that benefit from its unique characteristics.
What is Molybdenum Oxide?
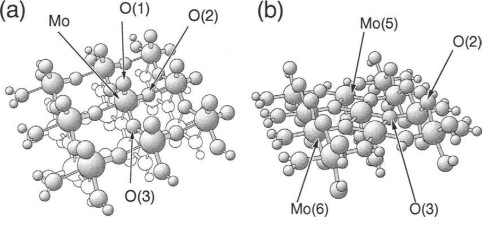
Molybdenum oxide (MoO₃) is an inorganic compound that consists of molybdenum in a high oxidation state (+6) combined with oxygen. It is commonly found as a solid with a characteristic yellow to white color. Molybdenum oxide is produced by heating molybdenum metal in the presence of oxygen or air, and it is typically available in several forms, including MoO₃ powder and MoO₃ thin films.
The material is known for its high melting point (around 795°C), high stability under normal atmospheric conditions, and its ability to undergo various oxidation and reduction reactions. These properties make molybdenum oxide suitable for use in a range of high-performance applications, especially in thin film deposition techniques like evaporation.
How is Molybdenum Oxide Used in Evaporation?
In evaporation, molybdenum oxide is used as a source material, typically in the form of a solid powder or pellet. The material is heated in a vacuum chamber or a high-vacuum environment, causing it to vaporize and then condense onto a substrate surface. This vapor deposition process is critical for the production of thin films that are uniform, precise, and have the desired optical, electrical, and mechanical properties.
During evaporation, molybdenum oxide can be used to form thin films of MoO₃ or combined with other materials to create mixed or alloyed films with specific characteristics. The film’s thickness, uniformity, and deposition rate can be carefully controlled by adjusting parameters such as the temperature of the evaporant, the vacuum level, and the deposition time.
The high-quality films produced through this process are often utilized in the fabrication of semiconductors, solar cells, and optical coatings, among other applications.
Industrial Applications of Molybdenum Oxide Evaporation Materials
Molybdenum oxide evaporation materials have a variety of uses across different industries. Below are some of the most prominent sectors that benefit from the use of MoO₃ in thin film deposition:
1. Electronics and Semiconductor Industry
In the electronics industry, molybdenum oxide thin films are essential for producing components like resistors, capacitors, and transistors. The high conductivity, stability, and optical properties of MoO₃ make it suitable for use in microelectronics, where precise control over material properties is necessary for optimal device performance.
Molybdenum oxide is also used in the fabrication of transparent conductive films, which are crucial in the production of touchscreens, flat-panel displays, and OLEDs (Organic Light-Emitting Diodes). MoO₃ thin films can provide excellent transparency while maintaining electrical conductivity, making them ideal for use in these applications.
2. Solar Cells and Photovoltaics
One of the most exciting applications of molybdenum oxide is in the field of solar energy, particularly in the production of thin-film solar cells. Molybdenum oxide is used as a hole transport material (HTM) in certain types of photovoltaic devices, including perovskite solar cells. The ability of MoO₃ to efficiently transport positive charge carriers (holes) while blocking electrons is crucial for enhancing the performance of these solar cells.
In thin-film solar cells, molybdenum oxide is also used as an electrode material, often in combination with other metals such as copper or silver, to improve the efficiency and stability of the solar cell. The thin-film deposition of MoO₃ can significantly enhance the power conversion efficiency (PCE) of solar panels, making them more competitive with traditional silicon-based solar cells.
3. Optoelectronics
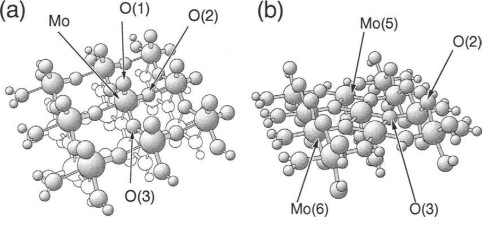
In optoelectronics, molybdenum oxide thin films are used for a variety of applications, including optical coatings, sensors, and light-emitting devices. MoO₃ films are often used in the fabrication of optoelectronic devices because of their unique electronic and optical properties. For instance, they can serve as transparent conductive layers in devices like organic solar cells, organic light-emitting diodes (OLEDs), and organic photodetectors (OPDs).
The optical properties of MoO₃ thin films, particularly their ability to interact with light in specific ways, make them useful for creating anti-reflective coatings and optical filters. These coatings can help improve the efficiency of optoelectronic devices by minimizing light losses and ensuring that the maximum amount of light is absorbed or emitted by the device.
4. Sputtering Targets and Coatings
In addition to evaporation, molybdenum oxide is also used as a sputtering target material for thin film deposition. Sputtering is a technique similar to evaporation but involves bombarding a material with high-energy ions to eject atoms or molecules, which then deposit onto a substrate. Molybdenum oxide sputtering targets are commonly used in the production of thin films for semiconductors, optical devices, and other high-performance coatings.
MoO₃ films created via sputtering are often used in hard coatings, corrosion-resistant films, and wear-resistant coatings. These applications benefit from the strong adhesion properties and stability of MoO₃ under various environmental conditions.
5. Catalysis and Chemical Reactions
Molybdenum oxide is also known for its catalytic properties, which make it useful in certain chemical processes. MoO₃ thin films are often employed as catalysts in reactions like oxidation, hydrogenation, and dehydrogenation, where they facilitate the conversion of raw materials into more valuable products.
In these applications, the thin molybdenum oxide films serve as highly active surfaces that speed up the reaction without being consumed in the process. This is particularly important in industrial settings where catalysts are required for large-scale chemical production, such as in the manufacture of chemicals, fertilizers, and petroleum products.
6. Superconductors and Advanced Materials
Molybdenum oxide is also of interest in the development of superconducting materials. MoO₃-based films have been explored for use in superconducting devices, particularly those operating at higher temperatures. These materials can exhibit superconductivity under certain conditions, making them suitable for use in advanced electronic systems, quantum computing, and magnetic resonance imaging (MRI).
Thin films of MoO₃ can be combined with other superconducting materials to create composite films with enhanced properties, including higher critical temperatures and improved stability.
7. Research and Development
Molybdenum oxide evaporation materials are also widely used in research and development (R&D) settings, particularly in laboratories studying advanced materials and novel technologies. Researchers use MoO₃ thin films to explore the properties of materials under different conditions, to test new fabrication techniques, and to investigate new applications in fields such as nanotechnology, quantum computing, and energy storage.
Advantages of Using Molybdenum Oxide in Evaporation
The use of molybdenum oxide as an evaporation material comes with several advantages that make it a preferred choice in various industries:
- High Melting Point: Molybdenum oxide has a high melting point, making it suitable for use in high-temperature deposition processes. This characteristic ensures that MoO₃ remains stable and does not degrade during the evaporation process.
- Good Electrical Conductivity: MoO₃ thin films exhibit good electrical conductivity, making them ideal for use in electronic and optoelectronic devices that require efficient charge transport.
- Optical Transparency: Molybdenum oxide thin films are transparent in the visible and infrared spectra, making them useful in applications where optical clarity and conductivity are required simultaneously.
- Chemical Stability: MoO₃ is chemically stable and resistant to oxidation, which ensures that the thin films produced from it remain stable under various environmental conditions, contributing to the longevity and performance of the devices.
- Versatility: Molybdenum oxide can be used in a wide range of applications, from semiconductors and photovoltaics to optical coatings and catalysis, making it a versatile material for advanced manufacturing.
Conclusion
Molybdenum oxide evaporation materials are indispensable in a wide range of high-tech industries, particularly in the fields of electronics, solar energy, optoelectronics, and catalysis. The unique properties of MoO₃, such as its high melting point, electrical conductivity, optical transparency, and chemical stability, make it ideal for thin film deposition processes that require precision and performance.
From improving the efficiency of solar cells to enabling the development of next-generation electronic devices, molybdenum oxide continues to play a critical role in driving innovation and progress across multiple sectors. Its versatility and wide range of applications make it a material of choice for both commercial production and cutting-edge research.
As industries continue to push the boundaries of technology, molybdenum oxide will remain a key player in the development of advanced materials, devices, and systems that shape our future.