Introduction to Silicon Carbide (SiC)
Silicon carbide (SiC) is an advanced semiconductor material known for its exceptional properties, making it a critical component in modern electronic applications. As the demand for high-efficiency, high-power, and high-temperature electronics continues to grow, SiC has emerged as a superior alternative to traditional silicon-based semiconductors. With its wide bandgap, high thermal conductivity, and mechanical robustness, SiC is driving innovation in power electronics, automotive technology, aerospace systems, and optoelectronics.
Unique Properties of Silicon Carbide
Silicon carbide exhibits several advantageous characteristics that set it apart from conventional silicon:
- Wide Bandgap: With a bandgap of approximately 3.26 eV, SiC operates efficiently at higher voltages and temperatures. This makes it ideal for applications requiring high power density and low energy losses.
- High Thermal Conductivity: SiC efficiently dissipates heat, reducing the risk of overheating and improving device longevity.
- Superior Breakdown Voltage: The material can withstand significantly higher electric fields than silicon, making it well-suited for high-power applications.
- High Electron Mobility: This property allows for faster switching speeds in electronic devices, improving overall efficiency.
- Chemical and Mechanical Stability: SiC is highly resistant to corrosion, radiation, and mechanical stress, enabling its use in extreme environments.
- High Hardness and Wear Resistance: With a hardness rating close to that of diamond, SiC is incredibly durable and suitable for mechanical applications in addition to electronics.
Applications of Silicon Carbide in Electronics
Silicon carbide is widely used across various industries due to its remarkable performance. Some of its key applications include:
Power Electronics
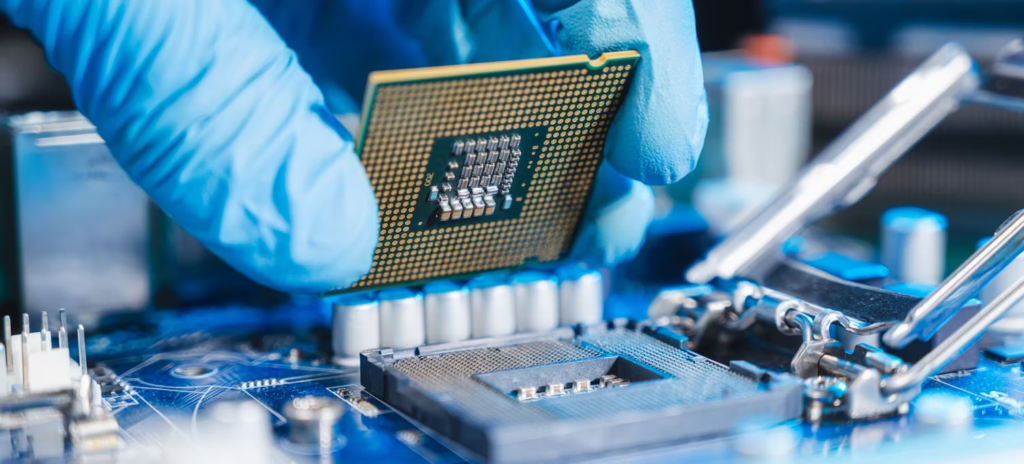
SiC-based power devices, such as MOSFETs and Schottky diodes, offer lower power losses and higher efficiency than their silicon counterparts. They are extensively used in power conversion systems, including:
- Electric Vehicles (EVs): SiC power modules improve battery efficiency, extend driving range, and reduce charging times.
- Renewable Energy Inverters: Solar and wind energy systems benefit from the high efficiency and durability of SiC components.
- Industrial Motor Drives: SiC-based converters and inverters enhance motor efficiency, reducing energy consumption.
- Smart Grid Infrastructure: SiC is used in grid-tied inverters and power transmission systems to improve performance and reliability.
Automotive Industry
The automotive sector has been one of the biggest adopters of SiC technology. Silicon carbide plays a pivotal role in modern electric vehicles by enhancing the efficiency of power electronics components, such as:
- Inverters: SiC-based inverters reduce energy losses, improve thermal management, and allow for compact designs.
- Onboard Chargers (OBCs): Faster and more efficient charging is possible with SiC-based OBCs, reducing energy waste.
- DC-DC Converters: Used for managing power distribution in EVs, SiC converters enhance energy utilization and longevity.
- Battery Management Systems (BMS): SiC components help optimize battery performance and safety.
Aerospace and Defense
SiC’s ability to withstand extreme temperatures, high radiation levels, and harsh conditions makes it indispensable in aerospace and defense applications. Some key uses include:
- Satellite Power Systems: The radiation resistance of SiC ensures the reliability of power electronics in space applications.
- Radar and Communication Systems: SiC enhances the efficiency and range of radar systems, improving target detection capabilities.
- Electric Propulsion Systems: SiC components contribute to more efficient and durable electric propulsion technologies for spacecraft.
- Military Equipment: High-power SiC electronics are used in secure communication devices and advanced defense systems.
RF and Microwave Applications
Due to its high electron mobility and thermal stability, SiC is extensively used in RF (radio frequency) and microwave devices. These applications include:
- 5G Infrastructure: SiC improves the efficiency and reliability of high-frequency signal processing components.
- Wireless Communication: SiC-based power amplifiers enhance the performance of cellular networks and satellite communication.
- Radar Systems: Military and civilian radar technologies benefit from SiC’s high-power handling capabilities.
LEDs and Optoelectronics
Silicon carbide substrates are commonly used in the production of high-brightness LEDs, enabling efficient lighting solutions with superior durability and energy efficiency. Key applications include:
- General Lighting: LED bulbs and fixtures leverage SiC substrates for improved longevity and brightness.
- Automotive Lighting: High-performance LED headlights and taillights use SiC-based LEDs.
- Display Technologies: SiC is used in micro-LED and OLED displays for enhanced color accuracy and efficiency.
- UV Light Sources: SiC-based UV LEDs find applications in sterilization, medical imaging, and industrial processes.
Advantages Over Traditional Silicon
Compared to conventional silicon, SiC offers several advantages:
- Higher efficiency: Reduced energy losses in power electronics.
- Greater thermal stability: Performs reliably in high-temperature environments.
- Increased power density: Supports miniaturization of electronic components.
- Extended lifespan: Reduced wear and failure rates in industrial applications.
- Better high-frequency performance: Essential for 5G, radar, and communication technologies.
Challenges and Limitations
Despite its many advantages, silicon carbide faces several challenges:
- High Manufacturing Costs: SiC wafers are more expensive to produce than traditional silicon wafers due to complex fabrication processes.
- Processing Difficulties: SiC’s hardness makes it challenging to cut, grind, and polish, increasing production time and costs.
- Limited Availability: The supply chain for high-quality SiC materials is still developing, leading to occasional shortages.
- Integration Complexity: Engineers must adapt existing manufacturing processes to accommodate SiC technology, requiring additional investment.
Future of Silicon Carbide in Electronics
As technological advancements continue, the adoption of SiC in electronic devices is expected to rise. Research and development efforts focus on:
- Cost Reduction: Innovations in wafer production, such as 200mm SiC wafers, aim to lower costs and increase availability.
- Improved Manufacturing Techniques: Advanced fabrication methods, including epitaxial growth and defect reduction, enhance the performance and yield of SiC devices.
- Expanded Applications: Emerging fields such as quantum computing, next-generation power grids, and autonomous vehicles will drive further demand for SiC components.
- Sustainability Initiatives: As energy efficiency becomes a global priority, SiC’s role in reducing carbon footprints will be a key factor in its widespread adoption.
Conclusion
Silicon carbide is revolutionizing the electronics industry with its superior properties, paving the way for more efficient and reliable electronic devices. Its integration into power electronics, automotive, aerospace, and RF applications underscores its significance in modern technology. As innovations in SiC processing and manufacturing progress, its role in the future of electronics will continue to expand. With ongoing research and advancements, SiC is set to become a cornerstone material in next-generation semiconductor technologies, driving efficiency and sustainability across industries.