Thin film deposition has revolutionized modern technology by enabling the creation of coatings and layered structures with controlled composition, uniform thickness, and precisely engineered properties. At the heart of many physical vapor deposition (PVD) processes lies the sputtering target—a solid source material that, when bombarded by ions, ejects atoms to form thin films on a substrate. Among the various materials used for sputtering targets, magnesium has emerged as an attractive candidate for advanced applications due to its unique combination of physical and chemical properties. This article delves into the nature of magnesium sputtering targets, their manufacturing and performance characteristics, and how they are enabling breakthroughs in electronics, optics, renewable energy, and beyond.
1. Overview of Thin Film Deposition and Sputtering
Thin film deposition is a technique that allows engineers to deposit layers of material only a few nanometers to several micrometers thick. This process is critical in fabricating semiconductor devices, optical coatings, sensors, and energy-related components. Among the various methods available, sputtering is especially popular for its versatility and ability to produce films with excellent adhesion, density, and uniformity.
In the sputtering process, a target material is placed in a vacuum chamber and bombarded by energetic ions—usually derived from an inert gas such as argon. The ion bombardment dislodges atoms or clusters from the target, and these species then condense on a substrate to form a thin film. The choice of target material is crucial; it not only determines the film composition but also influences deposition rates, film quality, and overall process efficiency.
2.The Role of Magnesium in Sputtering Targets
Material Type | Magnesium |
Symbol | Mg |
Color/Appearance | Silvery White, Metallic |
Melting Point | 650 °C |
Boiling Point | 1090 °C |
Density | 1738 kg/m3 |
Sputter | DC |
Type of Bond | Indium, Elastomer |
Comments | Extremely high rates possible. |
Available Sizes | Dia.: 2.0″, 3.0″, 4.0″, 5.0″, 6.0″ Thick: 0.125″, 0.250″ |
Magnesium (Mg) is a lightweight, silvery-white metal known for its high thermal conductivity, low density, and favorable electrical properties. Its use in sputtering targets offers several advantages:
·High Purity and Density: Magnesium sputtering targets are manufactured to achieve ultra-high purity levels (often greater than 99.95%) with high density and minimal grain size. This ensures that the thin films deposited are uniform and free of impurities that could affect device performance.
·Thermal Conductivity: The high thermal conductivity of magnesium facilitates efficient heat transfer during sputtering, helping to maintain stable deposition conditions. This is critical in high-power sputtering systems where effective heat management directly impacts film quality.
·Process Compatibility: With a relatively low melting point (around 650 °C) and moderate electrical resistivity, magnesium is well suited for sputtering applications where both metallic and oxide forms are used. Moreover, it can be alloyed with other elements (such as zinc or aluminum) to tailor film properties.
·Versatility: Magnesium sputtering targets are not only used for depositing pure magnesium films but are also key components in composite or alloy targets. These broader compositions extend the range of potential applications and allow for precise adjustment of electrical, thermal, and mechanical characteristics.
Magnesium’s chemical and physical properties make it especially well suited for advanced semiconductor and optical applications, where thin films must meet stringent performance and reliability standards.
3. Manufacturing of Magnesium Sputtering Targets
The production of high-performance magnesium sputtering targets involves several carefully controlled steps. Manufacturers employ advanced metallurgical techniques to ensure that the targets have the desired purity, density, and grain structure. The process can be divided into the following key stages:
3.1. Raw Material Purification
High-purity magnesium is sourced and refined to remove unwanted impurities. Techniques such as vacuum distillation, zone refining, or sublimation are often employed to achieve purity levels that meet or exceed industry standards. This step is crucial to ensure that the deposited films do not incorporate contaminants that could impair their function.
3.2. Casting and Ingot Formation
After purification, magnesium is melted and cast into ingots. The casting process is performed in a vacuum or under inert atmospheres to minimize oxidation and ensure that the metal solidifies into a dense, void-free form. Modern controlled casting techniques yield ingots with uniform microstructures that are ideal for subsequent processing.
3.3. Machining and Shaping
Once the ingots are formed, they are machined into the desired target geometries. Targets can be produced in various forms, including monoblock (solid disc), bonded, or rotatable designs. Rotatable magnesium sputtering targets, for example, are engineered for large-area coatings and incorporate specially designed backing and cooling configurations. Precision machining ensures that the target surfaces are flat and free of defects—a prerequisite for uniform sputtering.
3.4. Sintering and Post-Processing
For certain applications, particularly when producing composite or oxide targets, powder metallurgy and sintering techniques are used. Although pure magnesium targets are typically cast, composite targets or those used to deposit magnesium oxide films may require sintering. This process involves compacting magnesium powders under high pressure and temperature in a controlled atmosphere to produce a high-density target with excellent microstructural uniformity.
3.5. Quality Control and Characterization
After fabrication, the targets undergo rigorous quality control and characterization. Analytical techniques, including X-ray fluorescence (XRF), glow discharge mass spectrometry (GDMS), and inductively coupled plasma (ICP) spectroscopy, are used to verify purity levels. Additional measurements of dimensional accuracy, surface flatness, and thermal properties ensure that every target meets the demanding standards required for advanced thin film deposition.
4. Technical Advantages of Magnesium Sputtering Targets
Magnesium sputtering targets offer several technical benefits that enhance the thin film deposition process:
4.1. Uniform Deposition and High-Density Films
The high purity and uniform microstructure of magnesium sputtering targets result in films with consistent thickness and density. Uniform films are essential in semiconductor manufacturing and optical coating applications, where even minor variations can significantly affect device performance.
4.2. Enhanced Thermal Management
Magnesium’s high thermal conductivity helps to dissipate heat during the sputtering process. In high-power systems, efficient heat transfer minimizes localized heating that can lead to target damage or non-uniform film growth. This thermal stability allows for higher sputtering power densities while maintaining consistent deposition conditions.
4.3. Flexibility in Process Design
Magnesium targets can be tailored to various shapes and sizes to meet the requirements of different sputtering systems. Whether used in traditional planar deposition setups or in rotatable configurations for large-area coatings, magnesium targets offer process flexibility. The availability of both bonded and unbonded targets allows users to choose the configuration that best suits their equipment and desired film properties.
4.4. Superior Electrical and Mechanical Properties
Magnesium exhibits favorable electrical resistivity and mechanical strength, which contribute to reliable performance during sputtering. Its moderate melting point and low coefficient of thermal expansion help maintain target stability during extended sputtering runs, ensuring that targets perform consistently over time without significant degradation.
5. Advanced Applications Enabled by Magnesium Sputtering Targets
The high performance and versatility of magnesium sputtering targets have enabled their use in a wide array of advanced applications:
5.1. Semiconductor and Microelectronics
In semiconductor fabrication, thin metallic films are crucial for forming electrical interconnects, barrier layers, and electrodes. Magnesium sputtering targets are used to deposit films that are both lightweight and robust in terms of electrical conductivity. Additionally, magnesium can be alloyed with other elements to tailor the electrical and mechanical properties for specific device applications, making magnesium-based films attractive for next-generation microelectronic components where size, weight, and performance are critical.
5.2. Photovoltaics and Solar Energy
Thin film solar cells require materials that not only absorb light efficiently but also offer excellent charge transport properties. Magnesium sputtering targets contribute to the deposition of transparent conductive oxides (TCOs) or serve as components in alloy systems for light-trapping coatings. The high purity of magnesium films aids in the production of solar panels with improved energy conversion efficiency. Large-area rotatable targets are especially suited for coating substrates in photovoltaic manufacturing, enabling scalable production.
5.3. Optical Coatings and Displays
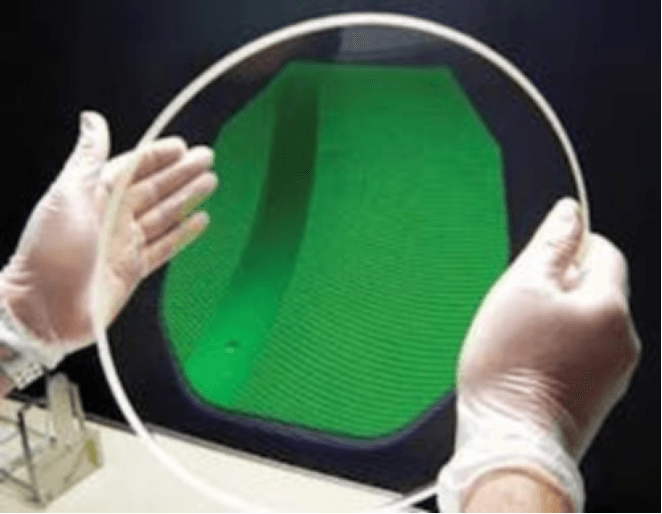
Optical applications demand films with precise optical properties, such as controlled refractive indices, high transparency, and minimal light scattering. Magnesium-based films—including magnesium fluoride (MgF₂) and magnesium oxide (MgO)—are widely used as anti-reflective coatings, beam splitters, and optical filters. The excellent uniformity achieved through sputtering with magnesium targets ensures that optical components perform reliably in high-precision instruments and display technologies.
5.4. Advanced Coatings in Aerospace and Automotive Industries
In high-performance environments like aerospace and automotive applications, coatings must withstand extreme temperatures, mechanical stress, and corrosive conditions. Magnesium sputtering targets are used to deposit thin films that serve as protective or functional coatings on components such as engine parts, structural elements, and sensor housings. The lightweight nature of magnesium, combined with its ability to form high-density films, results in coatings that enhance durability while contributing to overall weight reduction in vehicles and aircraft.
5.5. Energy Storage and Conversion Devices
Recent research has explored the use of magnesium-based thin films in energy storage systems and fuel cells. For instance, magnesium hydride (MgH₂) is a promising material for hydrogen storage due to its high gravimetric capacity. Sputtering targets composed of magnesium or magnesium alloys enable the deposition of films with controlled nanostructures that enhance hydrogen uptake and release kinetics. Moreover, magnesium-containing films are finding applications in catalytic converters and oxygen generation systems, where precise film composition and structure are crucial for optimal performance.
5.6. Nanostructured Materials and Emerging Technologies
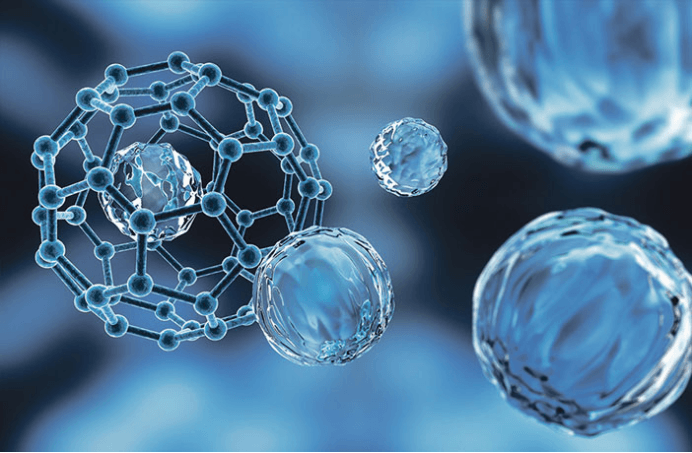
Beyond traditional applications, magnesium sputtering targets are being investigated for the fabrication of nanostructured materials. By varying sputtering parameters, researchers can control the crystalline facets and grain orientation in deposited magnesium films. Such nanoscale control opens up opportunities in catalysis, sensor technology, and emerging computing architectures. The ability to tailor nanostructures through physical deposition processes represents a significant advancement in materials science and engineering.
6. Integration of Magnesium Sputtering Targets in Modern Deposition Systems
Modern deposition systems are designed with flexibility and precision in mind, and magnesium sputtering targets are fully compatible with these advanced platforms. Manufacturers now offer targets in various configurations—such as standard planar targets for conventional sputtering and rotatable targets for large-area coating—to meet the diverse needs of different industries.
6.1. System Design and Process Optimization
Controlling key process parameters—such as sputtering power, substrate temperature, and gas pressure—is essential for achieving desired film properties. Magnesium sputtering targets, with their high thermal conductivity and uniform density, help maintain stability in these parameters. This stability allows for fine-tuning of film thickness, composition, and microstructure. Modern deposition systems often include in situ monitoring tools like quartz crystal microbalances and optical emission spectrometers, ensuring that deposition rates remain consistent throughout the process.
6.2. Backing Plate Technology and Cooling Strategies
To enhance performance and prolong target life, magnesium sputtering targets are frequently mounted on copper or molybdenum backing plates. These backing plates provide mechanical support and act as heat sinks to dissipate thermal energy during high-power sputtering. Advanced cooling strategies—including water-cooled target assemblies—ensure that the target remains at an optimal temperature, thereby minimizing thermal stress and reducing the likelihood of target degradation over extended sputtering runs.
6.3. Customization for Specialized Applications
Recognizing the diverse requirements of modern thin film applications, many suppliers now offer customized magnesium sputtering targets. Customization can involve adjusting target dimensions, modifying purity levels, or incorporating alloying elements to achieve specific electrical, thermal, or mechanical properties. This tailored approach enables researchers and industrial users alike to push the boundaries of thin film technology in niche applications ranging from microelectronics to biomedical coatings.
7. Future Perspectives and Emerging Trends
As the demand for advanced thin film materials continues to grow, magnesium sputtering targets are poised to play an increasingly important role. Several emerging trends are likely to shape the future of this field:
7.1. Integration with Hybrid Deposition Techniques
Hybrid deposition techniques, such as hybrid physical–chemical vapor deposition (HPCVD), are gaining traction—especially for depositing complex compounds like magnesium diboride (MgB₂) for superconducting applications. These processes combine the advantages of both physical and chemical deposition methods, providing enhanced control over film stoichiometry and crystalline quality. Incorporating magnesium sputtering targets into hybrid systems is expected to yield films with superior properties for applications in superconducting electronics and energy storage devices.
7.2. Nanostructured and Functional Coatings
Advances in nanotechnology are driving demand for films with engineered nanoscale features. By precisely controlling deposition parameters, researchers can now tailor the grain structure and orientation in magnesium-based films. Such nanostructured coatings offer enhanced catalytic, optical, and mechanical properties that are critical for applications in sensors, flexible electronics, and even emerging quantum computing components.
7.3. Sustainable Manufacturing and Recycling
Sustainability is becoming an increasingly important consideration in materials processing. The production of high-purity magnesium sputtering targets, when combined with efficient thin film deposition methods, contributes to reduced waste and lower energy consumption. Ongoing research into recycling and reclaiming target materials is expected to make sputtering processes more environmentally friendly, aligning with broader industrial trends toward green manufacturing.
7.4. Expanded Applications in Emerging Fields
New fields such as wearable electronics, flexible displays, and advanced photovoltaics are emerging with their own unique material challenges. Magnesium sputtering targets, with their favorable properties and high adaptability, are well positioned to address these challenges. As deposition techniques continue to be refined and customized, the role of magnesium in next-generation technologies is likely to expand even further.
8. Conclusion
Magnesium sputtering targets are at the forefront of thin film deposition technology, powering advanced applications across a diverse range of industries. Their high purity, excellent thermal management, and versatile process compatibility make them indispensable for fabricating high-quality films that meet the demanding standards of modern electronics, optics, energy devices, and more.
From the meticulous purification and casting processes to precision machining and rigorous quality control, the manufacturing of magnesium sputtering targets exemplifies the cutting edge of materials engineering. With ongoing advancements in deposition techniques—including hybrid methods and nanostructuring—the future of magnesium-based thin films looks brighter than ever.
As industries push the limits of performance and efficiency, the unique advantages offered by magnesium sputtering targets will continue to drive innovation in thin film technology. Whether it is through the production of lightweight semiconductor devices, robust solar panels, or advanced optical coatings, magnesium remains a key enabler in the quest for high-performance materials and sustainable manufacturing solutions.
In summary, the integration of magnesium sputtering targets into modern deposition systems not only enhances film quality but also expands the potential for novel applications in emerging technologies. With continued research and development, these targets will undoubtedly play a pivotal role in powering the next generation of advanced, high-performance devices.