The magnetron sputtering process is a critical technique in thin film deposition used across industries ranging from microelectronics and photovoltaics to decorative coatings and optics. Central to this technology is the sputtering target—the source material that is eroded by ion bombardment to deposit a film on a substrate. Over time, target designs have evolved to meet the demands for higher efficiency, better film quality, and improved cost-effectiveness. Two of the most common target configurations are planar (or flat) targets and rotatory (or rotary) targets. This article explores both types, detailing their respective advantages and disadvantages, and examines how each design influences sputtering performance.
Understanding Sputtering Targets
Sputtering targets serve as the material source in magnetron sputtering systems. In these systems, a plasma—typically generated in an inert gas atmosphere—bombards the target, causing atoms to be ejected from its surface. These atoms then condense on a substrate, forming a thin film. Because the target’s shape and structure directly influence the uniformity, sputtering rate, and overall efficiency of the deposition process, understanding the nuances of target design is essential.
A target’s design not only affects the yield—often expressed as the utilization ratio—but also determines how heat is managed during sputtering and how uniformly the material is eroded over time. Both planar and rotatory targets have found their niches in various applications. Planar targets, with their flat surfaces, are often favored in prototype work and laboratory experiments, whereas rotatory targets are generally more advantageous in high-volume industrial settings where maximizing material usage and maintaining process stability are paramount.
Planar Sputtering Targets
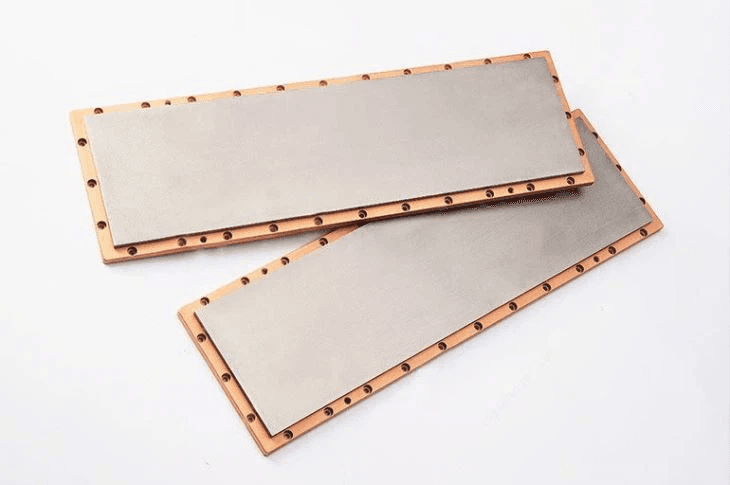
Design and Structure
Planar sputtering targets are typically flat, rectangular, or circular discs mounted onto the sputtering system. Their simple design means that the entire surface is exposed to the plasma, which is ideally distributed in a ring-like “racetrack” pattern defined by the magnetron’s magnetic field. As a result, the central and peripheral areas experience different sputtering intensities, leading to a phenomenon commonly known as “trenching” or non-uniform erosion.
Advantages of Planar Targets
- Simplicity and Ease of Use
The planar design is straightforward. Because of their geometric simplicity, planar targets are relatively easier to manufacture and mount. This makes them a popular choice for laboratory-scale experiments and for research and development where rapid prototyping is essential. - Cost-Effective for Small Scale Applications
In settings where large volumes of material are not required, planar targets are a cost-effective option. Their manufacturing and handling costs are lower than those of rotatory targets, making them attractive for low-volume production and elemental experimentation. - Uniform Coating Under Controlled Conditions
When operating under ideal conditions, planar targets can provide a relatively uniform film thickness across the sputtered substrate. This uniformity is often sufficient for many research applications where deposition parameters can be finely tuned.
Disadvantages of Planar Targets
- Low Utilization Ratio
One of the most significant drawbacks of planar targets is their low utilization efficiency. During sputtering, the plasma tends to concentrate along a ring-shaped “runway” on the target’s surface. As a result, only about 30–35% of the target material is effectively used, with the remainder becoming scrap. This low efficiency not only increases material costs but also results in frequent target replacement in production environments. - Non-Uniform Erosion and Trenching
The uneven magnetic field distribution inherent in planar target setups leads to non-uniform erosion. The edges of the racetrack may experience excessive sputtering (trenching), while areas outside the primary erosion zone are underutilized. This uneven wear can cause process instabilities and may adversely affect film quality over extended sputtering runs. - Thermal Expansion and Vacuum Challenges
Because planar targets are typically assembled in segmented pieces (especially in very large targets), gaps must be maintained between segments to allow for thermal expansion. However, these gaps can trap air, leading to difficulties in achieving high vacuum levels. Residual gases can then be incorporated into the film, potentially degrading its properties and uniformity. - Limited Continuous Runtime
The low utilization and non-uniform erosion often lead to shorter continuous operating times. When the most active areas of the target are exhausted, the sputtering process must be halted to replace the target, reducing overall production efficiency.
Overall, planar targets serve well in controlled research environments and for low-volume production. Their lower initial cost and ease of implementation make them an excellent choice for experimentation, but their inherent limitations in material utilization and long-term process stability present challenges in high-volume industrial applications.
Rotatory (Rotary) Sputtering Targets
Design and Structure
Rotatory sputtering targets are designed with a cylindrical or tubular geometry. In these systems, the target is mounted on a rotating backing tube. As the target rotates during sputtering, the entire surface is exposed to the plasma over time, which evens out the sputtering process. This continuous movement allows for a much more uniform erosion and leads to higher overall utilization of the target material.
Advantages of Rotatory Targets
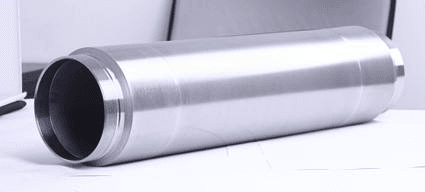
- High Utilization Ratio
One of the most compelling advantages of rotatory targets is their significantly higher material utilization. Due to the rotational motion, the sputtering area continuously changes, and the entire target surface is used more effectively. Utilization ratios can reach up to 80% compared to only about 30–35% for planar targets. This high efficiency reduces scrap and improves cost-effectiveness, particularly when using expensive or rare materials. - Uniform Erosion and Longer Runtime
The rotational design minimizes the “hot spots” that can form on planar targets. With the target spinning, material erosion becomes more uniform, which in turn leads to more consistent sputtering performance over time. This uniform wear extends the operational lifetime of the target and reduces downtime for target replacement—a significant advantage in continuous, high-volume production environments. - Enhanced Thermal Management
Rotatory targets generally benefit from improved thermal distribution. The continuous motion spreads the heat load over a larger surface area, keeping the target cooler and reducing thermal stresses. This improved cooling helps to mitigate issues like nodule formation (localized build-ups of sputtered material) and arcing, which are more common in planar designs where heat tends to concentrate in the sputtering “racetrack.” - Suitability for Continuous Processing
Because of their high utilization and even erosion, rotatory targets are ideal for continuous sputtering processes, such as roll-to-roll coating in large-scale manufacturing. The ability to run for extended periods without interruption not only boosts throughput but also enhances overall process stability.
Disadvantages of Rotatory Targets
Higher Initial Cost and Equipment Complexity
The advanced design of rotatory targets typically comes with a higher upfront cost. The manufacturing process for cylindrical targets is more complex, and the sputtering systems must be equipped with mechanisms to drive the rotation. This increased complexity also means that maintenance can be more challenging and that the equipment may require more frequent calibration to ensure consistent performance.
Potential Thermal Dissipation Issues
While rotatory targets generally offer superior thermal management, design imperfections can lead to localized overheating if the target is not engineered correctly. In some cases, issues such as inadequate bonding between the target sleeve and the backing tube can result in poor heat transfer, leading to elevated target temperatures and, eventually, mechanical stress or failure.
Mechanical and Structural Challenges
The dynamic nature of rotatory targets means that the mechanical integrity of the target assembly is paramount. Issues such as misalignment during rotation, vibrations, or mechanical wear of moving parts can lead to operational problems. Additionally, designing the target for optimal balance and rotational stability can be challenging, especially when scaling up the size of the target for large-area deposition processes.
Higher Production Complexity
In some production environments, the shift from planar to rotatory targets requires significant changes in the sputtering system configuration. Operators must be trained to handle the nuances of the rotary system, and process parameters may need to be optimized specifically for the rotating target design. This learning curve can represent an initial hurdle for facilities transitioning from planar targets.
In summary, rotatory targets offer a number of clear advantages for high-volume and continuous sputtering applications. Their superior material utilization, uniform erosion, and extended runtimes make them particularly appealing for industrial use—even though the higher equipment cost and increased mechanical complexity might pose challenges in some scenarios.
Comparative Analysis: Planar vs. Rotatory Targets
When choosing between planar and rotatory targets, several factors must be considered. The following analysis provides a detailed comparison based on key performance and operational criteria.
Utilization Ratio and Material Efficiency
- Planar Targets:
Planar targets typically have a low utilization ratio—often in the range of 30–35%. This is mainly due to the concentration of the sputtering plasma in a limited “racetrack” region. The majority of the target material remains unused, which results in higher material costs and frequent target replacements. - Rotatory Targets:
In contrast, rotatory targets, owing to their continuous motion, achieve utilization ratios of up to 80%. The design ensures that the entire surface area of the target is sputtered uniformly over time, dramatically reducing material wastage and making them ideal for expensive or critical materials.
Film Uniformity and Process Stability
- Planar Targets:
The fixed nature of the planar target can result in non-uniform erosion, which in turn may cause variations in film thickness across the substrate. Although careful process tuning and target design modifications (such as varying the target thickness in the sputtered “racetrack” area) can mitigate these issues, they add complexity to the system. Additionally, thermal expansion gaps between segmented planar targets can introduce inconsistencies in vacuum quality and film properties. - Rotatory Targets:
The dynamic nature of rotatory targets ensures that any localized non-uniformity is averaged out over time. This leads to a more stable sputtering process and a consistently uniform film, which is particularly important in applications where film thickness and quality are critical. Enhanced thermal management in rotatory targets also reduces defects such as nodules and arcing, further contributing to process stability.
Thermal Management and Mechanical Integrity
- Planar Targets:
The planar design tends to concentrate heat in the sputtering zone, which can lead to rapid temperature increases and localized thermal stress. To counteract this, many planar targets incorporate design features (such as thicker target sections in high-sputtering zones) or rely on sophisticated cooling systems. However, these solutions are often not enough to overcome the inherent limitations of the design. - Rotatory Targets:
Rotatory targets naturally dissipate heat more evenly due to their motion. By continuously exposing different parts of the target to the plasma, the overall heat load is spread out, lowering the risk of overheating and associated mechanical stresses. This more uniform thermal profile helps maintain the integrity of the target over long operational periods. It is crucial, however, that the mechanical design ensures proper contact between the rotating target and its backing tube to facilitate effective heat transfer.
Economic Considerations
- Planar Targets:
The simplicity of planar targets translates to lower manufacturing costs and easier integration into existing sputtering systems. For research laboratories and low-volume production, this cost efficiency is a major advantage. However, the low material utilization and frequent need for replacement can increase operating costs in the long run. - Rotatory Targets:
Although the initial investment for rotatory targets is higher due to more complex manufacturing and system requirements, their extended lifetime and higher material utilization often justify the cost in high-volume production settings. The decreased frequency of target replacement and improved process uptime can lead to significant savings over time.
Application-Specific Considerations
- Prototyping and R&D:
For experimental work and small-scale production, planar targets are often sufficient. Their ease of handling, lower cost, and simplicity make them attractive options for laboratories focused on elemental studies or the development of new materials. - High-Volume Manufacturing:
In industrial settings—such as semiconductor fabrication, large-area coatings for solar panels, or continuous roll-to-roll processing—the advantages of rotatory targets become clear. Their high utilization ratio, uniform film quality, and longer operational life are critical for maintaining process efficiency and reducing production costs.
Emerging Trends and Hybrid Designs
As the sputtering industry continues to evolve, engineers and researchers are exploring ways to combine the benefits of both planar and rotatory targets. One emerging development is the cylindrical planar sputtering target, which attempts to blend the uniform coating properties of planar designs with the high material utilization of rotatory targets.
Cylindrical Planar Sputtering Targets
This innovative design retains the “planar” coating characteristics—ensuring film uniformity—while adopting a cylindrical geometry that allows for rotational motion. By rotating the target, manufacturers can avoid the common pitfalls of non-uniform erosion and thermal hotspots that are prevalent in conventional planar targets. At the same time, the design aims to achieve utilization rates closer to those of rotatory targets. This hybrid approach is particularly advantageous when working with precious metals or expensive materials, where maximizing material usage is essential.
Future Directions
Looking forward, the potential for further optimization in target design is enormous. Innovations in bonding methods, thermal management, and mechanical engineering continue to push the boundaries of what sputtering targets can achieve. As the demand for high-quality thin films increases—especially in emerging sectors like flexible electronics, advanced optics, and next-generation photovoltaics—the development of targets that combine high efficiency, excellent uniformity, and robust operational stability will be paramount.
Ongoing research is focusing on:
- Improved Thermal Conductive Interfaces: Ensuring that even in rotatory designs, the target and backing tube maintain excellent thermal contact throughout prolonged sputtering runs.
- Adaptive Magnetron Designs: Tailoring the magnetic field distribution dynamically to optimize erosion patterns, regardless of whether a planar or rotatory target is used.
- Material-Specific Target Engineering: Developing target geometries optimized for the unique properties of different sputtering materials, where thermal and mechanical behaviors under sputtering conditions differ markedly.
These advances not only promise to improve the efficiency and cost-effectiveness of sputtering processes but may also enable new applications that were previously unattainable due to technical limitations.
Conclusion
Both planar and rotatory sputtering targets have distinct advantages and disadvantages that make them suitable for different applications:
- Planar Targets offer simplicity, lower upfront costs, and are well-suited for research and prototype work. However, they suffer from low material utilization, non-uniform erosion, and potential thermal and vacuum challenges.
- Rotatory Targets excel in high-volume manufacturing environments thanks to their high utilization ratio (up to 80%), uniform erosion, and improved thermal management. These benefits come at the cost of increased equipment complexity and higher initial investments.
For industrial applications where process stability, film uniformity, and long-term cost savings are critical, rotatory targets provide a clear advantage. Conversely, for laboratory-scale experiments and low-volume production, planar targets remain a practical and economical choice.
As technological advances continue to drive innovation in sputtering target design, hybrid solutions—such as cylindrical planar targets—promise to combine the best features of both approaches. These emerging designs may usher in an era of even more efficient and cost-effective thin film deposition, minimizing waste and maximizing operational efficiency.
In conclusion, understanding the strengths and limitations of each target type allows engineers and production managers to make informed decisions tailored to specific process requirements and production volumes. Whether opting for the simplicity of planar targets or the superior performance of rotatory targets, the ultimate goal is to achieve optimal thin film deposition with minimal waste and maximum efficiency.