Introduction
The evolution of solid-state ionic conductors and perovskite-based ceramics has given rise to a class of functional oxides whose electrochemical performance and chemical resilience make them integral to modern energy conversion and sensing technologies. Among them, Barium Cerium Yttrium Zirconate (BaCe₁₋ₓ₋ᵧYₓZrᵧO₃, abbreviated as BZCY) has emerged as a tunable perovskite-type compound offering both high protonic conductivity and remarkable thermochemical stability, particularly under intermediate-temperature conditions.
As deposition techniques transition from bulk ceramic fabrication to thin-film design for next-generation solid oxide fuel cells (SOFCs), hydrogen separation membranes, and electrochemical sensors, the need for high-purity, stoichiometrically consistent BZCY sputtering targets has become apparent. The fabrication and application of such targets are not trivial; the complexity arises not only from the multicomponent phase diagram but also from the physical challenges of sintering cerium-based oxides without secondary phase segregation.
This article focuses on the interplay between BZCY’s material chemistry and its behavior as a sputtering target, covering its structural considerations, fabrication constraints, deposition dynamics, and the critical role it plays in enabling proton-conductive thin films.
Crystallographic Considerations and Ionic Transport Mechanism
BZCY is structurally derived from the cubic perovskite ABO₃ lattice, where A-sites are occupied by Ba²⁺ ions and B-sites are partially substituted with Ce⁴⁺, Y³⁺, and Zr⁴⁺. The careful manipulation of Ce⁴⁺ replacement with Zr⁴⁺ and Y³⁺ introduces oxygen vacancies and modifies the local lattice distortion. The dopant ratio directly influences oxygen ion mobility and proton incorporation under humidified environments.
Yttrium, as a trivalent dopant, introduces acceptor states that increase protonic conductivity by generating oxygen vacancies, while zirconium enhances structural and chemical stability, particularly in environments containing CO₂ or H₂O — conditions under which pure BaCeO₃ would otherwise decompose due to BaCO₃ formation. The co-doping strategy effectively balances conductivity with thermodynamic robustness.
Neutron diffraction and impedance spectroscopy studies confirm that BZCY retains a pseudo-cubic structure with minor orthorhombic distortion, particularly in samples where Ce:Zr ratios range between 6:4 and 5:5. The phase homogeneity is essential for sputtering targets, as any secondary phases such as BaZrO₃ or BaCeO₃-rich domains can lead to compositional nonuniformity during deposition.
Powder Synthesis and Target Densification
Producing a BZCY sputtering target begins with the synthesis of homogeneously doped oxide powders. Traditional solid-state reactions involving BaCO₃, CeO₂, ZrO₂, and Y₂O₃ suffer from high-temperature calcination (>1200°C) and incomplete reaction unless extended dwell times are applied. A more refined approach utilizes sol-gel or Pechini methods, which allow molecular-level mixing and reduce the onset temperature for perovskite phase formation.
After calcination, the phase-pure powder is subjected to attrition milling to achieve a submicron particle size distribution, which is critical for high green density and sintering reactivity. Cold isostatic pressing (CIP) is preferred over uniaxial pressing to eliminate inter-particle voids and anisotropic compaction that may induce cracking during sintering.
Sintering of BZCY targets typically requires a controlled atmosphere—preferably a humidified Ar-H₂ mix or oxygen-deficient environment—to suppress cerium reduction and barium volatilization. High-purity alumina setters and sacrificial powder beds are used to mitigate alkali loss. Optimal densification (>95% theoretical density) is generally achieved at 1500–1550°C over 6–10 hours, with rapid heating rates avoided to prevent differential sintering and thermal shock.
Post-sintering, the ceramic is lapped and polished to achieve sub-µm surface roughness and <±0.05 mm thickness uniformity, essential for uniform sputter erosion profiles.
Sputtering Dynamics and Film Growth Behavior
When employed in radio-frequency (RF) or pulsed-DC magnetron sputtering, BZCY targets exhibit behavior characteristic of insulating ceramics. Ar/O₂ gas mixtures are typically required to stabilize the plasma and to maintain stoichiometric transfer to the substrate. The presence of zirconium improves target mechanical integrity, reducing the likelihood of catastrophic cracking under plasma bombardment.
During deposition, substrate temperature must be carefully controlled (typically 400–600°C) to encourage crystalline growth while preventing phase decomposition or volatile loss of Ba and Ce species. The growth of oriented BZCY films depends on lattice matching with the substrate (e.g., YSZ, sapphire, MgO), as well as post-deposition annealing protocols.
One challenge in thin-film growth lies in preserving the protonic conductivity of BZCY in nano-scaled layers. Studies have shown that grain boundary resistance and oxygen vacancy annihilation can reduce proton transport compared to bulk ceramics. However, modifying film microstructure via bias sputtering or multi-layered architectures has shown promise in recovering or even enhancing conductivity.
Applications in Energy and Sensing Platforms
Intermediate-Temperature Solid Oxide Fuel Cells (IT-SOFCs)
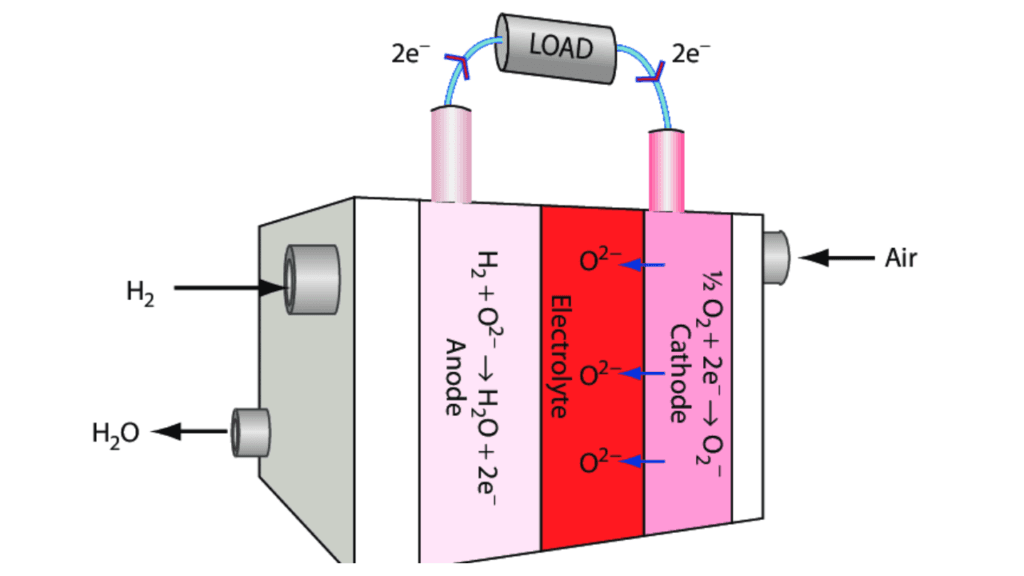
BZCY films serve as proton-conducting electrolytes in IT-SOFCs operating in the 400–700°C range. Unlike conventional oxygen-ion conductors such as YSZ, BZCY enables hydrogen conduction with lower activation energy, allowing reduced operating temperatures and extended material compatibility with metallic interconnects and catalysts.
The thin-film form factor, especially when fabricated using BZCY sputtering targets, allows reduction of electrolyte thickness below 1 µm, dramatically lowering ohmic resistance and enhancing power density. Additionally, the chemical resilience of BZCY towards H₂O and CO₂ extends the longevity of fuel cells exposed to hydrocarbon reformates.
Protonic Ceramic Electrochemical Cells (PCECs)
Beyond fuel cells, BZCY thin films are being integrated into electrochemical hydrogen pumps and ammonia synthesis reactors, where their dual proton/electron blocking capability and low crossover flux make them ideal for gas separation and catalysis.
High-Temperature Sensors
BZCY’s mixed ionic-electronic conduction and environmental stability make it suitable for use in NOₓ and oxygen sensors operating under harsh exhaust or industrial conditions. Thin films sputtered from dense BZCY targets provide fast response times and reproducibility, which are critical in closed-loop combustion systems.
Limitations and Emerging Challenges
Despite its promise, several material and processing issues remain unresolved:
- Target Fragility: Due to the inherent brittleness of perovskite ceramics, mechanical handling of BZCY targets must be conducted with care. Any microcrack can propagate during thermal cycling or plasma stress, leading to target failure.
- Phase Segregation Risk: Non-equilibrium film growth can lead to localized Ba or Ce enrichment, forming insulating phases detrimental to film conductivity.
- Hydration Instability: In thin-film form, exposure to humidified environments can lead to slow degradation via hydroxylation of grain boundaries, especially in films not properly annealed.
- Cost and Scale: High fabrication cost due to raw material purity requirements and sintering complexity limits large-scale commercial deployment.
Advanced Research Directions
Recent research has begun to address these issues through several strategies:
- Atomic Layer Deposition (ALD) and Hybrid Sputtering: These techniques offer atomic-scale control over film composition and thickness, allowing better interfacial engineering.
- Nanocomposite Targets: Incorporating doped ceria or layered heterostructures into BZCY targets to create composite sputtering sources can enhance mechanical durability and tailor film functionality.
- In-situ Diagnostic Tools: Real-time RHEED and spectroscopic ellipsometry during sputtering are being adopted to optimize deposition parameters dynamically, ensuring film stoichiometry and phase purity.
- Scalable Bonding Solutions: To reduce cracking risks, elastomeric or active metal bonding technologies are being explored for mounting brittle BZCY targets to backing plates without introducing thermal mismatch stress.
Conclusion
The deployment of Barium Cerium Yttrium Zirconate sputtering targets represents a confluence of materials chemistry, ceramics engineering, and thin-film deposition science. Its role in fabricating advanced proton-conducting layers, particularly for intermediate-temperature electrochemical energy systems, is both timely and transformative. Yet, the challenges associated with target fabrication, plasma stability, and film performance remain active areas of research.
With further innovations in powder synthesis, target densification, and plasma-assisted deposition techniques, BZCY sputtering targets are expected to underpin a new generation of high-efficiency, low-temperature, and durable ceramic devices — essential components in the global transition to sustainable energy technologies.