Zirconium, a transition metal with exceptional properties such as high melting point, remarkable corrosion resistance, and strength, is an integral material in numerous industrial applications. Among its many forms, zirconium tubes stand out due to their versatility and superior mechanical properties, making them essential in various high-performance industries. From nuclear energy to medical devices, aerospace, and chemical processing, zirconium tubes are employed in a wide range of applications where durability and reliability are crucial. In this article, we will explore the multiple uses of zirconium tubes, examining their unique properties, manufacturing processes, and their vital role in diverse industries.
1. Introduction to Zirconium
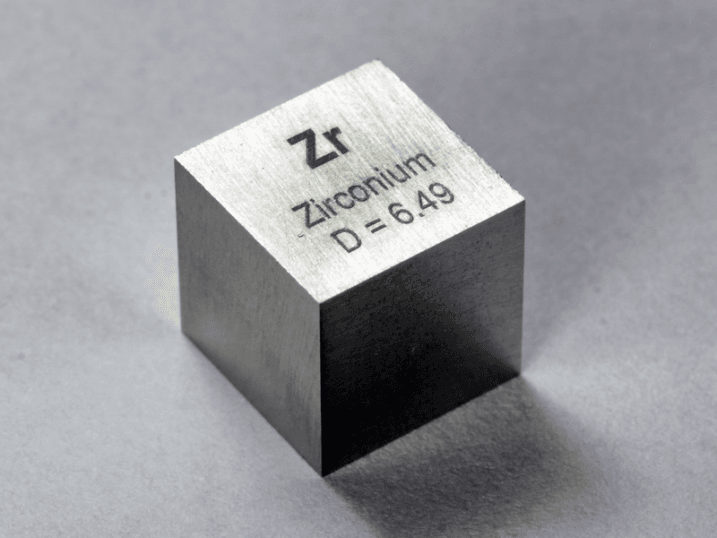
1.1 Physical and Chemical Properties
Zirconium (Zr) is a silvery-gray metal that exhibits outstanding resistance to corrosion, particularly in aggressive environments such as high temperatures and in the presence of acids and bases. It has a high melting point of approximately 1855°C (3371°F), which makes it resistant to degradation even in extreme conditions. Its ability to form a stable, protective oxide layer (ZrO2) on its surface enhances its durability and corrosion resistance, contributing to its extensive use in demanding industrial applications.
Zirconium is commonly derived from minerals like zircon (ZrSiO4), a naturally occurring silicate that is processed into pure zirconium metal. In many applications, zirconium is alloyed with other elements, such as tin, iron, and niobium, to enhance its mechanical properties, including strength, creep resistance, and resistance to radiation. The unique combination of high-temperature strength, corrosion resistance, and low neutron absorption makes zirconium an ideal material for a variety of applications.
1.2 Manufacturing of Zirconium Tubes
Zirconium tubes are produced through a series of manufacturing processes, including extrusion, drawing, and machining. The process starts with the extraction and refinement of zirconium metal, which is then heated to high temperatures to form billets. These billets are then extruded or drawn into tubular shapes of varying diameters and wall thicknesses, depending on the intended application. Once the tubes are formed, they may undergo additional treatments such as heat treatment and surface finishing to further enhance their mechanical properties and corrosion resistance.
Zirconium tubes are available in various grades and sizes, which makes them adaptable for use in numerous industries that require specific material characteristics. These tubes are highly customizable, with precise tolerances, surface finishes, and alloy compositions tailored to meet the requirements of different applications.
2. Zirconium Tubes in the Nuclear Industry
Zirconium tubes are perhaps most famously used in the nuclear industry, where they play a crucial role in nuclear reactors. Their unique combination of high-temperature resistance, low neutron absorption, and corrosion resistance makes zirconium an indispensable material in this field.
2.1 Fuel Cladding in Nuclear Reactors
In nuclear reactors, zirconium alloys are primarily used as fuel cladding. The fuel cladding is the protective outer layer that surrounds the fuel rods, which contain uranium or plutonium, in a nuclear reactor. The primary role of the cladding is to prevent the release of radioactive materials into the reactor coolant and to provide a structural framework that holds the fuel in place.
Zirconium alloys, such as Zr-2 and Zr-4, are the materials of choice for fuel cladding because they offer excellent corrosion resistance even in the extreme conditions found in nuclear reactors. The material must withstand high temperatures, high-pressure environments, and exposure to radiation without compromising the integrity of the fuel rod. Zirconium’s ability to resist corrosion in both acidic and high-temperature aqueous environments is a key factor that enables it to perform effectively in these harsh conditions.
Furthermore, zirconium has a very low neutron absorption cross-section, which means it does not interfere significantly with the nuclear reactions occurring within the reactor. This is crucial because any significant neutron absorption by the cladding material would reduce the efficiency of the nuclear reaction. Zirconium’s neutron transparency ensures that the fuel rods can operate effectively without hindering the chain reaction that powers the reactor.
2.2 Corrosion Resistance and Longevity
The zirconium alloy cladding is also known for its remarkable longevity. The material forms a stable, protective oxide layer when exposed to oxygen or water, which acts as a shield against further corrosion. This oxide layer helps maintain the structural integrity of the fuel cladding over time, even after extended periods of high radiation exposure and high-temperature operation. This resistance to radiation-induced degradation ensures that zirconium-based fuel cladding can remain reliable throughout the fuel’s lifetime in the reactor.
The durability of zirconium tubes used in fuel cladding also contributes to the overall safety of nuclear reactors. The material’s ability to maintain its strength and integrity under harsh reactor conditions minimizes the risk of failure and the potential release of radioactive materials.
2.3 Spent Fuel Management
Zirconium tubes are not only critical during the operation of nuclear reactors but also play a vital role in the storage and management of spent nuclear fuel. After fuel rods have completed their useful life in the reactor, they are removed and placed in spent fuel pools or dry cask storage systems. The zirconium cladding continues to serve as a protective barrier, ensuring that radioactive materials do not leak into the environment during storage.
The corrosion-resistant properties of zirconium ensure that spent fuel can be safely stored for extended periods without the risk of degradation or contamination. This long-term durability is critical in the management of spent nuclear fuel, which must be contained and monitored for decades or even centuries until it reaches safe levels of radioactivity.
3. Aerospace and Military Applications
3.1 High-Temperature Resistance
Zirconium tubes are also used in the aerospace industry, particularly in applications that involve extreme temperatures and pressures. Zirconium’s high melting point and excellent resistance to oxidation make it ideal for components exposed to high-velocity airflow, combustion, and other harsh conditions typically encountered in aerospace environments.
In aerospace applications, zirconium tubes are used in heat exchangers, rocket nozzles, and turbochargers. These components must withstand not only high temperatures but also corrosive fuel and exhaust gases. Zirconium’s ability to resist corrosion in these harsh environments ensures that these aerospace components can perform reliably and efficiently over extended periods.
3.2 Zirconium in Jet Engine Components
In military applications, zirconium tubes are used in components such as jet engine parts, where the material’s ability to withstand high temperatures and extreme pressure is essential for ensuring the safety and performance of the engine. Zirconium’s resistance to corrosion from fuel and exhaust gases is crucial for maintaining the reliability of jet engines, which must perform in challenging conditions without failure.
Zirconium’s high strength and resistance to heat-induced wear and tear also make it an ideal material for other military technologies, such as rocket propulsion systems, where the ability to withstand extreme temperatures and mechanical stresses is essential.
3.3 Nuclear Propulsion in Submarines and Aircraft Carriers
Zirconium is used in nuclear propulsion systems for military submarines and aircraft carriers. These vessels rely on nuclear reactors to generate power and propulsion, and zirconium’s resistance to radiation and high temperatures makes it the perfect material for use in nuclear reactors that power these ships.
In nuclear propulsion systems, zirconium tubes are used for fuel cladding and other reactor components, ensuring that the reactor operates efficiently and safely. Zirconium’s ability to endure prolonged exposure to radiation and high temperatures allows the reactors to operate for long periods without the need for refueling or major maintenance, giving these vessels unmatched endurance and autonomy.
4. Medical and Dental Applications
4.1 Prosthetics and Implants
In the medical field, zirconium tubes and alloys are used in a variety of applications, particularly in the development of medical implants and prosthetics. Zirconium’s biocompatibility, strength, and resistance to wear make it an ideal material for products that are implanted in the human body.
Zirconium oxide (ZrO2), a ceramic form of zirconium, is commonly used in dental implants, crowns, and bridges. It is highly durable, resistant to cracking, and mimics the appearance of natural teeth. Zirconium dental implants are preferred over traditional titanium implants due to their excellent aesthetic qualities, as they can be made to closely resemble the appearance of real teeth.
Zirconium alloys are also used in orthopedic implants, such as hip and knee replacements. These implants must withstand significant mechanical stresses over time, and zirconium’s strength and wear resistance make it an ideal material for long-lasting joint replacements. Additionally, zirconium’s resistance to corrosion ensures that these implants do not degrade within the body.
4.2 Surgical Instruments and Radiation Shielding
Zirconium tubes are also used in the manufacture of surgical instruments, particularly those designed for high-precision operations. The material’s hardness, strength, and resistance to corrosion ensure that surgical tools made from zirconium can perform reliably under harsh sterilization conditions.
In addition to surgical instruments, zirconium is employed in medical radiation shielding. Its ability to block radiation makes it useful in equipment such as X-ray machines and radiation therapy devices, where it helps protect patients and medical staff from excessive exposure to radiation.
5. Chemical Processing Applications
5.1 Corrosion Resistance in Harsh Environments
In industries that involve the processing of aggressive chemicals, zirconium tubes play a vital role due to their exceptional corrosion resistance. The material is highly resistant to a wide range of chemicals, including acids such as sulfuric acid, hydrochloric acid, and nitric acid, as well as alkalis and salts.
Zirconium is particularly useful in chemical processing environments where high temperatures and pressures are common. It is employed in heat exchangers, reactors, and piping systems that are exposed to aggressive chemical agents. Zirconium’s resistance to both corrosive chemicals and high temperatures ensures that these systems remain durable and reliable, even in the most challenging processing environments.
5.2 Pharmaceutical Manufacturing
The pharmaceutical industry also makes use of zirconium tubes in the production of specialized medicines and vaccines. In processes where high temperatures, corrosive substances, or sterilization procedures are required, zirconium tubes provide a safe and effective solution. Their ability to resist chemical degradation ensures that pharmaceuticals are produced without contamination from the materials used in the manufacturing process.
6. Other Industrial Applications
6.1 Superalloys and Titanium Alloys
Zirconium plays a key role in the production of superalloys, which are materials designed to operate in extreme conditions, such as in turbine blades or jet engines. Superalloys containing zirconium are designed to withstand high temperatures, corrosion, and mechanical stress, ensuring reliability in critical applications.
Zirconium is also used in the creation of titanium alloys, which are commonly used in aerospace, medical devices, and automotive manufacturing. Titanium alloys enhanced with zirconium exhibit superior strength, corrosion resistance, and heat resistance, making them ideal for use in components that must perform under challenging conditions.
6.2 Manufacturing Equipment
In various manufacturing processes, zirconium tubes are used as components in furnaces, reactors, and other high-temperature equipment. The material’s ability to withstand extreme temperatures and resist thermal expansion makes it a valuable choice for manufacturing equipment that must endure harsh operational conditions.
7. Conclusion
Zirconium tubes are essential in a wide variety of industries due to their unique combination of high temperature resistance, corrosion resistance, and mechanical strength. From the nuclear industry, where they ensure the safe operation of reactors, to the aerospace, medical, and chemical processing sectors, zirconium’s versatility makes it indispensable in modern technology. As industries continue to evolve and demand increasingly advanced materials, the use of zirconium tubes will undoubtedly expand, reinforcing their role as a critical material for high-performance applications across the globe.