1. Introduction: The Crucial Role of Thermal Management in Space
The space environment is uniquely hostile to human-made structures. Outside Earth’s atmosphere, spacecraft are subject to intense solar radiation, extreme thermal fluctuations, and a vacuum that eliminates conventional methods of heat dissipation. These conditions demand robust thermal control systems (TCS) that can maintain internal temperatures within strict operational limits, ensuring the stability of scientific instruments, electronic subsystems, and structural components.
Because convective and conductive heat transfer are nearly absent in space, radiative transfer becomes the dominant mechanism. To harness and regulate radiative heat exchange, engineers have developed specialized materials and surface treatments. Among these, thermal control coatings—engineered thin films applied to spacecraft surfaces—are a critical solution. These coatings help modulate solar absorption and infrared emission, effectively influencing a spacecraft’s thermal equilibrium.
A growing subset of these thermal coatings are created through advanced deposition technologies such as physical vapor deposition (PVD), particularly magnetron sputtering. At the heart of these systems lie the sputtering target materials, which serve as the source of coating atoms. The selection, engineering, and performance of these targets directly impact the reliability and efficiency of thermal control coatings.
2. Thermal Control Coatings: Principles and Function
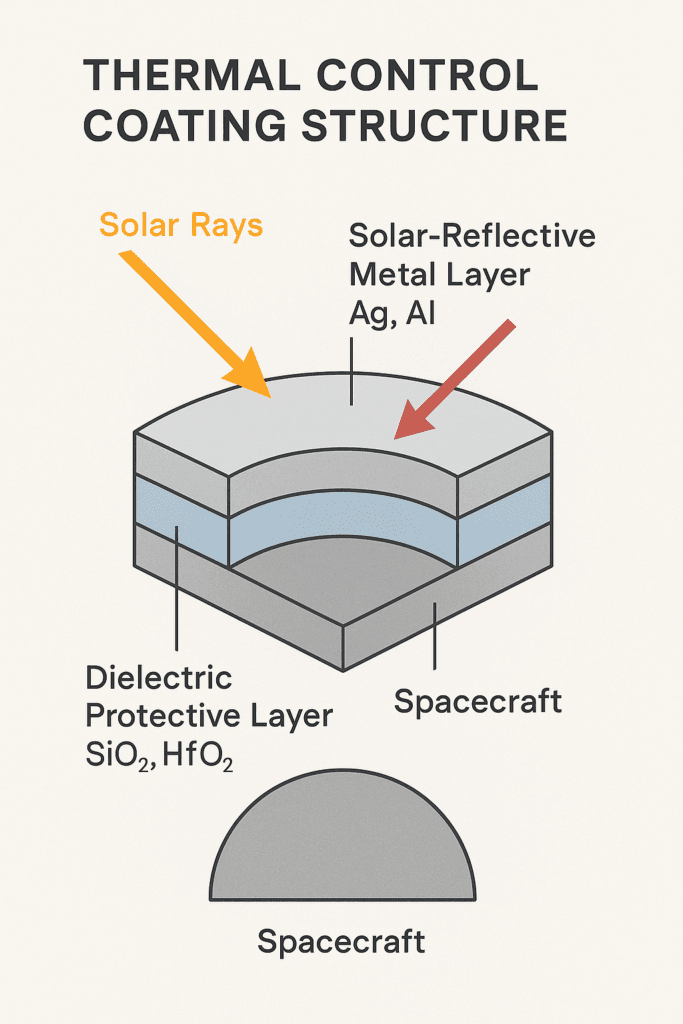
Thermal control coatings are engineered to either reflect incoming solar radiation or emit excess heat into space, depending on mission requirements. These coatings fall broadly into two functional types:
- Passive coatings: Rely on inherent optical and thermal properties to manage heat transfer.
- Active coatings: Alter their properties in response to external stimuli such as temperature, voltage, or light.
Key performance metrics include:
- Solar absorptance (\u03b1): Measures how much incident solar radiation is absorbed.
- Infrared emittance (\u03b5): Quantifies the efficiency of thermal radiation emission.
The \u03b1/\u03b5 ratio serves as a principal indicator of thermal coating performance. For spacecraft operating in hot environments (e.g., near the Sun), a low \u03b1/\u03b5 ratio is desired to promote radiative cooling. Conversely, a higher ratio helps retain heat in colder zones (e.g., deep space or shadowed orbits).
Magnetron sputtering, a PVD technique, allows precise control over film thickness, composition, and structure, making it ideal for producing high-performance thermal coatings. During this process, ions bombard a solid target, ejecting atoms that travel to the substrate and condense into a thin film. The physical and functional characteristics of the final coating are heavily influenced by the target material’s properties.
3. Categories of Sputtering Target Materials for Thermal Control Coatings
Different space missions impose diverse thermal constraints, demanding tailored materials with distinct optical, thermal, and mechanical properties. Below are core categories of sputtering target materials used in spacecraft thermal control:
3.1. Highly Reflective Metals
These materials minimize solar absorption by reflecting incoming radiation:
- Silver (Ag)
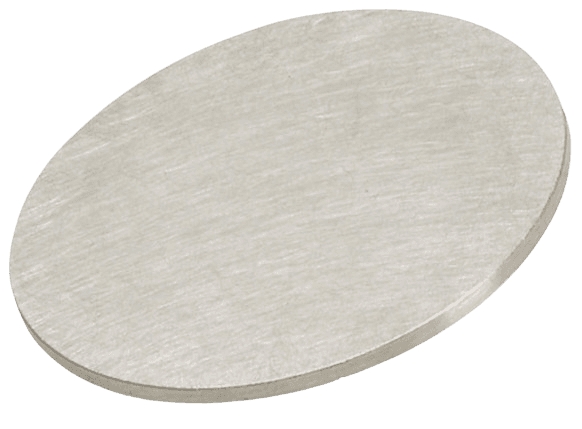
- Role: Backbone of low-emissivity reflective coatings.
- Advantages: Among the most reflective materials across the visible and infrared spectrum. Infrared emissivity as low as 0.02.
- Challenges: Tendency to oxidize; typically requires dielectric overcoats (e.g., SiO2, Al2O3).
- Aluminum (Al)
- Role: Common reflective layer in multilayer mirror and thermal coatings.
- Advantages: Lightweight, cost-effective, easy to sputter, and naturally forms a passivating oxide.
3.2. Transparent Conductive Oxides (TCOs)
These materials provide electrical conductivity while allowing light transmission—ideal for sensor windows and solar panel overlays:
- Indium Tin Oxide (ITO)
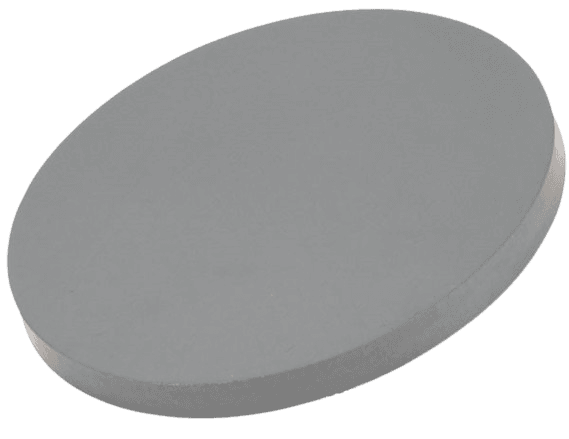
- Advantages: High optical transparency; excellent electrical conductivity; moderate IR emittance.
- Use: Common in solar cell shielding and electrostatic discharge protection.
- Zinc Oxide (ZnO) and Aluminum-doped ZnO (AZO)
- Advantages: Environmental stability; good radiation resistance; non-toxic and Earth-abundant.
- Use: Alternatives to ITO in eco-friendly spacecraft designs.
3.3. Dielectric Materials
Used to tailor spectral response in multilayer stacks or act as protective barriers:
- Silicon Dioxide (SiO2)
- Role: Interference and passivation layer.
- Properties: High optical transparency; thermal and chemical stability.
- Hafnium Dioxide (HfO2)
- Role: High-refractive-index dielectric.
- Properties: Excellent radiation hardness and high-temperature stability.
3.4. Nitrides and Carbides
Combining optical performance with mechanical robustness:
- Titanium Nitride (TiN) and Zirconium Nitride (ZrN)
- Properties: Metallic-like reflectivity, thermal and chemical resistance.
- Application: Often used in harsh orbital environments.
- Silicon Carbide (SiC)
- Use: Substrate or coating for high thermal conductivity and durability.
4. Multilayer Systems and Thermal Optimization Strategies
Modern spacecraft no longer rely on single-material coatings. Instead, they employ multilayer thin-film systems, often incorporating alternating layers of metals and dielectrics to finely tune optical and thermal behavior. These structures offer several key advantages:
- Tailored spectral reflectance: Multilayer stacks can be engineered to reflect or transmit specific wavelengths, optimizing energy balance.
- Enhanced durability: Dielectric top layers protect sensitive metals like Ag from oxidation and ion damage.
- Gradient structures: Layers with graded refractive indices can reduce reflection losses or thermal mismatch stress.
4.1. Typical Multilayer Configurations
A standard high-performance thermal control coating may include the following:
- Base layer: Adhesion promoter (e.g., Cr or Ti).
- Reflective layer: Metal (e.g., Ag or Al).
- Barrier layer: Thin metal or oxide to prevent diffusion.
- Top dielectric stack: Alternating SiO2 and HfO2 for optical tuning and environmental protection.
4.2. Deposition Process Parameters
Deposition parameters during sputtering are finely tuned to achieve layer-specific properties:
- Gas composition (Ar, O2, N2) affects stoichiometry and density.
- Power settings (RF vs DC) influence energy and coating uniformity.
- Substrate temperature controls film crystallinity and stress levels.
4.3. Trade-Offs and Considerations
Designing multilayer systems is a balance of performance and processability:
- More layers provide better spectral control but increase manufacturing complexity.
- Mismatch in thermal expansion can lead to film delamination in orbit.
- Radiation-induced color center formation can degrade coating performance over time.
Well-designed multilayer thermal coatings are critical in missions ranging from low Earth orbit (LEO) to interplanetary exploration. Their continued optimization depends on both materials science and precise control of sputtering conditions.
5. Real-World Case Studies: From Laboratory to Orbit
Understanding the practical applications of sputtering target materials in thermal control coatings requires examining how major aerospace agencies and private companies implement these technologies in real missions. Below are selected examples illustrating both the diversity of sputtering targets and the challenges of their deployment.
5.1. NASA’s OSIRIS-REx Mission and Silver-Based Coatings
NASA’s OSIRIS-REx spacecraft, launched in 2016 to collect samples from asteroid Bennu, operated under extreme thermal conditions—encountering direct solar radiation and cold-space shadowing. The thermal control system relied heavily on multilayer insulation (MLI) blankets with embedded thin-film coatings.
- Materials Used: Silver and aluminum served as reflective layers, deposited via magnetron sputtering onto polyimide substrates.
- Sputtering Advantage: Enabled ultra-smooth, dense reflective films with consistent optical properties across large surface areas.
- Thermal Control Performance: Achieved an α/ε ratio below 0.1 in critical areas, minimizing heat absorption while maximizing radiation.
This mission underscored silver’s unmatched reflectivity and the importance of controlling oxidation through dielectric overlayers like SiO₂.
5.2. ESA’s BepiColombo and High-Temperature Oxide Films
The BepiColombo mission to Mercury, developed by the European Space Agency (ESA), endures some of the highest thermal loads in space exploration. This demanded coating systems that could withstand continuous temperatures above 350°C.
Coating System: HfO₂/SiO₂ multilayers were sputtered onto spacecraft surfaces to provide high reflectivity and thermal resistance.
Hafnium Dioxide Role: Due to its high refractive index and radiation stability, HfO₂ enhanced solar reflectance in the visible and near-IR ranges.
Material Challenge: Sintering of HfO₂ sputtering targets required precise control to maintain phase purity and uniform erosion.
This application demonstrated the value of high-performance dielectrics from advanced ceramic sputtering targets.
5.3. SpaceX Starlink: Thermal Coatings in Mass Production
The SpaceX Starlink constellation—comprising thousands of LEO satellites—illustrates how sputtering target materials scale from bespoke missions to commercial volume production.
- Thermal Control Need: Starlink satellites operate in LEO, where atomic oxygen, UV exposure, and thermal cycling are constant challenges.
- Sputtered Coatings: SpaceX reportedly employs Al-based reflective coatings combined with ZnO or AZO protective layers.
- Key Innovation: Integration of sputtering processes into automated production lines for high throughput, consistency, and minimal coating degradation in orbit.
This case exemplifies the shift from experimental sputtering to industrial-scale coating of thermal films.
5.4. TFM Partnerships and Custom Target Development
As space missions diversify, coating requirements often demand custom sputtering targets. TFM (Target Fabrication & Materials) has played a key role as a supplier and R&D partner:
- Joint Development Projects: TFM collaborates with aerospace firms to co-develop specialized targets, including nanostructured TiN and VO₂.
- Process Innovation: Use of hot isostatic pressing (HIP) and spark plasma sintering (SPS) to create ultra-dense, fine-grained targets for long-term coating stability.
- Quality Assurance: Custom targets undergo optical testing, erosion uniformity studies, and vacuum chamber simulations.
These partnerships highlight how material science and engineering precision converge to meet real-world orbital performance demands.
6. Engineering Standards and Constraints in Selecting Sputtering Target Materials
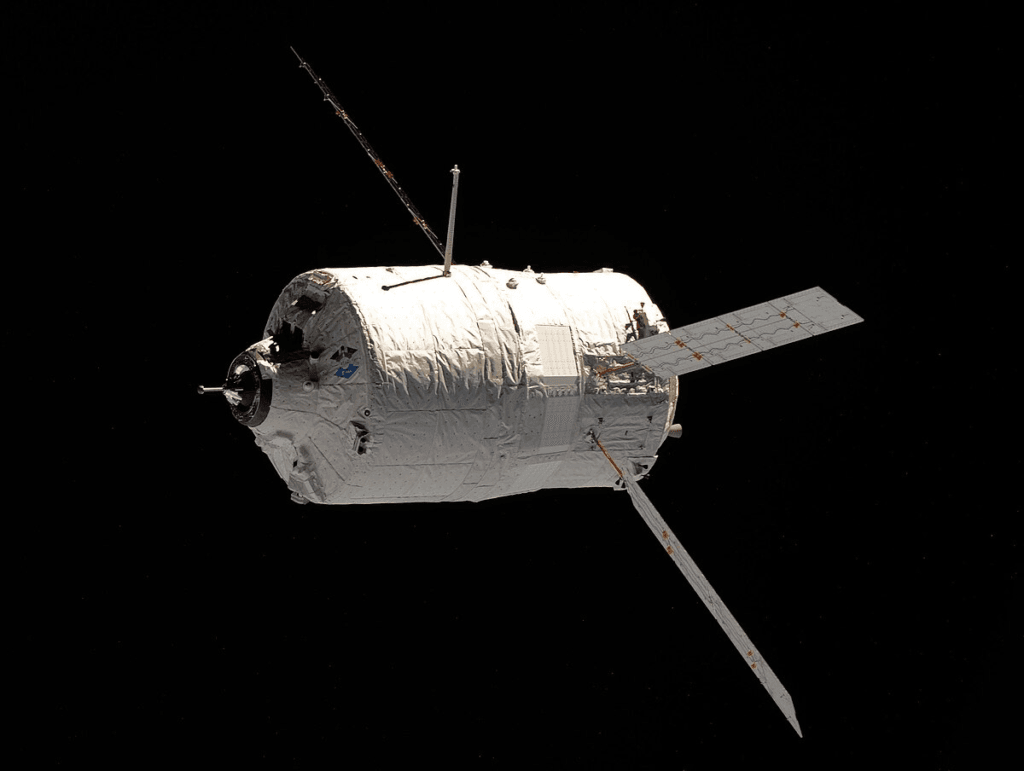
The selection of sputtering target materials for spacecraft thermal control coatings involves a careful balance of multiple engineering criteria. These standards ensure that the materials not only meet the thermal and optical performance requirements but also withstand the extreme conditions of space while remaining compatible with manufacturing processes.
6.1 Selection Criteria: Thermal Performance, Vacuum Compatibility, and Spectral Matching
- Thermal Properties: Targets must enable coatings with specific solar absorptance and infrared emissivity tailored to mission needs. For example, high reflectivity metals like silver offer very low emissivity, critical for heat rejection in hot environments.
- Vacuum Compatibility: Materials must exhibit low outgassing rates and maintain stability under ultra-high vacuum conditions typical in spacecraft environments.
- Spectral Properties: The sputtered film’s optical constants need to align precisely with design models to achieve the intended energy balance, requiring high purity and compositional control of targets.
6.2 Influencing Factors: Purity, Density, Grain Size, and Sintering Method
- Purity: Impurities can alter film optical behavior and increase defect density, causing absorption losses or coating degradation.
- Density: Dense targets promote uniform sputtering rates and reduce micro-arcing, enhancing coating quality.
- Grain Size: Fine-grained microstructures yield smoother films with fewer scattering centers, improving reflectivity and durability.
- Sintering Methods: Techniques like hot isostatic pressing (HIP) and spark plasma sintering (SPS) allow production of dense, homogenous targets with optimized microstructures.
6.3 Manufacturing Challenges: Cracking, Target-Holder Matching, and Arcing
- Cracking and Delamination: Thermal stresses during sputtering can cause cracking in targets, compromising film uniformity and process uptime.
- Target-Holder Fit: Precise mechanical compatibility is necessary to ensure even cooling and minimize target deformation under plasma bombardment.
- Arcing Issues: Defects or impurities can trigger arcing during sputtering, leading to film defects and reduced target lifespan.
6.4 Characterization Techniques: SEM, AFM, XRD, and Spectroscopic Ellipsometry
- Scanning Electron Microscopy (SEM) provides high-resolution imaging of microstructures and fracture surfaces.
- Atomic Force Microscopy (AFM) measures surface roughness and nanoscale texture.
- X-ray Diffraction (XRD) identifies crystal phases and evaluates grain size.
- Spectroscopic Ellipsometry assesses film thickness and optical constants post-deposition, verifying target-to-film correlation.
Meticulous quality control through these methods is essential for the development of sputtering targets meeting the demanding criteria of spacecraft thermal coatings.
7. Emerging Trends and Future Material Innovations
The field of sputtering target materials for spacecraft thermal control coatings is evolving rapidly, driven by new mission profiles, harsh orbital environments, and demands for smarter, multifunctional surfaces. Below are key areas of innovation and future research directions.
7.1 Thermochromic and Electrochromic Targets: VO₂, NbO₂
- VO₂ (Vanadium Dioxide): Exhibits a reversible metal-insulator transition near 68°C, enabling coatings that dynamically change their optical properties in response to temperature. This allows spacecraft surfaces to adaptively modulate solar absorption and infrared emission depending on environmental conditions.
- NbO₂ (Niobium Dioxide): Similar thermochromic behavior with potential advantages in transition temperature tuning and stability.
- Challenges remain in fabricating dense, uniform sputtering targets of these complex oxides and integrating their thin films into multilayer stacks.
7.2 Nanostructured Targets for Superhydrophobic and Self-Cleaning Coatings
- Nanostructured sputtering targets enable thin films with hierarchical surface textures that repel water and dust, critical for maintaining optical clarity and thermal performance in orbit.
- These coatings can reduce contamination buildup and atomic oxygen erosion.
- TFM is exploring nanopowder sintering and controlled grain boundary engineering to produce such targets.
7.3 Atomic Oxygen Resistant Coatings for Low Earth Orbit (LEO)
- LEO spacecraft face constant bombardment by highly reactive atomic oxygen, which erodes conventional polymeric and metallic coatings.
- Composite targets combining Al₂O₃, SiO₂, or novel ceramic phases are under development to create erosion-resistant protective layers.
- Such coatings prolong operational lifetimes and reduce maintenance needs for satellites and space stations.
7.4 TFM’s Role in Green and Sustainable Aerospace Materials
- Increasing focus on environmentally friendly materials drives the search for non-toxic, earth-abundant sputtering targets.
- TFM is actively developing lead-free, indium-free alternatives and recycling programs for used targets.
- These initiatives align with global aerospace sustainability goals and future regulatory requirements.
8. Conclusion: Advancing High-Performance Sputtering Targets for Spacecraft Thermal Control
Sputtering target materials play a pivotal role in the development and deployment of thermal control coatings that safeguard spacecraft from the extreme challenges of space. Their properties directly influence the optical performance, durability, and overall reliability of these coatings, which in turn affect mission success.
The intersection of materials science and aerospace engineering drives continuous innovation—from traditional metals like silver and aluminum to advanced dielectrics, nitrides, and emerging functional oxides. Multilayer thin-film architectures, enabled by precise sputtering processes, offer unprecedented control over spacecraft thermal management.
TFM stands at the forefront of this evolution, leveraging cutting-edge fabrication techniques and rigorous quality control to provide customized, high-purity sputtering targets. By embracing future trends such as adaptive thermochromic materials, nanostructured coatings, and sustainable manufacturing, TFM is positioned to meet the increasingly demanding requirements of modern space missions.
Looking ahead, the key challenges lie in integrating multifunctional properties, enhancing radiation resistance, and scaling production without compromising quality. Through collaboration and innovation, the next generation of sputtering targets will empower spacecraft to operate more efficiently, safely, and sustainably across diverse orbital environments.