In industries where precision and performance define success—like semiconductors, optical coatings, and solar cells—the use of precious metals in thin film deposition is both essential and costly. These high-value materials, prized for their conductivity, durability, and resistance to corrosion, are the backbone of cutting-edge technologies. Yet, the rising costs of raw materials, coupled with the need for stringent quality control, leave manufacturers, distributors, and exporters searching for innovative ways to balance performance with affordability. Reducing the cost of depositing precious metals isn’t just a financial imperative; it’s a strategic advantage that drives competitiveness in a global market. This guide will unveil proven strategies to optimize processes, manage expenses, and ensure the highest standards of quality.
Understanding the Cost Drivers in Precious Metal Deposition
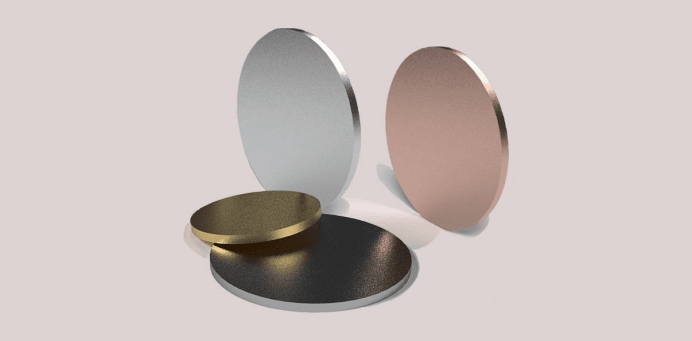
Precious metals like gold, platinum, and palladium are invaluable for thin film deposition, PVD processes, and other high-tech applications due to their exceptional properties, including conductivity, corrosion resistance, and durability. However, their high market value and the complexities of handling them in vacuum coating materials make cost management essential.
Several factors influence the overall expense of depositing precious metals:
- Raw Material Costs: High-purity metals and alloys come with a premium price.
- Process Efficiency: Inefficient deposition techniques lead to material waste.
- Equipment Maintenance: Regular upkeep is crucial for precision but adds to operational costs.
- Production Scale: Small-scale production often results in higher costs per unit.
- Global Market Volatility: Fluctuating metal prices impact budget stability.
Strategies for Reducing Costs in Precious Metal Deposition
Reducing the cost of precious metal deposition requires a multifaceted approach that combines material efficiency, advanced techniques, and thoughtful resource management. Here are some innovative strategies to achieve cost savings without sacrificing quality:
Utilizing Thinner Sputtering Targets
For applications requiring only a thin film of precious metal, using thinner sputtering targets can lead to significant cost reductions. Thin foils are often sufficient to achieve the desired coating, eliminating the need for oversized targets and minimizing material waste. By carefully matching the target thickness to the film requirements, manufacturers can achieve both cost and resource efficiency.
Reclaiming Spent Materials
One of the most effective ways to manage costs is by reclaiming spent precious metals. After deposition, any remaining material can be collected and sent for reclamation, where it is refined and credited towards future purchases. Many suppliers, including global manufacturers, offer reclamation services for a wide range of materials. This approach not only saves money but also supports sustainable practices by reusing high-value resources.
Capturing Overspray with UHV Grade Aluminum Foil
Lining the chamber walls with ultra-high vacuum (UHV) grade aluminum foil is a practical solution to capture overspray during deposition. Precious metal particles that do not settle on the substrate are collected on the foil, which can then be removed and reclaimed. Even in chambers where non-precious metals are deposited alongside precious metals, this method ensures minimal waste. Additionally, shields and liners can be periodically cleaned and refined to recover valuable material, further optimizing resource usage.
Employing Thicker-Walled E-Beam Crucible Liners
Electron beam evaporation (E-beam) often requires loading more material than needed to maintain a fill rate above 30%, which can result in waste. By using crucibles with thicker walls, the effective volume of the crucible is reduced, allowing for smaller material loads. Although recalibration of the beam pattern is necessary when wall thickness changes, this approach ensures that material use is more closely aligned with film requirements. Any residual material left in the crucible after deposition can also be reclaimed, further reducing waste.
Optimizing Thermal Evaporation Sources and Loads
Selecting the appropriate thermal evaporation source is critical when working with expensive materials like precious metals. For example, gold tends to alloy with refractory metals, so using an alumina-coated source can act as a barrier, preventing unwanted reactions between the molten metal and the tungsten boat. Similarly, reviewing the optimal temperatures for deposition is essential; for instance, platinum’s high melting point often makes thermal evaporation impractical. Precise loading of materials, with an additional 20% buffer to ensure completion, minimizes the leftover metal and enhances cost efficiency.
By adopting these strategies, businesses can reduce expenses associated with thin film deposition while maintaining the high standards of precision and quality demanded in industries such as semiconductors, optical coatings, and solar cells.
Real-World Applications of Cost-Effective Deposition
Cost-effective precious metal deposition is essential across various industries, including:
- Semiconductor Industry: High-purity materials are critical for microelectronics and thin film deposition, making process optimization essential.
- Optical Coatings: Durability and precision are key, requiring reliable vacuum coating materials.
- Solar Cells: Competitive pricing and efficient processes ensure cost-effective production.
- Research and Development: On-demand production and customization allow for tailored solutions.
These industries benefit greatly from collaborating with a trusted supplier offering precision-engineered solutions, technical support, and global shipping.
Conclusion
Reducing the cost of depositing precious metals involves a multifaceted approach, from optimizing material usage and improving processes to partnering with reliable suppliers and exploring recycling options. By focusing on quality control, leveraging advanced technology, and streamlining supply chains, businesses can achieve significant cost savings without compromising on the performance or durability of their thin film materials.
Manufacturers, distributors, and exporters in the deposition materials market must prioritize collaboration and innovation to meet the growing demands of the semiconductor industry, optical coatings, solar cells, and beyond. With the right strategies, companies can strike a balance between cost efficiency and exceptional quality, ensuring long-term success in a competitive global market.
For more information on high-purity metals, sputtering targets, and evaporation materials, connect with a trusted supplier today to explore customization, bulk orders, and on-demand production tailored to your needs.