Hafnium (Hf), a lustrous and ductile metal, has found its place in various advanced technologies due to its exceptional physical and chemical properties. As industries continue to push the boundaries of material science, the application of hafnium particles in evaporation coatings has emerged as a significant advancement. This article explores the characteristics of hafnium particles, their role in evaporation coating processes, and their applications across diverse fields.
Properties of Hafnium Particles
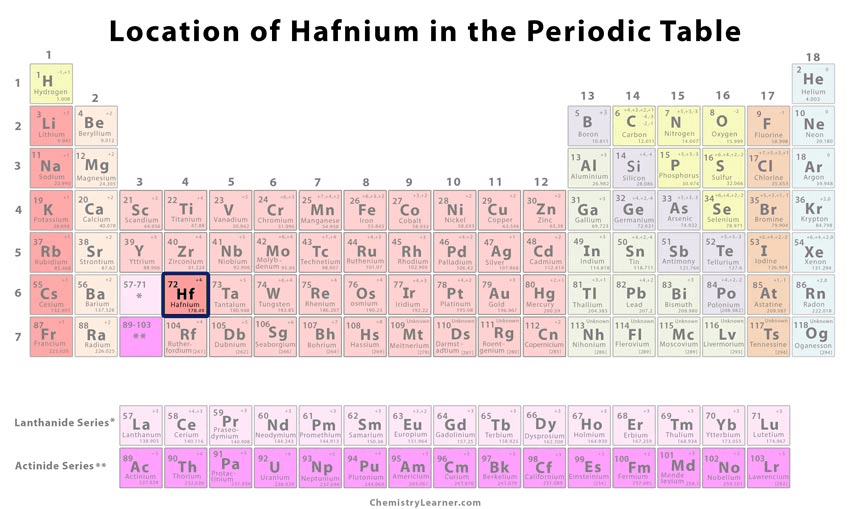
High Melting Point
Hafnium boasts an extraordinarily high melting point of 2,233°C, making it an excellent candidate for high-temperature applications. This property is particularly beneficial in evaporation coating, where materials are vaporized and deposited on substrates under vacuum conditions.
Corrosion Resistance
Hafnium’s resistance to corrosion by alkalis, acids, and other chemicals enhances its longevity in demanding environments. This trait ensures the durability of coatings produced using hafnium particles.
High Density and Atomic Number
With a density of 13.31 g/cm³ and an atomic number of 72, hafnium provides exceptional stopping power against high-energy radiation. This characteristic is critical in applications such as protective coatings in nuclear reactors and aerospace technology.
Thermal Stability
Hafnium maintains structural integrity under extreme thermal conditions, which is vital for coatings subjected to high temperatures. Its low thermal neutron absorption cross-section further enhances its suitability for nuclear applications.
Evaporation Coating: An Overview
Evaporation coating is a process where materials are heated in a vacuum until they vaporize. The vaporized material then condenses on a substrate to form a thin, uniform coating. This method is widely employed in industries requiring precision and high-quality coatings, such as optics, electronics, and aerospace.
Role of Hafnium Particles in Evaporation Coating
- Material Efficiency: Hafnium particles, due to their high purity and uniform size, enable efficient vaporization, reducing material waste during the coating process.
- Adhesion and Uniformity: Hafnium’s excellent adhesion properties ensure a uniform coating layer, which is critical for optical and electronic applications.
- Thermal Performance: Hafnium coatings exhibit superior thermal stability, making them ideal for components exposed to extreme heat.
Industrial Applications
Aerospace
Hafnium-based coatings are extensively used in aerospace for enhancing the performance of jet engines, turbine blades, and spacecraft components. These coatings protect against oxidation and thermal degradation, ensuring the reliability of critical parts.
Nuclear Industry
Hafnium’s ability to absorb neutrons without forming long-lived radioactive isotopes makes it indispensable in nuclear reactors. Coatings made from hafnium particles provide a protective barrier for reactor components, enhancing their safety and lifespan.
Optics
In optical devices, hafnium coatings are employed for their high refractive index and exceptional transparency in the ultraviolet (UV) spectrum. These properties make hafnium ideal for lenses, mirrors, and other precision optical components.
Electronics
Hafnium particles play a vital role in the electronics industry. Thin films of hafnium oxide, produced through evaporation coating, are used as high-k dielectrics in semiconductors. These films improve the performance of transistors and capacitors in modern integrated circuits.
Medical Devices
Hafnium’s biocompatibility has led to its use in coatings for medical implants and devices. These coatings enhance wear resistance and reduce the risk of corrosion, ensuring patient safety and device longevity.
Advantages of Hafnium in Evaporation Coatings
- Enhanced Durability: Hafnium coatings are highly durable, extending the service life of components in harsh environments.
- Precision in Coating Thickness: The uniform vaporization of hafnium particles ensures precise control over coating thickness, meeting the stringent requirements of industries like optics and electronics.
- Resistance to Wear and Corrosion: Hafnium’s inherent resistance to wear and corrosion makes it a reliable choice for applications requiring prolonged exposure to challenging conditions.
- Improved Thermal Performance: Hafnium’s thermal stability enhances the performance of coated components in high-temperature settings.
Challenges in Using Hafnium Particles for Evaporation Coatings
Despite its numerous advantages, the use of hafnium particles in evaporation coatings presents certain challenges:
High Cost
Hafnium is relatively expensive due to its scarcity and the complexities involved in its extraction and purification. This limits its widespread adoption in cost-sensitive industries.
Handling and Storage
Hafnium particles are reactive with air and water, requiring careful handling and storage under controlled conditions to prevent oxidation.
Technical Expertise
The deposition of hafnium coatings demands specialized equipment and technical expertise to achieve optimal results. Any deviation in process parameters can affect the quality of the final coating.
Future Trends
The growing demand for advanced materials is driving research into the development of hafnium-based coatings. Emerging trends include:
Nanostructured Hafnium Coatings
The use of nanotechnology to create hafnium coatings with enhanced properties, such as improved hardness, wear resistance, and optical performance, is gaining traction. These coatings have potential applications in next-generation electronics and aerospace components.
Sustainable Production Methods
Efforts are being made to develop eco-friendly and cost-effective methods for producing hafnium particles. Recycling hafnium-containing waste and exploring alternative extraction techniques are key areas of focus.
Integration with Additive Manufacturing
The integration of hafnium particles with additive manufacturing technologies, such as 3D printing, holds promise for producing complex components with tailored properties. This approach could revolutionize industries ranging from aerospace to healthcare.
Conclusion
Hafnium particles are a critical material in evaporation coating processes, offering unmatched performance in high-temperature and corrosive environments. Their applications span a wide range of industries, including aerospace, nuclear energy, optics, and electronics. While challenges such as cost and handling remain, ongoing research and technological advancements are paving the way for broader adoption of hafnium-based coatings. As industries continue to innovate, hafnium’s role in shaping the future of material science remains significant.