Hafnium Tube is fast becoming an essential component in many high‑technology industries. With its unique combination of high temperature resistance, corrosion resistance, and excellent mechanical properties, hafnium in tubular form is ideal for a wide range of applications—from aerospace and nuclear reactors to chemical processing and advanced electronics. In this comprehensive article, we delve into the properties, manufacturing techniques, diverse applications, and market trends for hafnium tubes, offering a detailed resource for professionals, researchers, and enthusiasts.
Table of Contents
- Introduction to Hafnium Tube
- Unique Properties of Hafnium
- Manufacturing Processes
- Applications Across Industries
- Market Overview and Future Trends
- Comparisons with Other Materials
- Challenges in the Hafnium Tube Industry
- Environmental and Safety Considerations
- Conclusion
Introduction to Hafnium Tube
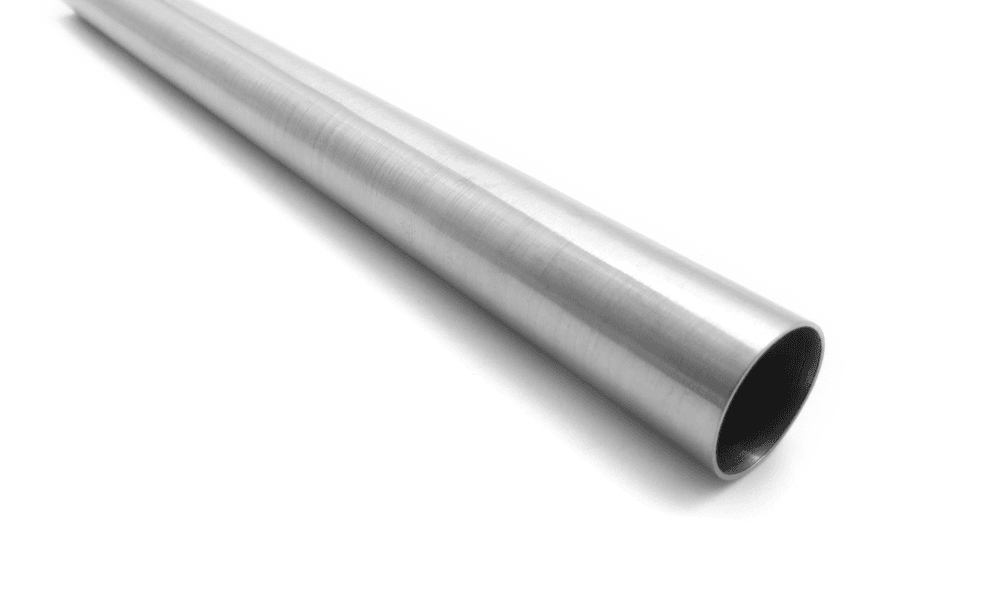
Hafnium, a refractory metal with the atomic number 72, is known for its high melting point and exceptional corrosion resistance. When formed into tubes, hafnium provides unparalleled performance under extreme conditions. These tubes are used where reliability, strength, and longevity are critical.
Hafnium Tube is often incorporated into systems that require sustained operation at high temperatures or in aggressive chemical environments. Because of its intrinsic properties, hafnium remains stable under conditions that would degrade other metals, making it a preferred material in critical applications.
Manufacturers and end users alike are turning to hafnium tubes as innovations in material science continue to drive demand for higher performance in industrial and technological applications. This article explores the wide-ranging benefits and applications of hafnium tubes, ensuring you gain a deep understanding of why they are indispensable in modern technology.
Unique Properties of Hafnium
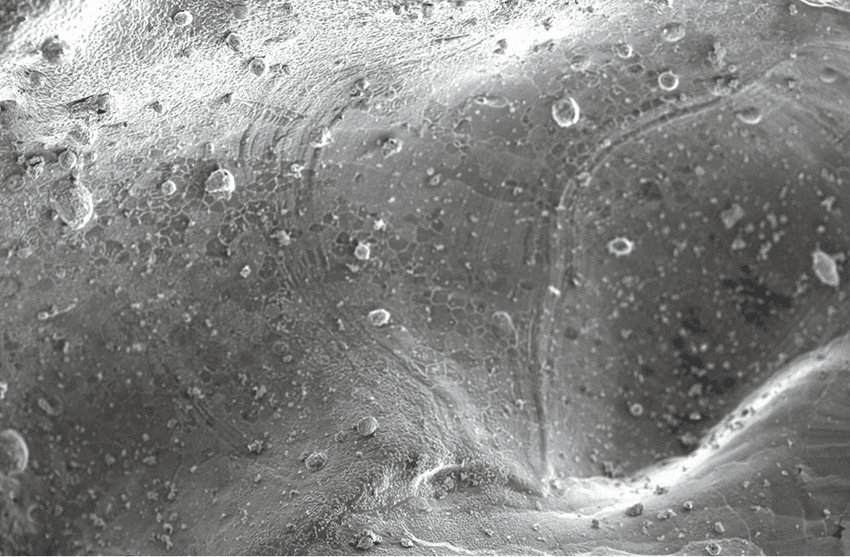
High Melting Point and Thermal Stability
One of the standout features of hafnium is its high melting point, which is around 2233 °C (4051 °F). This exceptional thermal stability ensures that hafnium tubes can withstand extreme heat without deforming or losing structural integrity. This property makes them ideal for applications in aerospace engines and high‑temperature industrial processes.
Corrosion Resistance
Hafnium’s chemical inertness is a key factor in its performance. When exposed to aggressive environments, including acids and bases, hafnium forms a stable oxide layer that protects it from further corrosion. This resistance to chemical attack makes hafnium tubes especially suitable for chemical processing and nuclear reactor components where exposure to corrosive substances is common.
Mechanical Strength and Durability
Hafnium exhibits excellent mechanical properties, including high tensile strength and resistance to wear. These features ensure that hafnium tubes can operate under mechanical stress over long periods, even in high‑pressure and high‑temperature environments. The durability of hafnium also translates to lower maintenance costs and a longer service life for equipment using these tubes.
Neutron Absorption Capabilities
In the nuclear industry, hafnium’s ability to absorb neutrons is highly valued. Hafnium tubes are used in control rods and other nuclear reactor components, where precise neutron absorption is crucial for maintaining safe and efficient reactor operations. The combination of high neutron absorption with thermal stability makes hafnium an integral material in reactor design.
Electrical Properties
While not as commonly discussed, hafnium also has interesting electrical properties, including high dielectric constant when used in thin films. This has led to its application in semiconductor devices, where hafnium oxide is used as a gate dielectric in transistors. As electronics continue to miniaturize, hafnium-based materials provide the performance needed in advanced microchips.
Manufacturing Processes
Raw Material Extraction and Purification
The production of hafnium tubes begins with the extraction of hafnium from ores, such as zirconium minerals. Hafnium is typically found in association with zirconium, and separating the two requires advanced purification techniques. The high‑purity hafnium is then refined to meet strict industry standards for use in high‑performance applications.
Tube Fabrication Methods
There are several fabrication methods employed to produce hafnium tubes, each chosen based on the required specifications:
- Extrusion: In this process, molten hafnium is forced through a die to form a tube shape. Extrusion is commonly used when uniform wall thickness and a smooth surface finish are required.
- Drawing: Cold or hot drawing processes are used to achieve precise dimensions and improved mechanical properties. Drawing ensures that the tube has consistent strength and durability.
- Welding and Seamless Production: For applications where there cannot be any seams or weak joints, seamless hafnium tubes are produced using methods such as pilgering or rotary piercing. Seamless tubes are critical in high‑pressure and corrosive environments.
Surface Treatments and Quality Control
Post‑fabrication, hafnium tubes undergo rigorous surface treatments to enhance corrosion resistance and smoothness. Processes such as annealing, passivation, and precision machining help optimize the final product. Additionally, quality control measures including X‑ray inspection and ultrasonic testing ensure that each tube meets the high‑quality standards required for critical applications.
Applications Across Industries
Hafnium tubes are versatile and have found applications in several high‑tech industries. Their unique properties make them indispensable in areas where reliability and performance under extreme conditions are paramount.
Aerospace and Defense
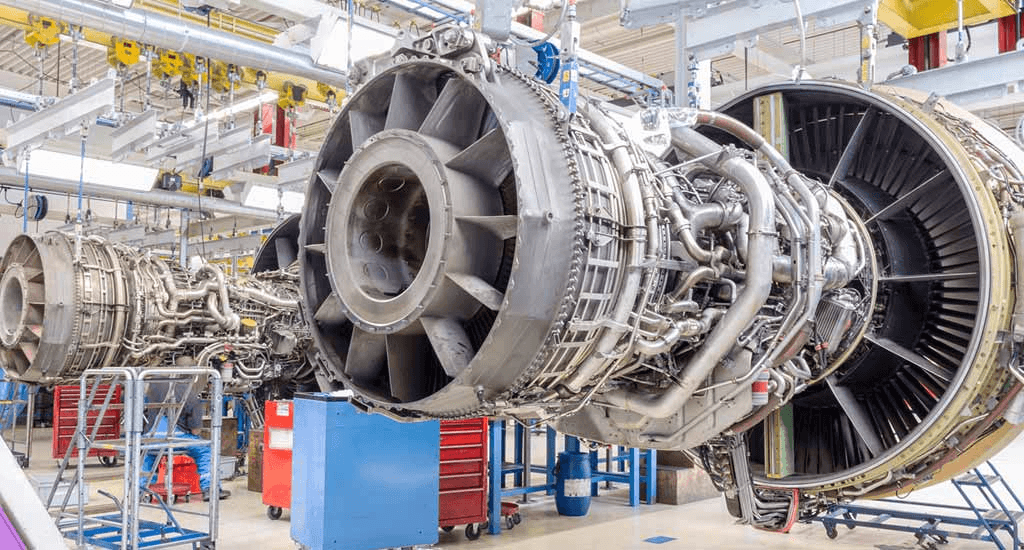
In the aerospace industry, materials are subjected to extreme thermal and mechanical stresses. Hafnium tubes are used in:
- Engine Components: Their high melting point and thermal stability make them ideal for engine parts that operate under intense heat.
- Exhaust Systems: The corrosion resistance of hafnium ensures longevity in harsh combustion environments.
- Structural Components: In military and defense applications, hafnium tubes are sometimes used in missile and aircraft components where both strength and heat resistance are crucial.
The reliability of hafnium in these applications helps improve overall performance and safety in aerospace systems, making it a material of choice for engineers seeking both durability and precision.
Nuclear Industry
Hafnium’s neutron absorption capability makes it a vital material in the nuclear sector:
- Control Rods: Hafnium tubes are incorporated into control rod designs in nuclear reactors. Their ability to absorb neutrons helps regulate fission reactions and maintain safe reactor conditions.
- Cladding: In some reactor designs, hafnium tubes are used as cladding for fuel rods. The material’s thermal stability and corrosion resistance ensure the safe containment of nuclear materials.
- Radiation Shielding: Hafnium’s properties are also leveraged in radiation shielding applications, protecting sensitive components and personnel from harmful neutron radiation.
These applications underscore the critical role hafnium plays in ensuring the safety and efficiency of nuclear power generation.
Chemical Processing
The chemical industry frequently encounters highly corrosive environments that demand robust materials:
- Reactor Tubing: Hafnium tubes are used in chemical reactors where they transport aggressive chemicals at high temperatures without degrading.
- Heat Exchangers: Their thermal stability and corrosion resistance make them ideal for heat exchangers used in chemical processing plants.
- Piping Systems: In applications where chemical compatibility is essential, hafnium tubes serve as reliable conduits for transporting corrosive substances.
By providing consistent performance even under chemically aggressive conditions, hafnium tubes help maintain operational efficiency and safety in chemical processing facilities.
Electronics and Semiconductor Applications
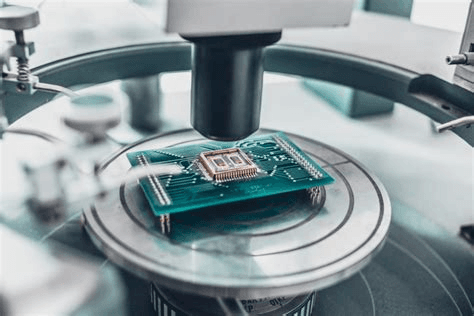
While perhaps less well‑known, hafnium is gaining prominence in the electronics industry:
- Gate Dielectrics: Hafnium oxide is a key material in advanced semiconductor devices. Its high dielectric constant improves the performance of transistors in modern microprocessors.
- Interconnects and Wiring: Hafnium’s thermal properties support the development of next‑generation electronics that require both durability and efficiency.
- Miniaturized Components: As devices shrink in size, the need for materials that can handle high performance in a small footprint increases. Hafnium-based materials are at the forefront of enabling further miniaturization and enhanced device performance.
The integration of hafnium into semiconductor devices marks a significant advancement in electronic materials, driving innovation in the technology sector.
Market Overview and Future Trends
Global Demand and Market Growth
The market for hafnium tubes has experienced steady growth over the past decade. Driven by the expanding nuclear energy sector, advancements in aerospace engineering, and increased demand for high‑performance electronics, the global demand for hafnium tubes is projected to rise. Several market research reports indicate a positive trend, with emerging economies contributing significantly to the growth.
Technological Advancements
Advances in manufacturing technologies are reducing production costs and improving the quality of hafnium tubes. New fabrication methods such as additive manufacturing and precision rolling techniques are on the rise, providing manufacturers with improved control over tube dimensions and properties. These innovations not only enhance product performance but also open up new applications across various industries.
Strategic Investments and Research
Both private enterprises and government agencies are investing in research to unlock new applications for hafnium tubes. Innovations in nuclear reactor safety, aerospace propulsion, and chemical processing continue to drive the research agenda. Increased funding in these areas is expected to yield breakthroughs that further enhance the performance and reduce the cost of hafnium tube production.
Environmental Considerations
As industries become more environmentally conscious, the long lifecycle and recyclability of hafnium tubes make them an attractive option. Research into sustainable production processes is ongoing, with a focus on minimizing waste and energy consumption. Companies are actively exploring methods to reuse and recycle hafnium components, aligning with global trends towards greener manufacturing practices.
Future Market Challenges
Despite promising prospects, the hafnium tube market faces challenges such as:
- Raw Material Availability: Hafnium is primarily extracted from zirconium ores, and fluctuations in supply can affect production.
- Cost: The high cost of hafnium extraction and purification remains a barrier, although ongoing research is addressing these issues.
- Competition: Alternative materials with similar properties may emerge as competitors, prompting continuous innovation in hafnium tube technology.
Nonetheless, with the ongoing development of high‑performance materials and innovative manufacturing techniques, hafnium tubes are expected to maintain a robust position in the market.
Comparisons with Other Materials
Zirconium vs. Hafnium
Hafnium and zirconium share many similarities, given that they often occur together in nature. However, there are distinct differences:
- Thermal Properties: Hafnium has a higher melting point compared to zirconium, making it more suitable for high‑temperature applications.
- Neutron Absorption: Hafnium is a better neutron absorber than zirconium, which is why it is preferred in nuclear reactor control rods.
- Cost: Hafnium is rarer and more expensive, which can be a limiting factor in cost‑sensitive applications.
Titanium and Stainless Steel
When compared to titanium and stainless steel, hafnium offers superior performance in extreme environments:
- Corrosion Resistance: While stainless steel provides good resistance in many settings, hafnium’s ability to form a protective oxide layer gives it an edge in highly corrosive environments.
- Temperature Resistance: Titanium and stainless steel cannot match the high‑temperature tolerance of hafnium, which is crucial for aerospace and nuclear applications.
- Mechanical Strength: Although titanium is strong, the unique combination of properties offered by hafnium makes it the material of choice for specialized applications where both thermal and chemical stability are required.
These comparisons highlight why many industries are willing to invest in the higher cost of hafnium tubes for applications that demand uncompromised performance.
Challenges in the Hafnium Tube Industry
Supply Chain Complexity
The production of hafnium tubes is subject to a complex supply chain. Since hafnium is typically obtained as a by‑product of zirconium refining, fluctuations in zirconium demand and supply can directly impact hafnium availability. Manufacturers must navigate these challenges by establishing reliable partnerships with mining and refining companies.
High Production Costs
The cost of extracting and purifying hafnium is relatively high due to the complexity of the separation process and the rarity of the metal. Investments in advanced processing techniques and recycling methods are critical to reducing costs and expanding the market for hafnium tubes.
Quality Control and Standardization
Ensuring consistent quality in hafnium tubes is essential for their performance in critical applications. Strict industry standards and rigorous testing protocols are required. Variations in tube dimensions, surface finish, or material properties can have significant implications, especially in nuclear or aerospace applications. As a result, ongoing efforts in quality control and standardization are a focal point for manufacturers.
Environmental and Safety Considerations
Sustainability in Production
Environmental considerations are becoming increasingly important in the production of advanced materials. The manufacturing of hafnium tubes is no exception:
- Energy Consumption: High‑temperature processes used in production require substantial energy inputs. Innovations aimed at energy efficiency are essential to reducing the environmental footprint.
- Waste Management: Recycling and reusing hafnium from spent components or scrap material is a growing area of focus. Companies are investing in technologies that minimize waste and promote sustainable practices.
- Green Manufacturing: Advances in green manufacturing techniques are being explored to reduce harmful emissions and improve the overall sustainability of hafnium tube production.
Safety in High‑Temperature and Nuclear Applications
The inherent properties of hafnium also contribute to safety in its applications:
- Nuclear Safety: In nuclear reactors, hafnium’s neutron absorption capabilities contribute to controlling fission reactions, reducing the risk of uncontrolled chain reactions.
- High‑Temperature Operations: The stability of hafnium at extremely high temperatures minimizes the risk of material failure, ensuring safer operation in demanding environments.
Environmental and safety standards continue to evolve, prompting manufacturers and end users to adopt best practices and cutting‑edge technologies that protect both workers and the environment.
Conclusion
Hafnium TubeHafnium Tube is a high‑performance material that plays a crucial role in some of the most advanced industrial and technological applications today. Its exceptional thermal stability, corrosion resistance, and neutron absorption properties make it indispensable in aerospace, nuclear, chemical processing, and electronics industries. As demand grows and technological advancements drive innovation in manufacturing processes, the future of hafnium tubes looks promising despite challenges such as raw material availability and high production costs.
The market for hafnium tubes is poised for steady growth, thanks to ongoing research, strategic investments, and a global focus on sustainability. As industries continue to push the boundaries of performance and safety, hafnium tubes will remain a critical material for applications that demand the best in reliability and efficiency.
This comprehensive guide provides a detailed overview of the properties, applications, and market dynamics of hafnium tubes. Whether you are a seasoned engineer, a researcher exploring advanced materials, or a business professional looking at market trends, understanding the intricacies of hafnium tube technology is essential for making informed decisions in today’s competitive landscape.
Embracing the future of material science and technological innovation means recognizing the value of specialized materials like hafnium. With its proven track record in extreme conditions and its growing importance across diverse sectors, hafnium tube stands as a testament to how advanced materials can drive progress, enhance safety, and offer sustainable solutions for modern industrial challenges.
By staying informed about the latest developments in hafnium tube manufacturing and applications, stakeholders can harness its unique benefits to create more resilient, efficient, and safe products. As research continues to unlock further improvements in processing techniques and as new applications emerge, the role of hafnium tube in high‑technology industries is set to expand even further.
In conclusion, the dynamic world of hafnium tubes reflects the broader trends in high‑performance materials. Its success is driven by a combination of inherent material advantages, ongoing innovation, and a commitment to meeting the evolving demands of modern technology. As we look to the future, hafnium tube technology is not only a key enabler for current applications but also a gateway to new possibilities in the fields of energy, aerospace, and electronics.