Introduction
High-temperature processes are ubiquitous in industries ranging from metallurgy and semiconductor manufacturing to advanced ceramics and chemical processing. One of the unsung heroes in these extreme environments is the alumina boat—a ceramic container crafted from high-purity aluminum oxide (Al₂O₃) that reliably endures harsh thermal, chemical, and mechanical conditions. Alumina boats serve as critical components in furnaces, melting chambers, and high-temperature reaction vessels due to their exceptional thermal stability, inertness, and resistance to corrosion. This article explores the versatility of alumina boats in high-temperature applications, examines their properties, design considerations, and manufacturing processes, and evaluates their performance relative to alternative materials.
The Science of Alumina: Properties and Advantages
Fundamental Characteristics of Alumina
Aluminum oxide, more commonly known as alumina, is one of the most important technical ceramics available today. Its popularity is derived from several key properties:
- High Melting Point and Thermal Stability: Alumina can maintain its structural integrity at temperatures exceeding 1600°C and even approach 1800°C under certain conditions. This makes it an ideal candidate for applications involving extreme heat. Its stability under both oxidizing and reducing atmospheres enables its use in diverse furnace environments.
- Excellent Chemical Inertness: Due to its high chemical purity and resistance to chemical attack, alumina does not react with molten metals or corrosive chemicals. This ensures that samples processed within alumina boats remain uncontaminated and that the container does not degrade over time.
- Mechanical Strength and Wear Resistance: Alumina is a hard material, almost rivaling diamond in terms of hardness, yet it is considerably lighter than most metals. Its wear resistance makes it suitable for repeated thermal cycling and exposure to aggressive conditions.
- Low Thermal Expansion and High Thermal Shock Resistance: Alumina’s low coefficient of thermal expansion allows it to withstand rapid changes in temperature without cracking. This is essential in high-temperature applications where thermal gradients are common.
- Electrical Insulation: With strong dielectric properties, alumina provides excellent electrical insulation even at elevated temperatures, which is a valuable feature in many electronic and semiconductor processes.
Advantages for High-Temperature Applications
The combination of these properties means that alumina is not only robust but also versatile. In high-temperature environments where many metals would melt or oxidize, alumina remains stable, maintaining both physical integrity and chemical inertness. This reliability translates into fewer interruptions during processing, higher reproducibility in scientific experiments, and lower maintenance costs in industrial settings. Its inherent non-reactivity prevents sample contamination—a crucial factor in analytical laboratories and manufacturing facilities that require high purity standards.
Understanding Alumina Boats
Definition and Design
Alumina boats are specialized crucibles or containers made from high-purity alumina ceramics. They come in various shapes—boat-shaped, flat-bottomed, rectangular, or custom-designed forms—to suit specific applications. The design of an alumina boat is driven by the need to maximize heat distribution, minimize thermal gradients, and facilitate easy handling and cleaning.
- Boat Shape: The typical “boat” shape is designed to provide a large surface area while allowing for a controlled and uniform exposure to the heat source. This shape is particularly beneficial when melting metals, sintering ceramics, or conducting chemical reactions that require uniform temperature distribution.
- Flat-Bottomed Designs: Flat-bottom boats are common in applications that demand stability during processing. The flat base ensures even contact with the furnace or heating element, reducing the risk of hot spots and uneven temperature distribution.
- Customization: Depending on the specific high-temperature process, alumina boats can be produced in a variety of sizes and capacities. Custom designs may include features such as perforations or holes to facilitate gas flow, lids to control oxidation, or special coatings to further improve thermal performance.
Manufacturing Considerations
The fabrication of alumina boats involves advanced ceramic processing techniques. Starting with high-purity alumina powders (often greater than 99%), manufacturers use methods such as slip casting, pressing, and high-temperature sintering to produce a dense, uniform ceramic material. Key manufacturing steps include:
- Powder Preparation: High-purity alumina powders are carefully milled and sieved to achieve a consistent particle size. The quality of the powder directly affects the final mechanical and thermal properties of the sintered boat.
- Shaping and Forming: The powder is then mixed with binders and cast into the desired shape using molds. Techniques such as slip casting allow for intricate shapes with precise dimensions.
- Sintering: The cast alumina is sintered at temperatures approaching 1600–1800°C. This high-temperature process densifies the material, reducing porosity and improving mechanical strength. Modern firing techniques enable manufacturers to keep closed porosity below 0.5%, ensuring that the final product is both robust and chemically inert .
- Quality Control: Post-sintering, alumina boats undergo rigorous inspection for defects such as cracks, irregularities, or inconsistent dimensions. Quality testing includes thermal shock testing and mechanical stress tests to ensure that the boats can withstand the demanding conditions of high-temperature applications.
Applications in High-Temperature Environments
Alumina boats are employed in a wide range of high-temperature applications. Their versatility allows them to be used in both laboratory research and industrial production processes. Some of the key applications include:
Metallurgy and Metal Casting
In metallurgical processes, alumina boats are frequently used as crucibles for melting metals and alloys. They are particularly valued in the production of stainless steel, nickel alloys, and specialty ferromagnetic materials. During metal casting, the alumina boat provides a chemically inert environment, preventing contamination from the container itself. Its high thermal stability ensures that the molten metal is evenly heated and maintained at the required temperatures until casting is complete. The reliability of alumina boats in these processes translates into improved quality of the final metal product and increased safety during high-temperature operations.
Ceramic Sintering and Advanced Ceramics Processing
Ceramic processing often involves sintering—a high-temperature process that fuses powdered materials into a solid mass. Alumina boats are ideal for sintering applications because they offer uniform heat distribution and can withstand the high temperatures required for densification. In the production of advanced ceramics, where precision and purity are paramount, alumina boats help maintain an uncontaminated environment. This results in ceramics with superior mechanical properties and resistance to thermal shock.
Semiconductor Manufacturing and Electronic Applications
The semiconductor industry requires materials that can tolerate rapid thermal cycling and extreme processing conditions. Alumina boats are used in processes such as chemical vapor deposition (CVD), physical vapor deposition (PVD), and annealing treatments in semiconductor fabrication. Their excellent electrical insulation properties and chemical inertness make them particularly useful as sample holders and processing containers in vacuum furnaces. In these applications, maintaining purity is critical, and alumina boats provide a stable, contamination-free environment that is essential for producing high-quality semiconductor devices.
Glass Melting and Optical Materials
Glass production and the manufacturing of optical materials require precise temperature control and a container that does not impart impurities into the molten glass. Alumina boats, with their high purity and inertness, serve as excellent crucibles for melting glass. Their uniform thermal conductivity helps prevent localized overheating, ensuring that the glass melt remains homogeneous. This is vital for producing optical components with the desired clarity and refractive properties.
Chemical Analysis and Laboratory Research
In laboratory settings, alumina boats are often used in thermal analysis and chemical reactions that require extreme heat. Analytical techniques such as thermogravimetric analysis (TGA) and differential scanning calorimetry (DSC) frequently use alumina boats to hold samples during testing. The inert nature of alumina ensures that the samples are not contaminated by the container, and its ability to withstand rapid temperature changes allows for precise measurements during thermal cycling. This makes alumina boats indispensable tools in research laboratories where accuracy and repeatability are essential.
Aerospace and Automotive Industries
High-performance aerospace and automotive components are often subjected to extreme temperatures and harsh environments. Alumina boats are used in the fabrication of components such as turbine blades, exhaust systems, and heat shields. In aerospace applications, the ability of alumina to resist thermal shock and chemical corrosion is critical for ensuring the safety and durability of engine components. Similarly, in automotive manufacturing, alumina boats support the processing of high-temperature alloys and composite materials that require precise control over the heating environment.
Performance Under Extreme Conditions
Thermal Shock and Temperature Cycling
One of the most significant challenges in high-temperature applications is thermal shock—sudden temperature changes that can cause materials to crack or fail. Alumina boats are designed with low thermal expansion coefficients, which help them accommodate rapid changes in temperature without developing internal stresses. Furthermore, their dense, sintered structure minimizes porosity, reducing the likelihood of crack initiation. Controlled heating rates (often between 150°C to 300°C per hour for the initial phase) are recommended to further mitigate thermal shock risk, ensuring that the alumina boat maintains its structural integrity even under aggressive thermal cycling.
Chemical Resistance and Inertness
In many high-temperature processes, the container is exposed to reactive chemicals, molten metals, or corrosive gases. Alumina’s excellent chemical resistance is derived from its high purity and the absence of glassy phases that could otherwise promote corrosion. This inertness is particularly important in processes such as metal melting, where contamination from the container could compromise the quality of the alloy. In chemical analysis and glass production, the purity of alumina boats ensures that the samples or melts are not affected by impurities, resulting in more accurate and consistent outcomes.
Mechanical Strength and Durability
Despite the extreme conditions to which they are exposed, alumina boats are remarkably durable. Their high hardness and wear resistance enable them to withstand repeated use in industrial processes without significant degradation. Even when subjected to high pressures from molten materials or mechanical stresses during handling, alumina boats retain their shape and functionality. This durability not only enhances safety by reducing the risk of catastrophic failure but also offers a cost-effective solution over the long term by minimizing the frequency of replacements.
Comparing Alumina Boats with Alternative Materials
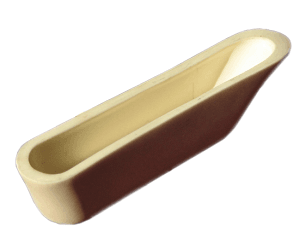
Graphite Crucibles
Graphite is another popular material for high-temperature crucibles, especially in processes involving non-oxidizing atmospheres. Graphite has excellent thermal conductivity and can handle very high temperatures. However, it is chemically reactive in oxidizing atmospheres, and its performance degrades when exposed to air at high temperatures. In contrast, alumina boats are chemically inert and perform consistently under both oxidizing and reducing conditions. While graphite may be preferred in certain specific applications, alumina boats offer a broader range of compatibility and durability.
Zirconia and Zirconia-Toughened Alumina (ZTA)
Zirconia and its composites, such as zirconia-toughened alumina (ZTA), are known for their superior toughness and high resistance to thermal shock. ZTA incorporates zirconia grains into the alumina matrix to improve fracture toughness through a process known as transformation toughening. Although ZTA can provide enhanced mechanical properties compared to pure alumina, it is generally more expensive and may be tailored for niche applications. For many standard high-temperature processes, pure alumina boats offer the optimal balance between performance and cost-effectiveness (
Silicon Carbide
Silicon carbide (SiC) is another advanced ceramic used for high-temperature applications. It boasts extremely high thermal conductivity and exceptional mechanical strength. However, silicon carbide can be more brittle and difficult to machine into complex shapes compared to alumina. Moreover, while SiC offers excellent performance, its cost and fabrication complexity often make alumina a more attractive choice for many industrial applications where slightly lower performance is acceptable in exchange for greater ease of manufacture and lower cost.
Design Considerations for Alumina Boats
Geometry and Dimensional Precision
The design of an alumina boat must account for the specific thermal and chemical environment in which it will be used. Dimensional precision is critical; even slight deviations can lead to uneven heating or stress concentrations. Manufacturers use advanced ceramic processing techniques to achieve tight tolerances. Customization options, such as variations in wall thickness, shape, and the inclusion of features like lids or perforations, allow the final product to be optimized for its intended application. For instance, flat-bottomed designs are particularly effective in providing stable contact with heating elements, while perforated designs may improve gas flow and reaction kinetics in chemical processing applications.
Surface Finishing and Porosity
The surface finish of an alumina boat affects its cleaning, handling, and thermal performance. A smooth, non-porous surface minimizes the risk of contamination and facilitates easy cleaning. Modern sintering techniques and post-processing treatments are employed to reduce surface roughness and closed porosity. This is essential in analytical applications where even minimal contamination can lead to erroneous results. In high-production environments, the ease of cleaning translates directly into reduced downtime and lower maintenance costs.
Integration with Furnace Systems
Alumina boats are designed to be used in a variety of furnace types—from laboratory muffle furnaces and vacuum furnaces to large-scale industrial melting furnaces. Their compatibility with these systems depends on factors such as thermal expansion matching, electrical insulation properties, and physical durability under repeated thermal cycles. In many cases, alumina boats are paired with custom-designed furnace furniture that ensures optimal heat transfer and minimizes thermal gradients. This integration is key to achieving the precise thermal conditions required for processes such as metal alloying, sintering, or chemical reactions.
Future Trends and Innovations
Advances in Alumina Processing and Composite Materials
Recent research in ceramic engineering has focused on improving the properties of alumina through the development of composite materials and advanced processing techniques. One such innovation is the incorporation of small amounts of magnesium oxide (MgO) during sintering. MgO additions help control grain growth and further reduce porosity, resulting in alumina with even higher mechanical strength and thermal shock resistance. Additionally, the advent of zirconia-toughened alumina (ZTA) represents a significant step forward in achieving enhanced toughness without compromising the inherent chemical inertness of alumina (
Additive Manufacturing and 3D Printing
The future of high-temperature ceramic components may well lie in additive manufacturing techniques. Advances in 3D printing of ceramics are enabling the production of complex, bespoke shapes that were previously unattainable using traditional methods. These technologies offer the potential for rapid prototyping and customization of alumina boats tailored to very specific process requirements. As 3D printing technology matures, it is expected that the cost and lead times for custom alumina ceramic parts will decrease, making them even more attractive for both research and industrial applications.
Environmental Considerations and Energy Efficiency
In an era of increasing environmental awareness, the energy efficiency of high-temperature processes is coming under scrutiny. Alumina boats contribute indirectly to energy savings by providing uniform heat distribution and reducing the energy required to achieve and maintain high temperatures. In addition, the durability and long lifespan of alumina components mean that fewer resources are consumed in manufacturing replacements. Future research may focus on further optimizing the thermal properties of alumina through surface treatments or the development of composite materials that offer even greater energy efficiency in furnace applications.
Smart Materials and Integrated Sensor Technology
Another emerging trend is the integration of smart sensor technology with high-temperature ceramic components. By embedding temperature sensors or strain gauges within the alumina boat or its supporting structures, it becomes possible to monitor the thermal and mechanical state of the system in real time. Such integration could lead to smarter, more adaptive furnace control systems that optimize heating profiles, improve energy efficiency, and predict maintenance needs before failures occur.
Advantages and Limitations Revisited
Advantages
- Thermal and Chemical Stability: The foremost advantage of alumina boats is their ability to withstand extreme temperatures and corrosive environments without degrading. This reliability is crucial in processes where maintaining material purity is paramount.
- Mechanical Robustness: Alumina’s high hardness and wear resistance mean that alumina boats can endure repeated use with minimal maintenance.
- Customization and Versatility: The design flexibility offered by ceramic processing techniques allows alumina boats to be tailored for a wide range of applications—from small-scale laboratory testing to large industrial furnaces.
- Electrical Insulation: Alumina’s excellent dielectric properties enable its use in processes where electrical insulation is required, such as semiconductor processing and vacuum furnaces.
- Energy Efficiency: Uniform heat distribution minimizes energy losses and contributes to more efficient high-temperature processes.
Limitations
- Brittleness: Although alumina is hard and durable, it is inherently brittle compared to metals. This brittleness means that alumina boats must be handled carefully, and thermal shock management is critical.
- Manufacturing Complexity: The production of high-quality alumina boats requires sophisticated processing techniques, and achieving tight tolerances can be challenging and costly.
- Customization Lead Times: While custom alumina boats offer great benefits, the lead times for bespoke parts can be longer compared to standard industrial components, especially when complex shapes are required.
Case Studies and Industrial Examples
Metal Casting in the Foundry Industry
In the foundry industry, alumina boats are commonly used to melt and cast alloys. For example, in the production of high-performance stainless steel, an alumina boat provides a non-reactive environment that prevents contamination from the container. By ensuring a uniform temperature profile, the alumina boat allows for consistent melting and alloying, which improves the quality of the final cast product. The longevity and durability of the alumina boat also reduce downtime, leading to increased production efficiency.
Semiconductor Annealing Processes
In semiconductor manufacturing, precise temperature control is critical. Alumina boats are employed in tube furnaces during annealing processes. The inert nature of alumina ensures that the semiconductor wafers are not exposed to contaminants, while its high thermal conductivity guarantees that the wafers experience uniform heating. This level of control is essential for achieving the desired electronic properties in semiconductor devices. The non-reactive and electrically insulating properties of alumina contribute to the overall reliability and performance of the semiconductor processing line.
Glass Melting in Optical Component Fabrication
Optical glass fabrication demands absolute purity and uniformity in the melt. Alumina boats are used to melt raw glass materials because their inert surface does not interact with the molten glass. The even heat distribution provided by the alumina boat is crucial in producing glass with the optical clarity required for high-end lenses and other optical components. The use of alumina boats in such processes minimizes defects and ensures that the final glass product meets stringent quality standards.
Future Outlook
Research and Development
Ongoing research in ceramic engineering continues to push the boundaries of what alumina can achieve. Researchers are investigating novel sintering techniques, such as spark plasma sintering and microwave sintering, to further enhance the properties of alumina. Improvements in additive manufacturing and 3D printing of ceramics are also expected to revolutionize the production of alumina boats, making them even more versatile and cost-effective.
Market Trends
As industries increasingly demand higher performance and greater energy efficiency from their high-temperature processing equipment, the market for advanced ceramics such as alumina is projected to grow. Alumina boats, in particular, are likely to see increased adoption in emerging sectors such as renewable energy, aerospace, and advanced manufacturing. The ability to tailor alumina components to specific process requirements will continue to drive innovation and open up new application areas.
Sustainability Considerations
With a global focus on sustainability and energy conservation, the longevity and efficiency of alumina boats will become even more valuable. Their long service life, combined with their ability to improve process efficiency, means that alumina boats offer an environmentally friendly solution for high-temperature processing. Research into recycled alumina and improved fabrication methods may further enhance the sustainability profile of these critical components.
Conclusion
Alumina boats have proven to be a cornerstone technology in high-temperature applications, offering unparalleled thermal stability, chemical inertness, and mechanical strength. Their unique properties make them suitable for a broad spectrum of applications—from metal casting and ceramic sintering to semiconductor processing and glass melting. Despite some limitations, such as brittleness and the complexities of ceramic manufacturing, the benefits of alumina boats continue to outweigh the challenges in many industrial and research settings.
The continuous evolution of ceramic processing techniques and the integration of advanced composite materials, such as zirconia-toughened alumina, promise to enhance the performance of alumina boats even further. Furthermore, the emerging trends in additive manufacturing and smart materials are set to transform the landscape of high-temperature engineering, offering new levels of customization, efficiency, and reliability.
In summary, the versatility of alumina boats lies not only in their ability to perform under extreme conditions but also in the wide range of processes they support. Whether it is maintaining the purity of high-temperature melts, enabling precise thermal treatments in semiconductor manufacturing, or providing a stable environment for chemical reactions, alumina boats continue to play a vital role in pushing the boundaries of what is possible in modern industry.
As industries look toward the future, the ongoing research and development in alumina ceramics will likely yield even more robust, efficient, and adaptable solutions. For engineers and researchers alike, alumina boats represent a critical tool that underpins many of today’s high-temperature technologies—and they will undoubtedly remain a key component in the evolution of advanced manufacturing and processing for years to come.