Molybdenum, a chemical element with the symbol Mo and atomic number 42, is a crucial material in the manufacturing industry due to its strength, high melting point, and resistance to corrosion. Among the many forms in which molybdenum can be used, molybdenum tubes are particularly significant. These tubes have a wide range of applications in various industries, from aerospace and electronics to energy and metallurgy. This article explores the various uses of molybdenum tubes, highlighting their importance in modern technology and industrial processes.
Molybdenum tubes are produced by extruding or drawing the metal into cylindrical forms. These tubes are typically used in high-temperature environments where strength and resistance to wear and tear are essential. Their ability to withstand extreme conditions without losing their structural integrity makes them indispensable in many fields, particularly where heat and corrosion resistance are paramount. The metal itself, with a melting point of 2,623 degrees Celsius (4,753 degrees Fahrenheit), offers exceptional durability in high-temperature environments.
Applications in High-Temperature Furnaces and Heating Elements
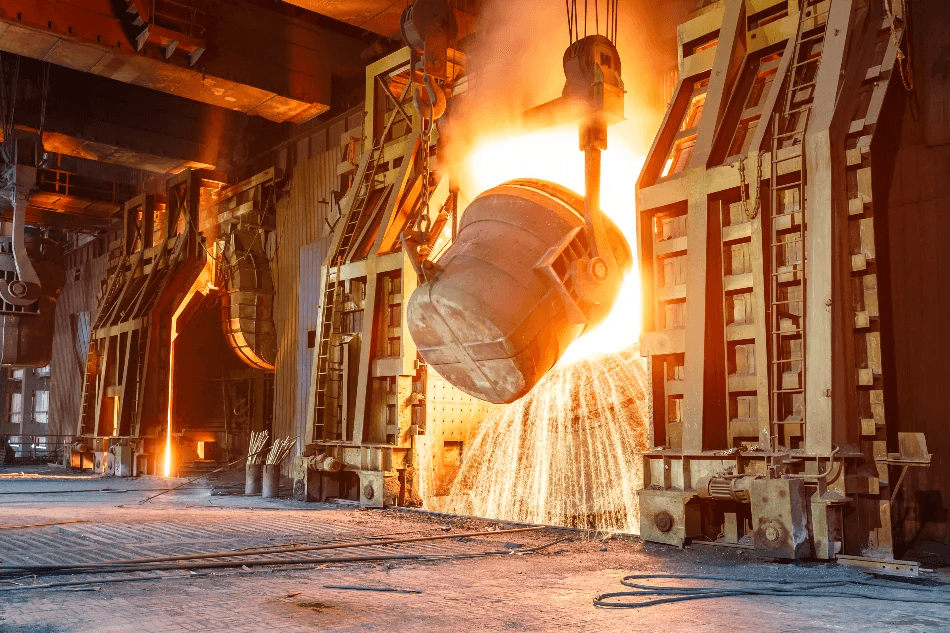
One of the primary uses of molybdenum tubes is in high-temperature furnaces and heating elements. Molybdenum is used extensively in applications that require materials to maintain their structural properties even when exposed to very high temperatures. In industries such as semiconductor manufacturing, metalworking, and materials processing, furnaces that operate at extreme temperatures require components made from materials like molybdenum due to its ability to withstand high heat without warping or degrading. Molybdenum tubes are often employed as heating elements or parts of the furnace’s structure, providing both durability and reliability.
The high melting point and thermal conductivity of molybdenum make it an ideal material for these applications. Its use in these environments ensures that the furnaces can operate efficiently without the need for frequent repairs or replacements. Molybdenum tubes can be used to create various components within the furnace, such as electrode rods, heating elements, and heat shields. These parts can function effectively at temperatures that would damage other materials.
Aerospace and Defense Applications
In the aerospace industry, molybdenum tubes are employed in various components, such as rocket nozzles, heat shields, and structural elements of spacecraft. The aerospace sector demands materials that can withstand the intense heat and stress associated with space travel, and molybdenum’s high melting point makes it an ideal choice for these applications. Molybdenum tubes are also used in high-speed aircraft engines, where their resistance to heat and thermal expansion is crucial for maintaining performance under extreme conditions.
The use of molybdenum tubes in aerospace applications goes beyond merely withstanding high temperatures. These tubes are also used for their ability to handle rapid temperature changes. In the harsh conditions of space, or during high-speed reentry into the Earth’s atmosphere, materials are subjected to drastic thermal cycling. Molybdenum’s low coefficient of thermal expansion helps to prevent deformation or failure under such stress, making it essential for the long-term durability of components in these applications.
Electronics and Semiconductor Industry
Molybdenum tubes play a significant role in the electronics and semiconductor industries. Molybdenum is used to produce thin films and components for various electronic devices. Its high electrical conductivity and resistance to corrosion make it a reliable material for electronic components that operate in harsh environments. Molybdenum tubes are used in the manufacturing of vacuum tubes, cathodes, and other high-performance components.
In semiconductor manufacturing, molybdenum is commonly used as a base material for certain types of thin-film deposition processes, including chemical vapor deposition (CVD) and physical vapor deposition (PVD). Molybdenum tubes are often used to house the substrates or as part of the equipment that produces thin films, as they provide excellent resistance to corrosion and can maintain their structural integrity at high temperatures.
The semiconductor industry is constantly innovating, with devices becoming smaller and more complex. As such, the demand for materials that can maintain stability and performance in increasingly compact and powerful systems is growing. Molybdenum tubes, with their unique properties, are essential in supporting this technological advancement.
Energy and Nuclear Industry
Molybdenum tubes also have crucial applications in the energy and nuclear industries. In nuclear reactors, molybdenum tubes are used as fuel cladding materials. The cladding serves as a protective layer around the nuclear fuel, ensuring that radioactive materials are contained and preventing any interaction between the fuel and the coolant. Molybdenum’s excellent thermal conductivity and resistance to neutron irradiation make it an ideal material for these applications.
The energy sector also utilizes molybdenum tubes in other applications such as heat exchangers, where the material’s ability to transfer heat efficiently is vital. In the nuclear industry, the tubes’ resistance to radiation damage and their ability to maintain strength under high heat and pressure conditions make them indispensable.
In the oil and gas industry, molybdenum tubes are used in the production of equipment for deep drilling and other high-pressure applications. The ability of molybdenum to resist corrosion from sulfur compounds and other harsh chemicals present in oil and gas fields ensures that the equipment lasts longer and requires less maintenance.
Metallurgy and Alloy Production
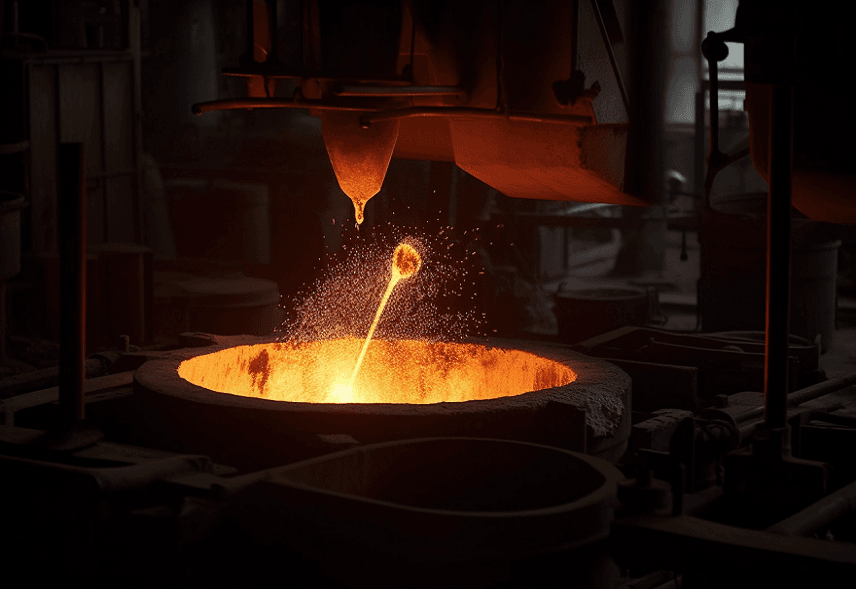
Molybdenum tubes are frequently employed in the production of specialized alloys. Molybdenum is often used as an alloying agent to produce stronger, more heat-resistant metals. It is commonly alloyed with steel, for example, to improve its hardness, toughness, and resistance to corrosion. Molybdenum tubes are often used in the creation of these alloys, both as a direct component and as part of the equipment used in alloy production.
In the metallurgy industry, molybdenum’s ability to enhance the properties of other metals makes it a critical element in creating materials that can be used in demanding environments. These alloys are employed in various sectors, including the automotive industry, where the need for strong, durable materials is paramount, and in the construction of machinery and equipment that must withstand extreme mechanical stress.
The use of molybdenum tubes in alloy production is not limited to just steel. Molybdenum is also used in producing other specialized alloys used in the aerospace, electronics, and nuclear industries, among others. These alloys benefit from molybdenum’s ability to improve their mechanical properties and resistance to high temperatures and corrosion.
Medical Applications
Molybdenum tubes have been used in the medical industry, especially in the production of specialized equipment used in diagnostic and therapeutic applications. Molybdenum is sometimes used in the construction of medical imaging devices, such as X-ray tubes and other radiation equipment. Molybdenum’s ability to withstand high levels of radiation and heat makes it ideal for these applications, where maintaining the integrity of the equipment is crucial.
Additionally, molybdenum is used in the manufacturing of some medical instruments, where its strength and resistance to wear make it valuable. While not as widely used as other materials like stainless steel, molybdenum still plays an important role in specific medical technologies that require its unique properties.
Molybdenum Tubes in Scientific Research
In scientific research, molybdenum tubes are sometimes used in experimental setups, particularly in high-temperature and high-pressure environments. Their resistance to corrosion and ability to withstand extreme conditions make them a good choice for applications where other materials would fail. Molybdenum tubes are often used in laboratory experiments that involve high temperatures, such as in furnaces or other equipment used for materials processing.
Molybdenum’s stability and durability under harsh conditions make it ideal for a wide range of scientific research applications. Whether in the development of new materials, the study of high-temperature phenomena, or other fields, molybdenum tubes provide a reliable and long-lasting solution to the challenges posed by extreme environments.
Conclusion
Molybdenum tubes are indispensable in many industries due to their unique combination of strength, heat resistance, and corrosion resistance. From their use in high-temperature furnaces and aerospace components to their application in the semiconductor, nuclear, and medical industries, molybdenum tubes play a critical role in modern technology. Their ability to withstand extreme conditions without degrading makes them an essential material in fields where performance, durability, and reliability are crucial.
As industries continue to push the boundaries of technology, the demand for advanced materials like molybdenum will only grow. Molybdenum tubes, with their unique properties, will continue to serve as an important component in a wide range of applications, ensuring the success of innovations across various sectors.