Introduction
The deposition rate is a critical parameter in thin film deposition processes, directly influencing production efficiency, cost, and material properties. Whether in industries like semiconductor manufacturing, optics, or coatings, optimizing the deposition rate is essential for achieving desired results while maintaining high quality. This article explores practical methods to increase the deposition rate and the associated benefits and challenges.
Understanding Deposition Rate
Definition of Deposition Rate
The deposition rate refers to the thickness of a material deposited on a substrate per unit of time, typically measured in nanometers per second (nm/s) or angstroms per second (Å/s). It reflects the efficiency of a deposition process and its ability to meet production demands.
Factors Affecting Deposition Rate
Several factors influence the deposition rate, including:
- Material Supply: The availability and delivery rate of the source material significantly impact the deposition rate.
- Vacuum Chamber Pressure: Lower chamber pressures reduce collisions between particles, enabling higher deposition rates.
- Substrate Temperature: Higher temperatures can enhance material adhesion and reactivity.
- Plasma Energy or Power: Adjusting power in processes like sputtering or plasma-enhanced chemical vapor deposition (PECVD) directly affects the deposition rate.
Practical Methods to Increase Deposition Rate
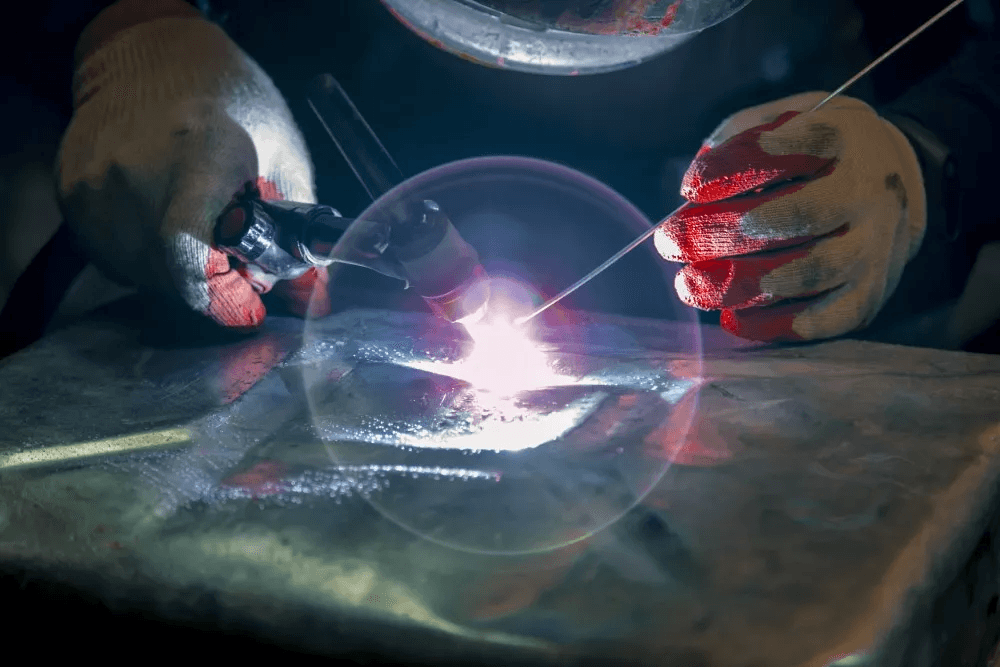
Increasing the Deposition Source Power
The most common way to boost the deposition rate is to increase the power of the deposition source. This can be done by increasing the beam current, filament current, or RF power, depending on the type of deposition technique. With greater source power, more atoms or molecules become available for deposition, leading to a higher deposition rate.
However, caution is needed because high power might damage the system or melt the target. Additionally, excessive power can result in energy dissipation, increased costs, and potential equipment wear.
Decreasing the Source-to-Substrate Distance
Reducing the source-to-substrate distance (“r”) is an effective method in certain deposition techniques. Since the arrival rate of sputtered particles is inversely proportional to 1/r², decreasing the distance can significantly enhance the deposition rate.
That said, reducing the distance may impact the uniformity and quality of the deposited film. A larger throw distance allows more particle collisions, which helps refine particles and improve uniformity, while a reduced distance might lead to less collision and lower uniformity.
Increasing the Substrate Temperature
Raising the substrate temperature increases the deposition rate by enhancing the diffusion rate of deposited species on the substrate. Higher temperatures promote faster surface mobility, resulting in quicker and more efficient deposition.
Nevertheless, the operating temperature must be carefully controlled to avoid adverse effects on the film’s properties, such as crystal structure, composition, and adhesion.
Using a Higher Pressure Environment
In certain cases, increasing the pressure of the deposition environment can boost the deposition rate. For instance, in physical vapor deposition (PVD) techniques like sputtering, higher pressure can increase plasma density, leading to a higher deposition rate.
However, increasing pressure may have drawbacks. For one, it could affect the characteristics of the deposited film, such as its density and surface roughness. Additionally, higher pressure might reduce thin film uniformity due to decreased particle collisions.
Employing Multiple Sources
Using multiple deposition sources is an effective method to enhance the deposition rate. This approach increases the deposition area and enables simultaneous deposition of various materials. It is especially beneficial for co-deposition processes, where composite films are formed by depositing two or more materials together.
High-Power Impulse Magnetron Sputtering (HiPIMS)
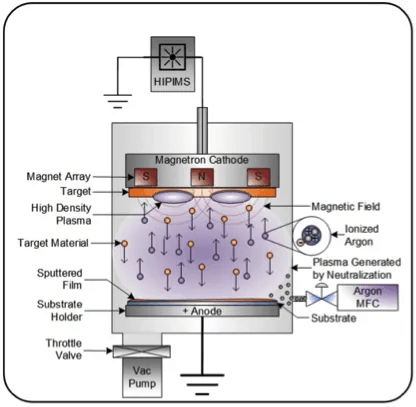
HiPIMS utilizes high power in short pulses to ionize a larger fraction of the sputtered material. This results in better adhesion and higher deposition rates compared to traditional DC magnetron sputtering. Though energy-intensive, HiPIMS produces denser and more uniform films.
Plasma Density Optimization
By using advanced plasma generation techniques, such as electron cyclotron resonance (ECR) or inductively coupled plasma (ICP), manufacturers can achieve a higher density of plasma, directly contributing to an increased deposition rate. These methods are particularly effective for precise control over film characteristics.
Other Methods
- Larger Target Sizes: Larger targets provide more material, resulting in increased sputter rates and deposition rates.
- Adding More Guns: Incorporating additional guns can double or even triple the sputtering and deposition rates, although this method can be expensive.
Benefits of Increasing Deposition Rate
Enhanced Productivity
Higher deposition rates translate to shorter production cycles, allowing manufacturers to meet higher demand efficiently.
Cost Efficiency
Increased rates reduce energy consumption per unit of material deposited, lowering operational costs.
Improved Competitiveness
Faster processes enable companies to bring products to market more quickly, providing a competitive edge.
Challenges of Increasing Deposition Rate
Maintaining Film Quality
Higher rates may compromise film quality, leading to defects like non-uniform thickness, stress, or poor adhesion.
Equipment Limitations
Existing equipment may not support high deposition rates without modifications or upgrades, requiring additional investment.
Process Complexity
Balancing deposition rate with other parameters like temperature, pressure, and material properties adds complexity to the process.
Environmental Considerations in High Deposition Rates
Energy Consumption
Increasing deposition rates often results in higher energy usage. Employing energy-efficient systems and practices can mitigate this impact.
Sustainability
Using recyclable target materials and optimizing material usage helps reduce waste and environmental impact.
Vacuum Pump Maintenance
Efficient maintenance of vacuum systems ensures stable deposition conditions while minimizing unnecessary energy loss.
Case Studies
Example 1: Semiconductor Manufacturing
In semiconductor applications, optimizing magnetron sputtering with higher power and advanced target designs increased deposition rates by 30% without affecting film uniformity.
Example 2: Optical Coating Production
In optical coating processes, implementing multi-target configurations reduced cycle times by 40%, enabling higher throughput while maintaining optical clarity.
Future Trends in Thin Film Deposition
Scalability
Emerging deposition methods are becoming increasingly scalable for industrial production while maintaining efficiency.
Nano-Scale Precision
Innovations in atomic-level control ensure high deposition rates without compromising precision and quality.
Material Innovations
Developing novel materials with high sputtering yields and better thermal properties enables faster and more efficient deposition processes.
Conclusion
Increasing deposition rates offers significant advantages, including enhanced productivity, cost efficiency, and competitiveness. By implementing strategies such as optimizing material supply, improving chamber conditions, and leveraging advanced techniques, manufacturers can achieve higher rates without compromising film quality. However, addressing challenges like equipment limitations and process complexity is essential for sustainable improvements. A balanced, well-monitored approach tailored to specific applications ensures the success of deposition processes.