Introduction to ASA HV Flanges
ASA HV Flanges, also known as American Standards Association High Vacuum Flanges, are essential components in vacuum technology. These flanges are specifically designed to meet the demands of high vacuum systems, ensuring reliable sealing and compatibility across various applications. Their standardized design and superior sealing capabilities make them indispensable in industries that require precise control of vacuum environments, such as semiconductor manufacturing, optical systems, and scientific research.
History and Standardization
The ASA HV Flanges were developed under the guidelines of the American Standards Association, now known as the American National Standards Institute (ANSI). These standards provide a uniform design framework, ensuring that components from different manufacturers can work seamlessly together. The ASA standardization extends to dimensions, materials, and pressure ratings, offering users confidence in the reliability and compatibility of these components across diverse applications.
The origins of ASA HV Flanges trace back to the growing demand for reliable vacuum sealing solutions in scientific and industrial settings. As vacuum technologies advanced, it became evident that a standardized approach was necessary to streamline the integration of components across systems. ASA played a pivotal role in establishing these standards, focusing on durability, functionality, and ease of use.
Key Features of ASA HV Flanges
ASA HV Flanges offer a variety of features that make them suitable for high and ultra-high vacuum environments. Below are detailed descriptions of their key attributes:
High Vacuum Sealing Capability
ASA HV Flanges are engineered to provide exceptional sealing performance. This is achieved through the use of precise machining and high-quality sealing materials. The sealing mechanisms commonly involve:
- Metal gaskets made from malleable materials like copper or aluminum, which conform to surface irregularities and create an airtight seal.
- Elastomer O-rings crafted from materials such as nitrile or Viton, which are ideal for systems requiring frequent assembly and disassembly.
These sealing solutions ensure minimal leakage rates, even under the demanding conditions of high vacuum environments.
Durable Construction
Manufactured from robust materials such as stainless steel and aluminum, ASA HV Flanges are built to withstand extreme temperatures, mechanical stress, and corrosive environments. Stainless steel, particularly grades like 304 and 316, is a preferred material due to its excellent resistance to oxidation and chemical degradation.
Standardized Design
The standardized dimensions and configurations of ASA HV Flanges simplify integration into vacuum systems. This standardization ensures compatibility with a wide range of components, reducing the need for custom parts and facilitating modular system designs.
Ease of Assembly and Maintenance
ASA HV Flanges are designed with user convenience in mind. The bolted construction allows for straightforward assembly and disassembly, making it easier to conduct system maintenance or modifications. The use of common tools and techniques further enhances their practicality.
Structural Components of ASA HV Flanges
The functionality of ASA HV Flanges relies on several critical components, each contributing to the overall performance of the flange system. Detailed descriptions of these components include:
Flange Body
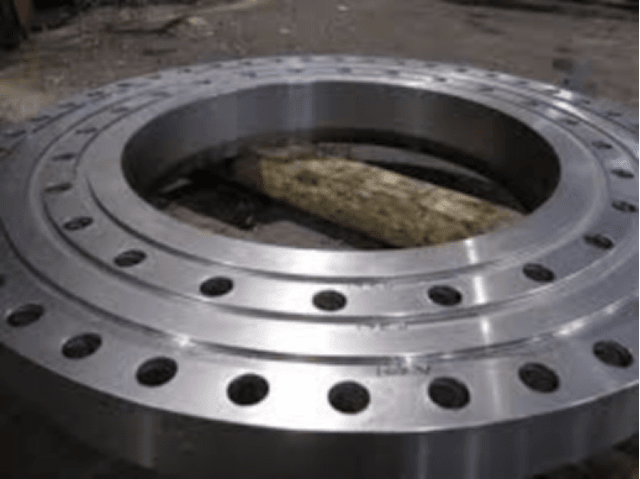
The flange body serves as the primary structural element, providing a flat and smooth sealing surface. The precision machining of this surface is crucial to achieving a reliable seal. Some flange designs incorporate grooves to better retain gaskets, enhancing the sealing performance.
Sealing Gasket
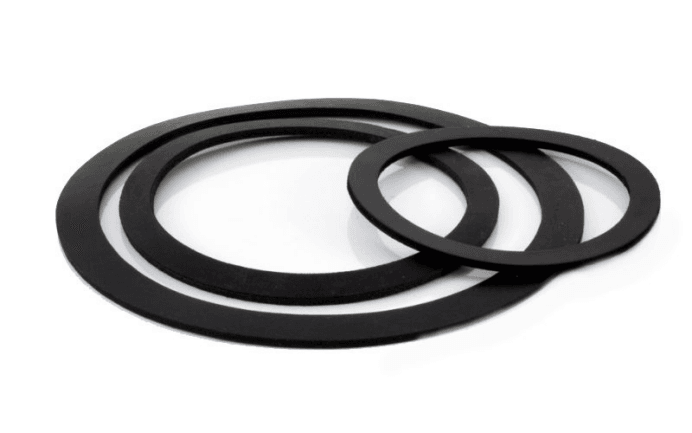
The sealing gasket is a vital component in ensuring vacuum integrity. Two primary types of gaskets are used in ASA HV Flanges:
- Metal gaskets, such as those made from copper, are designed for ultra-high vacuum applications due to their ability to deform and fill microscopic surface imperfections.
- Elastomer gaskets, including materials like nitrile or silicone, are easier to handle and are suitable for less stringent vacuum requirements.
Bolts and Nuts
High-strength bolts and nuts are employed to secure the flange assembly. These fasteners compress the gasket between the mating surfaces, creating a vacuum-tight seal. The bolts are typically arranged in a circular pattern, ensuring even distribution of pressure.
Centering Ring
In certain designs, a centering ring is included to ensure the proper alignment of the gasket and the mating flanges. This alignment is crucial for achieving a consistent and reliable seal.
Materials Used in ASA HV Flanges
The choice of materials significantly impacts the performance and durability of ASA HV Flanges. Common materials include:
Stainless Steel
Stainless steel is the most commonly used material due to its exceptional mechanical properties and corrosion resistance. Grade 304 stainless steel is often used for general-purpose applications, while grade 316 stainless steel provides enhanced resistance to corrosive environments, such as those involving chemicals or saltwater.
Aluminum
Aluminum is a lightweight alternative to stainless steel, offering adequate strength and corrosion resistance for less demanding applications. Its reduced weight makes it suitable for systems where mass is a critical factor.
Copper
Copper is primarily used for gaskets due to its excellent malleability and thermal conductivity. These properties allow copper gaskets to create an effective seal under high pressure.
Elastomers
Elastomeric materials, such as Viton or nitrile, are commonly used for gaskets in systems that require frequent maintenance. Their flexibility and ease of use make them ideal for moderate vacuum applications.
Types of ASA HV Flanges
ASA HV Flanges are available in various configurations to meet the diverse needs of vacuum systems. These include:
Blank Flanges
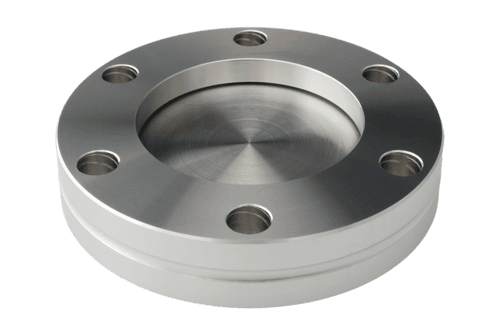
Blank flanges are solid components used to close off unused vacuum ports. They are essential for isolating sections of a system during maintenance or when specific ports are not required.
Through-Hole Flanges
Through-hole flanges are designed with openings to accommodate the passage of pipes, valves, or instrumentation. These flanges are critical for connecting different parts of a vacuum system.
Non-Rotatable Flanges
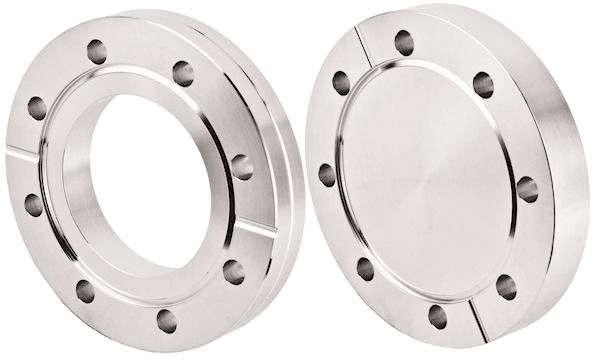
Non-rotatable flanges feature fixed bolt holes, ensuring consistent alignment during installation. This design is particularly useful in applications where precise orientation is necessary.
Rotatable Flanges
Rotatable flanges allow for greater flexibility during installation by enabling bolt holes to be aligned easily with the mating flange. This design simplifies assembly, especially in complex systems.
Applications of ASA HV Flanges
ASA HV Flanges are widely used across various industries. Detailed descriptions of their applications include:
Semiconductor Manufacturing
High vacuum environments are essential in semiconductor fabrication processes such as chemical vapor deposition (CVD), physical vapor deposition (PVD), and etching. ASA HV Flanges ensure the integrity of vacuum chambers, providing reliable sealing for these critical operations.
Optical Coating Systems
In the production of optical devices, thin films are deposited onto lenses and mirrors under high vacuum conditions. ASA HV Flanges are used to construct the vacuum chambers necessary for these processes, ensuring consistent performance.
Scientific Research
Research facilities, such as those involved in high-energy physics or material science, rely on ultra-high vacuum conditions for experiments. ASA HV Flanges play a key role in maintaining these environments, supporting sensitive instruments and experimental setups.
Aerospace Testing
In the aerospace industry, vacuum testing simulates the conditions of outer space to evaluate the performance of components like satellites. ASA HV Flanges are used to create the high vacuum environments required for these tests.
Nuclear Fusion
Vacuum systems used in nuclear fusion research depend on ASA HV Flanges to contain high vacuum environments. These flanges are critical for maintaining the conditions necessary for plasma confinement.
Installation and Maintenance of ASA HV Flanges
Proper installation and maintenance are crucial for ensuring the performance and longevity of ASA HV Flanges. Detailed steps include:
Preparation
- Clean all flange surfaces and gaskets thoroughly to remove contaminants such as dust, grease, or particles.
- Inspect components for scratches, dents, or other defects that could compromise the seal.
Assembly
- Position the gasket carefully between the mating flanges, ensuring proper alignment.
- Insert bolts into the bolt holes, tightening them gradually in a cross-pattern to ensure even pressure distribution.
Leak Testing
After assembly, conduct leak testing to verify the integrity of the vacuum seal. Common methods include helium leak testing or pressure decay testing.
Maintenance
- Regularly inspect gaskets and replace them if signs of wear or damage are observed.
- Check bolt torque periodically to maintain consistent sealing pressure.
- Clean flange surfaces during routine maintenance to prevent contamination.
Advantages of ASA HV Flanges
ASA HV Flanges offer numerous benefits, including:
- Reliable sealing performance for high and ultra-high vacuum environments.
- Standardized dimensions and designs that ensure compatibility across systems.
- Robust construction that withstands harsh conditions and prolonged use.
- Ease of assembly and maintenance, reducing downtime and operational costs.
Challenges and Limitations
Despite their advantages, ASA HV Flanges have certain limitations, such as:
- The weight of stainless steel flanges can add to the overall system mass.
- High-quality materials and manufacturing processes make these flanges relatively expensive.
- Sensitive sealing surfaces require careful handling to prevent damage.
Future Developments
Ongoing advancements in materials science and manufacturing technology are expected to enhance the performance of ASA HV Flanges. Potential developments include:
- The use of advanced composite materials to reduce weight while maintaining strength.
- Improved surface coatings for enhanced resistance to corrosion and wear.
- Innovations in gasket design to simplify installation and improve sealing efficiency.
Conclusion
ASA HV Flanges are critical components in high vacuum technology, offering reliable and standardized solutions for creating and maintaining vacuum environments. Their robust design, material versatility, and ease of integration make them indispensable across industries such as semiconductor manufacturing, scientific research, and aerospace. As technology continues to evolve, ASA HV Flanges are poised to deliver even greater performance and reliability, meeting the demands of future vacuum applications.