Sputtering targets are vital in thin-film deposition processes, but they can sometimes fail prematurely, causing delays and added costs. These failures can often be traced back to specific causes related to material properties, operating conditions, or equipment issues. A detailed understanding of these factors is essential to prevent such failures and improve sputtering outcomes.
This article explores the reasons sputtering targets break, using examples of cerium oxide, indium tin oxide, and aluminum-doped zinc oxide targets. It also provides actionable insights into preventing these issues.
Common Causes of Sputtering Target Failure
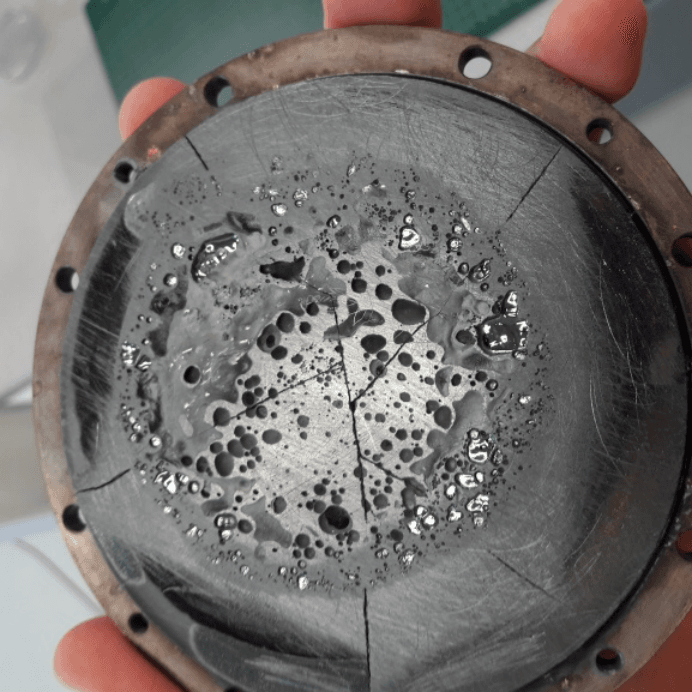
A common reason for sputtering target breakage is exceeding the material’s power limits. Each material has a maximum power density it can handle safely. Applying power beyond this threshold leads to overheating and damage. For instance, an indium tin oxide target with a diameter of 3 inches was sputtered at 1000 watts, roughly seven times its recommended maximum power. This excessive power caused catastrophic failure.
To avoid similar issues, refer to material-specific recommendations for power limits. TFM offers detailed guidance for common sputtering materials at www.thinfilmmaterials.com.
Another factor that contributes to target failure is the improper ramping of power. Sudden application of full power can cause thermal shock, especially in ceramics or low-melting-point materials. These materials often require a gradual increase in power to avoid stress fractures. In one case, a cerium oxide target bonded to a copper backing plate failed when the indium bond melted due to excessive power, causing the target to crack. A gradual ramping process minimizes temperature gradients, reducing the risk of damage.
Bonding issues also play a significant role in sputtering target failure. Proper bonding to a backing plate enhances heat dissipation, stabilizes thin or fragile targets, and allows sputtering to continue even if minor cracks develop. However, bonded targets are limited in their power capacity, typically handling about 20 watts per square inch. Improper bonding can lead to overheating, as demonstrated with the cerium oxide target where the indium bond melted under excessive heat. Ensuring proper bonding and adhering to power limitations is essential to prolong target life.
Inadequate cooling is another critical factor that contributes to target failure. Effective cooling prevents localized overheating, which can cause cracks or fractures in the material. For example, an aluminum-doped zinc oxide target experienced localized overheating due to insufficient cooling at one position and excessive power application. This resulted in cracking. Verifying the cooling system’s functionality and ensuring good thermal contact between the target and the cooling assembly can prevent such issues.
Material-Specific Challenges
Certain materials have unique challenges that make them more prone to failure. Low-melting-point materials, for example, can melt during sputtering if power levels are not carefully managed. In such cases, sputtering is only feasible at very low power settings, often requiring the target to be bonded to a backing plate for added stability and heat dissipation. However, in extreme situations, sputtering may not be viable for these materials.
Ceramic materials are also particularly susceptible to damage. Their brittleness makes them vulnerable to thermal stress, emphasizing the importance of gradual power ramping and consistent cooling. Without these precautions, ceramic targets are likely to crack or shatter during operation.
Oxide targets, such as indium tin oxide and aluminum-doped zinc oxide, present their own challenges. These materials require precise cooling and strict adherence to power limits. Bonding these targets can significantly enhance their performance and longevity, but only when bonding is performed correctly.
Equipment and Setup Troubleshooting
Even when all operational parameters seem correct, equipment issues can contribute to sputtering target failure. The cathode’s surface must be flat to ensure good thermal contact between the target and the cooling assembly. An uneven cathode surface reduces cooling efficiency, increasing the risk of overheating and failure.
Cooling water systems are another common source of problems. Before sputtering begins, it is crucial to confirm that the cooling water is turned on and functioning effectively. Poor cooling performance often results in localized overheating, which can lead to cracking or melting of the target material.
Best Practices to Extend Target Life
Applying the recommended power density for the target material is one of the most effective ways to prevent breakage. Exceeding this limit often leads to overheating and damage. Gradually increasing power during startup is another critical practice, as it prevents thermal shock and reduces stress on the material.
Bonding the sputtering target to a backing plate can enhance heat dissipation and provide additional stability. However, it is important to remember that bonded targets have lower power limits, and exceeding these limits can cause overheating and failure.
Maintaining a consistent and efficient cooling system is also essential. Ensure that the target is in good thermal contact with the cooling assembly and that the cooling water system is functioning optimally. Periodic checks of the sputtering gun and cathode surface can help identify and resolve potential issues before they lead to failure.
Conclusion
Sputtering targets are consumables, but their lifespan can be significantly extended by following best practices and understanding the unique requirements of each material. Exceeding power limits, neglecting proper bonding, and failing to maintain effective cooling are among the most common reasons for sputtering target breakage.
By addressing these issues proactively, you can reduce the likelihood of target failure and improve the efficiency of your sputtering process.